Table of Contents
The next reagent that is added is the Flotation FROTHER. The frother strengthens the surface tension of the air that is injected into the flotation cell. As the air rises in the shape of bubbles, they come into contact with the mineral laden collector which attaches itself to the air. The bubble will continue to rise until it reaches the surface and flows over the side of the cell. While the bubble is rising lets change the different variables and see what effect they have on the bubble.
As the name froth flotation would cause us to expect, an important class of chemical reagents is frothing agents. As is the case with collectors, a wide range of compounds is used, depending on mineral type and operating conditions.
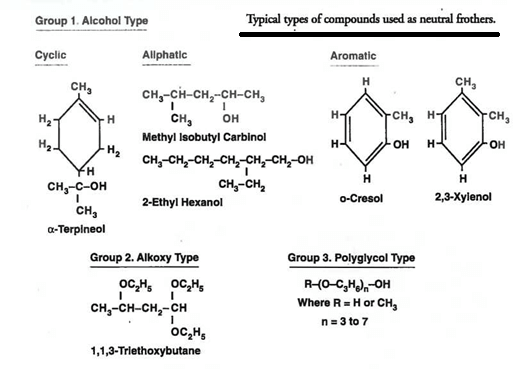
The dosage of frother required in any given application is quite variable, ranging from zero in some systems to 0.3 kg/ton in others. Part of the reason for this variability is that many collectors presented earlier demonstrate some frothing action as well as collecting action. This is particularly true of the nonsulfide collectors.
From a strictly fundamental viewpoint, the actual quantitative role of frothers is difficult to predict. Applied research work has shown that a major role of a frother is to increase the rate of valuable recovery.
This task is accomplished by the formation of a froth of consistent character (a consistent bubble size distribution) under a variety of operating conditions, an increase in the ability to disperse air in the flotation cell, a reduction in the rate of coalescence of individual bubbles in the cell, and a decrease in the rate of bubble rise to the pulp surface. In terms of stability, a successful frother must achieve a delicate balance between the colliding bubble and the particle so that attachment can take place in the time frame of the collision. At the same time, the frother must provide sufficient stability of the bubble-particle kinship to allow the weakly adhering or mechanically trapped particles of unwanted gangue materials to escape with the draining liquid.
Frothers behaves as Soap
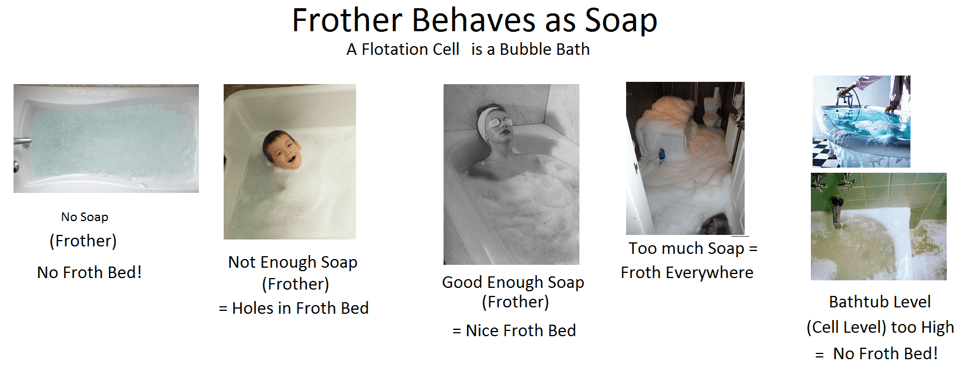
A common feature of most commercial frothers is their heteropolar nature, consisting of a non-ionic polar group (or groups) exhibiting a hydrophilic character coupled with a hydrophobic non-polar character. It is generally accepted that adding a surface-active agent to water lowers the surface tension of the solution due to the heteropolar nature of the molecules.
This result occurs because the molecules are preferentially adsorbed at the air-water interface, with the polar or hydrophilic group situated in the water phase and the non-polar or hydrophobic chain in the vapour phase. Thus, the surface tension of a solution containing frother is a partial indication of the activity of a frother, with chemicals that strongly lower the surface tension often producing more stable (persistent) froths. It will be demonstrated in a later section of this module that the major practical influence of changing frother chemical structure appears to be in the effective particle size range recoverable by that frother.
Frothing Reagents
The manner in which a frothing reagent stabilizes the air-bells in the pulp and the bubbles in the froth, at the same time reducing the surface-energy and therefore the surface-tension of the air/water boundaries, has already been sufficiently explained. It has also been pointed out that the total energy of the air-bell surfaces must not be unduly decreased, since a definite amount is needed for the attachment of the mineral particles which it is desired to float. These factors determine the “ selectivity ” of the reagent. Thus a frother which decreases the energy of the air/water surface very slightly will tend to float a wider variety of minerals, including particles of comparatively low contact-angle value, than one whose adsorption-film has lowered the energy to a high degree ; in the latter case only particles of high contact-angle value will remain attached to the air-bells. Frothers of the first type, of which pine oil is an example, are classed as “ non- selective ”; the others, of which cresylic acid is typical, are termed ” selective “.
As a rule, frothing reagents are liquids which are sparingly soluble in water. They include a wide range of substances from essential oils to compounds such as phenols, cresols, toluidines, etc. Of the many varieties that have been put on the market from time to time, pine oil and cresol are the only two in common use at the present time.
Pine oil is obtained from certain species of pine trees by steam distillation, its main constituent being pinene, which is a terpene having the general formula C10 H16. It is a powerful non-selective frothing reagent and has the advantage that it can be emulsified and dissolved with a very small amount of agitation.
Cresylic acid, or cresol, CH3.C6H4.OH, is a product of the distillation of coal tar. Its active constituents are meta, pyro, and ortho-cresol, but it always contains a small amount of other coal-tar products. It is less powerful and more selective than pine oil.
None of the other frothing reagents that are encountered at times has any wide application. Many of them are more or less local products which are used because they are cheaper than imported oils and frequently contain the active constituents of pine oil or cresol. Thus the Eucalyptus oil, which is made for flotation purposes in Australia from the species Eucalyptus amygdalina, contains about 80% of pinene, the remainder consisting mainly of the aromatic alcohol “ eucalyptol ”. In the early days of flotation many varieties of coal- and wood-tar oils were used, partly for their frothing properties, but chiefly because of their value as collectors. Although the employment of such reagents, particularly coal-tar creosote, is still extensive, they function chiefly as collectors, frothing requirements being met almost entirely by means of pine oil and cresol.
The amount of frothing reagent needed in the pulp is very small. The normal consumption of pine oil in single-stage flotation is between 0.05 and 0.15 lb. per ton of ore entering the plant, that of cresol being between 0.1 and 0.4 lb. per ton.
SURFACE TENSION
Froth Flotation Frothers are chemicals used to strengthen the SURFACE TENSION of an air bubble. They do not create air bubbles. To demonstrate surface tension, fill a glass of water just prior to over flowing, you will notice that the surface of the water actually extends past the lip of the glass.
That is surface tension. In the case of frothers, it is the surface tension of the air bubble that is strengthened. Different flotation frothers will have different properties. They may (Glycol) or may not (MIBC) be persistent, in other words the length of time that the frother will last in the circuit will change depending on the frother. Some circuits need a very persistent frother others don’t. A frother may make the air bubble more elastic (Glycol) or brittle (MIBC) each type again will have a special application.
For effective flotation to take place there were two problems that had to be corrected. The air bubble had to be strong enough to support the weight of the mineral on its surface, and it was also required to be able to withstand the internal pressure caused by the air expanding as it came to the surface of the slurry.
To correct this the surface tension of the bubble had to be strengthened without loss of elasticity, what was finally developed is a range of reagents that have different combinations of strength, flexibility and endurance. In many cases it’ is desirable to have the effectiveness of the frother to deteriorate rapidly. This will help limit frothing problems from developing in equipment further along in the process.
Creating a Froth for Flotation
Important to the flotation process is controlling the surface tension of the interface among the bubbles, the aqueous solution, and the hydrophobed particles. This is achieved by a combination of the design of the flotation machine (called a flotation cell) and the use of a second class of surfactants known as frothers. In a simplified sense, the role of the flotation machine is twofold:
- to maintain an agitated (mixed) pulp in the cell, and
- to introduce air bubbles into the agitated pulp.
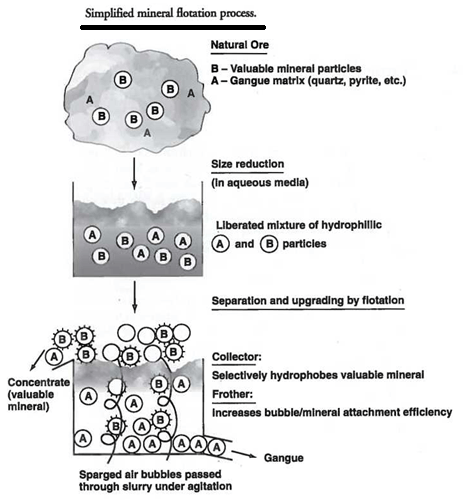
In theory, the actions that take place in a flotation cell are designed to present the most efficient repeated collision frequency between all particles in the pulp and the gas bubbles. Those fine particles that are more hydrophobic should have the greatest probability of attaching to air bubbles and maintaining the attachment. As the bubbles rise in the cell, they carry the hydrophobed particles to the surface of the cell where they can be removed. The major problem with the above description of the performance of the cell is that the bubbles generated by the machine itself have a tendency to coalesce as they rise. This coalescence causes two problems:
- Larger bubbles become weaker; hence, they can break rather easily either from the agitation forces present or because of collisions with the particles themselves; and
- As a given volume of air becomes associated with larger bubbles, the probability of a collision of bubbles with particles is dramatically decreased thus diminishing the effectiveness of the separation process.
To handle this coalescence, a broad family of non-ionic surfactants, denoted as frothers in the flotation literature, is used. Frothers control the dynamic surface tension involving the bubbles, thereby preventing bubble coalescence from occurring to the same extent as without frother. The proper choice of frother chemistry can lead to significant differences in the bubble size distribution present in a cell. It is possible to actually match the particle size distribution of the hydrophobed component to the bubble size distribution created by the frother because each particle size can be recovered optimally by a specified range of bubble sizes. Thus, for example, the broader the particle size range to be recovered, the broader the range of bubble sizes required. As is the case with collectors, the dosage of frother involved in industrial applications is very low, with typical dosages being 5 to 50 grams per ton of mixed solids. Also, to avoid any false intuitive thinking, it is important to realize that many smaller and stronger bubbles are required to float the larger particles. The idea that larger particles are floated by larger bubbles is not correct because of the lower strength of larger bubbles.
Testing Frother Performance
Figure X illustrates a study done on a copper sulfide ore to evaluate the frother performance of MIBC, DF-250, and DF-1012 with constant Z-200 dosage and pH. The results are typical of many studies performed in that R generally increases with increasing frother concentration in the starvation region of concentration but R can pass through a maximum as the frother loading becomes too great. Generally, the value of K increases with frother loading but again can pass through a maximum with high quantities of frother.
The figure also illustrates the often observed higher rate ability of some frother types on a given ore (e.g. in Figure X, the glycol ether type frothers such as DF-250 and DF- 1012 over MIBC), In this example, the relative rate selectivity of copper over gangue stays about the same with the different frothers. However, some improvement in grade should be expected with the glycol ethers over time due to the change in R patterns between copper and gangue. This higher over-all rate capability of some frothers types like the glycol ethers was also demonstrated in a previous study involving coal flotation utilizing R and K analyses. Further work on frother evaluation using the R-K analysis is underway. It appears from progress made to date that plant frother performance is strongly linked to rate as might be expected. However, it should be pointed out that, unlike the lab evaluation of collectors which has provided quantitative plant information, the R-K lab analysis on frothers has sometimes provided only qualitative plant information on concentration. Thus, the relative nature of different frother types has been accurately estimated and proven in the plant but in some cases the concentration required in the plant is not certain based only on lab data.
The importance of using higher rate frothers in plants potentially running under rate control, especially those using Xanthate collectors, can not be over estimated. Figure VI demonstrated the importance in increased plant recovery of the rate control aspects of Z-200 over Z-6 with a fixed frother. The plant trial corresponding to the data of Figure X also demonstrated the same rate control pattern: a 3% increase in measured plant recovery and slightly better grade with DF-1012 over MIBC with a fixed collector despite the apparent similarity in the lab measured copper R values. When there are no obvious differences in the lab R values for copper and gangue for different frothers on a given ore and the plant is definitely not in rate control under normal operation, implication is to use the frother giving the lowest over-all cost (e.g, a natural product or MIBC, etc.) and ignore the K values. As in the case of collectors, the blending of frothers to achieve improved rate character at lower cost may be desirable and is often done in practice. The evaluation of these blends can be done using the R-K approach as previously demonstrated.