Table of Contents
Beneficiation by Flotation of feldspar is well established. It is a simple matter by flotation to remove the contaminating impurities and keep the alumina (Al2O3) content at 19% even on low grade feldspar ores. Dry recovery methods are economically limited to about 17% Al2O3.
The problem in feldspar flotation is to recover slime free granular products, all minus 20 mesh, usually with not over 10% finer than 200 mesh. Flotation under these conditions is critical and pulps are abrasive as well as corrosive. Action of the feldspar pulp must be counteracted by proper selection of equipment to withstand these conditions.
Feldspar is the basic raw material in the manufacture of virtually all burned clay products. It is used in glass, ceramics, pottery, porcelain, enamels, and in securing powders as well as in binders for grinding wheels.
The Feldspar Beneficiation & Flotation Process Flowsheet
The flowsheet illustrated is typical for the average feldspar ore containing quartz, mica, garnet and other iron bearing silicates normally encountered in pegmatites or large dykes of alaskite-granite. Equipment requirements and flotation conditions should always be established by a comprehensive laboratory testing program.
Why is Felstar Important
Feldspar Ore Crushing
Feldspar ore is generally quarried from an open pit deposit and transported to the mill by truck. The flowsheet shows a conventional two stage open circuit crushing system capable of reducing the ore to ¾” which is suitable for further reduction by rod milling. Closed circuit crushing is advisable in larger tonnage operations for maximum grinding efficiency and capacity.
Feldspar Ore Grinding
The Rod Mill is standard for grinding feldspar ore, producing a granular product with a minimum of slime and fine size material. Grinding is always done to minus 20 mesh on account of market requirements. Feldspar this coarse will float very nicely and if liberation is obtained at this size no further grinding is necessary.
Classifying or sizing the rod mill discharge can be done quite efficiently with a Spiral Screen. By operating the rod mill at 25-35% solids partial classification is accomplished in the mill and only the finer fraction discharges onto the spiral screen. Normally the spiral screen oversize is discarded to waste as it will contain coarse pieces of mica and hard particles of quartz with very little feldspar. This waste product may only represent 3 to 5% of the mill tonnage.
Large tonnage operations may require sizing the rod mill discharge through a Dillon Vibrating Screen. In the case of grinds minus 48 mesh and finer a conventional rake or spiral classifier may be used.
Rod Mills with Standard Trunnion overflows and manganese steel grates have given very good service and capacity on feldspar. The grates permit carrying a larger rod charge and also discharge the ground product without excessive production of fines. Slime losses are usually under 10% of the initial mill feed.
Filtering and Drying of Feldspar Concentrate
The feldspar flotation concentrates are dewatered in a Classifier to approximately 20% moisture and further dewatered on a top feed or horizontal vacuum filter down to 7-9% moisture. The balance of the moisture is removed in a Standard Rotary Dryer. The dry product is elevated to storage silos and passed over a 20 mesh Dillon Vibrating Screen to remove possible tramp oversize and scale which finds its way into the feldspar flotation product.
Desliming and Conditioning
The rod mill discharge is deslimed in a Rake Classifier producing a sand and a slime product. The product overflowing the classifier is further deslimed in a Hydroclassifier and its overflow, generally minus 325 mesh, goes to waste. The underflow from the hydroclassifier is metered back to the rake classifier just above the liquid level by a Diaphragm Pump.
This arrangement has worked out very well in plant practice without build-up of critical size material in the system. The Mineral Jig also has an application as a deslimer in this system where sand raking capacity is limited.
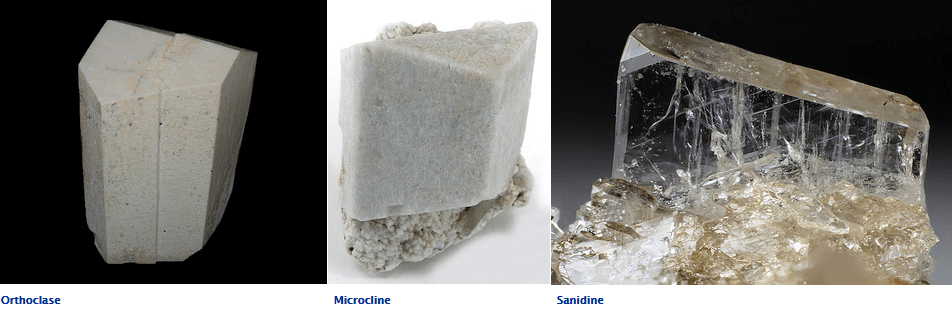
The sand product from the classifier is subjected to high density intense conditioning in a Duplex Heavy Duty Conditioner. This conditioner is the open type and both mechanisms are driven by one motor. The shaft and propeller are rubber covered and the tank is wood to resist the corrosive action of the acid reagents which are introduced into the circuit at this point for subsequent flotation of the mica and iron oxide impurities. Conditioning is normally carried out at 65-70% solids.
Feldspar Flotation
All flotation is carried out in acid circuits, either with sulphuric acid or hydrofluoric acid both of which are highly corrosive to metal parts. For this reason it is necessary to use flotation machines with wooden tanks, partitions, hoods and standpipes, and molded rubber impellers and wearing plates. Conical impellers give the best service in handling the coarse, abrasive, slime-free solids.
In the flowsheet shown, the first bank of “Sub-A” cells removes the impurities. However, in some cases it may be desirable and necessary to float the mica first and then float out the iron bearing impurities including garnets.
After removal of impurities the feldspar-quartz fraction discharging as a tailing product from the primary flotation step is deslimed through a Rake Classifier and the sands conditioned at high density to depress the silica. Feldspar is floated in the last flotation step which is also in an acid circuit with hydrofluoric acid.
Feldspar Flotation Reagents
Often the silica product, due to local conditions, is of commercial value as a by-product. In this case it may be transferred to a drainage bin or silo for storage and market. Mica recovered in the primary circuit, if of sufficient quantity and quality, may be processed further and also marketed as a by-product.
Reagents normally used in feldspar are sulphuric acid, hydrofluoric acid, kerosene, fuel oil, amine acetates such as ARMAC T (also C-CDT and TD amine acetates derived from coconut and tallow fatty acids respectively), and mahogany soap, a petroleum sulfonate. An alcohol frother such as B-23 or Methyl Isobutyl Carbinol may also be used to regulate the character and type of froth. Pine oil may also be used. The amounts and combination of these reagents varies depending upon the character and grade of ore but for average conditions reagent costs are about 75 cents per ton of ore treated. The big reagent item is the hydrofluoric acid which must be used to depress the silica and make it possible to float the feldspar with one of the amine salts at a pH of 2.5-3.0.
For certain market requirements, as in the case of pottery grade, it is necessary to cut the reagent film from the feldspar and thereby make it water wettable. This can be accomplished by conditioning the feldspar concentrate in a Super Agitator and Conditioner ahead of the dewatering classifier and filter. Clays such as Kaolinite or bentonite or a combination of the two have the property of absorbing the reagents condition. The clay with its absorbed reagent can then be washed out in the classifier overflow and discarded as waste. Usually 2 to 5 pounds of clay per ton of the concentrate added to the agitator is sufficient to de-reagentize the feldspar.
Feldspar Beneficiation Process
Feldspar Market Specifications
Standard classification of ground feldspar is set up through co-operation of the (U.S.) National Bureau of Standards, Division of Trade Standards. This classification is effected under Commercial Standard CS 23-30 which covers standard screen tests and standard methods of chemical analysis. There is a physical classification based on fineness of grinding and a chemical classification based on composition as it influences use.
Group 1. includes commonly accepted ceramic or body grade spar, based on silica content and alkali ratio and containing less than 4 per cent Na2O.
Group 2. includes the spars used chiefly for glazing purposes, based on soda content and containing 4 per cent or more Na2O.
Group 3. includes the spars used for glass making purposes, based on silica alumina and iron content.
Feldspar: Three 6-cell No. 18 Special “Sub-A” Acid Proof Flotation Machines with wood tanks and molded rubber parts are used to produce marketable feldspar concentrate in this mill in the southeastern United States.
Production Problems
For all the grades of feldspar, requirements are that the iron content be below 0.10 per cent Fe2O3 and that there be definite ratios of K2O and Na2O to silica. These requirements necessitate ore dressing preparation, and flotation is fast developing into the principal method used.
Reagent Combinations
Stage flotation of de-slimed ground ore is advisable. Mica impurity is first floated with a combination of fuel oil and some amine acetate in a pulp made acid with H2SO4. Second-stage flotation may be preceded by washing and re-conditioning with one of the petroleum sulphonates in a pulp made acid with sulphuric acid to remove additional iron. Third stage flotation with hydrofluoric acid and amine acetate floats the feldspar and leaves a highly siliceous tailing. The first and second stages may be combined if the mica is not to be recovered. Owing to the diversity in mineral content of feldspar deposits, a separate reagent combination needs to be developed for each. Here again, thorough desliming and high-density conditioning are most important for a good separation of feldspar from its impurities.
Typical feldspar flow-sheet, incorporating rod-milling, desliming and flotation. Acid-proof flotation cells and special heavy-duty conditioners are required.
Source: This article is a reproduction of an excerpt of “In the Public Domain” documents held in 911Metallurgy Corp’s private library.