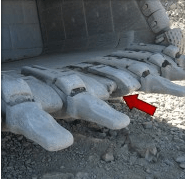
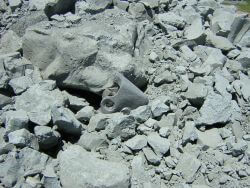
The fourth operating variable is the capacity of the crushing circuit. We have talked about the size of the ore, the hardness, and the condition of the equipment, the RPM, and the speed in which the crusher will crush the ore. The sum of these things add up to the crushing capacity of the crusher itself. If conditions are exactly right and not one of those variables are slowing production, the limiting factor may become the rest of the circuit. The rate of production will depend upon the slowest or weakest piece of equipment in the circuit. The throughput may be limited to the speed that a conveyor is taking the ore away or to a volume of ore, the chute is able to handle. Once the weakest link in the chain of crushing events is discovered it will become the controlling- factor in tonnage control.
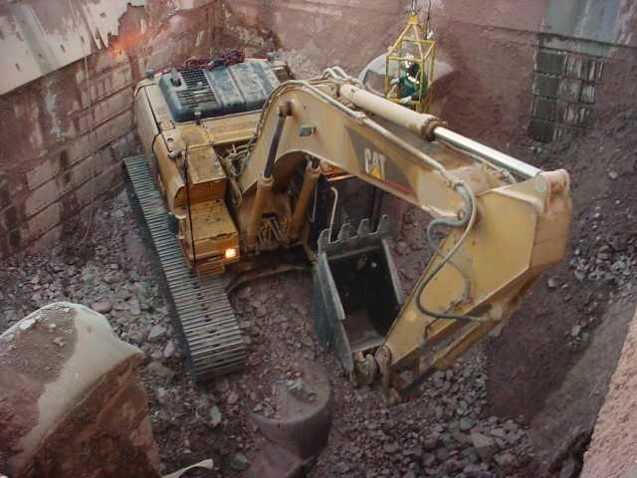
This is the last item about operating techniques. Our subject is foreign objects in the ore. We will show you some of the things to watch for, what the dangers are, and what to do about them.
Quite often the mine department will send things other than rock to the crusher to be crushed which ends up killing your crushing circuit capacity. This could be anything from rock bolts, drill steel and timbers to teeth and adaptors from the Electric shovels that load the trucks. Each of these things can do damage to the crushers or to the rest of the equipment in the circuit. It wouldn’t be reasonable to expect the operator to be able to stop every one of these potentially dangerous items from getting into the circuit, after all it may be buried in the ore or his attention may be elsewhere. If he does see it though, there are some things he can do to at least limit any damage, spill or plug up that may occur.
As soon as it is spotted an operator will know by its size and shape if it will go through the crusher or not. If it will and he can identify the material he will know where and what damage it can do. As an example a long piece of wood would not damage the crusher but it might plug a transfer chute to a conveyor. In a case like this, shutting the feed off and then checking the circuit until it is found may be sufficient. If it is small enough you may not even have to shut your feed off, just have your helper go look for it. On the other hand if it was a long steel bar that may rip conveyor belts, or a shovel tooth and adaptor that may jam in the crusher, don’t take a chance, shut-down, even under load. The down time involved in getting a loaded crusher going again is much less than digging one out by hand to unplug it, or having to replace a conveyor belt.
That pretty well finishes our description of the workings of a Gyratory crusher and some of the operating techniques required to run it. As I mentioned in the introduction we didn’t get into operating practices and procedures in this session. We stayed with what was common throughout the Industry. This was mainly because operating procedures tend to change with each individual mine and circumstance. They are, in many cases, a preference rather than a rule, so it was decided to leave that for later consideration.
Here is a safety procedure for working inside crusher cavity. Never the less, it is dangerous!
Watch how dangerous trap steel trapped in a crusher can be.