Table of Contents
- High Capacity Variable Speed Cutting Mill
- Method of operation
- Grinding
- Operator & Safety Friendly
- Benefits and applications
- Bottom sieves
- Features and Benefits
- Particle Extraction Equipment
- Laboratory Cutting Mill
- Features and Benefits
- Variable Speed Cutting Mill
- Applications for what a Cutting Mill used for
- Before VS After Examples of Grinding with a Cutting Mill
- Cutting Mill Specification
- Rotary Knife Mill
- Features & Benefits
- Applications
- Rotary Knife Mill Method of Operation
- Grinding
- Practical, Convenient & Safe
- CM500 Benefits and applications
- Bottom Sieves of this Rotary Knife Mill
- Performance features 911MPECM500
- Knife Mill
- Feed Hopper / Rotor and Stator knives / Bottom sieves
- Large Industrial Waste Shredder
- Benefits and Applications
- Method of Operation
- Grinding
- Highly Operable & of the Best Safety Standards
- Bottom sieves
- Features, Benefits and Applications
- Infeed Hopper / Rotor and Stator knives / Bottom sieves
- Cutting Mill Specifications
Our line of cutting mills includes models which reliably process: soft, medium-hard, elastic, tough and, fibrous materials. All models are based on the same grinding geometry and feature. Depending on which model, our cutting mills may feature:
Variable speed and adjustable in a range from 700- 3000 revolutions per minute
A fixed rotational speed of 1500 revolutions per minute
This allows your mill to be adapted to different sample requirements like breaking behavior or temperature sensitivity. Additionally, our larger cutting mill features superior rotational energy storage technology which can improve the performance of the 3-kilowatt drive to up to 20 kilowatts. When necessary the according power is provided by a flywheel. The stored rotational energy in this flywheel provides additional energy & allows for grinding even difficult material like rubber products without blockage of the rotor. Therefore larger mill succeeds even with grinding tasks that cannot be processed by other mills. Another important feature is provided by the double-acting cutting bars which permit 18 cutting events per revolution thus allowing for a fast size reduction process. The large cutting mill can be equipped with the optional cyclone suction combination consisting of an industrial vacuum cleaner and a cyclone unit the vacuum cleaner generates an airflow that cools the sample materials as well as the grinding tools.
Furthermore, the airflow accelerates the discharge of the sample from the grinding chamber a particularly useful option when processing heat-sensitive samples the used air is channeled off into the vacuum cleaner whereas the cyclone separates the sample material from the air jet and collects it in a sample bottle. Cleaning our cutting mills is easy as can be. Just open the door, flip the hopper, and detach the router and bottom sieve with one simple move. This is completely tool-free and without bothersome screwing. Opening the mill only takes a few seconds in a combination of smooth surfaces cleaning the mill is particularly efficient so that cross-contamination between samples can be successfully prevented. Cutting mills reliably grind materials like secondary fuels, electronic scrap or circuit boards, wood, straw, and other plant parts, plastics, or toys to name just a few.
Furthermore, they are particularly for grinding materials which have to be aligned in the context of ROHS and to WEEE.
A wide range of accessories is available for cutting mills in order to customize the devices for specific application requirements. The rotors of the cutting mills are easily exchangeable without tools. The right choice whether a parallel section or 6-disc rotor depends on the sample properties and the requirements of the particular application.
The parallel section rotor is suitable for a wide range of elastic, soft, and fibrous materials.
The 6-disc rotor effectively grinds medium-hard and brittle samples.
Bottom sieves are available with aperture sizes from 250 microns to 20 mm (millimeters). In addition to stainless steel sieves, we also offer sieves made for grinding without heavy metal contamination. Depending on the application two different hoppers are available:
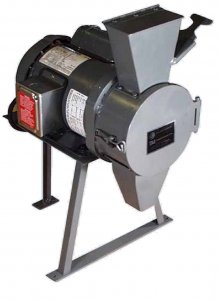
A standard hopper for universal use
A long-stock hopper
for feeding in long and bulky materials like hay, branches, or twigs.
The range of accessories is completed by collecting receptacles of various volumes. Ranging from sample bottles of 250 or 500 milliliters to 30 liter collectors. Furthermore, we provide different types of filters.
An important aspect of our products is operating safety. The specially designed sample outlet ensures that the grinding chambers cannot be accessed by hand; a feature that also applies to the hoppers. The rebound protection prevents material from splashing back. A combination of a safety switch, central locking device, and motor brake causes the rotor to come to a complete stop before the door can be opened.
All of the presented features and their outstanding performance makes our family cutting mills, the standard of industry and laboratory.
ON REQUEST, any of our cutting mills can by variable speed. Below is what ‘standard’ mills have for specifications:
911MPECM100, direct drive, variable speed
911MPECM200, direct drive, variable speed
911MPECM500, direct drive, fixed speed
911MPECM1000, fixed speed, indirect drive with V-belt and flywheel
911MPECM2500, fixed speed, indirect drive with V-belt and flywheel
911MPECM4000, fixed speed, indirect drive with V-belt and flywheel
High Capacity Variable Speed Cutting Mill
Superior High Capacity Cutting Mills with Variable Speed engineered for fast particles size reduction.
- Rapid reduction of large particles from 300 mm to 2 mm
- Quick and easy to clean
- Full range of bottom sieves
-
The 911MPECM-2500 can process samples of up to 150Kg/h
- The 911MPECM-4000 can finely cut samples of up to 200Kg/h
These Cutting Mills are used by laboratories and processing companies to granulate solid materials such as waste or wood and thermoplastics. The material to be processed falls into the cutting chamber via a guide chute and is shredded by cutting between rotating and fixed knives until it passes an attached sieve as ground product. The sieve extends over the lower half of the grinding chamber and can be changed easily. Final particle size is determined by the selected sieve perforation aperture.
Method of operation
Sieve dimension (free open surface) must be large in order to obtain:
- a high throughput
- a low heat creation
- a homogeneous result.
No other Cutting Mill is easier to clean then the 911MPECM2500 & 911MPECM4000 Cutting Mills. When the grinding process is finished the grinding chamber is fully accessible by unscrewing two hand screws and folding back of the infeed hopper. The grinding chamber is fully accessible for quick and easy cleaning in order to perform a fast and systematic cleaning of the grinding tools.
Select between the 911MPECM2500 & 911MPECM4000
|
|
Superior Cutting Mills engineered to reproducibly grind volumes from 100g of up to 200 kg/h.
Grinding
The Cutting Mill is the first machine in a state of the art sample prep. laboratory when it comes to sample prep. of cuttable materials. This system is suitable for the coarse and fine grinding of any dry substance, typically samples with a feed size of up to 350mm (CM 4000) and a total batch of up to 200 kgs per hour (volume depending on the characteristic of the samples) can be ground down to 2 mm or finer depending on the product.
Operator & Safety Friendly
Maximum Grinding performance and maximum safety are important for Cutting Mills. Due to the integrated safety switch the machine can only be started when the “Easy-Lock Cover“ is closed and the grinding chamber cover is inserted properly.
The Infeed Hopper as well as the housing of the CM2500 / CM 4000 is made from solid steel.
The ergonomic design of the machine and the positioning of the funnel and the starter box require a minimum space in the laboratory.
![]() 911MPEC-2500 |
![]() 911MPEC-4000 |
Benefits and applications
- Acoustic Noise Reduction: Infeed hopper made from Bondal, a vibration-damping composite material with a sandwich structure consisting of a viscoelastic core between two outer steel sheets.
- Various infeed hopper types are available
- Restrained opening of the infeed hopper due to a gas spring
- Massive grinding chamber made from vibration-reducing components
- Grinding chamber with safety switch for easy access and cleaning
- Flexible solid sample collector flange for optional extraction or connection to a collection vessels
- High precision solid steel underframe
- Industrial Castor wheels lockable
Bottom sieves
The size of the bottom sieve is important in order to decrease the heat created during the grinding and to increase the capacity. The sieve dimension is 240mm x 240mm. This assures a large open surface which is essential for the cutting process to:
- Obtain a high throughput (see graphics)
- Have a low heat creation during the grinding process
- Receive a homogeneous result
Features and Benefits
- Rapid sieve and knife changeover
- Quick and easy to clean
- Performance-enhancing diagonal cutting action
- No need to adjust the rotor knife
- Ideal granulate quality with similar grain characteristics
- No tool required to open
- Outer bearing assembly protected from dust ingress
- CE certified
Applications
- Linoleum, Carpets, Cloth
- Secondary fuels and Biomass
- Food and Animal food
- Wood, Paper, Carton, Cellulose
- Rubber, Shredder Light Fractions
- House Waste, Industrial Waste
- Computer Scrap and Electronic Scrap
- Plants, Twigs, Roots etc.
- Herbs, Spices, Gras, Straw
- Bones
- Technical Plastics such as ABS, PA, POM, PE etc.
Particle Extraction Equipment
![]() |
![]() |
The particle extraction unit is optional and not part of the basic package.
Bottom sieves of various sizes |
Rotor and Stator knives |
911MPECM-2500
911MPECM-4000
Laboratory Cutting Mill
Laboratory Cutting Mills are ideal in time-saving assistance in daily laboratory work they are suitable for size production of soft to medium-hard fibrous and tough materials plastics and heterogeneous mixtures we will demonstrate the key points of cutting mills and how they work. Our mills allow you to insert bulky samples that fall in so there is no need to manually break up the materials first. Laboratory Cutting Mills comminute sample materials with the rotors fitted with knives in combination with fixed skater knives by cutting and shearing forces due to the progressive cutting geometry between the cutting edges of the rotors and the fixed knives the sample material is automatically transported until the desired final fineness is achieved. The rotor has double cone bearings on the shaft and in the lid, the bearings ensure stable running and minimal wear. For each application we offer the appropriate cutting tools made of four (4) different materials:
- Stainless steel
- Tools steel
- Hard metal tungsten carbide
- Chromium free tool steel
For each application the perfect rotor, for example, the standard rotor with V-cutting edges especially for tougher elastic materials. Our sieve cassette guarantees the constant distance between rotor and sample material and always ensures an ideal result. Work even faster with the cutting mill sample exhauster with cyclone separator the sample is exasperated with negative pressure the advantage and even faster throughput and good cooling. Our Laboratory Cutting Mills are the ideal solution for your application. Fast, safe, simple.
- Rapid reduction of large particles from 80 mm to 0.25 mm
- Quick and easy to clean
- Full range of bottom sieves
- Collector volume 5 Liters
Features and Benefits
Acoustic Noise Reduction Infeed Hopper made from Bondal. Bondal is a vibration-damping composite material with a sandwich structure consisting of a viscoelastic core between two outer steel sheets. Various infeed hopper types are available with wooden/Teflon plunger
- Massive grinding chamber made from vibration-reducing components
- Solid door with safety switch for easy access and cleaning
- Solid 5 Liters sample collector with two side handles and a Plexi window for sample process observation
- High precision solid steel underframe with industrial castor wheels (lockable)
Variable Speed Cutting Mill
Cutting Mill with closed EASY LOCK DOOR |
Cutting Mill with opened EASY LOCK DOOR |
The Model 911MPECM100 Cutting Mill is used by Laboratories and processing Companies to granulate solid materials such as waste or wood and thermoplastics. The material to be processed falls into the cutting chamber of the CM100 via a guide chute and is shredded by cutting between rotating and fixed knives until it passes an attached sieve as ground product. The sieve extends over the lower half of the grinding chamber and is easily exchanged. The final particle size is determined by the selected sieve perforation aperture. No other Cutting Mill is easier to clean than the CM 100 Cutting Mill. When the grinding process is finished the front door can be opened sidewise and the rotor/infeed hopper can be taken out in order to perform a fast and systematic cleaning of the grinding tools. |
Applications for what
|
Before VS After Examples of Grinding with a Cutting Mill
Cutting Mill Specification
![]() |
![]() |
Rotary Knife Mill
Introducing the floor-mounted variable speed Rotary Knife Mill as you can see the instrument is mounted on a frame with four (4) casters the front two (2) of which are lockable for extra stability the instrument is supplied complete with a 3 kilowatt motor with additional flywheel mass. This delivers an optimal cutting performance which is unparalleled. This instrument is an extremely powerful and versatile machine that can be supplied with a very wide range of company accessories. This can facilitate many applications in areas common examples: refuse-derived fuels, the preparation of biomass and agricultural samples, electronic scrap, plastic parts, non-ferrous metals, and more.
We offer a very wide range of company accessories. The instrument can be supplied with a universal feed hopper or a long-stock hopper. Furthermore they are three (3) different types of rotor to allow for different types of material to be prepared in different application areas.
Depending on your needs, we have a range of cyclones whereby we can have suction provided by an industrial vacuum cleaner to pull through light and low-density sample materials. These can be collected in a variety of collection vessels including small removable glass bottles. We have a wide range of accompanying bottom sieves the maximum size aperture is 20mm (millimeters) and the range goes right down 0.25 mm (millimeters).
The rotors can simply be inserted using the rotor extraction tool. The bottom sieve at the right aperture can simply be inserted with ease. The operating principle is to exploits cutting and shearing forces. The parallel cut rotor we see 3 moving blades and 3 fixed cutting bars. All three (3) of which have double-acting edges. Furthermore, the instrument can be run from a minimum of 700 RPM to a maximum of 3000 RPM according to the application requirements. Therefore when combined with the use of the 3-kilowatt motor and the variable speed this leads to unparalleled cutting performance.
This Rotary Knife Mill is very straightforward to operate. You simply close the door set the required speed and press the start button. Once it’s reached the pre-set speed, simply take the sample material feed it in through the top of the feed hopper, and use the plunger system to push the material down into the crushing chamber. After some time, all of the sampling material will be expelled through the bottom sieve. Simply stop the instrument, remove the collecting receptacle and recover the ground material.
- Rapid reduction of large particles from 100 mm to 1 mm
- Quick and easy to clean
- Full range of bottom sieves
-
The 911MPECM500 can handle samples of up to 30Kg/hr
At only 50 centimeter wide, the Model 911MPECM500 Rotary Knife Mill is used by processing companies to granulate solid materials such as secondary waste, wood or thermoplastics.The material to be processed falls into the cutting chamber of the 911MPECM500 via a guide chute and is shredded by cutting between rotating and fixed knives until it passes an attached sieve as ground product.
The bottom sieve extends over the lower half of the grinding chamber and is easily exchanged. Final particle size is determined by the selected sieve perforation aperture.
Features & Benefits
- Rapid sieve and knife changeover
- Quick and easy to clean
- Performance – enhancing diagonal cutting action
- No need to adjust the rotor knife
- Ideal granulate quality with similar grain characteristics
- No tool required to open
- Outer bearing assembly protected from dust ingress
- CE certified
Applications
- Linoleum, Carpets, Cloth
- Secondary fuels and BioMass
- Food and Animal food
- Wood, Paper, Carton, Cellulose
- Rubber, Shredder Light Fractions
- House Waste, Industrial Waste
- Computer Scrap and Electronic Scrap
- Plants, Twigs, Roots etc.
- Herbs, Spices, Grass, Straw
- Bones
- Technical Plastics such as ABS, PA, POM, PE etc
A Rotary Knife Mill engineered for Superior reproducibly grind of volumes from 30g of up to 30 kg/hour
![]() |
![]() |
Rotary Knife Mill Method of Operation
The Model 911MPECM500 Rotary Knife Mill is used by Laboratories and processing Companies to granulate solid materials such as waste or wood and thermoplastics. The material to be processed falls into the cutting chamber of the 911MPECM500 via a guide chute and is shredded by cutting between rotating and fixed knives until it passes an attached sieve as ground product. The sieve extends over the lower half of the grinding chamber and is easily exchanged. Final particle size is determined by the selected sieve perforation aperture.
Sieve dimension (free open surface) must be large in order to obtain:
- a high throughput
- a low heat creation
- a homogeneous result.
No other Rotary Knife Mill is easier to clean then the 911MPECM500 Rotary Knife Mill. When the grinding process is finished the Front door and the Infeed Hopper can be opened sidewise and the milling chamber is fully accessible for quick and easy cleaning in order to perform a fast and systematic cleaning of the grinding tools.
![]() |
![]() |
Grinding
The Rotary Knife Mill is the first machine in a sample prep. Laboratory of today when it comes to sample prep. of cuttable materials. This system is suitable for the coarse and fine grinding of any dry substance, Typically samples with a feed size of up to 100mm and a total batch of up to 30kgs per hour (volume depending on the characteristic of the samples) can be ground down to 1,00 mm or finer depending on the product.
Practical, Convenient & Safe
Maximum Grinding performance and maximum safety is important for Laarmann Mills. Due to two integrated safety switches (door and collector) the machine can only be started when the “Easy Lock Cover“ is closed and the Sample collector is inserted properly.
The Infeed Hopper as well as the housing of the 911MPECM500 is made from solid steel.
The ergonomic design of the machine and the positioning of the funnel and the starter box require a minimum space in the laboratory.
CM500 Benefits and applications
Bottom Sieves of this Rotary Knife Mill
A full range of bottom sieves is available in various sizes. The size of the bottom sieve is important in order to decrease the heat creation during the grinding and to increase the capacity.
The sieve dimension is 230mm by 135mm which assures a large open surface which is essential for the cutting process to: obtain a high throughput (see graphics), have a low heat creation during the grinding process and receive a homogeneous result.
Performance features 911MPECM500
- Acoustic Noise Reduction In Feed Hopper made from Bondal. Bondal is a vibration damping composite material with a sandwich structure consisting of a viscoelastic core between two outer steel sheets. Various In Feed Hopper Types are available with wooden/teflon plunger
- Massive grinding chamber made from vibration reducing components
- Solid door with safety switch for easy access and cleaning
- Solid 30 Liters sample collector with two side handles and a plexi window for sample process observation
- High precision solid steel underframe
- Industrial Castor wheels lockable
Examples of what materials this Rotary Knife Mill can cut: before / after grinding photos
Knife Mill
Feed Hopper / Rotor and Stator knives / Bottom sieves
![]() |
![]()
|
Large Industrial Waste Shredder
- Rapid reduction of large particles from 100 mm to 0.5 mm
- Quick and easy to clean
- Full range of bottom sieves
-
The 911MPECM1000 can handle samples of up to 60 Kg/hour
The Model 911MPECM1000 Industrial Waste Shredder is used by processing companies to granulate solid materials such as secondary waste, wood or thermoplastics.The material to be processed falls into the cutting chamber of the 911MPECM1000 via a guide chute and is shredded by cutting between rotating and fixed knives until it passes an attached sieve as ground product.
The bottom sieve (240mm Length / 240mm Width) extends over the lower half of the grinding chamber and is easily exchanged. Final particle size is determined by the selected sieve perforation aperture.
A nice application to sell the 911MPECM1000 on is industrial waste. Electricity companies for example who buy the waste to produce electricity would like to know how much electricity they can get out of the batch they just bought. If they would use a small cutting mill, like the 911MPECM100, the product might be staying in the milling chamber for too much time,
resulting in heating up the sample.
In order to determine the amount of electricity the waste will provide, the company will check the caloric value. Inserting heat in the sample will either reduce the amount of moisture or add energy to the sample. Both ways the caloric value will seem higher than it is in reality.
Benefits and Applications
- Acoustic Noise Reduction: Infeed hopper made from Bondal, a vibration damping composite material with a sandwich structure consisting of a viscoelastic core between two outer steel sheets.
- Various infeed hopper types are available with wooden/plastic plunger
- Restrained opening of the infeed hopper due to a gas spring
- Massive grinding chamber made from vibration reducing components
- Grinding chamber with safety switch for easy access and cleaning
- Flexible solid sample collector flange for optional extraction or connection to a collection vessels
- High precision solid steel underframe
- Industrial Castor wheels lockable
Method of Operation
The Model 911MPECM1000 Cutting Mill is used by laboratories and Industrial Waste Shredders to granulate solid materials such as waste or wood and thermoplastics. The material to be processed falls into the cutting chamber of the 911MPECM1000 via a guide chute and is shredded by cutting between rotating and fixed knives until it passes an attached sieve as ground product. The sieve extends over the lower half of the grinding chamber and can be changed easily. Final particle size is determined by the selected sieve perforation aperture.
Sieve dimension (free open surface) must be large in order to obtain:
- a high throughput
- a low heat creation
- a homogeneous result.
No other Cutting Mill is easier to clean then the 911MPECM1000 Cutting Mill. When the grinding process is finished the grinding chamber is fully accessible by unscrewing two hand screws and folding back of the infeed hopper. The grinding chamber is fully accessible for quick and easy cleaning in order to perform a fast and systematic cleaning of the grinding tools.
![]() |
![]() |
Grinding
The Cutting Mill is the first machine in a state of the art sample prep. laboratory when it comes to sample prep. of cuttable materials. This system is suitable for the coarse and fine grinding of any dry substance, typically samples with a feed size of up to 100mm and a total batch of up to 60kgs per hour (volume depending on the characteristic of the samples) can be ground down to 0,5 mm or finer depending on the product.
Highly Operable & of the Best Safety Standards
Maximum Grinding performance and maximum safety is important for our cutting mills. Due to the integrated safety switch the machine can only be started when the “Easy Lock Cover” is closed and the grinding chamber cover is inserted properly.
The Infeed Hopper as well as the housing of the 911MPECM1000 is made from solid steel.
The ergonomic design of the machine and the positioning of the funnel and the starter box require a minimum space in the laboratory.
Bottom sieves
The size of the bottom sieve is important in order to decrease the heat creation during the grinding and to increase the capacity.
The sieve dimension is 240mm x 240mm. This assures a large open surface which is essential for the cutting process to:
- Obtain a high throughput (see graphics)
- Have a low heat creation during the grinding process
- Receive a homogeneous result
Features, Benefits and Applications
|
|
Infeed Hopper / Rotor and Stator knives / Bottom sieves
![]() |
|
Cutting Mill Specifications