Crusher are used to reduce the ore in size, the purpose and the responsibility of the crusher operator is to operate that crusher in such a manner as to ensure that every possible ton is processed in the shortest period of time possible. This is accomplished by knowing and understanding all of the Gyratory Crusher Operating Variables that are inherent to his circuit, then by manipulating these variables achieve the best possible results. This holds true to all operating positions within a concentrating plant, so you will be hearing about them a lot.
Before you can begin to manipulate variables you must be able to recognize them. This then is what this next portion is all about. The variables that we are about to describe are standard, and by no means a complete list. Your mine may have some that are unique to your area or equipment. However the first one we will look at is the physical characteristics of the ore. As you know this is what ever physical qualities that the rock may exhibit, such as the hardness, the shape, and the size.
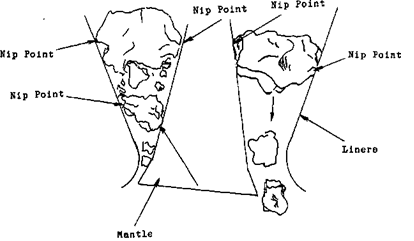
The ‘first of these three, the hardness, will regulate the feed rate by the output of energy that will be required to break it. A hard rock may take several crushing cycles of the crusher before it has been completely reduced in size. The next one is the shape of the ore, some shapes especially round ones are harder to break. When the ore is round it is an indication that there are few fracture lines in it. The absence of fracture lines is a characteristic of hard ore. Because the ore is round and probably hard as well, it is difficult for the nip-point to grip the rock and break it.
In this set of circumstances the rock will bounce up and down in the crushing chamber while the nip-point tries to get a hold on it.
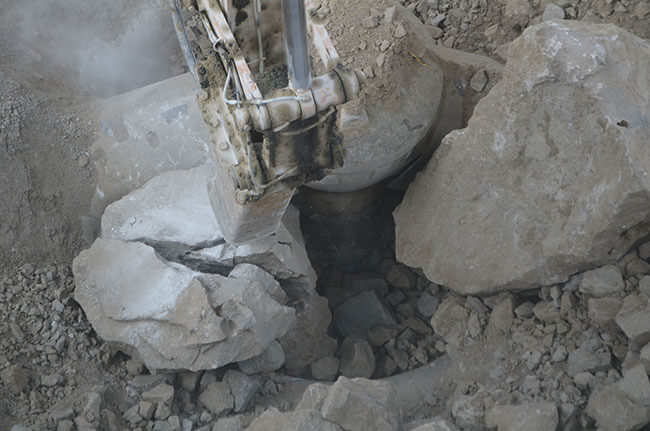
To get this type of rock broken you may have to resort to using an impact hammer if you have one. Or sometimes if you are able to, by turning the rock to present another face to the crushing surface the nip-point will be able to grab the new surface. If this fails there is another gambit you may try, dump some more ore on top of it. The weight plus the PINES between the rock surface and the crusher will give the nip-point some abrasion to grip against, possibly breaking the rock.
If all else fails the rock may have to be removed, remember, the priority here is to crush as much rock as possible. Spending too much time on one boulder will slow down the production too much.
There will be times when the mine department will deliver ore that is too big in size to enter the crushing chamber. These will have to be removed or broken, after all, it can’t be crushed if it can’t get into the crusher. This large ore will slow things down greatly due to the delivery of new ore being suspended until the large ore is out of the way. Even If this large ore is small enough to make it into the crusher, production will still be slow. The size of the feed will be one of the variables determine the rate of throughput. This is due to the amount of time that the ore will have to spend in the CRUSHING CHAMBER to be reduced to the required size.