Table of Contents
Flotation is both a science and an art. It brings together many complex variables. Such basic factors as knowledge of mineral structure, chemical reagents, pH of mill water, pulp density, temperature, technical skills of the operator, the dependability of the flotation machine, as well as a host of other factors which affect the flotation of each specific ore must be combined to produce “economic metallurgy.”
“Economic Metallurgy” is the practical objective of all mineral processing — that of securing the greatest possible profit from the operation. It incorporates the elements of greatest possible recovery, highest possible grade of concentrates, lowest possible milling, capital, operating and maintenance costs.
In 1961 the American Institute of Mining and Metallurgical Engineers commemorated the 50th Anniversary of Flotation in the U.S.A. with a special 700- page documentary report. The book, “Froth Flotation, 50th Anniversary Volume,” highlights some of the many changes to flotation machines that have taken place since the first flotation cells in the United States went on stream in 1911 at Basin, Montana.
In 1911 the only mineral recovered by flotation was sphalerite. However, today “flotation” is the principal method of mineral processing throughout the world. Capacity of the first flotation mill was only 50 tons of ore per day. Now more than 100 different minerals are commercially recovered by flotation and some mills process as much as 50,000 tons of ore every 24 hours.
CHANGES IN FLOTATION MACHINE DESIGN
With economic metallurgy as its objective, flotation machines have changed over the years as the demands on the process have changed.
DEVELOPMENTS WHICH REDUCED OPERATION COSTS
One of the significant changes made to reduce operating costs has been the extensive use of pressure molded rubber parts to withstand abrasion and thus reduce maintenance. Design of flotation cells has been improved and simplified to handle increased tonnage. One such development was the “free-flow” tank design. Another change has been the use of flotation mechanisms which can be removed from the flotation machine quickly for the inspection or change of wearing parts. A simple change in the method of pre-mixing air with pulp as it enters the throat of the flotation impeller has made it possible to reduce power cost as much as 50%. Development of larger flotation cells means fewer flotation cells are needed to do the job. This simplifies maintenance and reduces construction costs.
Two BASIC TYPES OF FLOTATION MACHINES
To meet the varying conditions and requirements, two basic types of flotation machines have been developed:
(1) Cell-to-cell Flotation Machine
(2) Free-flow Flotation Machine
THE CELL-TO-CELL FLOTATION MACHINE
The cell-to-cell flotation machine meets the needs for both mineral recovery and cleaning and recleaning of flotation concentrates. It incorporates simplicity and flexibility of adjustment that permits the flotation operator to use his skill in securing the exact flotation conditions required by his specific ore for economic metallurgy.
The cell-to-cell flotation machine is typified by a flotation mechanism suspended in an individual cell separated from the adjoining cells by an adjustable weir. A feed pipe conducts the flow of pulp from the weir of the preceding cell to the mechanism.
Cell-to-cell Flotation Mechanism showing how feed pipe conducts pulp to throat of the rotating impeller. Each cell has its own mechanism, adjustable overflow weirs and feed pipe. Molded rubber wearing parts are used.
Free-Flow Flotation Mechanism showing how the pulp flows through the machine without interruption of weirs. Feed pipes are not used. Pulp enters the throat of the rotating impeller by flowing down the outer feed well. Air, under low pressure, is pre-mixed with the pulp and is thoroughly diffused throughout the cell by intense action of the impeller.
A modern high – tonnage copper mill equipped with Free-Flow Flotation Machines. Flotation concentrates are combined from all cells and then further upgraded by cleaning in other Flotation Cells.
A typical modern fluorspar mill where cell-to-cell Flotation Machines are used to clean and reclean fluorspar concentrates to meet market specifications for acid-grade fluorspar. Note pipes on launders return froth for multiple cleaning without need for pumps.
Early-day “Sub-A” Flotation Machine. Note the wood tank and flat-belt drive. Machines of this type were used in the 1920’s and 1930’s. They were the principal type of flotation machine used throughout the world. Experience and continual improvement are behind modern Flotation Cells.
THE FREE-FLOW FLOTATION MACHINE
The need for a flotation machine to handle larger tonnages in bulk flotation circuits led to the development of the “Free-Flow” type flotation machine. These units are characterized by the absence of intermediate partitions or weirs between cells. Individual cell feed pipes have been eliminated. Pulp is free to flow through the machine without interference. Flotation efficiency is high, operation is simple and the need for operator attention is minimized. Most high tonnage mills today use the “free-flow” type of flotation machine. Many are equipped with automatic devices for control of pulp density, pulp level, and other variable factors.
FLOTATION MACHINES OF THE FUTURE
Just as modern flotation machines have evolved from the past they will change to meet future needs of the industry. Larger, more efficient flotation cells, automatic control of grinding circuits, flow meters, continuous on-stream sampling, direct – reading density, pH, and pulp – level devices, new reagents as well as instantaneous X-ray analysis will make possible almost completely automated flotation circuits and new achievements in economic metallurgy.
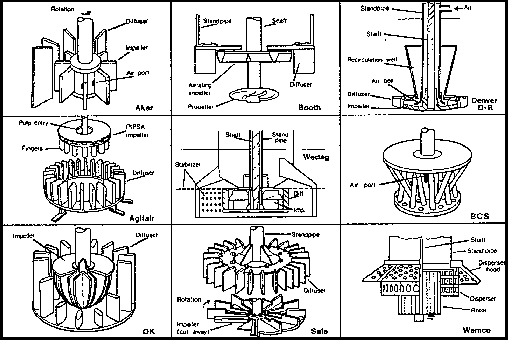
Source: This article is a reproduction of an excerpt of “In the Public Domain” documents held in 911Metallurgy Corp’s private library.