Table of Contents
The ores of copper are usually associated with minerals containing arsenic, antimony and bismuth. Whatever the means adopted for extracting the copper, these metals are usually found, to a greater or less extent, in the product. There is, however, usually some elimination in the various metallurgical operations to which the ores are subjected, and some attempt is made here to determine the degree to which this elimination is effected.
The degree, as well as the cause, of the elimination varies considerably with the amount of impurity in the material under treatment, and the results given here can only be taken as conclusive in the case of such materials as have come under the writer’s observation. The conclusions have, however, been drawn from the study of large quantities of materials that may be considered as fairly typical.
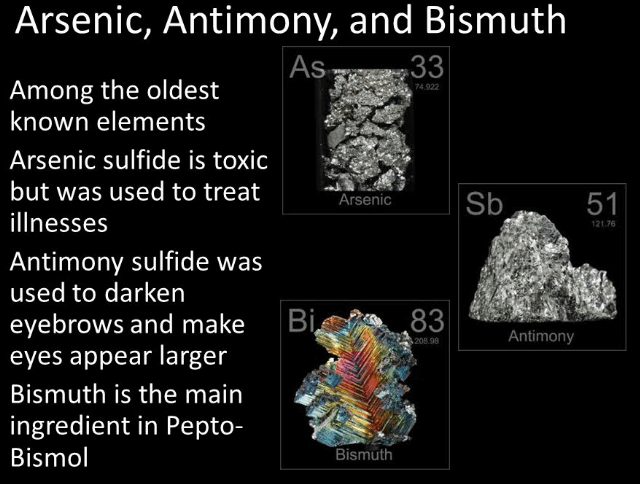
Removal of arsenic, antimony and bismuth from copper may take place in the smelting operations by scorification, volatilization, or, under special treatment, by processes of concentration. Owing to the great variety of materials that are treated in economical metallurgy, it is rarely possible to obtain exact weights from any particular operation. It is, consequently, a matter of some difficulty to obtain data that will show how elimination has taken place. In much of the following work the writer has had to be satisfied with determining the relative elimination of the impurity under consideration. In only a few cases have I been able to obtain exact weights, etc., of products.
Roasting of Copper-Ores
This operation may be carried on in heaps or stalls, when the ore is treated in the form of lumps, or in closed furnaces into which the ore is introduced in the form of a powder. The action of heat and air in the elimination of the elements under consideration appears to be the same in either case.
Arsenic, when present in sulphides, in arsenides, or in the metallic state, volatilizes at incipient redness as arsenious sulphide or as metal, or it is oxidized to arsenious oxide, which is readily volatilized. Arsenates, mainly those of iron and copper, are formed by the oxidation of both elements of the metallic arsenides, and by the action of atmospheric oxygen and arsenious oxide upon metallic oxides. These salts, as well as any similar compounds that may be present in the ores under treatment, are fixed at the highest temperatures. Arsenates may possibly be reduced by the action of sulphur and sulphides with the production of sulphides, arsenides or arsenites, and under the action of air these may be volatilized. But as this reducing action is in every case endothermic, it is very unlikely to take place under the conditions of low temperature and oxidation pertaining to the roasting operation. In point of fact, the arsenic remaining in calcined ores consists largely of metallic arsenates.
Antimony is, to a great extent, similar to arsenic in its occurrence in copper-ores, and also in its deportment when subjected to the action of heat and air. It volatilizes as a sulphide and as metallic antimony, but to a less extent than the corresponding compounds of arsenic. Metallic antimonates are probably formed in greater proportion to the amount of the impurity present than in the case of arsenic, and are fixed at all temperatures.
Bismuth may be present in the metallic state or in sulphides, arsenides and antimonides. The metal and sulphides are volatile at the roasting temperatures, but much less readily than in the cases of arsenic and antimony. The minerals containing bismuth are readily oxidized to fixed compounds.
The roasting of copper-ores preparatory to smelting is always incomplete. Arsenic, antimony and bismuth may remain in the roasted product in the same combinations in which they occurred in the ores, accompanying the fixed compounds that are formed during the operation.
The degree of elimination of these impurities in this operation varies, necessarily, with the minerals in which they occur, as well as the copper-ore, and the conditions under which the operation is carried on. The following analytical data show the elimination from fairly typical ores when roasted in heaps and in closed furnaces.
No. 1 was a cupreous iron pyrites which was roasted in heaps and subsequently smelted in a blast-furnace. No. 2 was a dressed ore containing copper, mainly in the form of copper pyrites, with smaller proportions of bornite and copper-glance. It was calcined in a reverberatory furnace.
In both ores, as is usually the case with sulphuretted ores, the proportion of arsenic is much larger than that of either antimony or bismuth. From the table it will be seen that the elimination of arsenic is considerably greater, in proportion to the original amount contained, than is the case with either antimony or bismuth.
Smelting Calcined Ores
In this operation there is a distinct difference in the action of the reverberatory and the blast-furnace. The atmosphere in the reverberatory furnace is always oxidizing, and the reactions that take place in melting calcined ores are (except in so far as they form a continuation of the roasting operation) only such as take place between the constituents of the ore. Arsenates heated strongly with silica are decomposed with the formation of metallic silicates, oxygen and arsenious oxide. Silica usually being present in the furnace-charge, arsenic may be eliminated by this action. Ter-sulphides of arsenic and bismuth remaining in the calcined ore may be volatilized when heated to the smelting temperature. Arsenates or antimonates and fixed oxides of these elements combine, in notable proportions, with the slag-forming elements. Arsenic and antimony are often present in considerable proportions in the slags from reverberatory furnaces smelting calcined ores.
The conditions are different in the blast-furnace when smelting calcined ores, as the gases are of a reducing character. The larger part of the arsenates and antimonates are probably reduced to arsenides and antimonides. These combine with the sulphides of iron and copper, forming the regulus, while the resulting slags contain none, or only minute traces, of these elements. Arsenic and antimony are probably volatilized as sulphides, but the greater part of both is concentrated in the resulting regulus. Bismuth and its sulphides, which may be reduced from the oxides and sulphates formed in the calcination, are volatilized in considerable proportions during the smelting operation. Furnace slags, whether produced in the blast-furnace or in reverberatory furnace are, so far as they have come under the writer’s observation, practically free from bismuth. The following analytical data were obtained from calcined ores and the regulus resulting from smelting in the two classes of furnaces.
In smelting calcined ores, arsenic, antimony and bismuth are, as has been already explained, only partially concentrated in the regulus known as coarse metal. The elimination of these elements, affected by volatilization and scorification, could have only been deduced from the analyses of the ores, regulus and slags from the same operation, or series of operations, in the same furnace. In the absence of these complete data it is only possible, as in the above table, to show the total elimination. The relative proportions in which the metals occur in the slags from this operation, however, enable us to deduce, to some extent, the relative effect of the two agencies to which the elimination is due. In examining the slags from reverberatory furnaces smelting ores containing arsenic and antimony, I have never failed to find these metals,—arsenic in various amounts up to 0.4 per cent., and antimony up to 0.06 per cent. In the examples of reverberatory practice given in the above tables the proportion of slag formed would be, respectively, about six times and four times as much as the copper in the ore, so that the presence of considerably smaller proportions of arsenic and antimony than those mentioned would account for the total elimination deduced from the analysis. It is therefore probable that only a small proportion (in some cases practically none) of the arsenic and antimony is eliminated by volatilization in reverberatory practice. The elimination of arsenic and antimony in this operation is considerably greater than that of bismuth.
In the case of slags produced from blast-furnace practice, smelting similar materials, I have never found more than 0.015 per cent, of arsenic, and only traces of antimony. It is, therefore, probable that the elimination of these elements in blast-furnace practice is almost entirely due to volatilization. On no occasion have I found more than traces of bismuth in ore-slags, whether produced in blast- or reverberatory furnaces, so that its elimination, which in the blast-furnace is considerable, may be taken as resulting entirely from volatilization.
Calcining Coarse Metal
Arsenic, antimony and bismuth are more uniformly diffused in coarse metal than in the ore, where they occur in separate intermixed minerals. In coarse metal these elements probably exist entirely as sulphides, uniformly diffused through a comparatively large proportion of regulus, and their behavior under calcination differs notably from that of the minerals rich in these elements mixed with copper-ores. The annexed analytical data show to what extent elimination is effected from coarse metal containing arsenic, antimony and bismuth in proportions fairly representing the product obtained from smelting the ores that usually reach the United Kingdom.
The above table shows that, in the coarse metal under consideration, over one-third of its arsenic and about one-sixth of its bismuth were volatilized during calcination, while the calcined product retained all the antimony.
Arsenic is probably partly oxidized and volatilized as arsenious oxide. The elimination, however, is less marked than in calcining ores, in which the arsenic is mainly present in minerals associated with the copper-ore, but not in combination with the bulk of the copper. These minerals are readily decomposed by heating with air, or per se, giving off arsenic as oxide, sulphide and metal. In coarse metal, on the contrary, all the arsenic is probably combined with the sulphur, and is diffused through the whole mass of regulus in comparatively small proportion. In the earlier stages of the operation arsenic is probably volatilized as oxide. But, as the operation proceeds, metallic oxides increase in quantity and the conditions become more favorable for the formation of metallic arsenates, which remain fixed in the product of calcination.
Antimony is not volatilized in appreciable quantity during calcination. It is more or less completely oxidized to form metallic antimonates which are fixed at the temperature of the calcination.
Bismuth is probably partly volatilized as sulphide, but its oxides, formed during calcination, remain in the calcined product.
Smelting Calcined Coarse Metal
In smelting calcined coarse metal in the reverberatory furnace for the production of white metal, the three elements under consideration are eliminated to a considerable extent. The slags from this operation contain notable quantities of arsenic and antimony. These amounts vary with the proportions present in the material under treatment, which consists of calcined coarse metal and slags from the roasting and refining furnaces. The slags from this operation, under ordinary conditions, often contain 0.50 per cent, of arsenic and 0.10 per cent, of antimony. In smelting calcined coarse metal, containing 31 per cent, of copper, to white metal, its iron and the siliceous earthy matter derived from the furnace give a slag about equal to twice the weight of its copper contents. In the following data the elimination from metal containing 100 of copper is seen to be 0.209 of arsenic and 0.118 of antimony, which would represent 0.104 per cent, of arsenic and 0.059 per cent, of antimony on the slag produced, so that it is probable that the greater part of the eliminated arsenic and antimony are present in the slag.
In the case of bismuth the elimination is practically effected by volatilization alone. The slags from ordinary materials never have more than 0.02 per cent, of bismuth.
In smelting roasted coarse metal in the blast-furnace the slags are practically free from arsenic, antimony and bismuth, so that the total amount of these elements eliminated may be taken as volatilized.
The elimination in blast-furnace smelting as compared with smelting in reverberatory furnaces is only about one-third in the case of arsenic and antimony. It is about one-eighth more in the case of bismuth. These comparative results are similar to those found in smelting calcined ores.
Roasting White Metal to Blister-Copper
In roasting white metal, oxidation of cuprous sulphide and mutual reduction of the oxides and sulphides of copper may be said to proceed together at a high temperature. Oxidation of arsenic and antimony, and their volatilization as oxides, probably goes on during the scorification in which the two oxides combine with the cuprous oxide formed in the operation. The analytical results of the examination of white metal, blister-copper and slag produced in its roasting show that, of the arsenic eliminated, about equal proportions have been volatilized and scorified; while the proportion of antimony scorified is greater than that volatilized. Bismuth is scorified only to the extent of one-eighth of the amount present, while about three-fourths of the whole quantity is eliminated by volatilization.
In the tables on p. 662 the blister-copper and slag are calculated from working-results in treating 100 tons of white metal.
Refining Blister-Copper
The elimination of arsenic, antimony and bismuth in the preceding operations has, unless the materials under treatment are uncommonly impure, left only small amounts of these metals in the blister-copper. Their elimination during the refining operation probably takes place entirely by scorification. The products, refined copper and refinery-slag, together contain quantities of arsenic, antimony and bismuth equal to those present in the blister-copper subjected to the operation.
In the tables on p. 663 the products of refining are calculated from the working-results on 100 tons of blister-copper.
A variation of the usual plan of purifying copper by scorification is described by Dr. E. D. Peters as follows: “ The addition of 3 to 5 per cent, of pure white metal—subsulphide of copper—to the bath at the beginning of the refining operation has a most rapid and satisfactory effect in removing both antimony and arsenic. Very bad cases may require two such additions with an intervening oxidizing operation.” This is, in effect, throwing the copper back and enforcing a prolonged
roasting that, I venture to say, would be more effective without the addition of white metal. In roasting copper, the removal of arsenic and antimony proceeds with notably greater rapidity after the copper has become dry (i.e., when it is saturated with cuprous oxide) than when it still contains appreciable quantities of iron and sulphur.
With unusually large proportions of arsenic in metallic copper subjected to roasting, there is a considerable elimination of this element by volatilization. Mr. P. C. Gilchrist, in his paper on “ The Basic Process as Applied to Copper Smelting,” gives weights and analyses of highly arsenical “ metallic bottoms ” roasted in a furnace with the usual siliceous bottom and of the copper produced in the operation. These give the following results for the elimination of arsenic (arranged from data on pages 12 and 13 of paper cited):
In comparing the relative elimination by the reverberatory and blast-furnaces, as shown by the foregoing analytical data, it will be seen that in the reverberatory furnace arsenic and antimony are eliminated in considerable proportion by volatilisation and in the ore-slags. These slags do not enter again into the smelting routine. In the blast-furnace the only final elimination is by volatilization, the ore-slags being practically free from these elements. Bismuth, in both methods alike, is eliminated only by volatilization.
In both furnaces the slags from the later stages are returned to the smelting circuit, with the effect of rendering the regulus and copper less pure. To obviate this return of impurities, the roaster- and refinery-slags are in some instances treated separately, and not returned to the ordinary smelting- furnaces.
Bessemerizing Copper Regulus
The process of treating copper regulus in Bessemer converters (which now replaces, to a large extent, roasting to blister-copper) has an effect in eliminating arsenic, antimony and bismuth similar to the roasting methods. The following analytical data show the elimination in treating regulus containing 56 per cent, of copper:
The above data show that in this process bismuth is eliminated more completely than either arsenic or antimony.
Pyritic Smelting
I have never had an opportunity to examine the products of the operation known as pyritic smelting, in which the calorific effect of the oxidation of iron and sulphur together with externally heated blast were the main sources of heat. I have, however, smelted siliceous iron pyrites mixed with copper pyrites, using considerably less carbonaceous fuel than is usual in blast-furnace practice. The following data were obtained from smelting such ores to which limestone was added as flux, and for which only 8.25 per cent, of coke was added to the charge. Cold-blast was used. The ores were practically free from antimony and bismuth:
There was thus about 90 per cent, of the total arsenic eliminated in the operation. About 80 tons of slag were produced with 100 tons of ore, and this contained 0.53 per cent, arsenic, or about 0.43 ton. About 54 per cent, of the arsenic was eliminated in the slag. The remaining 36 per cent, would consequently be eliminated by volatilization.
Working under these conditions, with a powerful blast, the top of the charge was always hot, and probably the whole of the volatilization took place at this point before the charge reached the smelting-zone. The action in the upper layer of the charge would correspond to calcination; but, owing to the high temperature, probably a considerable proportion of the arsenic was oxidized to arsenic oxide, which formed fixed arsenates with the iron oxide and entered the slag. The proportion of coke used would not allow the furnace to be entirely oxidizing; but it is possible that, were a smaller proportion of coke used, the elimination of arsenic by scorification would be even greater.
Mr. W. Gowland has described an interesting method which is still largely used in Japan, and by the use of which considerable elimination of arsenic, antimony and bismuth is effected. As in the very ancient liquation process by which the early German metallurgists desilverized copper, the impure copper is alloyed, or rather mixed, with metallic lead, and the mixture is heated to a temperature below the melting-point of copper. By this means a porous mass of purified copper is obtained with metallic lead and an excrescence known as shirome. The lead is found to carry all the bismuth, and the shirome practically all the arsenic and antimony that was present in the copper. The following analyses of Ashiwo copper are given by Mr. Gowland:
In 1889 Mr. P. C. Gilchrist patented the use of basic bottoms for copper furnaces, and, in the paper already quoted, gave examples of their practical working with elaborate analytical data which show very considerable reductions in the time required to eliminate arsenic from copper. Although the advantages and economy of the basic process, as described by Mr. Gilchrist,. appear to be highly important, this method of working has been abandoned.
The principle involved in the basic process has long been taken advantage of in the treatment of arsenical copper, though it had never been systematically applied until Mr. Gilchrist worked upon it. It has long been the practice in Swansea and elsewhere to add lime and sodium nitrate to the copper during the refining operation, with the view of hastening the removal of arsenic.
It is possible to concentrate the impurities (contained in the copper) in a small amount of the metallic copper, with a relative purification, and this forms the basis of the operation known as “ best selecting.” I have already published data bearing on this process. And, in the case of the elements under consideration, I found that only antimony could be concentrated with any degree of perfection. There is a fair concentration of arsenic in the metallic bottoms, but no such concentration is effected in the case of bismuth.
Elimination by Wet Processes of Extraction
Atmospheric Oxidation Without Burning
In atmospheric oxidation of cupreous iron pyrites, and subsequent extraction of copper by leaching, as carried on in Portugal and Spain, arsenic and antimony are to some extent dissolved and reprecipitated with the copper. The proportion in which they are separated and precipitated is only a fraction of the amount contained in the ores. But this is so important as to seriously deteriorate the copper precipitate for smelter’s use, and to entail excessive expense in smelting and refining the copper.
The contaminating elements, or their sulphides, are probably oxidized with the copper and dissolved by the agency of free sulphuric acid formed by the action of ferric sulphate on cuprous sulphide. The arsenic is present, in less proportion as metallic arsenic or arsenide than as arsenic acid, forming arsenates, and these compounds are deposited to the greatest extent in the later stages of the copper precipitation. This is probably due to the gradual neutralization of the free acid by the metallic iron in the precipitation troughs, and by the acid solution of ferrous sulphate being oxidized to form neutral solutions of ferric salts. In the oxidizing and neutralizing action, antimonates and basic salts of bismuth are probably deposited with the arsenates. The copper precipitated in the troughs, through which the liquors first flow, is less contaminated with arsenic than that in the later troughs,—the arsenic it contains usually being in the metallic state.
Burning and Subsequent Washing of Cupreous Iron Pyrites
This is the process usually adopted in Spain and, to some extent, in Portugal for the extraction of copper from cupreous iron pyrites. In burning, there is a considerable elimination of all three elements, as was explained in the consideration of roasting of copper-ores previous to smelting. The following may be taken as fairly typical of heap-roasting, preparatory to lixiviation, as conducted in Spain :
Arsenious acid is, to a greater or less extent, deposited in the outer layers of the heaps. The sulphurous acid produced in burning the ore, passing with excess of air over the partially burnt pyrites containing ferric oxide, forms sulphuric acid, which is also, to some extent, caught in the colder portions of the heaps. Consequently, the solutions obtained by washing contain free acid. This probably acts on the residual and dissolves the partially oxidized arsenic, antimony and bismuth. These elements are precipitated in a manner similar to that in which they are deposited, in the precipitating troughs, from solutions obtained by washing raw pyrites after atmospheric oxidation. Although the proportions of arsenic, antimony and bismuth contained in the precipitated copper obtained by this process are notable and important, they are smaller than in the copper obtained in oxidizing pyrites by the direct action of atmospheric air. The considerable proportions of these elements eliminated during the roasting leave smaller proportions to be subjected to the lixiviation-action.
After the exhaustion of the soluble copper, the residue is laid out with smalls, produced in mining and in the handling of the heaps, and is treated in the same way as the raw pyritic heaps. The contaminating elements are extracted and precipitated as in the corresponding treatment of raw pyrites already explained.
Extraction of Copper from Burnt Cupreous Pyrites
In this process the chloridation of the copper, preparatory to its solution, is accompanied by the chloridation of the three elements under consideration. These chlorides all being volatile at low temperatures are carried off, to a greater or less extent, in the gaseous current from the furnaces, and are largely dissolved in the wash-water and collected, with the condensed acids, in the tower liquors. Their expulsion is not complete. The arsenic in a notable quantity and antimony in a less amount, mainly in combination as arsenates and antimonates, with some bismuth, remain in the calcined ore. In washing with water, these salts, as well as the bismuth that remains in the calcined ore, are dissolved only in minute traces, so that if the copper is precipitated from these solutions it would be practically free from these impurities. The copper, insoluble in water, that is in the calcined ore, is removed by the use of tower liquors, and under the action of this solvent a considerable proportion of the arsenic, antimony and bismuth that remained in the calcined ore is also dissolved. This increases the proportion of these elements that is already present in the tower liquors. In some works the tower liquors are purified before use. The extent to which these elements are volatilized in the calcining operation may be partially indicated by the proportions in which they are found in the liquors and in the calcined ore, as compared with the burnt ore under treatment. Burnt cupreous pyrites and the calcined ore resulting from roasting it with 15 to 20 per cent, of common salt contained the following proportion of arsenic: Burnt pyrites, 0.145, and the calcined ore, 0.020 per cent.
In the tower liquors, obtained by washing the gases from the furnaces, there was found: Arsenic, 0.0222 gm.; antimony, 0.0005 gm.; and bismuth, 0.0046 gm. per liter.
The proportions of impurities in the copper from the same ore vary greatly according to whether the practice of treating the aqueous and acid separately is followed or not.
The following data are taken from practice in which the two solutions are not kept separate :