Table of Contents
Cupellation is conducted in a muffle furnace, the construction of which is shown in Figs. 62-63. The fire is lighted, a little bone-ash is sprinkled on the floor of the muffle to prevent its corrosion by litharge in case of the upsetting of a cupel, and the cupels introduced as soon as a bright red heat is attained. The cupels are cleaned by gentle rubbing or blowing before being charged-in, and are again cleaned with bellows before the lead is charged-in. They are placed in the furnace one by one, or, better, charged-in together on a tray, see below.
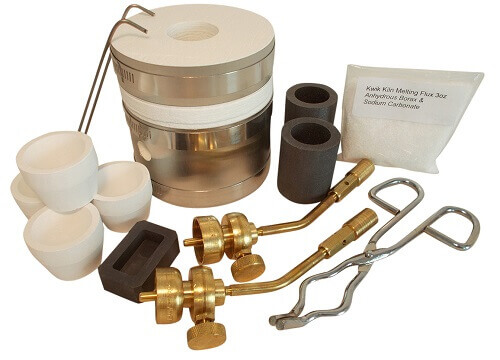
Cupels are little cups made of bone-ash, and are either round or square. In their manufacture the bone-ash is finely powdered so that it will pass a 40-mesh sieve, then slightly moistened with water (to which a little carbonate of potash is sometimes added), put into a mould (Fig. 65), and compressed by the blows of a mallet, or, better still, of a screw press, so as to cohere firmly. The mould is preferably made of steel, as gun-metal wears sooner, and an uneven surface is disadvantageous. It is kept clean, bright, and smooth, and the sides should be tapered upwards slightly to facilitate the removal of the cupel without injury. Cupels must be dried very carefully and slowly, but completely, as otherwise cracks appear when they are heated, and loss is thereby occasioned.
The cupels at the Royal Mint are made two years before being used, and are dried slowly on shelves at some distance from the assay furnaces. More rapid drying has been tried on many occasions with less satisfactory results. Nevertheless fair results, but not the best, can be obtained when using cupels only a few days’ old. If too much water is used in mixing the bone-ash, the cupels lose part of their porosity ; if too little is used they are too soft and crumble readily.
About 6 or 7 per cent, of water answers very well. Care must be taken to preserve cupels from the access of nitrous or other acid fumes. These are absorbed by the bone-ash and given out in the furnace so that they may cause spitting. Lengthened heating of an hour or more in the muffle before charging-in the lead buttons will prevent loss from this cause. It is always advisable to heat cupels for 15 minutes after they have attained the temperature of the muffle before charging-in the lead buttons.
Bone-ash of good quality is supplied by several makers. It may be prepared by calcining carefully clean knuckle-bones. The crude bone-ash is crushed through a 30-mesh sieve, and recalcined. Caustic lime and carbonate of lime are next removed by lixiviation with ammonium chloride, and the bone-ash, after thorough washing and drying, is graded by sieving, and is then ready for use. The old German assayers of the 16th century used wood ashes mixed with bone-ash for all but the surface of their cupels.
Magnesia was introduced a few years ago, as a substitute for bone-ash. It is strongly calcined, and does not absorb acid fumes. The cupels require to be made under high pressure, and should be baked at a high temperature before use. They are then as hard and strong as fireclay. Magnesia absorbs and holds less litharge than bone-ash does. For the absorption of gold by these cupels, see below.
The cupels having been sufficiently heated in the muffle, the lead buttons obtained as described are charged-in by the tongs (A, Fig. 94). The buttons collapse and lose their shape in a few seconds if the temperature is sufficiently high, but the molten mass formed is covered by a black crust for some time later. The crust then breaks up, and the brilliant surface of a liquid bath is seen.
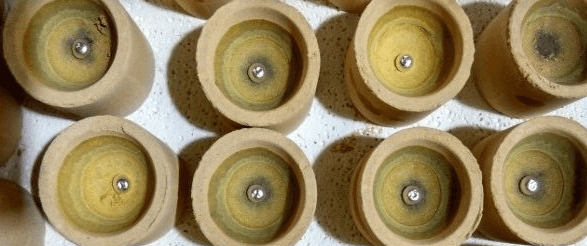
The muffle door should be closed immediately after the charging-in is completed, and kept closed until all the assays have thus “uncovered.” The door is then opened a little way to let in a current of air by which the lead is oxidised, and the litharge, floating to the edge of the bath, is absorbed by the cupel, together with the oxides of other base metals, which are not taken up by bone-ash if they are in a state of purity. Uncombined metals are not readily absorbed by the cupel, and only traces of gold and silver are carried into it by the litharge.
As the cupellation advances the lead bath is reduced in size by oxidation and absorption; reddish patches float slowly over its surface, appearing earlier in the richer assays; it becomes more convex and brighter; the red spots move more quickly and finally whirl round with great speed and then disappear; moving iridescent bands take their place for a moment and then disappear likewise, and the bead becomes suddenly much duller in appearance, thus indicating that the cupellation is at an end.
The cupels may then be removed from the muffle, provided the ore is poor or has little silver in it. It must, however, be remembered that silver absorbs oxygen when molten and gives it off suddenly when solidifying, so that if the bead weighs more than 0.01 gramme (Rivot) little fountains of metal are thrown up, and some part may be projected out of the cupel. This “ sprouting,” “ spitting,” or “ vegetation ” may take place in argentiferous-gold beads if the gold does not exceed one-third of the silver (Levol). At the Mint it is found that a still larger percentage of gold does not prevent spitting unless a trace of copper is present. Where spitting is to be feared, therefore, the cupel containing the silver bead is covered with a red-hot empty cupel, and is withdrawn gradually from the muffle so that the bead may cool slowly. Sprouting is avoided in this way. When the beads are very large (0.2 gramme or more) the muffle is closed and lifted up and the fire allowed to go out, as in the assay of silver bullion.
When cooled the beads often “flash”—i.e., brighten suddenly at the moment of solidification. This is due to the fact that the latent heat of fusion being released raises the temperature of the bead enormously, the metal having been in a state of surfusion at a temperature many degrees below its melting point. The flashing of small beads can rarely be observed.
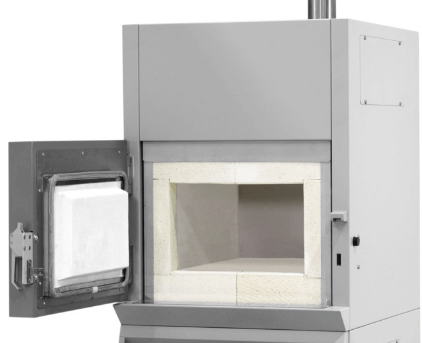
The proper temperature for cupellation of gold ores is the same as for silver ores. The lowest temperature at which good soft lead uncovers is about 675°—that is, a dull red heat—and a good temperature for the air in the muffle is 700°, which need not be reduced throughout the operation. Litharge freezes at about 640°. When antimony, iron, &c., are present, the temperature must be much higher, and time is saved in all cases by using a higher temperature at first, but the losses are then greater. The muffle should be at a full red heat, the cupel dull red, and the melted lead much more luminous than the cupel; the fumes should rise slowly to the crown of the muffle. Many assayers prefer to finish the cupellation at a temperature low enough to enable crystals of litharge to form in a ring round the cupel—that is, at about 625°—but it is doubtful whether there is any advantage in this. The temperature must be rapidly reduced at the finish by bringing the cupel towards the front of the muffle, and even then the feathers are not readily formed unless the cupel is almost saturated with litharge. It is probably better that the litharge should be completely absorbed. The formation of scales, due to low temperature, is accompanied by a sluggish heavy movement of the fumes, which fall in the muffle. On the other hand, “the heat is too great when the cupels are whitish,” the fused metal is seen with difficulty, and the scarcely visible fumes rise rapidly in the muffle (Mitchell). This statement is correct as far as it goes, but the temperature may be too low for these characteristics to be observable, and yet too high for cupellation. If the assays are long in uncovering they may sometimes be started by dropping on them a little charcoal powder wrapped in tissue paper, or, still better, by placing a piece of charcoal near them. If one freezes before completion it is restarted in the same way, or fresh lead is added or the temperature is raised, but the results are not good. Spirting or “spitting” of the lead may occur, due to the use of raw cupels, or to the presence of sulphur, arsenic, &c., in the lead.
The bead thus obtained should be well rounded and bright, loosely adherent to the cupel and slightly crystalline although malleable. If it contains lead it is more globular and brittle and its surface is very brilliant, while it does not adhere at all to the bone-ash. If copper is present in large quantities, the bead adheres firmly to the cupel, and in extreme cases its surface is blackened. Rhodium and iridium occasion black patches at the bottom of the bead ; platinum makes the surface of the bead crystalline and rugose. If the bead cracks on being flattened Van Riemsdijk recommends a second cupellation with some more lead and 10 per cent, of cupric chloride. In this way the metals with volatile chlorides are eliminated.
What Effect Base Metals have on Cupellation
Iron oxide is not readily fusible with lead oxide: the button is long in melting, and a brown scoria is sometimes left on the cupel, which may entangle lead globules and so contain gold. The lead may contain about 4 per cent, of iron, without the formation of any scoria. The cupel is stained dark red, and is moderately corroded.
Zinc burns with a brilliant green flame at first and volatilises; it forms a voluminous white or pale yellow scoria. The cupel is deeply corroded.
Tin gives a brown scoria if it constitutes more than 3 per cent, of the lead button. In all cases it floats to the top, oxidises, and forms a floating scoria which delays cupellation, but is subsequently carried off by the litharge. The cupel is stained pale brown.
Copper carries gold into the cupel and is usually not wholly removed from the bead. The cupel is stained dark brown or black.
Nickel and Cobalt are not so easily carried into the cupel as copper; they form a black scoria.
Antimony does not interfere if less than 2 per cent, is present. If 4 per cent, is present, a slight yellow scoria is formed, and the cupel is stained dark brown.
Arsenic at first burns with a blue flame and causes spitting. After a few minutes the flame turns greenish-white, and becomes very brilliant. The cupel is stained pale brown, and if 4 per cent, of arsenic is present, there is much pale brown scoria.
Manganese causes black stains and deep corrosion of the cupel, and forms a black scoria. The lead boils and spits.
Chromium gives a brick-red stain and a black scoria on the cupel, and aluminium a grey scoria; both these metals delay the course of cupellation. Chromium causes deep corrosion.
Cadmium causes a black sooty ring to form inside the cupel near its margin. When cupellation begins, the action is very violent, a yellowish-red flame is seen, followed by much spitting and the appearance of large red-hot scales floating on the lead. Oxide of cadmium is not absorbed by the cupel.
Tellurium is absorbed quietly, but whitish fumes appear, which give the bath a greenish-white appearance. The cupelled bead is sometimes, but not often, subdivided. The cupel has a brown stain in a ring round the litharge stain, but there is no scoria.
Selenium gives brown fumes, which change to blue fumes at a little distance. The effect on the cupel is similar to that of tellurium, but the brown stain is less pronounced.
Molybdenum causes slight boiling of the lead. The cupel is stained pale brown, and very deeply corroded, but there is no scoria.
Vanadium gives a dark red stain, and causes remarkably deep corrosion of the cupel, but leaves no scoria.
Thallium gives a pale brown, and bismuth an orange stain. Neither of these metals leaves a scoria.
Silicon gives a voluminous yellow or white scoria, which delays cupellation, and is left on the cupel.
Metal Losses in Cupellation
The loss during cupellation by volatilisation was proved to occur by Makins, but is insignificant. The absorption by the cupel is more serious. Rivot states that gold is oxidised to some extent at a red heat in the presence of antimonic oxide, litharge, or cupric oxide, and that it is the oxidised part which is absorbed by the cupel.
Still heavier losses may be caused by large amounts of scoria, in which the whole of the gold and silver may be retained in the form of minute beads, impossible to collect except by scorification with fresh lead. Small losses are sometimes caused by spitting, but these are usually trifling, as the spitting ceases before the lead bath becomes rich in gold and silver.
In some experiments made by the author, the exact losses due to the presence of base metals were determined. In each case 25 grammes of lead were cupelled with 1 milligramme of gold, 4 milligrammes of silver, and 1 gramme of the impurity. Bone- ash cupels made at the Royal Mint were used. The results were as follows:
Nickel and chromium caused total loss in each case, due to scoria.
Silicon occasioned losses amounting to between 40 and 50 per cent., due to scoria.
The losses in cupellation under the same conditions as to temperature, air supply and using similar cupels, but with pure instead of impure lead, were 1.2 per cent, of gold and 12.8 per cent, of silver. In no case was proof afforded of any loss by volatilisation. Practically the whole of the missing gold and silver was recovered by fusing the cupels when tellurium and selenium were present. The percentage losses observed in these experiments appear very large, but it must be remembered that the absolute losses were very small. It will be observed that the formation of a scoria was not necessarily accompanied by a heavy loss of gold.
The percentage losses are much smaller when the beads are larger. Thus metallurgists found that the loss on 5 grains of silver (= 324 mgs.) when cupelled with 175 grains of bismuth was 4.6 per cent., against a loss of 1.88 per cent, when lead was substituted for bismuth, and Ricketts observed a loss of 2.3 per cent, on the crucible assay of a lead ore containing 2,260 ozs. of silver per ton.
Lodge records that the loss in cupelling 200 milligrammes of gold with 10 grammes of lead ranged from 0.15 per cent, at 775° to 2.99 per cent, at 1,075°. The addition of 0.05 grams of copper increased the loss of gold from 0.15 per cent, to 0.25 per cent. In these cases the gold beads were apparently weighed without being parted.
The absorption by the cupel varies with the temperature and with the quality of the bone-ash, as well as with the amount of the impurities present, Crosse observed a loss of 5 per cent, in cupelling small amounts of pure gold with test lead. T. L. Carter found losses up to 10 per cent, of gold with a particular set of cupels. The author compared the absorption of gold and silver at about 900° by magnesia cupels with those of two samples of bone-ash cupels with the following mean results:
Bone Ash
The absorption by magnesia cupels, according to these tests, is not much greater than that by bone-ash. Whatever cupels are used, the absorption should be tested frequently. Losses of gold, and especially of silver, are greater at a high temperature than at a low one. This is illustrated by comparing the following mean results of experiments, in which the bone-ash cupels “ A ” were used, with the results in the table given above:
Examination of the Cupel
When rich ores are assayed, appreciable quantities of gold are carried into the cupel, especially if certain base metals are present in the lead button. To assay the cupel, all clean bone-ash is detached and thrown away, and the remainder crushed so as to pass through an 80-mesh sieve, and the charge made up as follows:
The fusion is made in an earthen crucible, and the resulting button of lead cupelled. The slag of the original fusion may be cleaned by adding it to the charge, when less fluxes will be required.