Table of Contents
- Types of Flotation Reagents
- Flotation Collectors & Promoters
- Flotation Reagents
- Flocculants
- Flotation Reagents Handbook
- List of Flotation Reagents and Flotation Chemicals
- Flotation Reagent Pumps
- Flotation Chemical and Reagents
- Other Mining Reagents and Chemicals
- Flotation Reagent Manufacturers
- Flotation Reagent Suppliers
- Gold Mining Chemicals
This data on chemicals, and mixtures of chemicals, commonly known as reagents, is presented for the purpose of acquainting those interested in froth flotation with some of the more common reagents and their various uses.
Flotation as a concentration process has been extensively used for a number of years. However, little is known of it as an exact science, although, various investigators have been and are doing much to place it on a more scientific basis. This, of course, is a very difficult undertaking when one appreciates how ore deposits were formed and the vast number of mineral combinations existing in nature. Experience obtained from examining and testing ores from all over the world indicates that no two ores are exactly alike. Consequently, aside from a few fundamental principles regarding flotation and the use of reagents, it is generally agreed each ore must be considered a problem for the metallurgist to solve before any attempt is made to go ahead with the selection and design of a flotation plant.
Types of Flotation Reagents
Flotation reagents may be roughly classified, according to their function, into the following groups: Frothers, Promoters, Depressants, Activators, Sulphidizers, Regulators. The order of these groups is no indication of their relative importance; and it is common for some reagents to fall into more than one group.
Flotation Frothers
What is the Function of Frothers
The function of frothers in flotation is that of building the froth which serves as the buoyant medium in the separation of the floatable from the non-floatable minerals. Frothers accomplish this by lowering the surface tension of the liquid which in turn permits air rising through the pulp to accumulate at the surface in bubble form.
The character of the froth can be controlled by the type of frother. Brittle froths, those which break down readily, are obtained by the alcohol frothers. Frothers such as the coal tar creosotes produce a tough bubble which may be desirable for certain separations.
Flotation machine aeration also determines to a certain extent the character of the froth. Finely divided air bubbles thoroughly diffused through the pulp are much more effective than when the same volume of air is in larger bubbles.
Common Types of Frothers
In practice the most widely used frothers are pine oil and cresylic acid, although, some of the higher alcohols are gradually gaining favor because of their uniformity and low price. The frothers used depends somewhat upon the location. For instance, in Australia eucalyptus oil is commonly used because an abundant supply is available from the tree native to that country.
How much Frother to Use
Frothers are usually added to the pulp just before its entrance into the flotation machine. The quantity of frother varies with the nature of the ore and the purity of the water. In general from .05 to .20 lbs. per ton of ore are required. Some frothers are more effective if added in small amounts at various points in the flotation machine circuit.
Overdoses of frother should be avoided. Up to a certain point increasing the amount of frother will gradually increase the froth produced. Beyond this, however, further increases will actually decrease the amount of froth until none at all is produced. Finally, as the excess works out of the system the froth runs wild and this is a nuisance until corrected.
Not enough frother causes too fragile a froth which has a tendency to break and drop the mineral load. No bare spots should appear at the cell surface, and pulp level should not be too close to the overflow lip, at least in the cells from which the final cleaned concentrate is removed.
Characteristics of Frothers
A good flotation frother must be cheap and easily obtainable. It must not ionize to any appreciable extent. It must be an organic substance. Chemically a frother consists of molecules containing two groups having opposite properties. One part of the molecule must be polar in order to attract water while the other part must be non-polar to repel water. The polar group in the molecule preferably should contain oxygen in the form of hydroxyl (OH), carboxyl (COOH), carbonyl (CO); or nitrogen in the amine (NH2) or the nitrile form. All of these characteristics are possessed by certain wood oils such as pine oil and eucalyptus oil, by certain of the higher alcohols, and by cresylic acid.
Flotation Collectors & Promoters
What is Function of a Float Promoter/Collector
The function of promoters in flotation is to increase the floatability of minerals in order to effect their separation from the undesirable mineral fraction, commonly known as gangue. Actually what happens is that the inherent difference in wettability among minerals is increased and as a result the floatability of the more non-wettable minerals is increased to the point where they have an attraction for the air bubbles rising to the surface of the pulp.
In practical operation the function of promoters may be considered two-fold: namely, to collect and select. Certain of the xanthates, for instance, possess both collective and selective powers to a high degree, and it is reagents such as these that have made possible some of the more difficult separations. In bulk flotation all of the sulphide minerals are collected and floated off together while the gangue remains unaffected and is rejected as tailing. Non- selective promoters serve very well for this purpose. Selective or differential flotation, on the other hand, calls for promoters which are highly selective or whose collecting power may be modified by change in pulp pH (alkalinity or acidity), or some other physical or chemical condition.
Common Types of Flotation Promoters/Collectors
The common promoters for metallic flotation are xanthates, aerofloats, minerec, and thiocarbanilide. Soaps, fatty acids, and amines are commonly used for non-metallic minerals such as fluorspar, phosphate, quartz, felpsar, etc.
Promoters are generally added to the conditioner ahead of flotation to provide the time interval required for reaction with the pulp. Some promoters are slower in their action and in such case are added directly to the grinding circuit. Promoters which are fast acting or have some frothing ability are at times added directly to the flotation machine, as required, usually at several points. This practice is commonly known as stage addition of reagents.
How much Flotation Collector/Promoter to Use
The quantity of promoter depends on the character and amount of mineral to be floated, and in general for sulphide or metallic minerals .01 to .20 lbs. per ton of ore are required. Flotation of metallic oxides and non-metallic minerals usually require larger quantities of promoter, and in the case of fatty acids the range is from 0.5 to 2.5 lbs. per ton.
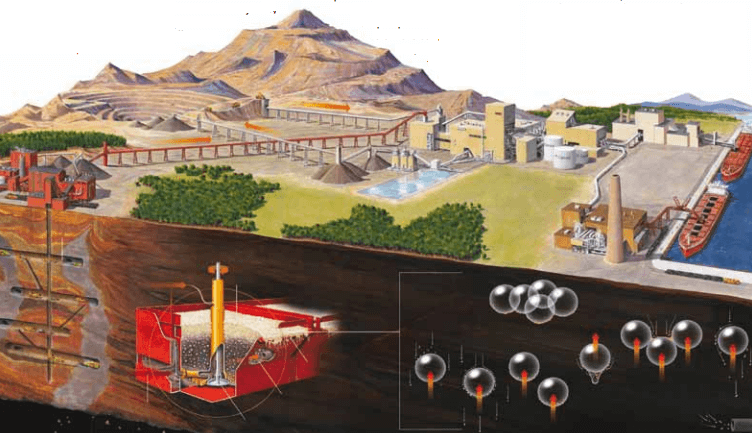
What are the Characteristics of a Collector
In general the requirements of an ideal promoter are that it combine collective power with selectivity, act speedily, resist decomposition, and be easily transported and handled.
Flotation Depressants
What is a Flotation Depressant used for
The function of depressants is to prevent, temporarily, or sometimes permanently, the flotation of certain minerals without preventing the desired mineral from being readily floated. Depressants are sometimes referred to as inhibitors.
Common Type of Flotation Depressants
Lime, sodium sulphite, cyanide, and dichromate are among the best known common depressants. Among organic depressants, starch and glue find widest application. If added in sufficient quantity starch will often depress all the minerals present in an ore pulp. Among the inorganic depressants, lime is the cheapest and best for iron sulphides, while zinc sulphate, sodium cyanide, and sodium sulphite depress zinc sulphide. Sodium silicate, quebracho, and also cyanide are common depressants in non-metallic flotation.
How much Flotation Depressants is needed
Depressants are generally added to the grinding circuit or conditioner usually before addition of promoting and frothing reagents. They may also be added direct to the flotation cleaner circuit particularly on complex ores when it is difficult to make a clean cut separation or where considerable gangue may be carried over mechanically into the cleaning circuit as in flotation of fluorspar. Quantity of depressants required depends on the nature of the ore treated and should be determined by actual test. For instance, lime required to depress pyrite may vary from 1 to 10 lbs. a ton.
Flotation Activators
What are Flotation Activators used for?
The function of activators is to render floatable those minerals which normally do not respond to the action of promoters. Activators also serve to render floatable again minerals which have been temporarily depressed in selective flotation. Sphalerite depressed with cyanide and zinc sulphate can be activated with copper sulphate and it will then respond to treatment like a normal sulphide. Stibnite, the antimony sulphide mineral, responds much better to flotation after being activated with lead nitrate.
The theory generally accepted on activation is that the activating substance, generally a metallic salt, reacts with the mineral surface to form on it a new surface more favorable to the action of a promoter. This also applies to non-metallic minerals.
Common Types Flotation Activators
Activators are usually added to the conditioner ahead of flotation and in general the time of contact should be carefully determined. Amounts required will vary with the condition of the ore treated. In the case of zinc ore previously depressed with zinc sulphate and cyanide, from 0.5 to 2.0 of copper sulphate may be required for complete activation. Quantities required should always be determined by test.
Flotation Sulphidizers
Why & When to use a Flotation Sulphidizer
The function of sulphidizers is to precipitate a film of sulphide on the surface of oxidized minerals or metals in order to make the surfaces more responsive to the action of promoters.
Common Types of Flotation Sulphidizers
The most widely used sulphidizer is sodium sulphide, which is commonly used in the flotation of lead carbonate ores and also slightly tarnished sulphides such as pyrite and galena. In the sulphidization of ores containing precious metals careful control must be exercised as in some instances sodium sulphide has been known to have a depressing effect on flotation of metallics. In such cases it is advisable to remove the precious metals ahead of the sulphidization step.
How much Flotation Sulphidizer is needed
Sulphidizers are usually fed into the conditioner just ahead of the flotation circuit. The quantity required varies with the characteristics of the ore and may range from .5 to 5 lbs. per ton. Conditioning time should be carefully determined and an excess of sulphidizing reagent avoided.
Flotation pH Regulators
What is a pH Regulator’s Function
The function of regulators is to modify the alkalinity or acidity in flotation circuits, which is commonly measured in terms of hydrogen ion concentration, or pH. Modifying the pH of a pulp has a pronounced effect on the action of flotation reagents and is one of the important means of making otherwise difficult separations possible.
The action of regulators may often be considered three-fold as follows:
- To precipitate soluble salts out of solution.
- To clean the mineral surfaces, thus enhancing the action of other reagents.
- To depress certain minerals.
Soluble salts may have their source in the ore or water, or both, and in precipitating them out of solution they generally become inert to the action of flotation reagents. Soluble salts have a tendency to combine with promoters thus withdrawing a certain proportion of the reagents from action on the mineral to be floated. Removal of the deleterious salts therefore makes possible a reduction in the amount of reagent, required. Complexing soluble salts by keeping them in solution yet inert to the reagents is in some cases desirable.
Mineral surfaces may vary according to pulp pH conditions as many of the regulators appear either directly or indirectly to have a cleansing effect on the mineral particle. This brings about more effective action on the part of promoters and other reagents, and in turn increases selectivity.
pH control by action of regulators is in some cases very effective in depressing certain minerals. Lime, for instance, will depress pyrite, and sodium silicate is excellent for dispersing and preventing quartz from floating. It is necessary, however, to have a definite concentration of the reagents for best results.
Common Types of pH Regulators
The common regulators are lime, soda ash, and sodium silicate for alkaline circuits, and sulphuric acid for acid circuits. Many other reagents are used for this important function. The separation required and character of ore will determine which regulators are best suited. In general, from an operating standpoint, it is preferable to use a neutral or alkaline circuit, but in some instances it is only possible to obtain results in an acid circuit which then will require the use of special equipment to withstand corrosion. Flotation of non-metallic minerals is at times more effective in an acid circuit as in the case of feldspar and quartz. The pulp has to be regulated to a low pH by means of hydrofluoric acid before any degree of selectivity is possible between the two minerals.
How much pH Regulator should be used
Regulators are fed generally to the grinding circuit or to the conditioner ahead of flotation and before addition of promoters and activators. The amounts required will vary with the character of the ore and separation desired. In the event an excessive quantity of regulator is required to obtain the desired pH it may be advisable to consider removing the soluble salts by water washing in order to bring reagent cost within reason.
Flotation Reagents
The tables on the following pages have been prepared to present in brief form pertinent information on a few of the more common reagents now being used in the flotation of metallic and non-metallic minerals. A brief explanation of the headings in the table is as follows:
Reagent: Reagents are listed alphabetically according to their technical names or manufacturer’s trade designation.
Description: Includes chemical composition if known, color, and other physical characteristics useful in identification of the flotation reagent.
Usual Method of Feeding: Whether in dry or liquid form. A large number of reagents are available in liquid form and naturally are best handled in wet reagent feeders, either full strength or diluted for greater accuracy in feeding. Many dry reagents are best handled in solution form and in such cases common solution strengths are specified in percent under this heading. A 10% water solution of a reagent means 10 lbs. of dry reagent dissolved in 90 lbs. of water to make 100 lbs. of solution. Some dry reagents, because of insolubility or other conditions, must be fed dry. This is usually done by belt or cone type feeders designed especially for this service to give accurate and uniform feed rates.
Pasty, viscous, insoluble reagents present a problem in handling and are generally dispersed by intense agitation with water to form emulsions which can then be fed in the usual manner with a wet reagent feeder or using a pump.
Usual Quantity Fed: Average figures in lbs. of reagents per ton of mill feed are shown and are to be used only as a guide.
Price Per Lb.: Prices shown are approximate and in general apply to drum lots and larger quantities F.O.B. factory. This information is very useful when making tests to determine the lowest cost satisfactory reagent combination for a specific ore. Some ores will not justify reagent expenditures beyond a certain limit, and in this case less expensive reagents must be given first consideration.
Uses: General use for each reagent as given is determined from experience by various investigators. Although the Equipment Company uses a large number of these reagents in conducting test work on ores received from all parts of the world, opinion, data, or recommendations contained herein are not necessarily based on our findings, but are data published by companies engaged in the manufacture of those reagents.
The ore testing Laboratory of 911metallurgist, in the selection of reagents for the flotation of various types of ores, uses that combination which gives the best results, irrespective of manufacturer of the reagents. The data presented on the following tables should be useful in selecting reagents for trials and tests, although new uses, new reagents, and new combinations are continually being discovered.
The consumption of flotation reagents is usually designated in lbs. per ton of ore treated. The most common way of determining the amount of reagent being used is to measure or weigh the amount being fed per. unit of time, say one minute. Knowing the amount of ore being treated per unit of time, the amount of reagent may then be converted into pounds per ton.
The tables below will be useful in obtaining reagent feed rates and quantities used per day under varying conditions. The common method of measurement is in cc (cubic centimetres) per minute. The tables are based on one cc of water weighing one gram. A correction therefore will be necessary for liquid reagents weighing more or less than water. Dry reagents may be weighed directly in grams per min. which in the tables is interchangeable with cc per min.
In the table on the opposite page the 100% column refers to undiluted flotation reagents such as lime, soda ash and liquids with a specific gravity of 1.00. Ninety-two per cent is usually used for light pine oils, 27 per cent for a saturated solution of copper sulphate and 14 per cent for TT mixture (thiocarbanilide dissolved in orthotoluidine). The other percentages are for solutions of other frequently used reagents such as xanthates, cyanide, etc.
Flocculants
The action of promoting reagents in increasing the contact-angle at a water/mineral surface implies an increase in the interfacial tension and, therefore, a condition of increased molecular strain in the layer of water surrounding the particle. If two such mineral particles be brought together, the strain areas enveloping them will coalesce in the reduction of the tensionary system to a minimum. In effect, the particles will be pressed together. Many such contacts normally occur in a pulp before and during flotation, with the result that the floatable minerals of sufficiently high contact-angle are gathered together into ” flocks ” consisting of numbers of mineral particles. This action is termed “ flocculation ”, and obviously is greatly increased by agitation.
The reverse action, that of “ deflocculation ”, takes place when complete wetting occurs, and no appreciable interfacial tension exists. Under these conditions there is nothing to keep two particles of ore in contact should they collide, since no strain area surrounds them ; they therefore remain in individual “ suspension ” in the pulp.
Since substances which can be flocculated can usually be floated, and vice versa, the terms “ flocculated ” and “ deflocculated ” have become more or less synonymous with “ floatable ” and “ unfloatable ”, and should be understood in this sense, even though particles of ore often become unfloatable in practice while still slightly flocculated—that is, before the point of actual deflocculation has been reached.
Flotation Reagents Handbook
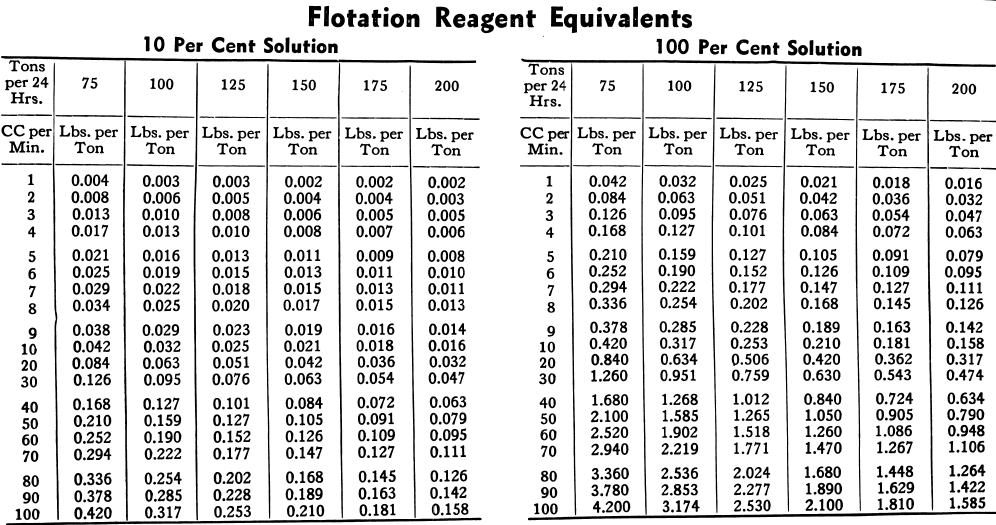
List of Flotation Reagents and Flotation Chemicals
Here is a List Flotation Reagents & Chemicals prepared to present in brief form pertinent information on a few of the more common reagents now being used in the flotation of metallic and non-metallic minerals. A brief explanation of the headings in the table is as follows:
Reagent: Reagents are listed alphabetically according to their technical names or manufacturer’s trade designation.
Description: Includes chemical composition if known, color, and other physical characteristics useful in identification of the reagent.
Usual Method of Feeding: Whether in dry or liquid form. A large number of reagents are available in liquid form and naturally are best handled in wet reagent feeders, either full strength or diluted for greater accuracy in feeding. Many dry reagents are best handled in solution form and in such cases common solution strengths are specified in percent under this heading. A 10% water solution of a reagent means 10 lbs. of dry reagent dissolved in 90 lbs. of water to make 100 lbs. of solution. Some dry reagents, because of insolubility or other conditions, must be fed dry. This is usually done by belt or cone type feeders designed especially for this service to give accurate and uniform feed rates.
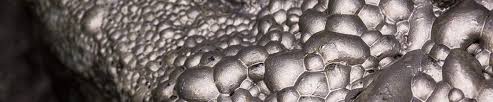
Pasty, viscous, insoluble reagents present a problem in handling and are generally dispersed by intense agitation with water to form emulsions which can then be fed in the usual manner with a wet reagent feeder.
Usual Quantity Fed: Average figures in lbs. of reagents per ton of mill feed are shown and are to be used only as a guide.
Flotation Reagent Pumps
The performance of froth flotation cells is affected by changes in unit load, feed quality, flotation reagent dosages, and the cell operating parameters of pulp level and aeration rates. In order to assure that the flotation cells are operating at maximum efficiency, the flotation reagent dosages should be adjusted after every change in feed rate or quality. In some plants, a considerable portion of the operator’s time is devoted to making these adjustments. In other cases, recoverable coal is lost to the slurry impoundment and flotation reagent is wasted due to operator neglect. Accurate and reliable processing equipment and instrumentation is required to provide the operator with real-time feedback and assist in optimizing froth cell efficiency.
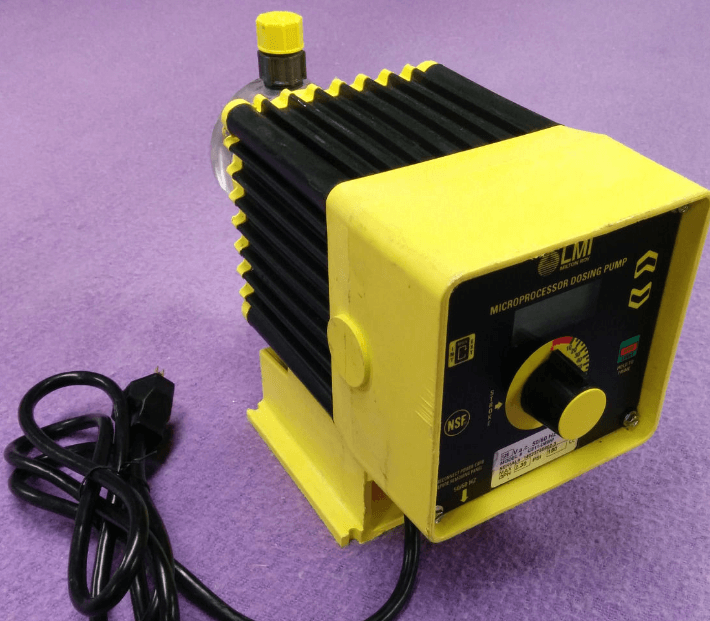
This process of optimizing froth cell efficiency starts with a well-designed flotation reagent delivery system. The flotation reagent pumps should be equipped with variable-speed drives so that the rates can be adjusted easily without having to change the stroke setting. The provision for remotely changing the reagent pump output from the control room assists in optimizing cell performance. The frother delivery line should include a calibration cylinder for easily correlating pump output with the frother delivery rate. Our experience has shown that diaphragm metering pumps of stainless steel construction give reliable, long-term service. Duplex pumps are used to deliver a constant frother-to-collector ratio over the range of plant operating conditions.
In most applications, the flotation reagent addition rate is set by the plant operator. The flotation reagents can be added in a feed-forward fashion based on the plant raw coal tonnage. Automatic feedback control of the flotation reagent addition rates has been lacking due to the unavailability of sensors for determining the quality of the froth cell tailings. Expensive nuclear-based sensors have been tried with limited success. Other control schemes have measured the solids concentrations of the feed, product, and tailings streams and calculated the froth cell yield based on an overall material balance. This method is susceptible to errors due to fluctuations in the feed ash content and inaccuracies in the measurement device.
Advances in Flotation Technology
Reagent | Description | Usual Feeding Method | Typical Dosage lbs/ton | Uses |
Acid Sludge | Oil refinery bi-product high in sulphuric acid | Undiluted liquid | 1.0 to 3.0 | Frother and promoter for bulk sulphide flotation |
Acid-Thio | Dissolve 5 grams dry thiocarbanilide in cold solution 100 grams concentrated H2so4, diluted with 25 grams of water. | Solution | .05- to .20 Thio | This combination makes thiocarbanilide water soluble and is useful in selective flotation of lead and zinc. |
Aciterage OL | A cationic surface active reagent formulated from Alkaterage C with lactic acid, shellacol, and water | 5-10% solution | .25 to 1.00 | Wetting, frothing, and emulsifying agent for floating non-metallic minerals in an acid circuit. Slime flocculator. |
Actinol C | A crude Tall Oil 40-53% Rosin Acids, 40-52% fatty acids. | Undiluted liquid | .5 to 2.5 | Flotation of non-metallic minerals. |
Actinol D | A refined Tall Oil 46% Linoleic, 51% oleic. | Undiluted liquid | .5 to 2.5 | Flotation of non-metallic minerals. |
Activated Carbon | A finely divided activated carbon product. | Dry | 05 to 1.5 | In some cases when used with xanthate higher grade sulphide concentrates have been produced. |
Aerofloat 15 | 15% phosphorus pentasulphide in cresylic acid. | Undiluted liquid | .05 to .20 | Frother and promoter for gold and sulphides of silver, copper, lead and zinc. |
Aerofloat 25 | 25% phosphorus pentasulphide in cresylic acid. | Undiluted liquid | .05 to .20 | In acid or neutral circuit is a strong non-selective promoter and frother for sulphide minerals. |
Aerofloat 31 | 31% phosphorus pentasulphide in cresylic acid. | Undiluted liquid | .05 to .20 | Excellent frother-promoter for galena and oxidized gold ores, also silver sulphides. |
Aerofloat 203 | A water soluble dry aerofloat reagent. | 5-10% solution | .05 to .20 | Promoter for gold, silver, copper and zinc sulphide ores. Stronger than sodium aerofloat. |
Aerofloat 208 | A non-frothing water soluble dry aerofloat. | 5-10% solution | .01 to .10 | Alone or in the combination with reagent 301 is widely used for flotation of gold and silver. |
Aerofloat 211 | A water soluble dry aerofloat. Formerly sodium aerofloat B. | 5-10% solution | .05 to .20 | Same as sodium aerofloat B. A powerful selective zinc reagent. |
Aerofloat 213 | A water soluble dry aerofloat. | 5-10% solution | .01 to .10 | Promoter for gold, silver, copper and ores. Has some tendency to froth. |
Aerofloat 226 | A water soluble dry aerofloat. | 5-10% solution | .02 to .10 | Similar to Aerofloat 213. |
Aerofloat 238 | A water soluble dry aerofloat. | 5-10% solution | .02 to .15 | Strong promoter for gold and silver, copper and zinc sulphide ores. Very little tendency to float pyrite in alkaline pulps. |
Aerofloat 241 | Neutralized aerofloat 25. Greenish black liquid. | 5-10% solution | .05 to .15 | Fast acting aerofloat promoter-frother for silver bearing lead ores, also copper and zinc sulphide. |
Aerofloat 242 | Neutralized aerofloat 31. Black and water soluble. | 5-10% solution | .02 to .15 | Similar to aerofloat 241 but a stronger promoter for copper, lead and silver sulphides. |
Aerofloat 243 | A water soluble dry aerofloat. | 5-10% solution | .02 to .15 | Slightly stronger promoter than reagent 203. |
Aerofloat 249 | Water soluble aerofloat. Brown to black color. | 5-10% solution | .02 to .15 | Strong non-selective promoter for sphalerite, copper sulphides and gold ores. Also a frother. |
Aerosol OT 100% | Sodium salt of di-octyl-sulfosuccinic acid. Resembles paraffin. | 1% solution | .01 to .20 | Wetting and dispersing agent in treatment of oxides and non-metallic minerals. |
Alamac | Acetate of Tallow amine. | 5% water solution | .10 to .50 | Cationic reagent for flotation of non-metallics such as feldspar, potash and phosphate. |
Alamac 26-D | Acetate of distilled tallow amine. | 5% water solution | .10 to .50 | Cationic reagent for flotation of non-metallics such as feldspar, potash and phosphate. |
Alamine 26 | A tallow amine. | 5% water solution | .10 to .50 | Flotation of non-metallics. |
Alamine 26-D | A distilled tallow amine. | 5% water solution | .10 to .50 | Flotation of non-metallics. |
Aliphat 44-A | Double distilled tall oil fatty acids primarily oleic and linoleic. | Undiluted liquid | .5 to 2.0 | Fatty acid collector promoter for flotation of non-metallic minerals. |
Aliphat 44-B | Single distilled tall oil fatty acids. Primarily oleic, linoleic and rosin acids. | Undiluted liquid | .5 to 2.0 | Fatty acid collector promoter for flotation of non-metallic minerals. |
Aliphat 44-E | Fractionally distilled tall oil fatty acids. Oleic and linoleic acids low in rosin acids. | Undiluted liquid | .5 to 2.0 | Very effective collector-promoter for flotation of fluorspar. |
Alkaterges A, E & T | Cationic oil soluble surface active agents similar to Alkaterge C. | Emulsion | .25 to .50 | Emulsification agents useful in non-metallic flotation. |
Alkaterage C | A non-volatile high molecular weight cationic surface active amine type agent. | Emulsion | .25 to .50 | Wetting, frothing, and emulsifying agent for non-metallic flotation. |
Aluminum Sulphate | Commonly known as alum, white crystalline water soluble solid solution Al2(So4)3. 18 H2O. | 5-10% solution | .1 to .5 | A good flocculating agent for slimes. |
Amijel | A form of corn starch. Granular powder. | 1-2% solution | .1 to .3 | Disperses gangue slimes and in some cases permits production of higher grade sulphide concentrates. |
Amine 220 | A mixture of high molecular weight amines. | 5% solution | .10 to .50 | Has been used to float silica and iron oxide from barite . Acts as frother and promoter. |
Amono-Phos | A crude mono-ammonium phosphate. | Dry | .5 to .30 | A modifying agent similar in action to soda ash and sodium silicate. |
Annite Reagent A | An amine soap. Water soluble powder. | 1-2% | .5 to 1.5 | Promoter for oxidized minerals such as lead carbonate. Effective without sulphidization. |
Antifoam HF | Colorless liquid. | Undiluted liquid | .05 to .25 | Froth modifier for use with cationic reagents. |
Armac 12-D | Distilled N-dodecylamine acetate. Laurylamine acetate. | 1-5% water solution | .05 to 1.00 | Strong cationic collector. Hematite, manetite, ilmenite, wolframite, scheelite, feldspar, monazite, chromite. |
Armac 16-D | Distilled N-hexadecylamine acetate. Palmitylamine acetate. | 1-5% water solution | .05 to 1.00 | Strong cationic collector. Potash, phosphate, feldspar, mica, spodumene, beryl, silica, clays. |
Armac 18-D | Distilled octadecylamine acetate stearylamine acetate. | 1-2.5 water solution | .05 to 1.00 | Strong cationic collector. Same minerals as Armac 16 D. |
Armac CD | Distilled primary amine acetate derived from cocoanut fatty acids. | 1-5% water solution | .05 to 1.00 | Strong cationic collector. Same minerals as Armac 12 D. |
Armac SD | Distilled primary amine acetate derived from soya fatty acids. | 1-5% water solution | .05 to 1.00 | Strong cationic collector. Same minerals as Armac 16 D. |
Armac T | Technical primary amine acetate derived from tallow fatty acids. | 1-5% water solution | .05 to 1.00 | Strong cationic collector. Same minerals as Armac 16 D. |
Armac TD | Distilled primary amine acetate derived from tallow fatty acids. | 1-5% water solution | .05 to 1.00 | Strong cationic collector. Same minerals as Armac 16 D. |
Armac HTD | Distilled primary amine acetate derived from tallow hydrogenated fatty acids. | 1-2.5 water solution | .05 to 1.00 | Strong cationic collector. Same minerals as Armac 16 D. |
Armeen 12-D | Distilled primary N-dodecylamine . Laurylamine . | In isopropyl alcohol or kerosene solvent. | .05 to 1.00 | Strong cationic collector. Hematite, magnetite, ilmenite, wolframite, scheelite, feldspar, monazite, chromite. |
Armeen 18-D | Distilled primary N-hexadecylamine. Palmitylamine. | In isopropyl alcohol or kerosene solvent. | .05 to 1.00 | Strong cationic collector. Potash, phosphate, feldspar, mica, spodumene, beryl, silica, clays. |
Armeen CD | Distilled primary amine derived from cocoanut fatty acids. | Liquid or in isopropyl alcohol or kerosene solvent. | .05 to 1.00 | Strong cationic collector. Same minerals as Armeen 12-D. |
Armeen SD | Distilled primary amine derived from soya fatty acids. | Liquid or in isopropyl alcohol or kerosene solvent. | .05 to 1.00 | Strong cationic collector. Same minerals as Armeen 18-D. |
Armeen TD | Distilled primary amine derived from tallow fatty acids. | In isopropyl alcohol or kerosene solvent. | .05 to 1.00 | Strong cationic collector. Same minerals as Armeen 18-D and Armeen SD |
Armeen HTD | Distilled primary amine acetate derived from tallow hydrogenated tallow fatty acids. | In isopropyl alcohol or kerosene solvent. | .05 to 1.00 | Strong cationic collector. Same minerals as Armeen TD. |
Arquad C | 33% active coconut tri-methyl ammonium chloride. | 1-5% water solution. | .10 to 1.00 | Weak cationic collector. Flotation of silica. |
Arquad 2C | 50% active di-coconut dimethyl ammonium chloride. | 1-5% water solution. | .10 to 1.00 | Weak cationic collector for silica. Flocculating agent for slimes. |
Arquad S | 50% active soya tri-methyl ammonium chloride. | 1-5% water solution. | .10 to 1.00 | Weak cationic collector. Flotation of paper pulp fiber, waste oils, fats, etc. |
Arquad T | 50% active tallow tri-methyl ammonium chloride. | 1-5% water solution. | .10 to 1.00 | Weak cationic collector for silica. Same material as Arquad S. |
Barium Chloride | BaCl2 water soluble crystalline solid. | 1-5% water solution. | .01 to 1.00 | Modifier or quartz. |
Barium Sulphide | A grayish black powder. | Dry | 1.0 to 3.0 | Sulphidizing agent for oxidizing minerals. High pH avoided by its use. |
Barrett Flotation Oil No. 4 | Coal tar creosote oil. slightly more viscous than cresylic acid. Insoluble in water. | Undiluted liquid | .05 to 2.0 | Has strong frothing and collecting properties. Used on sulphide ores quite extensively. |
Barrett No. 410 | Coal tar creosote oil. | Undiluted liquid | .05 to 2.0 | Froth modifier and promoter similar in action to Barrett No. 4. |
Barrett No. 634 | A coal tar creosote oil slightly more viscous than Barrett No. 4. Insoluble in water. | Undiluted liquid | .05 to .20 | Useful if a stiff and more persistent froth is desirable for sulphide flotation. |
Calcium Polysulphide | A liquid calcium polysulphide. | Undiluted | 05 to 2.0 | Sulphidizer for lead carbonate and tarnished sulphides. |
Calcium Sulphite | CaSo3 2H2O. Insoluble white crystalline solid. | Dry | .1 to 5.0 | Similar in action to sodium sulphite for depressing iron and zinc sulphides. |
Calgon | Sodium hexameta-phosphate. Water soluble glassy flakes. | 5-10% solution. | 0.1 to 1.0 | Excellent water softener, useful when floating non-metallics with fatty acids. Good dispersant. |
Castor Oil Acids 9-11 | Distilled fatty acids of dehydrated castor oil. Clear liquid. | Undiluted or emulsion | .5 to 2.0 | Promoter of oxide and non-metallic minerals, similar to oleic acid in its action. |
Castor Oil Acids 135 | Clear bright oily liquid. Octadecadienoic acids 9-11 and 9-12. | Undiluted or emulsion | .5 to 2.0 | Promoter of oxide and non-metallic minerals, similar to oleic acid in its action. |
Caustic Soda | NaOH, flakes or pellets. Water soluble. | 5-10% solution. | .5 to 3.0 | Alkalinity regulator and dispersing agent for sulphide and non-sulphide flotation. |
Caustic starch | A water solution of starch and sodium hydroxide. | 1-2% solution | .1 to .3 | Aids production of high-grade sulphide concentrates by depressing slimes, settling aid. |
Cellulosics CMC | Sodium carboxymethyl – cellulose, ionic. Dry powder cellulose gum. | Water dispersion | .01 to .05 | A flocculant and dispersant; also a depressant or gangue slimes in flotation of sulphides. |
Cellulosics HEC (Natrosol) | Hydroxyethyl cellulose, non-ionic. Dry powder cellulose. | Water dispersion | .01 to .05 | A flocculant and dispersant useful in flotation of non-metallic and iron ore along with cationic promoter. |
Cement | Standard cement with variable lime content. | Dry | .5 to 2.0 | Alkalinity regulator. Has been used to depress pyrite and pyrrhotite. |
Coal tar | A coal distillation by-product. | Undiluted liquid | .1 to .5 | Frother for sulphide minerals being replaced by more uniform reagents. |
Copper Sulphate | A blue crystalline solid commonly known as blue stone or blue vitriol. CuSo4. 5H2O | Saturated solution | 025 to 1.0 | Activator for sphalerite, arsenopyrite, and tarnished gold, the latter when used with caustic soda. |
Creosote coal Tar | A creosote produced as a coal tar distillation by-product. | Undiluted liquid | .1 to .3 | Frother and collector for sulphides. Produces a tough froth. |
Creosote No. 1 Hardwood | Black, slightly viscous liquid. | Undiluted liquid | .1 to .3 | Frother and collector for sulphides. Extensively used for gold flotation. |
Cresylic Acid | A crude grade of carbolic acid. Straw color to dark brown. | Undiluted liquid | .05 to .20 | Frother extensively used for lead sulphide flotation. |
Cupferron | Ammonium phenylnitroso-hydroxyl-amine. | Solution | .01 to .05 | A cationic collector for cassiterite. (Sno2) (experimental only). |
Cyanide | Sodium cyanide eggs or granular. Very poisonous. | 5-10% solution. | .03 to .75 | Depressant for iron and zinc sulphide. Also depresses silica in presence of fatty acids. |
Daxad No. 23 | Polymerized sodium salts of substituted benzoic alkyl sulfonic acids. Water soluble brown powder. | 5-10% solution. | .05 to .20 | Dispersing agent for gangue slimes. Best at pH 7.0 – 9.5 Aid in classification. |
Denver Sulphidizer | A calcium polysulphide in liquid form. | Undiluted liquid | .5 to 1.5 | An inexpensive sulphidizer for lead carbonate. Has slight frothing properties. |
Dichromate | Na2Cr2O7 2H2O. Sodium dichromate, an orange crystalline powder. | 5-10% solution. | 1.0 to 5.0 | Positive depressor for galena in copper, lead, zinc separations. |
Dowforth 250 | Water soluble alcohol type frother. | Undiluted liquid | .01 to .05 | Excellent frother for selective flotation. Produces brittle froth. Does not attack rubber |
Dresinates X, XX, TX | Sodium salts (soaps) of selected rosin acids. | 1-5% water solution | .2 to 3.0 | Anionic collector. Non-metallic flotation. |
Duomeen T | Light red soft paste. A diamine with 75-80% amine content. | 1-5% emulsion | .05 to 1.0 | Strong cationic collector. |
Duponal 100 | Dry water soluble white flakes. Sodium octyl sulphate. | 5-10% solution | .01 to .10 | Anionic collector. Flotation of molybdenite similar to Syntex L. |
Elastoil LL | A dark colored liquid bi-product from linseed oil processing. | Undiluted liquid | .3 to 1.5 | A collector for non-metallics and tungsten minerals. Has little or no tendency to froth. |
Emcol X-25 | Alkanolamine salt of a sulfated complex alcohol. | 1-5% solution | .1 to .5 | A cationic collector; also used as an emulsion with oleic acid or kerosene. See kerosene. |
Emcol 4150 | A complex fatty acid amite sulfate. | Undiluted liquid | .25 to 1.5 | Manganese flotation. |
Emersol 300 | A distilled vegetable liquid fatty acid 95-98% free oleic. | Undiluted liquid | .5 to 2.0 | A fatty acid promoter-collector for flotation or fluorspar |
Ethyl Silicate | (C2H2)4SiO4. Water will hydrolize it to pure SiO2 | Undiluted liquid | .05 to .25 | Similar in action to sodium silcate but for acid or neutral circuits where pH is critical. |
Eucalyptus Oil | An oil extracted from eucalyptus tree. | Undiluted liquid | .05 to .20 | Frother used in place of pine oil in tropical countries. |
Ferric Sulphate | A water soluble iron salt. Fe2(So3) 4 plus water. | 10-20% solution. | .5 to 1.5 | Activates arsenopyrite and tetrahedrite in presence of cyanide and zinc sulphate. Permits floating these minerals from sphalerite. |
Fish Oil Fatty Acid | A mixture of saturated and unsaturated fatty acids. Pasty and insoluble in water. | Undiluted or with fuel oil. | .5 to 1.5 | Anionic collector. A promoter and frother similar in action to oleic acid. |
Flexricin 9 | Propelene glycol monoricinoleate. Clear viscous liquid. | Undiluted or emulsion | 05 to 2.0 | Highly polar. Flotationof non-metallic a nd oxide minerals. |
Fluorspar | Finely ground acid grade calcium fluoride. CaF2 | Dry | 1.0 to 3.0 | Used with sulphuric acid to release fluoride ion required in selective flotation of feldspar from quartz. |
Fuel Oil | Petroleum oils of various grades. | Undiluted liquid | .5 to 2.5 | Used for froth control and also in flotation of various metallics and non-metallics. |
Glue | An organic colloid powder. | 5% water solution | .1 to .5 | Depressant and slime regulator. |
Galactasol | A food grade guar gum-dry powder flakes. | 1% water solution with Preservative. | 0.1 to 0.5 | Excellent slime flocculent and settling aid. |
Guartex | Industrial grade guar gum-dry powder flakes. | 1% water solution with Preservative. | 0.1 to 0.5 | Excellent slime flocculent and settling aid. |
Gum Arabic | A white powder water soluble. | 5-10% solution | .1 to .3 | A good dispersant and depressant for gangue slimes. |
Hydrochloric Acid. | Comercially known as muriatic. Approx, 32% HCl. | Undiluted liquid | .5 to 5.0 | To lower pH when necessary to float in acid circuit. |
Hydrofluric Acid. | Comercial 60% HF. Very corosive. | Undiluted 10% solution. | .5 to 4.0 | Extensively used in selective flotation of feldspar from quartz. Depresses mica. |
Hydrogen Sulphide | H2S gas or saturated water solution. | Gas or water solution. | .25 to 1.0 | Sulphidizing agent from oxide minerals. Most effective in nascent forms from Ca or Na-polysulphide and sod-bicarbonate. |
Indusoil | Refined tall oil. Mixture of fatty and rosin acids. | Undiluted liquid | 0.5 to 2.0 | Substitute for oleic and other fatty acids for floating non-metallic minerals and oxides. |
Invadine | Sodium alkylbenzenesulfonate. Light tan powder. Water soluble. | 5-10% solution. | .2 to .5 | Wetting agent. |
Kerosene | A water white distillate from petroleum. | Undiluted or emulsion | .5 to 2.5 | Promoter for coal and graphite. Best when emulsified with Emcol X-25 or similar reagents.Floats ink from paper pulp. |
Lactic Acid | C3H3O3. Colorless liquid. | Undiluted liquid | .25 to 1.0 | Depressant for mica. |
Lead Nitrate | A white crystalline water soluble salt Pb(No3)2 | 5-10% solution. | .5 to 1.5 | Activator in flotation of sodium chloride from potash salts. Activates stibnite. |
Lime | Calcium hydroxide. White powder. Solubility 2.6 lbs. per ton of water. | Slurry or dry. | 1.0 to 10.0 | An alkalinity modifier regulator and depressor of pyrite. Used extensively in lead-zinc flotation. |
Liqro | A Crude tall oil, bi-product from paper pulp manufacture. | Water emulsion | .5 to 2.5 | Contains fatty and resin acids and is used as a substitute for oleic acid in flotation of non-metallics. |
Lintz Reagent R-52 | A surface active agent dry powder. Non-toxic. | 4% water solution. | 1.0 to 5.0 | An excellent flocculating agent useful in thickening and filtering. |
Manganese Sulfate | MnSO4-Reddish. | 5-10% water solution. | 1.0 to 5.0 | Activator in flotation of manganese dioxide. |
Mahogany Sherosope F-445 | A dark brown of viscous liquid. Sodium salt of crude or refined petroleum sulfonic acids. | 5% solution. | .1 to .5 | Has been used to float metallic and oxide copper ores. Also good to float carbonaceous or graphitic impurities from lead-zinc ores. |
Marsperse CB | A water soluble ligno sulfonate. | 5-10% solution | .1 to .5 | A dispersing agent similar in action to Quebracho. Used in phosphate flotation. |
Methyl Amyl Acetate | A water white liquid with a high boiling point. | Undiluted liquid | .05 to .10 | Produces a very brittle froth. Similar in action to methyl amyl alcohol. |
Methyl Amyl Alcohol | A medium high boiling alcohol. Water high liquid. | Undiluted liquid | .05 to .10 | An excellent frother for selective flotation of metallics and non-metallics. Brittle forth. |
Methyl Isobutyl Carbinol | A higher alcohol water white liquid. | Undiluted liquid | .05 to .10 | An excellent frother for selective flotation of metallics and non-metallics. Produces a brittle forth. |
Metso | Sodium metasilicate pentahydrate. Approx. 57.5% Na2SiO3. | Dry or 10% solution. | .5 to 1.5 | A substitute for sodium silicate as a gangue dispersant. Does not raise pH abnormally. |
Micate | A dry powder soap made from tall oil. 50.5% sodium oleate, 38% sodium abietate. | 5% water solution | .5 to 1.5 | Flotation of non-metallics. |
Minerec A | Dixanthogen (diethyl dithiobis thionoformate). Light yellow liquid. | Undiluted to grinding circuit. | .05 to .25 | An effective sulfide promoter in either acid or alkaline circuits. An excellent copper reagents. |
Minerec B | Similar to Minerec A. | Undiluted to grinding circuit. | .05 to .25 | Especially adapted to flotation of copper and gold ores in lime circuit. Non-frothing promoter. |
Minerec 27 | Similar to Minerec A & B | Undiluted liquid | .05 to .25 | Powerful and selective collector for flotation of copper ores. |
Nacconol NR | White flaky solid. Sodium alkylated aryl sulfonate. | 1-5% solution. | – to .5 | A neutral surface active wetting agent possessing frothing and collecting properties for talc and similar non-metallics. |
Naphtha Solvent | Commonly known as Stoddard’s solvent. Water white liquid. | Undiluted liquid | .5 to 1.5 | Modifying agent when used with Tallso and other fatty acids in flotation of ilmenite and rutile from beach sand. |
Naphthenic Acid “D” | A petroleum bi-product. | Undiluted liquid | .5 to 2.0 | A frother and promoter for flotation of potash salts, barite, magnesite and various other non-metallics. |
Naphthenic Acid “P” | A petroleum bi-product dark colored liquid. | Undiluted liquid | .5 to 2.0 | Same as Napthenic Acid D. |
Neofat 42-12 (formerly S-142) | Tall oil fatty acids single distilled. | Undiluted liquid or emulsion | .20 to 2.00 | Anionic collector for non-metallics such as fluorspar, barite, beryl, magnetite, hemotite, calcite, spodumene, phosphate. |
Neofat 42-06 (formerly D-142) | Tall oil fatty acids double distilled. | Undiluted liquid or emulsion | .20 to 2.00 | Anionic collector for non-metallics. Same as above. |
Oleic acid | A fatty acid commonly known as Red Oil. | Undiluted liquid | .5 to 2.0 | One of the most common promoter-collectors for flotation of non-metallic minerals. Used extensively for fluorspar. |
Oronite Wetting Agent | A viscous brown paste. Petroleum bi-product. | Water solution | .1 to 1.0 | Wetting agent in non-metallic flotation. |
Orso | A blown neutral shop of vegetable origin containing about 40% moisture | 1-2% solution | .2 to 1.0 | Promoter and collector for scheelite and other tungsten minerals. |
Orthotoluidine | A brownish black liquid. Very fluid. | Liquid | See TT mixture | A frother and froth modifying agent. Excellent for mixing with cresylic or pine oil. |
Pentasol Frother No. 26 | An amyl alcohol of special distillation range. | Undiluted liquid | .05 to 0.20 | A frother and froth modifying agent. Excellent for mixing with cresylic acid or pine oil. |
Pine Oil Yarmor “F” | A standard high grade pine oil of uniform consistency, steam distilled. | Undiluted liquid | .05 to 0.20 | An extensively used frother for bulk and selective flotation of sulphide minerals. |
Potassium Permagnate | KMnO4, crystalline solid | 5% water solution | .1 to 2.0 | A selective sulfide depressant. |
Quebracho | A tannic product containing approximately 70% tannic acid. Dry brown powder. | 5-10% solution | .05 to .30 | An excellent depressor for calcite in fluorspar flotation. Also depressant for wolframite when floating sulphides. |
Reagent 301 | An xanthate of a higher petroleum alcohol similar to Z-8. Light yellow powder. | 10% solution | .05 to .15 | Promoter for sulphide and oxidized base metal ores the latter after sulphidizing. |
Reagent 322 | A higher xanthate similar to Reagent 343. | 10% solution | .05 to .15 | Strong promoter for all sulphide minerals. |
Reagent 325 | An xanthate made from a lower alcohol than Reagent 301. | 10% solution | .05 to .15 | Strong promoter for bulk flotation of sulphide minerals. |
Reagent 343 | An higher xanthate similar to Reagent 301. | 10% solution | .05 to .15 | Strong promoter for all sulphide minerals. Promoter activity between ethyl xanthate and Reagent 301. |
Reagent 404 | Mercaptobenzthiazole. Greenish yellow water. Soluble pasty solid. | 5% solution | .2 to .5 | Promoter for oxidized base metal ores. Also used for flotation of vanadium and auriferous pyrite ores. |
Reagent 425 | A yellow to greenish yellow hydroscopic powder. | 5% solution | .2 to .5 | Developed primarily for flotation of oxidized copper ores. Promoterfor malachite and azurite without sulphidization. |
Reagent 444 | A yellow water soluble powder. | 5% solution | .2 to .5 | An effective promoter for copper and zinc sulphide ores. |
Reagent 610 | A dark colore powder. Slightly hydroscopic. | 2-5% solution | .10 to 1.0 | A slime and gangue dispersant; aids production of clean concentrates. |
Reagent 645 | A dark colore powder. Slightly hydroscopic. | 2-5% solution | .10 to 1.0 | A depressant for carbonaceous gangue, also arsenic and antimony sulphides. |
Reagent 710 | A fatty acid of vegetable origin. Dark brown to brownish black liquid. | Undiluted if kept warm. | .5 to .20 | Used as a substitute for oleic acid and other fatty acids for flot. of phosphate, fluorspar, and barite, replaces Reagent 708. |
Reagent 712 | A clear amber to dark brown pasty liquid. Water soluble. | 5-10% solution | .05 to 0.50 | A secondary promoter and frother for flotation of base metal precious metal, and non-metallic ores. Floats middlings. |
Roccal 50% | A high molecular alkyldimethyl-benzyl-ammonium chloride. Sanitizing agent. Germicide | 10% solution | .01 to .02 | Useful floating bacteria, and solids from water. Non toxic 10 parts per million usually sufficient. |
Rosin Amine D-Acetate (RADA 80%) | A primary amine acetate. Water soluble. Also available in 50% and 70% aqueous grades. | 1-5% water solution | .05 to 1.0 | A strong cationic collector for flotation of non-metallic minerals. Mica, quartz, and feldspar. |
Reagent 801 | Dark colored viscous liquid petroleum sulfonic acids. Water soluble up to 30%. | 10-30% water solution | .5 to 3.0 | Promoter for flotation of non-metallics, calcite, barite, tungsten, garnet, and iron ores. |
Reagent 825 | Dark colored viscous liquid or paste. Petroleum sulfonic acids. | 5-12% dispersion in water | .5 to 3.0 | Strong promoter similar to 801. More selective on some ores often mixed with 801. |
Red Oil | Same as oleic acid. Commercial grade, low titre oleic-linoleic acids. | Undiluted | .5 to 2.0 | Anionic collector. See oleic acid. |
Sapamine MS | A cationic reagent. Clear liquid. | Undiluted | .1 to .3 | Promoter in floating silica from gypsum. Also useful in flotation of iron ores. |
Soda Ash | Na2Co3. White water soluble powder. “Trona”. | Dry or 10-20% solution | 1.0 to 5.0 | A widely used alkalinity regulator in selective flot. of lead-zinc ores. Also used in bulk and non-metallic flot. |
Sodium Aero float B (Now Aerofloat 211) | A water soluble granular gray powder. Sodium diethyl dithiophosphate. | 5-10% solution | .5 to 2.0 | A powerfyl selective zinc promoter also used in flot. of gold, silver and copper from pyrite. Non-frothing. |
Sodium Bicarbonate | NaHCO3. Water soluble white powder commonly known as baking soda. | Dry or 10-20% solution | .05 to .20 | Same general use as soda ash.In some cases improved results warrant its use. pH buffer. |
Sodium Bisulphite | A white to yellow powder. Na2S2O5 | 10% solution | .5 to 2.5 | Similar in use to sodium sulphite as a depressant. |
Sodium Dichromate | Orange crystalline powder. Na2Cr2O7.2H2O | 5-10% solution | 1.0 to 5.0 | See dichromate. Sulfide depressant. |
Sodium Ferro-cyanide | Na4Fe (CN)6. 10H2O Crystalline powder. | 5% solution | .1 to 2.0 | Useful in floating molybdenite from bulk copper concentrates. A selective depressant for sulfides. |
Sodium Fluoride | NaF. Insoluble white powder | Dry | .5 to 1.5 | May be used with sulphuric acid in flotation of non-metallics in place of hydrofluoric acid. Ilmenite and fluorspar flotation. |
Sodium Hydro-sulphide | Light yellow crystalline solid approx. 72% NaHS. Sodium sulphydrate | 5-10% solution | .5 to 1.0 | Sulphidizing agrent used in place of and at times more effective than sodium sulphide. |
Sodium Hydro-sulphite | A white powder. NaHSO2 | 5-10% | .1 to 1.5 | Similar in action to sodium sulphite as depressant. |
Sodium Metasilicate | Commonly known as “metso” | Dry to 10% solution | .5 to 1.5 | See Metso. |
Sodium Oleate | A fatty acid soap. Made from oleic acid and sodium hydroxide. | 1-2% solution | .5 to 2.0 | A promoter for oxides and non-metallic. Sometimes more effective than oleic acid. |
Sodium Polysulphide | Solid form of sodium polysulphide. Water soluble. | 10% solution | .5 to 3.0 | A sulphidizing agent for oxide lead minerals similar in action to calcium polysulphide. |
Sodium Silicate | Commonly known as water glass. Usual grade is 41° Baume. | 10% solution | .5 to 3.0 | A depressant for gangue slimes and siliceous gangue minerals in sulphide and non-sulphide flotation. |
Sodium Palconate | The unrefined soluble product which results when redwood bark is cooked with sodium hydroxide. | Water dispersion | 0.1 to 0.5 | Calcite depressant. Similar use to quebracho. |
Sodium Palcosulfonate (Palcotan) | The unrefined product which results when redwood bark is cooked with sodium sulfite. | 5-10% Water dispersion | 0.1 to 0.5 | Calcite depressant. Similar use to quebracho. |
Sodium Silicofluoride | Na2SiF6. Slightly soluble white granule solid. | Dry | .5 to 2.5 | Depressant for quartz and feldspar in flotation of spodumene. |
Sodium Sulphide | A reddish brown flaky water soluble solid. Na2S. 9H20 | 10% solution | .5 to 3.0 | Used to sulphidize lead and copper ores. Depressant for silver sulphide minerals and metallic gold. |
Sodium Sulphite | Na2SO3. White granular water soluble solid. | 10% solution | .1 to 5.0 | Depressant for zinc and iron sulphides. Used in place of cyanide particularly in ores containing silver. |
Sodium Tetra Pyrophosphate | Na4P2O7. 10H2O. White granular solid. | 5-10% water solution | 05 to 3.0 | Has been used as a depressant for calcite in flotation of magnesite with napthenic acid. Dispersant. |
Starch | Usually a white granular solid. Most effective when causticized. | 1-5% solution | .05 to .30 | Floccculating agent and aids in depressing slime gangue when floating sulphides. |
Reagent | Description | Usual Feeding Method | Typical Dosage lbs/ton | Uses |
Sulphuric Acid | H2SO4. Strong acid. Common name of vitriol. | Undiluted or as 10% solution | .5 to .2.0 | Used to reactive pyrite after being depressed by lime or cyanide. Lowers Ph. Depress quartz. |
Sulphurous Acid | H2SO3. Available commercially as SO2 in liquid form. | Gas or saturated sol. | .5 to 2.0 | To acidify flotation pulps and reactive pyrite. Substitute for sulphuric acid when source of supply permits. |
Syntex L | Sulphated mono-glyceride of cocoanut oil derivation. Powder. | 5-8% solution | .01 to .10 | Frother and promoter for molybdenite and its use permits greater selectivity. |
Sonneborn Reagents (1-2-3) | Petroleum sulfonates. Dark colored viscous liquids. | Water solution emulsion | 0.5 to 3.0 | Non-metallic collectors for phosphate, barite, feldspar, fluorspar, manganese oxides. |
Tannic Acid | Tannin C76H52046. Light brown powder. | 5% solution | 0.05 to 0.30 | Depressant for calcite. Can be used in place of quebracho but is more expensive. |
Tall Oil | See liqro and Indusoil. | Undiluted or emulsion | .5 to 2.5 | Used as a substitute for oleic acid and other fatty acids in flotation of non-metallics. |
Tergitol Dispersant NPX (formerly NPG-101) | Non-ionic surface active dispersant. Mixture of alkyl aryl polyglycol ethers. | Undiluted liquid | .05 to .30 | A wetting agent used in paper pulp flotation to depress cellulose fibers when de-inking. |
Tergitol Penetrant No. 4 | Sodium lauryl sulphate: A surface active wetting agent. | 5-10% solution | .25 to .75 | A wetting agent useful as a frother and collector in non-sulphide flotation. |
Tergitol Wetting Agent No.7 | A surface active wetting agent. | 5-10% solution | .25 to .75 | A wetting agent useful as a frother
and collector in non-sulphide flotation. |
Terposol No. 3 | Mixture about 60% terpinyl methyl ethers balance tertiary terpene alcohols. | Undiluted liquid | .05 to .2 | Good frother with very little collecting properties. |
Thiocarbanilide | A white fluffy powder insoluble in water. 1,3-Diphenyl 2-thiorea. | Dry to grinding mill | .05 to .10 | A good promoter for lead, zinc, copper and silver ores. Excellent for selective flotation of sulphides. |
Thiocarbanilide 130 | A cream to white dry powder. Wettable. | Dry or 5-10% slurry | .05 to .10 | Same general use as thiocarbanilide but more dispersible. |
Tragacine Powdafloc | A starch base powder. | Make paste then dilute to 2-10% solution. | 1.0 to 1.5 | Flocculating agent settlement of slimes. |
Tri-Sodium Phosphate | Na3PO4. 12H2O. Water soluble. White solid. | 5-10% solution | .5 to 3.0 | An alkaline detergent and water softener useful in flotation of non-metallics. Slime dispersant and depressant. |
Triton k-60 | Dimethyl cetyl benzyl ammonium chloride. Aqueous solution. | Undiluted | .10 to .30 | A cationic collector for non-metallic minerals. |
Trostol | A crude tall oil product. Approximately 48% rosin acids and 52% fatty acids. | Undiluted or emulsion | .5 to 2.5 | A substitute for oleic and other fatty acids as a collector for non-metallic minerals. |
TT Mixture | Made by dissolving not more than 15% thiocarbanilide in hot orthotoluidine. | Undiluted (hot) mixture. | .25 to .50 | A good promoter of lead, copper and silver ores. Thiocarbanilide solubility increased in this form. |
Turkey Red Oil | Sulphated and sulfonated castor oil. Viscous. | Undiluted or emulsion | .5 to 1.5 | Promoter and frother similar in action to oleic acid. |
Ultrawet DS | Dry powder. Sodium alkyl aryl sulfonate 85% active. | 10-20% solution | .05 to .30 | An anionic wetting and dispersing agent. Also an excellent frother-collector for talc and steatite. |
Ultrawet 30-DS | A 30% aqueous solution of ultrawet DS. | 10-20% solution | .10 to .60 | Same as ultrawet DS. Aqueous solution. |
Vapor Oil | A pale neutral petroleum hydrocarbon oil low in paraffin wax. | Undiluted liquid | .25 to 1.0 | Flotation of molybdenite used with pine oil and Syntex L. |
Wattle Bark Extract | A tannin product similar to quebracho. | 5-10% solution | .05 to .30 | Calcite depressant when floating fluorite with fatty acids. |
Xanthate Z-3 | C2H3OCSSK. Potassium ethyl xanthate, yellowish gray pellets. | 10% solution | .05 to .30 | One of the most widely used collectors for bulk flotation of copper and other complex sulphides. |
Xanthate Z-4 | C2H3OCSSNa. Sodium ethyl xanthate. Pale yellow pellets. | 10% solution | .05 to .30 | Same as Z-3 but preferred by some on account of its higher xanthate content. |
Xanthate Z-5 | C5H11OCSSK. Potassium sec amyl xanthate. Yellowish brown pellets. | 10% solution | .01 to .20 | A powerful collector and flocculator for flotation of slow floating and semi-oxidized sulphides. |
Xanthate Z-6 | C5H11OCSSK. Potassium amyl xanthate. Grayish pellets. | 10% solution | .01 to .20 | Collector power of the same order as Z-5. Excellent for metallic gold arsenopyrite, and slow floating sulphide minerals. |
Xanthate Z-8 | C4H9OCSSK. Potassium sec butyl. Dark yellow pellets. | 10% solution | .01 to .20 | Superior to Z-9 in collecting power. Excellent for tarnished sulphide minerals or metallics. |
Xanthate Z-9 | C3H7OCSSK. Potassium isopropyl xanthate. Slightly yellow gray pellets. | 10% solution | .05 to .30 | Collector of lead-zinc-iron sulphide ores. Superior collecting power and selectivity toward pyrite in cleaner circuits. |
Xanthate Z-11 | C3H7OCSSNa. Sodium isopropyl xanthate. Yellowish white pellets. | 10% solution | .05 to .30 | Lead-zinc selective flotation. Improved selectivity. |
YellowDexthrine | A yellow amorphous powder. A starch product. | 10% solution | .1 to .3 | Slime and insoluble depressant in flotation of copper and other metallic sulphides. Add to cleaners. |
Zinc Hydrosulphite | A water soluble white powder. | 10% solution | .5 to 1.5 | Depressant similar in action to sodium sulphite. Best in acid circuit. |
Zinc Sulphate | A white granular water soluble powder. | 5-10% solution | .5 to 1.5 | Depressant for pyrite and sphalerite in selective flotation of lead, zinc and copper ores. |
Flotation Chemical and Reagents
Absorbents and adsorbents | Sodium ferrocyanide | Ferric sulfate | Anthracite, bituminous, lignite carbon |
Activated alumina | Sodium fluoride | Inorganic flocculants | Diatomaceous earth |
Activated carbon | Sodium hydrosulfide | Lime | Perlite |
Coconut shell carbon | Sodium hydroxide | Non-ionic polymers | Specialty filtering aids |
Ion exchange resins | Sodium metasilicates | Organic flocculants | Specialty flocculants |
Molecular sieve | Sodium silicates | Specialty flocculants | Surfactants |
Perlite | Sodium sulfide | Collectors | Frothers |
Silica gel | Sodium zinc cyanide | Absorbents | Alcohols |
Acids and acid cleaners | Specialty and commodity activators | Activated carbon | Custom blends |
Acetic acid | Sulfur dioxide | Alcohols | Flotation oil |
Custom blends | Sulfuric acid | Amines | MBC |
Fatty acids | Surfactants | Coconut shell carbon | Pine oil |
Formic acid | Tall oil | Cresylic acid | Specialty frothers |
Gluconic acid | Thionocarbamates | Custom blends | Gas treating |
Hydrochloric acid | Xanthates | Dextrin | Gas treating |
Hydrofluoric acid | Zinc sulfate | Dithiophosphates | Absorbents |
Hydroxyacetic acid | Alcohols | Fatty acids | Activated aluminum |
Lactic acid | Butanol | Flotation oil | Activated carbon |
Leaching chemicals | Custom blends | Ion exchange resins | Alcohols |
Nitric acid | Cyclohexanol | Mercaptobenzothiazole | Amines |
Oleic acid | Isobutanol | Organic sulfonates | Ammonia |
Organic sulfonic acid | Isodecanol | Specialty collectors | Ammonium hydroxide |
Oxalic acid | Isopropanol | Tall oil | Custom blends |
Phosphoric acid | Methanol | Thionocarbamates | DEA |
Sulfamic acid | MIBC | Thiophosphate collectors | Defoamers |
Sulfuric acid | Propanol | Xanthates | Moleccular sieve |
Activators, modifiers and depressants | Specialty alcohols | Xanthogen formats | Monoethanolamines |
Fatty acids | Bases | Crystal growth modifiers | Pottasium hydroxide |
Ferric chloride | Caustic soda | Alkyl aryl sulfonates | Silica gel |
Ferric sulfate | Lime | Sodium ferrocyanide | Soda ash |
Ferrous sulfate | Magnesium oxide | Defoamers | Specialty solvent |
Hydrochloric acid | Potassium hydroxide | Silicone defoamers | Urea |
Hydrofluoric acid | Soda ash | Specialty defoamers, numerous | Alkyl aryl sulfonates |
Hydroxyacetic acid | Chelating agents | Tributyl phosphate | Polypropylene glycols |
Lead acetate | Citric acid | Electrolytic refining chemicals | Ion precipitants and metal value recovery aids |
Lead chloride | Custom blends | Absorbents | Activated aluminum |
Lead nitrate | DETA | Ammonium chloride | Activated carbon |
Litharge | EDTA | Manganese dioxide | Activated carbon, coconut shell |
Lignin sulfonate | Hydroxyacetic acid | Organic sulfonates | Carbon, anthracite bituminous, lignite |
Mercaptobenzothiazole | Sodium cyanide | Potassium carbonates | Diatomaceous earth |
Non-ionic polymers | Coagulants and flocculants | Potassium permagnate | Ferric chloride |
Organic sulfonates | Alum | Strontium carbonate | Ferric sulfate |
Organic sulfonic acid | Anionic polymers | Filtering aids | Ferrous sulphate |
Oxalic acid | Cationic polymers | Absorbents | |
Potassium permagnate | Cresylic acid | Activated aluminia | |
Soda ash | Custom blends | Activated carbon | |
Sodium cyanide | Ferric chloride | Activated carbon, Coconut shell |
Other Mining Reagents and Chemicals
Ion precipitants and metal value recovery aids (continued) | Slurry viscosity reducers | Tributyl phosphate | Hydrochloric acid |
Floor dry | Custom blends | Triethanolamine | Hydrofluoric acid |
Lead acetate | Dispersants | Surfactants | Hydrogen peroxide |
Lead chloride | Glycols | Carbon blanking agents | Hydroxyacetic acid |
Lead nitrate | Sodium hexametaphosphate | Custom blends | Inhibitors-corrosion |
Methanol | Sodium silicates | Defoamers | Inorganic flocculants |
Sodium sulfide | Sodium tripolyphosphates | Dispersants | Iodine |
Zinc dust | Specialty viscosity reducers | Emulsifiers | Ion exchange resins |
Machinery maintenance, repair and operation | Surfactants | Surface tension modifiers | Lime |
Absorbents | Smelter chemicals | Wetting agents | Magnesium hydroxide |
Activated aluminia | Absorbents | Water treatment | Magnesium oxide |
Activated carbon | Acids | Absorbents | Molecular sieve |
Coconut shell carbon | Activated alumina | Acetic acid | Muriatic acid |
Alcohols | Activated carbon | Acids | Nitric acid |
Antifreeze, glycol-based | Ammonium chloride | Activated carbon | Non-ionic polymer |
Calcium chloride | Antimony potassium tartrate | Alum | Organic flocculants |
Carbon tetrachloride | Arsenic trioxide | Aluminum chloride | Perlite |
Custom blends | Barium carbonate | Aluminum potassium sulfate | Phosphoric acid |
Dedust agents | Bone glue | Amines | Potassium iodide |
Detergents | Borax | Ammonia | Potassium permagnate |
Glycols | Caustic soda | Ammonium silicofluoride | Silica gel |
Inhibitors – corrosion | Copper arsenate | Ammonium sulfate | Silicone defoamers |
Mineral oils | Copper sulfate | Anionic polymers | Slurry viscosity reducers |
Specialty solvents | Custom blends | Ammonium hydroxide | Soda ash |
Trisodium phosphate | Fluorspar | Barium carbonate | Sodium aluminate |
Urea | Lead chloride | Barium chloride | Sodium bicarbonate |
Mining and ore digging aid | Manganese dioxide | Bases | Sodium bisulfite |
Antifreeze, glycol-based | Mineral oils | Bentonite clays | Sodium carbonate |
Calcium chloride | Mold release agents | Biocides | Sodium chlorate |
Conveyor belt antifreeze | Silica gel | Bleach | Sodium chloride |
Custom blends | Silica sand | Boiler water treatment | Sodium chlorite |
Dedust agents | Soda ash | Bromine | Sodium chromate |
Detergents | Sodium nitrate | Calcium fluoride | Sodium fluoride |
Methanol | Sodium silicates | Calcium hydroxide | Sodium hexametaphosphate |
Sodium chloride | Strontium carbonate | Calcium hypochlorite | Sodium hydroxide |
Pelletizing aids | Sulfamic acid | Calcium oxides | Sodium metabisulphite |
Bentonite clays | Sulfur | Carbon, anthracite, bituminous, lignite | Sodium nitrate |
Custom blends | Thiourea | Cationic polymers | Sodium phosphate |
Pumping, shipping & storage aids | Zinc dust | Caustic soda | Specialty flocculants |
Antifreeze, glycol-based | Solvent extraction | Chelating agents | Sulfamic acid |
Calcium chloride | Acids | Chlorine | Sulfur dioxide |
Conveyor belt antifreeze | Alcohols | Citric acid | Sulfuric acid |
Custom blends | Chelating agents | Copper sulfate | Surfactants |
Dedust agents | Cobalt sulfate | Cresylic acid | Terra sodium pyrophosphate |
Glycols | Custom blends | Custom blends | Tricalcium phosphate |
Lignin sulfonate | Defoamers | Defoamers | Trisodium phosphate |
Silicone defoamers | Diluents, specialty | DETA | |
Slurry viscosity reducers | Ion exchange resins | Diatomaceous earth | |
Surfactants | Isodecanol | Disodium Phosphate | |
Leaching chemicals | Dispersants | ||
Mineral oils | Ferric chloride | ||
Monoethanolamines | Ferric sulfate | ||
Specialty solvent | Ferrous sulfate | ||
Sulfuric acid | Hydrazine |
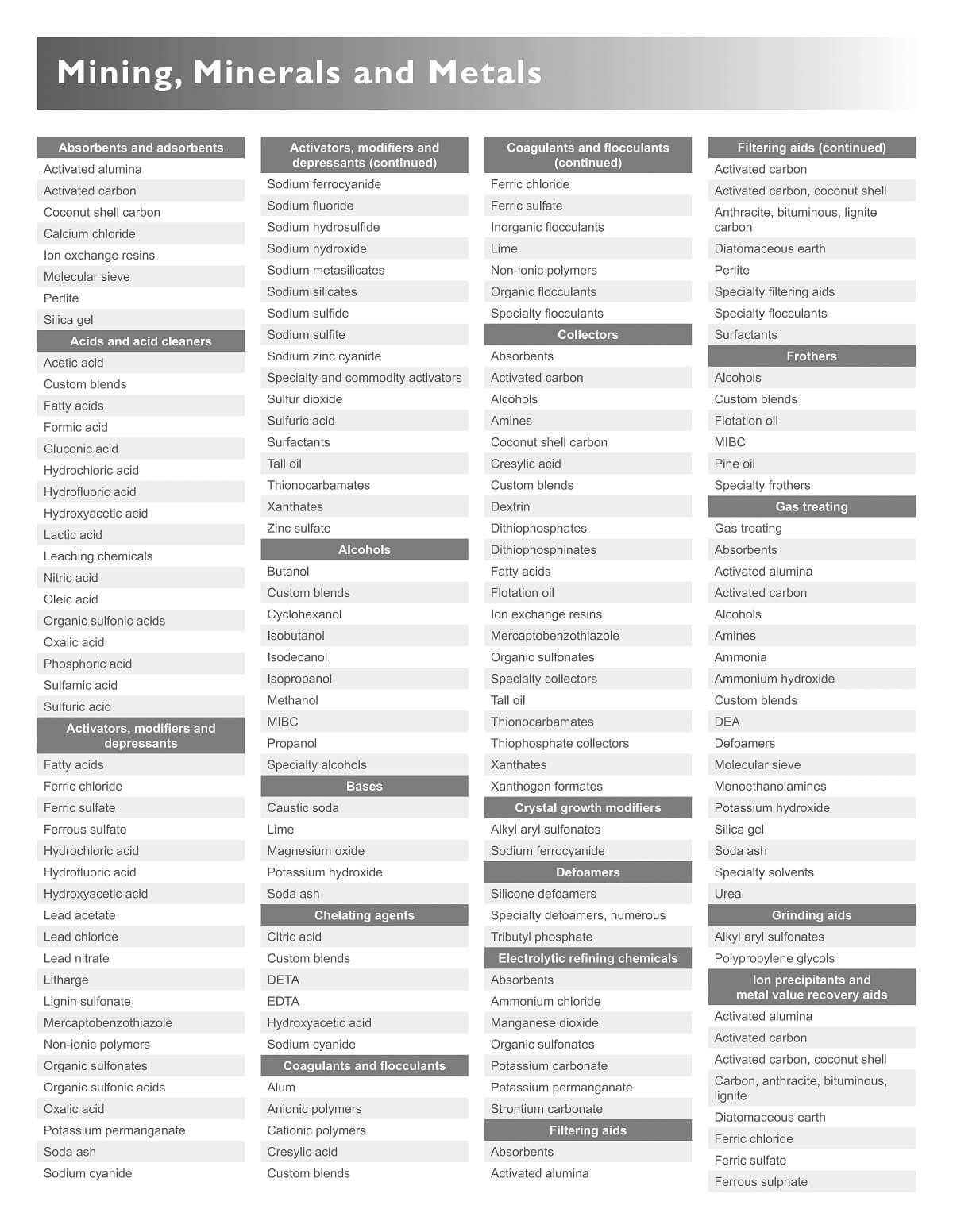
Flotation Reagent Manufacturers
Flotation Reagent Suppliers
Gold Mining Chemicals
Source: This article is a reproduction of an excerpt of “In the Public Domain” documents held in 911Metallurgy Corp’s private library.
A series of simple math models have been developed to assist in the engineering analysis of batch lab data taken in a time-recovery fashion. The emphasis is to separate the over-all effect of a reagent or operating condition change into two portions : the potential recovery achievable with the system at long times of flotation, R, and a measure of the rate at which this potential can be achieved, K.
Such patterns in R and K with changing conditions assist the engineer to make logical judgements on plant improvement studies. Standard laboratory procedures usually concentrate on identifying some form of equilibrium recovery in a standard time frame but often overlook the rate profile at which this recovery was achieved. Study has shown that in some plants, at least, changes in the rate, K, are more important relative to over-all plant performance than changes in the lab measured recovery, R. Thus the R-K analysis can serve to improve the engineering understanding of how to use lab data for plant work. Long term plant experience has also shown that picking reagent systems having higher K values associated can be beneficial even when the plant, on the average, is not experiencing rate of mass removal problems. This is due to the cycling or instabilities that can and do exist in industrial circuits.
It is also important to note that the R-K approach does not eliminate the need for surface chemistry principles and characterization. Such principles and knowledge are required to logically select and understand potential reagent systems and conditions of change in flotation. Without this, reagent selection is quickly reduced to a completely Edisonian approach which is obviously inefficient. What the R-K analysis does is to provide additional information on a system in a critical stage of scale-up (from the lab to the plant) in a form (equilibrium recovery and rate of mass removal) which are interpretable to the engineer who has to make the change work.
The influence of operating conditions such as pH, temperature of feed water, degree of grind, air flow rate, degree of agitation, etc. have been characterized using the R-K approach with clear patterns evolving.
The effect of collector type and concentration on a wide variety of ore types have been studied with generally rather clear and sometimes rather significant patterns in R and K. The quantitative ability to analyze collector performance from the lab to the plant using the R-K profiles has been good.
The effect of frother type on various ores has also been undertaken with good success in differentiating between the qualitative directions and effects involved. However, the actual concentrations required in plants have not, in at least some tests, been accurately predicted. Thus further work remains in this area but in almost all cases the qualitative information on frothers that has been gained has proven very valuable in test work as a guide.