Electrowinning is defined as the cathodic deposition of metal, in this example copper, from a copper bearing solution by the passage of an electric current current using an insoluble anode.
For copper the electrowinning reaction reaction is:
CuSO4 + H2O ⇒ Cu + ½O2 + H2SO4
The overall reaction is the combination of two electrochemical half reactions.
The cathodic reaction is:
Cu++ + 2e- ⇒ Cu°
The anodic reaction is:
H2O ⇒ 2H+ + ½O2 + 2e-
The amount of copper that is deposited in the reaction is defined as an electrochemical equivalent. One faraday or 96489 ampere seconds (coulombs) will deposit the atomic weight of an element measured in grams divided by the valance of the metal. The electrochemical equivalent for copper is 0.02846 kilogram per ampere day.
It is important to note that copper deposited at the cathode is not a function of voltage, but of time and ampheres. The amount of copper from a single electrolytic cell is determined by the number and size of anode/cathode pairs in the cell and the time that electrical current is applied to the cell. The voltage required is determined by the electrical resistance of the electrowinning cell and the electrical system providing electricity to the cell. A detailed explanation of these individual resistances which comprise the electrowinning system are beyond the scope of this paper, but can generally classified as; the reaction potential as determined by the electromotive force of the electrowinning reaction, over voltage due to chemical and physical reactions at the surfaces of the anodes and cathodes, electrolyte and hardware resistances. These resistances are combined and require a voltage between 1.8 and 2.5 volts per cell.
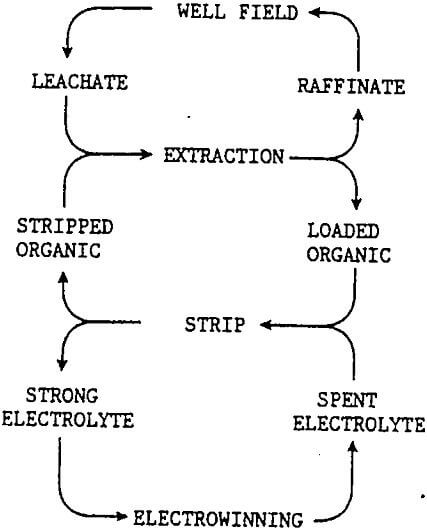
If copper production is greater than the output of a single cell, additional cells are added in series and the cell voltages are additive. The ampheres of the an electrowinning circuit is a function of the capacity of the electrowinning cells and the voltage is a function of the number of cells.
The overall reaction takes place in the electrowinning cells as the electrolyte is circulated through the circuit and an electrical current is passed between the anodes and cathodes. For proper operation in electrowinning the copper and acid concentrations must be keep within a narrow concentration range. Strong electrolyte, the copper rich aqueous phase from the solvent extraction strip stage, is continually added to to the circulating elelctrolyte to maintain the copper concentration about 45 grams per liter. A portion of the copper depleted or spent electrolyte from the electrowinning circuit is returned to solvent extraction to be used as the acid rich, aqueous phase in the strip stage to accept copper from the copper rich, loaded organic phase. This final flow completes the recirculating systems in solvent extraction / electrowinning.
Constraints
The illustration shows three separate circulating or recycle systems; raffinate-leachate, stripped organic-loaded organic, and spent electrolyte-strong electrolyte. The interactive nature of the these recycle systems places constraints on the in situ leaching of the copper ore body.
The recycle of leachate and raffinate provides the leach field with a continuous source of acid, with acid addition only as required to replace the acid consumed by gangue minerals. Before the raffinate can be returned the leach zone, all traces of the organic solution must be removed to prevent coating of leach surface or blocking of the small flow channels. This is done by allowing excess time for separation in extraction, a raffinate pond with organic recovery, and filtration as a final control. Lubricants for well field equipment also require careful control. Additives should not be added to the injected leachate without first testing to insure that they do not have a detrimental affect upon their return to solvent extraction in the leachate.
The solvent extraction circuit prefers a constant solution volume and copper tenor in the leachate. The copper transfer capacity of solvent extraction must be matched to the copper concentration of the leachate and the electrowinning circuit also matched to produce the equivalent amount of copper cathode. These systems will operate smoothly as steady state conditions are reached in the leach zone. New wells will be brought on line to replace the older wells as copper in the leach zone is depleted. The greater the number of wells the better the blending of the leachates to provide the steady state flow to the surface plant and the returning raffinate. Variable speed pumps allow limited volumetric flexibility and current adjustment in the cell house can match cathode production to the well field.Electrowinning Equipment
Ground water from the surrounding area can be drawn into the leach zone by the production wells when the leach zone is located in saturated rock. This results in dilution of the leachate. Some leachate remains in the leach zone in the pore space in the rock. If the net result is an increase in leachate volume, an evaporation pond will be required as part of the surface facilities to maintain a constant solution volume.
There is a upper limit for the copper tenor in the leachate. By controlling the acid concentration of the leach solution and the retention time in the leach zone, it possible to increase the concentration of copper in the leachate solution. As shown above in the extraction and strip reactions, solvent extraction is stoichiometric. The mass of extractant in the organic phase is determined by the mass of copper in the leachate solution. As the copper tenor increases the percentage of extractant in the organic phase increases. Because the volume of the organic phase must remain constant to maintain the volumetric ratio with the aqueous phase or leachate, this increase in extractant decreases the percentage of diluent in the organic. Depending on the special characteristics of the extractant and diluent chosen, the upper percentage of extractant in the organic phase is approximately 20 per cent. The corresponding upper limit of copper in the leachate is generally considered to be 12-15 per cent. If greater copper tenors in the leachates are anticipated other recovery process should be considered. Direct electrowinning, precipitation, or non commercial solvent extraction are suggested alternatives.