Table of Contents
The Problem with copper-pyrite ores
This flowsheet, is designed for the treatment of a copper-iron sulfide ore containing appreciable values in gold. The major portion of the gold is associated with the copper but the pyrite contains appreciable gold values also. The demand for pyrite for sulphuric acid also gives added incentive for the recovery of the pyrite in a marketable concentrate. The sulfide minerals in the ore are chalcopyrite and pyrite and the gangue is siliceous.
The flowsheet is designed for the production of a high grade copper concentrate followed by the production of a clean pyrite concentrate for further treatment to recover the gold values.
The copper pyrite separation Process Flowsheet
Crushing circuit of a copper pyrite ore
The crushing section shown consists of single stage crushing with a Forced Feed Jaw Crusher. The mine run ore is fed from the coarse ore bin by means of a Apron feeder to the grizzly Jaw Crusher. The grizzly undersize and crusher discharge product are delivered to the fine ore bin by means of a belt conveyor.
Copper pyrite ore Grinding circuit
The ore from the fine ore bin, delivered at a uniform rate by a Adjustable Stroke Belt Ore Feeder, is ground to minus 65-mesh in a Ball Mill operating in closed circuit with a Spiral Classifier. Reagents are added to the ball mill-classifier circuit for proper depression of the pyrite during the flotation of the copper.
Flotation process of Copper-Pyrite minerals
The flotation section is composed of two 8-cell “Sub-A” Flotation Machines. The copper section has four rougher cells, two scavenger cells and two cleaner cells for dual cleaning of the rougher concentrates. The rougher copper froth passes to the cleaner cells and the scavenger froth to the second rougher cell.
The copper tailing is conditioned with sulphuric acid to a near neutral pH in a Super-Agitator and Conditioner, and then subjected to a second stage of flotation for the production of a pyrite concentrate. The cell arrangement for the pyrite is the same as for the copper circuit. Dual cleaning is used in order to maintain a clean and high grade pyrite product.
It should be noted that recirculation of the various middlings and froths for cleaning is accomplished without the use of pumps. This demonstrates the complete flexibility of the “Sub-A” Flotation Machine for producing high grade concentrates.
The recleaned copper concentrates are either thickened or filtered direct. The filtering characteristics and tonnage will determine if direct filtering of the concentrates can be used or if thickening prior to filtering must be used.
The pyrite concentrates are also either filtered direct or thickened prior to filtering. The filtered pyrite concentrates are treated by roasting for acid production from the expelled sulphur and to produce a calcine for cyanidation.
The filtered pyrite concentrate, if low in gold and silver, is marketed for its sulphur content in making sulphuric acid or sulphur dioxide gas. Marketing of this low value concentrate depends on transportation costs to the acid plant. Increased demand for acid in industrial and chemical applications, or even in treatment of low grade ores makes the recovery of pyrite most attractive.
If the pyrite concentrate contains precious metals in commercial amounts, the product usually can be marketed to a smelter, particularly if it requires the extra iron in its smelter flux balance or has an acid plant where it can use the sulphur content.
In some cases, it may be practical to cyanide the pyrite fraction before marketing. The operation could thus realize a greater economic return. Laboratory tests will establish if the pyrite can be cyanided direct for gold and silver recovery or if it must be roasted, washed and leached before being subjected to cyanide treatment.
Sampling
Automatic Samplers are used to sample the feed, concentrates and tailings. A portion of the tailing is removed and treated on the Visual Sampler which consists of a ¾” Suction Pressure Diaphragm Pump and a Wilfley Concentrating Table. The flotation results and conditions can be controlled easily by observing the concentrate streak on the table.
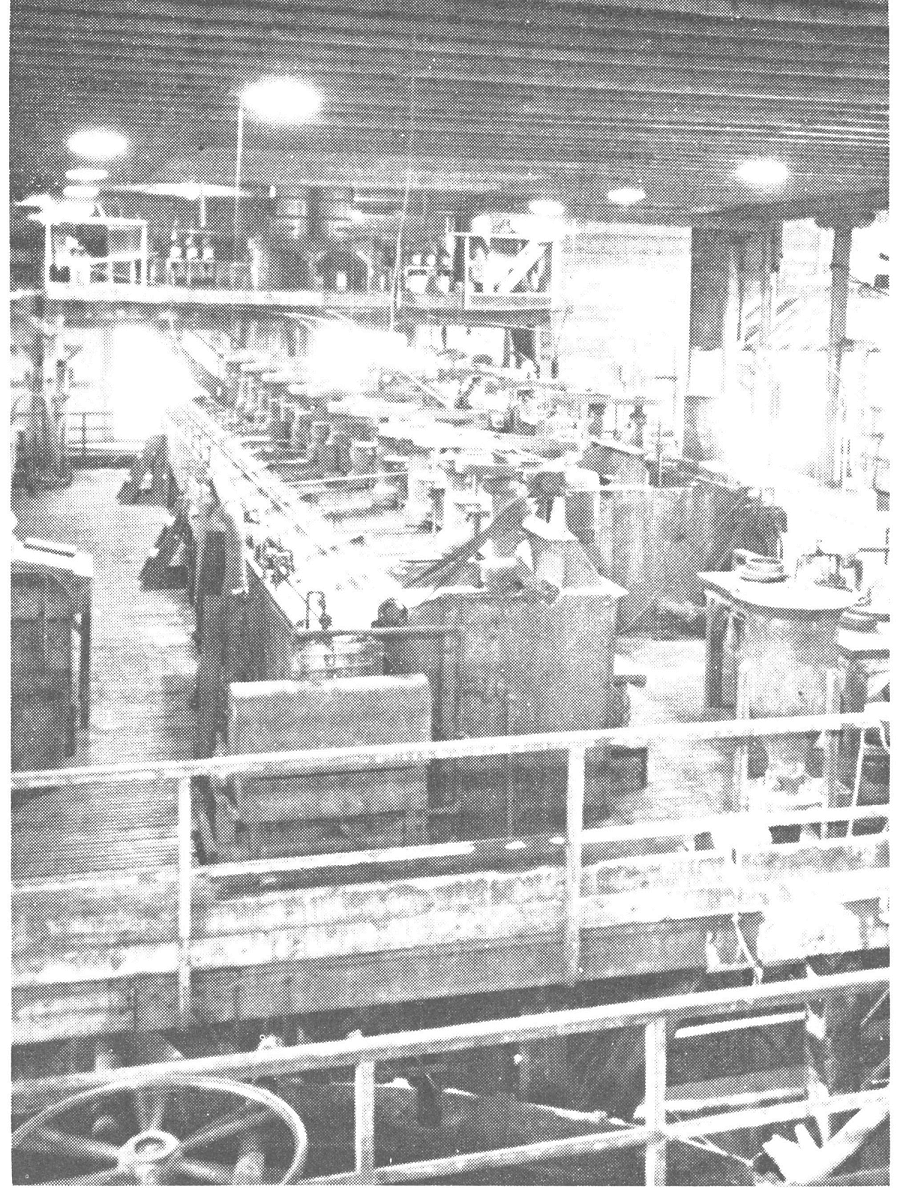
The Copper pyrite concentration process Summarized
The success of an operation of this type is dependent upon the production of a high grade concentrate. This is accomplished by the use of “Sub-A” Flotation Machines which provide the maximum flexibility in flotation operations, thus insuring the maximum grade of concentrates will be achieved.
The increased demand for sulphuric acid in industrial uses, and even in mining operations for extracting metals, makes it very important to consider recovering the pyrite in the overall development of the milling operation. This is worth considering, even in plants as small as 100 tons per 24 hours. Large tonnage operations find it most important to recover pyrite as a by-product to help pay a substantial share of operating costs and to produce greater profit in the overall operation.
https://www.911metallurgist.com/copper-flotation
Source: This article is a reproduction of an excerpt of “In the Public Domain” documents held in 911Metallurgy Corp’s private library.