Table of Contents
The choice between wet and dry milling is, in general, unimportant in small-scale milling but is a major technical problem when large-scale milling in the metallurgical industries is involved. On purely mechanical grounds it is difficult to see any great difference in fundamental principles between wet and dry milling, since dry milling may be regarded as wet milling with a fluid having the viscosity and density of air, whereas with wet milling the fluid is a liquid. A slight difference of condition between the two cases, however, is that with dry milling the fluid (air) fills the whole of the mill shell not occupied by the balls, whereas with wet milling the liquid occupies only a part of the mill volume not occupied by the solid charge. This difference would be expected to have some slight effect on the motion of the ball charge but the effect would be expected to be so small as to be practically negligible.
An examination of the literature shows, however, that the actual difference between the results of wet and dry milling are often very large; for example the power to drive a tube mill in which a given material is being wet ground may be as much as 30 % less than that of a similar mill dry grinding. Furthermore the throughput of a continuous feed mill is greater in wet grinding; probably due to the better flow properties of a pulp in comparison with a dry material. It appears, however, that the rate of ball and liner wear is greater in wet milling so the decision between wet and dry operation is, in cases where the choice is permitted, a matter of balancing the economic gain arising from reduced power demand and increased throughput against the increased cost of replacement of the ball charge and the mill liners and the loss of production during the shut down period necessary for such replacements to be made.
Clearly in certain applications, this choice is not permitted since, for example, the grinding of the raw mix in a cement plant may be carried out either wet or dry but the grinding of the cement can, from the nature of the material, only be carried out dry.
A further important point of difference between wet and dry milling is that wet milling allows the easy introduction of surface active media for the reduction of the energy required to produce unit new surface or for the inhibition of aggregation of the fine particles. It is theoretically possible to introduce such substances in gaseous or vapour form into dry mill but, in practice, such methods have not been sufficiently successful to justify wide adoption, and, in fact the only practicable method of introducing such materials is wet milling.
Consideration can now well be given to some of the factors upon which the choice of the type of mill, or the method of operation of a given mill, for the grinding of a specified material will depend. In the first place it is perhaps of interest to note that the problems encountered in the preparation of powdered materials are not necessarily reduced when the quantity of material to be processed is small. As an example of this, in the preparation of materials such as Portland Cement, which sell at relatively low prices, the problem is mainly one of obtaining a final product having the required size characteristics at a minimum total cost per ton and, in this case, questions of the the contamination of the material, during processing, scarcely arise.
In the grinding of drugs and cosmetic preparations, however, the question of the cost of the grinding process, per pound of product, is scarcely significant in relation to the high value of these materials but the avoidance of contamination is a major problem. Thus, the inclusion of iron, from the balls and the mill body, in “face powder” is highly undesirable since such iron imparts a brown tint to the powder, and for this reason cosmetic and similar materials are usually ground in a mill having a ceramic body and with smooth natural pebbles as the grinding medium; that is, in a pebble mill. Similarly, pebble mills are used for grinding of feldspar for high-grade porcelain, since, as the previous case, minute traces of iron will introduce objectionable tinting. In this connection, it is of interest to note that there appears to be extant a licence for the removal of five tons of pebbles from Chesil Beach per annum; these pebbles, which are naturally graded for size, being ideal for use in pebble mills.
As an extreme example of the importance of the elimination of contamination may be quoted the grinding of minute quantities of metallic halides, used in certain classes of infra-red absorption spectroscopy, for which purpose a small vibration mill with body and balls made of agate is often used. In cases such as these, the decision as to wet or dry grinding is rarely based on economic considerations, but is usually made on the basis of a study of a number of extraneous factors, such as some special property of the material being processed, some desired condition of the final product or of the initial and final states of the materials involved.
Thus pyrotechnic materials might well be ground dry, since this would, in general, give a product having superior characteristics to one which has been ground wet, but if the material were very reactive it would probably be ground in an inert atmosphere. Similarly, tungsten carbide for use in the preparation of sintered carbide tool-tips would be ground dry, since moisture would complicate the subsequent processes and be harmful to the final product. Metallic powder pigments would probably be ground dry, since by this means discoloration is minimized. The grinding of aluminium for the preparation of paint is, however, often carried out wet since by this means stearic acid, or some other antiflocculent, may be introduced.
Finally, clays for the preparation of ceramic slips would reasonably be expected to be ground wet, since the initial condition of the clay is wet and it is required in a wet form for subsequent processing. Clearly, in such a case, dry grinding, which would involve drying, would be uneconomic and would only be adopted in very special circumstances. An application of the ball mill which can scarcely be classed as milling but which should, nevertheless, be mentioned is the dispersion of pigment in the varnish vechile in connection with the manufacture of paint. The concentration of solid material in the suspension is, in this application, usually quite low, generally being about 10% by volume, and, although no appreciable reduction of the size of the particles occurs, considerable ball wear is often encountered. These observations are of some interest in view of a theory of the internal dynamics of the ball mill, propounded by one of the present writers, since that theory suggests that when the quantity of solid material is small in relation to the volume of the ball charge, the particle size reduction might be small but that the ball wear would be appreciable.
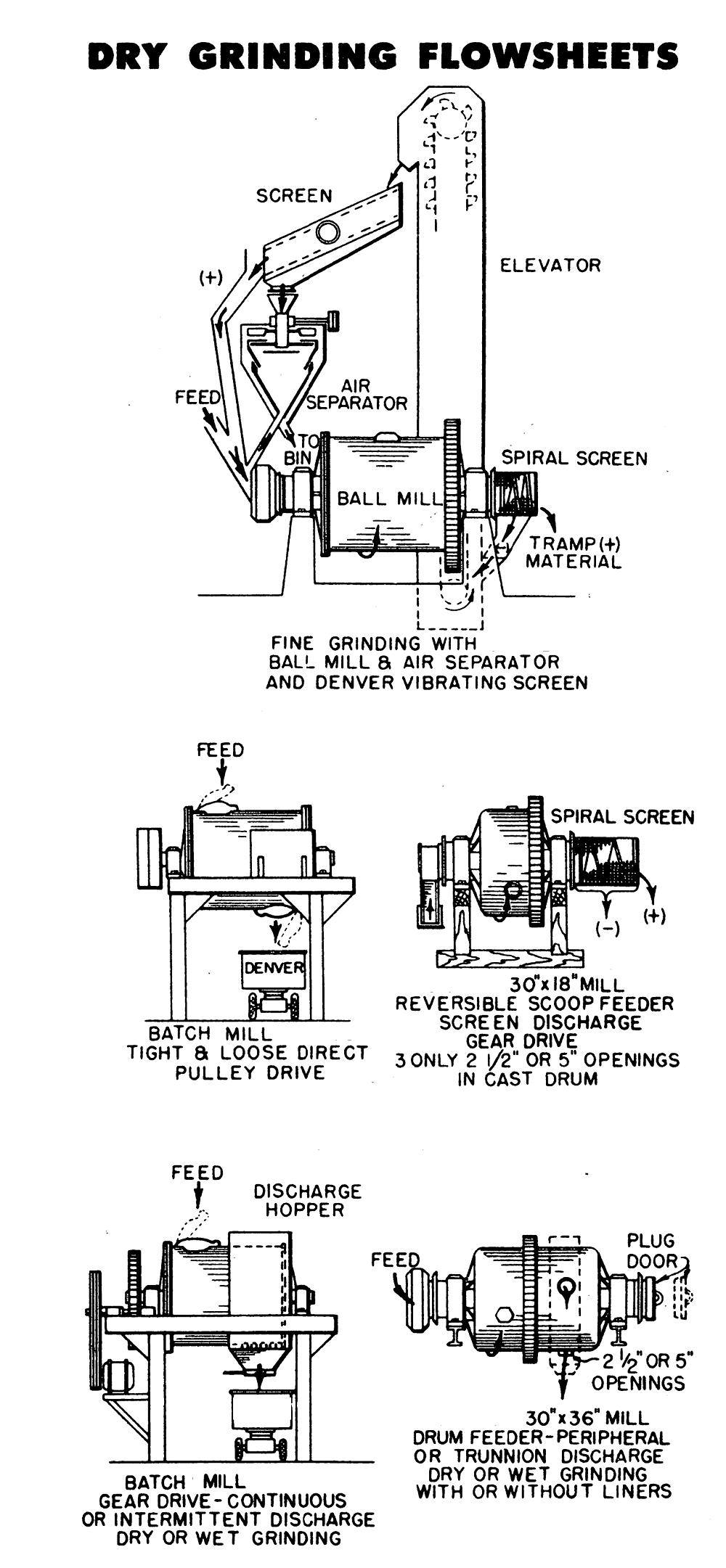
From the foregoing outline of the problems involved in the selection of a mill for a given purpose and in the operation of mills, it is apparent that the subject is very complex. Furthermore, much of the theory underlying a rigid solution of any problem is in a very fluid state and, in consequence, the solution of a practical problem generally involves the use of considerable judgement, based on previous experience, to temper the conclusions drawn from theoretical analysis.
Effect of Particle Size Distribution on Grinding Rate in Dry Ball Milling
It has been shown above that: (i) the particle size distribution has a significant effect on the breakage rate of the particles, and (ii) intersize particle-particle interactions play an important role in determining the breakage kinetics.
Generally, grinding rates are regarded to be proportional to the specific energy input to the mill. A change in the grinding rate with no change in the specific energy input to the mill therefore suggests that it is either the energy received by the particles, or the degree of its utilization by the particles, or both of these factors that are significantly affected by the particle size distribution. The precise details of the various phenomena that are involved are not clearly understood at this stage.
It is well known that both the batch as well as continuous grinding operations can be simulated to a reasonable degree of accuracy using a number of combinations of the S and B values. However, from the point of view of the correct analysis and the scale-up design of the grinding systems, it is important that precise estimates of these parameters are obtained. The literature on the ball milling operation is full of controversies and contradictions. The main reasons for this state of affairs are: (i) a lack of thorough investigation of various observed phenomena, a tendency to oversimplify the models, (iii) poor design of experiments and (iv) use of insensitive methods of parameter estimation.
Size Distribution Effect
The effect of the coarser particles on the grinding rate of the finer ones was investigated by introducing coarse quartz particles in the natural size distribution environment of limestone. Results of Tests 1 and 2 in Table 6 show that 50% replacement of the 20/28 mesh limestone particles by same size quartz particles reduced the breakage rate of limestone particles by only about 2.5%. Therefore, the use of quartz for our purposes was considered to be alright. In Test 3, the same quantity of a slightly coarser 14/20 mesh quartz was used instead of the 20/28 mesh quartz. A further reduction in limestone grinding rate (sL 20/28) about 1.7% was observed. In Test 4, even coarser quartz (10/20 mesh) was used, but no further reduction in SL 20/28 was observed. These results show that, over the range of size distribution investigated here, coarser particle have only a slight (negative) effect on the breakage rate of the finer particles. To a first approximation, this effect can be ignored.
![]() |
![]() |
![]() |
![]() |