Table of Contents
Aluminum is the most abundant metal in the earth’s crust and is a constituent of many minerals. However, the material which is highest in aluminum and most free from objectionable impurities is bauxite which, therefore, is practically the only source of the metal under present processes.
Bauxite is the general name given to the hydrated oxides of aluminum. It contains varying amounts of combined water and several impurities of which ferric oxide and silica are usually predominant. It is essential that the Al2O3 (alumina) be obtained substantially free from these impurities as otherwise the iron oxide and silica would be reduced and contaminate the metallic aluminum produced in the Hall (or Heroult) Process.
The separation of the alumina from the impurities in the bauxite ore is usually accomplished by the Bayer Process. In this process the ground bauxite is leached with caustic soda (NaOH) to produce soluble sodium aluminate (NaAlO2), leaving the impurities in the insoluble residue. The aluminate solution is then decomposed producing Al(OH)3 which is calcined to produce Al2O3.
Alumina Extraction Problem
In the standard Bayer Process for refining bauxite to produce alumina, the dissolution of the alumina in the ore to form sodium aluminate is accomplished in autoclaves under high pressures varying from 70 to 200 pounds per square inch. However, some lateritic bauxite ores are readily soluble in caustic, making it possible for them to be leached, or “digested,” at atmospheric pressure.
This study deals with the treatment of one such lateritic bauxite ore. Batch laboratory tests showed that a high alumina extraction in caustic could be accomplished at a coarse grind, thus promising low grinding costs, and, of greater importance, a coarse sand residue which could be washed more efficiently, thus keeping soluble loss to only a trace. The optimum grind was found to be minus 3/16″ with 51% plus 32 mesh. However, at this coarse grind and at the desirable pulp density for digestion of approximately 23% solids, the heavy specific gravity solids (3.0 to 3.5) had a settling rate as high as 75 feet per minute. The problem resolved itself to finding some type of continuous mixer or agitator which would keep the coarse, fast-settling solids in homogeneous suspension during the digestion operation so that all of the bauxite particles would be attacked by the caustic sodium aluminate liquor. In this way it would be possible to capitalize on the important advantages of the coarse grind.
Aluminum Extraction Flowsheet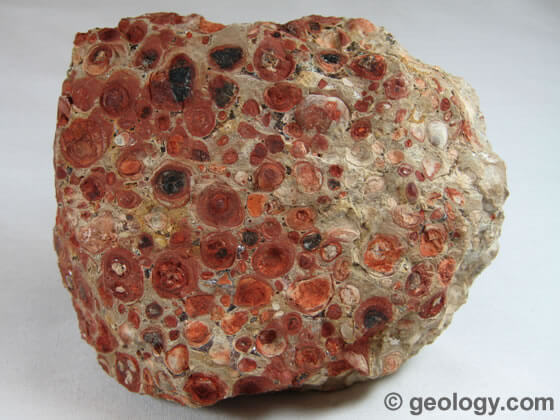
The flowsheet in this study illustrates only the following two steps in the modified Bayer Process:
- grinding and digestion of bauxite in the sodium aluminate liquor,
- separation and washing of the coarse red mud residue from the sodium aluminate liquor. Other major steps in the process are the precipitation of aluminum hydroxide from the sodium aluminate liquor and the calcination of the aluminum hydroxide to produce aluminum oxide (alumina).
In this study the minus 1.5″ bauxite ore is ground to minus 3/16″ in a Steel Head Rod Mill operating in open circuit. The ore is ground wet with hot sodium aluminate liquor at a temperature of 110°C. The rod mill is equipped with water-cooled bearings because of this high temperature.
The rod mill discharges to a Agitator equipped with a turbine type propeller. The agitator acts as a mixing tank to mix the rod mill discharge with caustic soda and sodium aluminate liquor ahead of the digestion circuit. The slurry is pumped from this agitator with a Sand Pump to the digesters for the dissolution of the alumina content of the ore.
The digestion process is accomplished in a series of several Agitators to prevent short-circuiting. As the digestion process continues and the alumina is dissolved, the specific gravity of the solids is actually higher at the discharge point than it is when introduced to the circuit. The bauxite-sodium aluminate slurry is maintained at a temperature of 107°C by means of steam coils around the inside periphery of the covered concrete tanks. The interconnecting piping between the agitators is arranged so that any one agitator acts as a standby and can be by-passed for maintenance.
After digestion the slurry flows to a Hydro-classifier in which classification is effected at 150-mesh. The minus 150-mesh overflow is sent to a series of counter current washing thickeners where the sodium aluminate liquor is separated from the fine-red-mud residue. The plus 150-mesh hydroclassifier underflow is metered by a Adjustable Stroke Diaphragm Pump to a series of Spiral Classifiers where the coarse red mud residue is washed countercurrently. Hot water is added to the last classifier in the series and hot sodium aluminate liquor, recovered from the aluminum hydroxide precipitation step, is added to the next-to-last classifier. This coarse solids washing operation recovers more than 98% of the strong sodium aluminate liquor which was in the coarse red mud residue underflowing the hydroclassifier.
The overflow of the first spiral classifier joins the hydro-classifier overflow, and these products flow to the fine-red-mud washing thickeners mentioned above. The sodium aluminate liquor which overflows the primary thickener is clarified by filtering and the filtrate is decomposed to aluminum hydroxide which is calcined to produce the final alumina product.
In the conventional Bayer Process, due to the fine grind employed, counter current washing of all the residue from the digestion circuit is done in thickeners. A great many large thickeners are required and the soluble loss of sodium aluminate, entrained in the mud, is considerable. However, the coarse grind used in this study allows the use of the spiral washing classifiers to treat approximately 70% of the residue solids from the digesters, resulting in a great reduction in both thickener area requirements and soluble loss of sodium aluminate.
One large alumina plant employing this modified Bayer Process has two parallel grinding and digestion circuits similar to that shown in this flowsheet. The feed rate to each 7 ft. diameter by 12 ft. long rod mill is approximately 95 tons per hour of bauxite ore. The minus 3/16″ product from each rod mill discharges to a 10.5 ft. diameter by 8.5 ft. deep Agitator equipped with a 42″ turbine type propeller consuming approximately 11 H.P.
The slurry from each of these agitators is pumped to a series of nine 22 ft. diameter x 20 ft. deep Digestion Agitators, each of which is equipped with a 96″ diameter turbine type propeller consuming 70 HP. Eight Agitators in each series are operational, with the ninth employed as a stand-by. Each series of eight agitators handles 19,800 gallons per minute of slurry, and the reaction time is three hours.
Results at this plant are excellent, enabling this plant to realize a high alumina extraction with a minimum soluble loss.
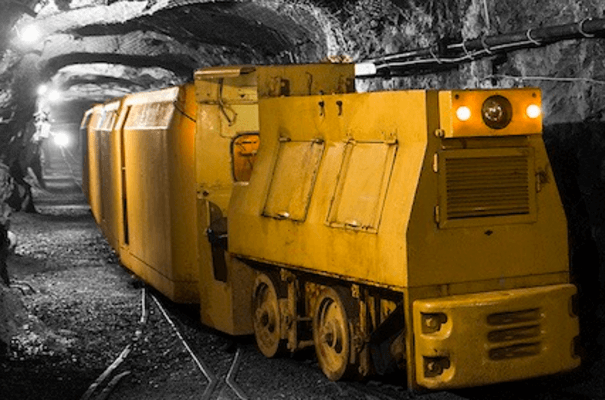
Aluminum Facts
- Atomic Number (number of protons in the nucleus): 13
- Atomic Symbol (on the Periodic Table of Elements): Al
- Atomic Weight (average mass of the atom): 26.9815386
- Density: 2.70 grams per cubic centimeter
- Phase at Room Temperature: Solid
- Melting Point: 1,220.58 degrees Fahrenheit (660.32 degrees Celsius)
- Boiling Point: 4,566 degrees F (2,519 degrees C)
- Number of isotopes (atoms of the same element with a different number of neutrons): 22, one stable
- Most common isotopes: Al-27 (stable) and Al-26 (radioactive; half-life 730,000 years)
From Bauxite to Aluminium
The Bayer Process
https://www.youtube.com/watch?v=EK4dEEoKNiE
Hall or Heroult Process
Source: This article is a reproduction of an excerpt of “In the Public Domain” documents held in 911Metallurgy Corp’s private library.