On our EXAMPLE mining operation, the power generation and distribution system consists of four components:
- Diesel electric generation
- Diesel fuel system
- Heat recovery system
- Power distribution system
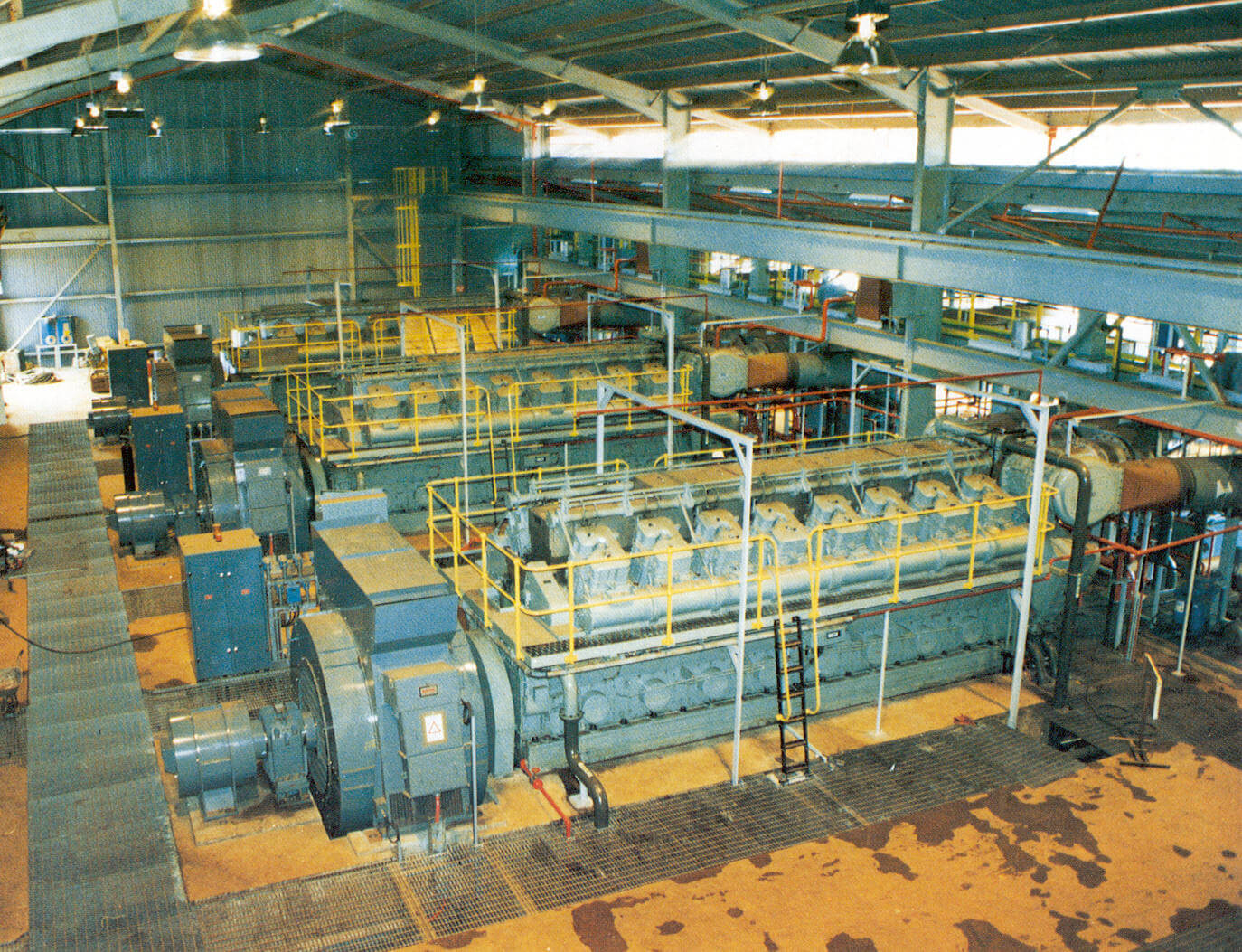
The system is intended to operate automatically with local control panels in the generating/electrical room, with some remote monitoring in the main control room.
Detailed Process and Control Description
The diesel electric generation system consists of four 1135 kW, 1200 rpm engine generator sets that are operated either manually or automatically by selecting desired position on the engine mode switches and the sequence selector switch.
The engines are 4 cycle, V16, 4210 cubic inch displacement, provided with air, fuel and lube oil filters, fuel and jacket water pumps, service hour meter, governor, fuel and lube pressure gauges, water temperature gauge, pyrometer, oil filter gauge and hourmeter. Protective devices include: low oil Pressure, high water Temperature, low water level and overspeed. The starting system is dual 24V with changer.
The diesel fuel system consists of five 785,000 liter fuel storage tanks, fuel unloading and transfer system, diesel engine day tank and oil recirculation system.
The heat recovery system consists of a glycol-water heat transfer system, capturing waste heat from both the engine cooling jackets and exhaust. A back-up boiler is provided.
The power distribution system consists of 600V power switchgear for controlling generator output and primary distribution, a 12.5 kV power line for site distribution and 600V motor control system. Each generator is provided with a circuit breaker, and the entire power plant has a synchronizing panel.
Operation – Diesel Electric Generation + Manual – Single Unit Operation
- For initial start-up, all engine mode switches and sequence selector switch should be in OFF position.
- Governor switch in ISOCH position.
- Idle/Rated Switch in RATED position.
- Governor raise lower potentiometer in mid position.
- Synchronizing switch in OFF position.
- Synchronizer mode switch in OFF position (located inside panel).
- Switch one engine mode switch to manual position, this engine will now start when the pushbutton at the engine is pressed.
- To close breaker on to a dead bus, put synchronizing switch to ON position, hold breaker control switch in close position and at same time press dead bus pushbutton. The breaker should now be closed. The synchronizing switch should now be returned to the OFF position.
Manual – Synchronizing Operation
- All switches should be as above steps 2 through 6.
- Put synchronizer mode switch to the RUN position (located inside panel).
- Start second engine as in step 8.
- Turn synchronizing switch on second unit to ON position.
- Watching the synchroscope, close the breaker control switch just as the needle on the synchroscope reaches the 12 o’clock position (synchronizing lamps are out). The second breaker should now be closed. Return synchronizing switch to the OFF position.
Automatic Operation
- For initial start-up all engine mode switches should be in OFF position.
- All switches should be as in steps 2 through 6.
- Put all synchronizer mode switches to RUN position (located inside panels).
- Select prime unit on sequence control switch.
- Switch all engine mode switches to AUTO position.
- Prime unit will start.
- Reset system abnormal light by pressing system abnormal pushbutton.
- If generator set or breaker fails, next unit in numerical order (on sequence control switch) will start and at the same time bring on a system abnormal light and also a remote flasher. This light and flasher indicate that the sequence selector switch is now in the wrong position. The switch should now be put into its correct position (i.e. if Engine #2 is now running, then sequence selector switch should be in Position 2). Before resetting system abnormal pushbutton, correct engine fault, put faulted engine mode switch to OFF, then back to AUTO position, now reset system abnormal pushbutton.
- There are two resettable reserve power time clocks in the system. Time clock 2 (TC2) will only come into
effect when a fourth engine/generator set is installed in the future. (Could be used to start third unit). - Time close 1 (TCI) is only in effect when the engine mode switches are in the auto position and the sequence selector switch is in any position other than the OFF position. This time clock can be set for any time of the day to start and stop a second unit should the load increase and decrease at specific times of the day.
- When the time clock calls for a second engine to start, the engine will start automatically, synchronize with the first unit and close the breaker. At the end of the time clock period, the second unit’s breaker will trip and the engine will shutdown after a 5 minute
minimum run delay.
Load Control – Manual or Auto Positions
- With one unit running and the load increases to 500 kW, the horn and remote flasher will operate indicating that a second unit should be started manually. If the second unit is not started within 60 seconds, then a timer (Tl) will time out (and drop off the mill feeder and the office distribution breakers).
- With two units running and the load increases to 1,000 kW, the horn and remote flasher will operate indicating that the third unit should be started manually. If the third unit is not started within 60 seconds, then a timer (Tl) will time out and drop off the mill feeder and the office distribution breakers. If the load has not dropped below 1,000 kW, then a second timer (T2) will time out and drop off the camp and pump feeder and also the warehouse/shop distribution breakers.
- With three units running and the load increases to 1,500 kW, 5(b) would be activated. At this point, this would indicate that a fourth engine/generator set would be necessary (future).
- The horn may be silenced by pushing the silence pushbutton however, the remote flasher will still be activated until the load drops below the load settings of the transducers.
- When load decreases, shutdown engine via the engine mode switch to OFF position, then back to AUTO position if automatic mode is required.
- Reset system abnormal light by pressing system abnormal pushbutton.
- Note: When one or more units are operating in manual position, no auto standby is available.
To change Prime Unit-Conditions:
a) All engine mode switches are in AUTO position, sequence selector switch is in Position 1. With these conditions Unit No. 1 will be running as prime unit, No. 2 unit will be the first standby, No. 3 unit will be the second standby and No. 4 will be the third standby.
b) If No. 3 unit is now to be the prime unit, put Unit No. 2 engine mode switch to OFF position, then put sequence control switch to Position 3. (Note: this eliminates No. 2 unit from trying to start). No. 3 unit will instantly start and synchronize with Unit No. 1. The first unit will continue to run for another 5 minutes until the expiry of the minimum run timer. No. 2 unit mode switch should now be returned to AUTO position. No. 3 unit will now be the prime unit, with No. 1 unit being the first standby and No. 2 unit being the second standby.
Note: By putting No. 2 engine mode switch into the AUTO position, this will now have brought on the system abnormal light, to reset, push system abnormal reset pushbutton.
- Engines will shutdown and lockout when either in MANUAL or AUTO position for the following reasons:a) Overcrank
b) Low oil pressure
c) High water temperature
d) Overspeed
e) Reverse power
f) Breaker locked out
To reset, first eliminate cause for shutdown, reset engine mode switch to OFF position, then back to MANUAL or AUTO position.
- Since the system has been designed for automatic operation, the system abnormal light and the remote flasher will operate for the following reasons:a) Any engine mode switch in MANUAL or OFF positions.
b) Sequence selector switch in OFF position.
c) Any lockout as in (a) above.
Note: Resetting the system abnormal pushbutton will note cancel the light or remote flasher when in 11(a), 11(b) or 11(c) above. - It is important that when in AUTO, the sequence selector switch is in the correct position with respect to the prime units. See Table 14-1 below.
Diesel Fuel System
The diesel fuel system consists of five storage tanks on site and one at Sturdee Strip, a pumphouse, unloading facilities, fuel dispenser, two generator day tanks, four diesel generators and a recirculation tank and pump.
Fuel is unloaded from trucks and pumped to the tanks using either a truck-mounted pump, or one of the pump house pumps. Fuel is pumped from the tanks to the dispenser using a manually controlled pump and to the day tanks using automatically controlled pumps. The diesels only burn about 20% of the fuel flowing into the fuel pumps; the rest is returned to the recirculation tank, and from there pumped back into the main tanks. The warm return fuel helps to keep the main storage tanks warm. There is provision to recirculate directly back into the day tanks, but this should not be done for prolonged periods, as excessive heat will build up in the day tanks.
Fuel can be transferred between the main storage tanks using a variable speed transfer pump in the pumphouse.
Selector Switch Position | Engine No. 1 Mode Switch Position | |
All units will start when each engine pushbutton is pressed. One unit can be put on line via dead bus and breaker close switch. All others must be manually synchronized. | Off Position | Manual Position |
Engine No. 1 will start and automatically close its breaker on to dead bus. All other units will automatically synchronize.
Engine #2 1st auto standby Engine #3 2nd auto standby Engine #4 3rd auto standby |
Position 1 | Auto Position |
Engine No. 2 will start and automatically close its breaker on to dead bus. All other units will automatically synchronize.
Engine #3 1st auto standby Engine #4 2nd auto standby Engine #1 3rd auto standby |
Position 2 | Auto Position |
Engine #3 will start and automatically close its breaker on to dead bus. All other units will automatically synchronize.
Engine #4 1st auto standby Engine #1 2nd auto standby Engine #2 3rd auto standby |
Position 3 | Auto Position |
Engine #4 will start and automatically close its breaker on to dead bus. All other units will automatically synchronize.
Engine #1 1st auto standby Engine #2 2nd auto standby Engine #3 3rd auto standby |
Position 4 | Auto Position |
Fuel Dispenser
The fuel dispenser is supplied by a transfer pump located in the pumphouse. The pump is controlled remotely by a handswitch at the dispenser. There is also a stop switch in the pumphouse.
Fuel Transfer Pumps
The main fuel transfer pumps are remotely controlled by the day tank level switches and hand-switches. Emergency stop switches are located in the pumphouse and the generator room. Lights on the mill control panel indicate the status of the pumps.
When the fuel pump Hand/Off/Auto switches are on AUTO the two pumps are alternated at each startup. When main fuel transfer pump only is selected for automatic operation, it can be used for fuel transfer, either between two main storage tanks, or from a truck to a main storage tank. PU-902B has a variable speed drive which can be used to increase the flowrate when desired.
Day Tanks
The two 500 USgal day tanks are identical and installed in parallel so that the system can operate normally with one tank isolated. The tanks are equipped with a locally mounted level gauge glass, high and low level switches which control and high and low alarm switches which alarm at the mill control panel when the oil levels are outside the normal operating range.
Fuel Recirculating Tank and Pump
The fuel recirculating from the diesel generators is routed into the 100 USGal recirculating tank . The fuel can be routed into the fuel days tanks by opening valve No. 4, and then closing valve No. 5.
The fuel recirculating pump is controlled by high and low level switches in the recirculating tank, and by a Hand/Off/Auto switch which must be on AUTO for automatic control. The recirculating tank also has a locally mounted level gauge.
Start up and Shut Down Procedures / Preparation for Start up
- Inspect tanks, pumps and piping for leakage. Repair all damage and dispose of all leakage prior to starting any equipment.
- Ensure heat tracing system is operational; or in warm weather, switched off.
- Ensure generators are ready for start up.
- Ensure day tanks and recirculating tank, and all level switches and alarms, are operational.
- Clean out all strainers and filters.
- Ensure all air relief valves are operations, and their isolating valves open.
- Ensure pressure gauges, are operational, and their isolating valves open.
Start up
- Select a main tank and open the inlet and outlet valves.
- For normal operation, select the hand switches for AUTO. Ensure valves Nos. 1 and 2 are open and valve No. 3 is closed. Ensure pump belt drive is on low speed.
- If the pump is to be used to transfer or unload fuel, select the pump Hand/Off/Auto switch for Hand, and open and/or close the appropriate valves.
- Select the Hand/Off/Auto switch for AUTO.
- Ensure recirculating fuel from generators is routed into.
- Start diesel generators.
Transferring Fuel Between Tanks For example, assume fuel will be transferred from diesel oil tank.
- Open the inlet valve of diesel oil tank A.
- Open the outlet valve of diesel oil tank B.
- Select the Hand/Off/Auto switch for Auto.
- Select the Hand/Off/Auto switch for Hand switch on pump.
- Open and/or close the appropriate valves.
- Select high speed on the belt drive.
Monitor levels in tanks by using tank level gauges glasses.
Shut down
Switch off diesel generators.
Select PU-906 handswitch for OFF.
https://www.911metallurgist.com/plant-tailings-reclaim-process-water-system-startup-shutdown-procedure