Table of Contents
We studied the precipitation of copper from dilute acidic sulfate solutions using shredded automobile scrap in a rotary drum. The tests established that the scrap in the rotary drum precipitated copper faster and more completely than shredded, detinned, tinplate scrap in a launder, with comparable iron consumption. Although power is required to rotate the drum, the faster precipitation and continuous recovery of cement copper are advantages of the tumbler method. Cost evaluation indicates that the rotary drum method, which uses relatively low-cost and readily available shredded automobile scrap, is competitive with the launder method, which uses relatively high-cost shredded tinplate scrap or detinned shredded cans.
The first recorded domestic production of cement copper was 8,200 tons in 1921. By 1967 production had expanded to about 200,000 tons annually. Presently, about 300,000 tons of shredded tin cans and tinplate scrap are used annually for the production of cement copper. New facilities to leach porphyry mine waste dumps will further increase production in the near future.
Two methods are used in current cementation practice. The first method consists of passing acidic copper-bearing leach solutions through launders containing shredded tin cans. The second method, developed by Kennecott Corp., uses shredded and detinned cans and tinplate scrap in cone-type precipitators. The copper-bearing solutions are pumped through nozzles into the cones to impinge on the shredded scrap, causing a reaction with the iron and scouring the surfaces of the shredded scrap. The copper precipitates as cement copper by a reaction with iron which goes into solution in accordance with the following chemical equation:
CuSO4 + Fe → Cu + FeSO4…………………………………………………(1)
Shredded cans are commonly used because of their high ratio of surface area to weight, which promotes rapid precipitation.
Nadkarni and Wadsworth state that copper cementation is a first order reaction rate process. However, deviations from first order kinetics were observed at low stirring speeds and attributed to the buildup of copper on the iron surface, increasing the diffusion path length. Based upon these observations, it was conjectured that automobile-body iron, which has less surface area per pound than cans, would be effective if the cemented copper was removed rapidly to produce clean iron surfaces. Presumably iron materials more massive than shredded tinplate could be tumbled to constantly abrade cemented copper and thereby speed the reaction. These considerations suggested that automobile scrap iron, which has an appreciable surface area without great weight and is cheaper and more readily available than shredded tinplate scrap, might prove a suitable and economic substitute for copper cementation. Investigations were initiated to assess the comparative merit of using shredded automobile scrap in a rotating drum and shredded tinplate in launders for copper cementation. The materials, equipment, and procedures used are described, and the results are compared as to both efficiency and cost of operations.
Materials, Equipment, and Procedures
Two samples of automobile scrap were tested. The first sample was composed of pieces of automobile metal that had been cut into 6- by 6-inch pieces and leached for removal of nonferrous metals. After crimping, this sample had a bulk density of about 30 pounds per cubic foot. The second sample was the magnetic fraction from a commercial automobile shredding operation. The pieces were crumpled and compacted to a bulk density of 66 pounds per cubic foot. This material was coated with rust and magnetic scale; pieces of fabric, rubber, and other foreign impurities were entrapped in the crumpled iron.
The shredded precipitant used was clean, detinned, tinplate scrap from a can manufacturer. The bulk density of this material was approximately 19 pounds per cubic foot.
The copper-bearing solutions used for the cementation studies were compounded from technical-grade reagents to approximate the composition of leach liquors normally produced in cementation operations. Unless otherwise stated, the solutions contained about 1.6, 1.6, and 2.5 grams per liter of Cu, Fe++, and H2SO4, respectively. The pH of the compounded solutions was about 2.0.
The rotating-drum precipitator, shown in figure 1, is a stainless steel cylinder 18 inches in diameter by 36 inches long, equipped with thirty-six 1 – by 4-inch evenly spaced lifters. The drum was mounted on trunnions in a horizontal position and was rotated by a variable-speed-drive mechanism. In this position and with a centered inlet and outlet 6 inches in diameter, the capacity of the drum was about 10 gallons. Weighed samples of the iron precipitant were charged to the drum, and copper-bearing solution was metered into one end. Cement copper and solution were discharged from the other end of the drum. The discharged solution and cement copper were collected in a basin, allowed to settle, and the clear supernatant liquor decanted. About 4 hours of operation were required to establish a state of dynamic equilibrium prior to sampling.
The gravity launder used in the investigations comprised three sections connected in series with a 1-inch drop between sections. Each section was 1 foot by 1 foot in cross section and 4 feet long. Centered in each section was a lateral baffle to prevent short circuiting of the solution. The overflow weirs between each section were V-notched laterally and fitted with sampling devices. Weighed samples of iron precipitant were charged to the individual launder sections, and copper-bearing solutions were metered to the head of the launder. The solution was allowed to flow by gravity through the beds of iron. At intervals, solution samples were withdrawn at the overflow weirs to determine the progress of the copper cementation. The launder, also shown in figure 1, was used as the settling basin during the other phase of the investigation.
In tests using the drum precipitator, iron was charged batchwise, but solution flow and the removal of the cement copper were continuous. In tests using the gravity launder, the iron was charged and the cement copper removed by batch operations. The copper-bearing solution was metered to the head of the launder and allowed to flow continuously through the bedded iron precipitant.
For the reported test results, reliance was placed upon solution analysis. Each solution sample was acidified with 1 to 3 drops of concentrated H2SO4 per 150 ml of sample to prevent hydrolysis of the iron. The sample dilution lay this procedure was insignificant, and the iron analyses correlated well with a balance of the iron byproducts.
The cementation tests were conducted at ambient temperatures, and test data showed reaction temperature variations from 18.5° to 23.5° C. The temperature during the launder test averaged 21.5° C, and the drum tests averaged about 23° C. Temperature effects were inconsequential within this
range.
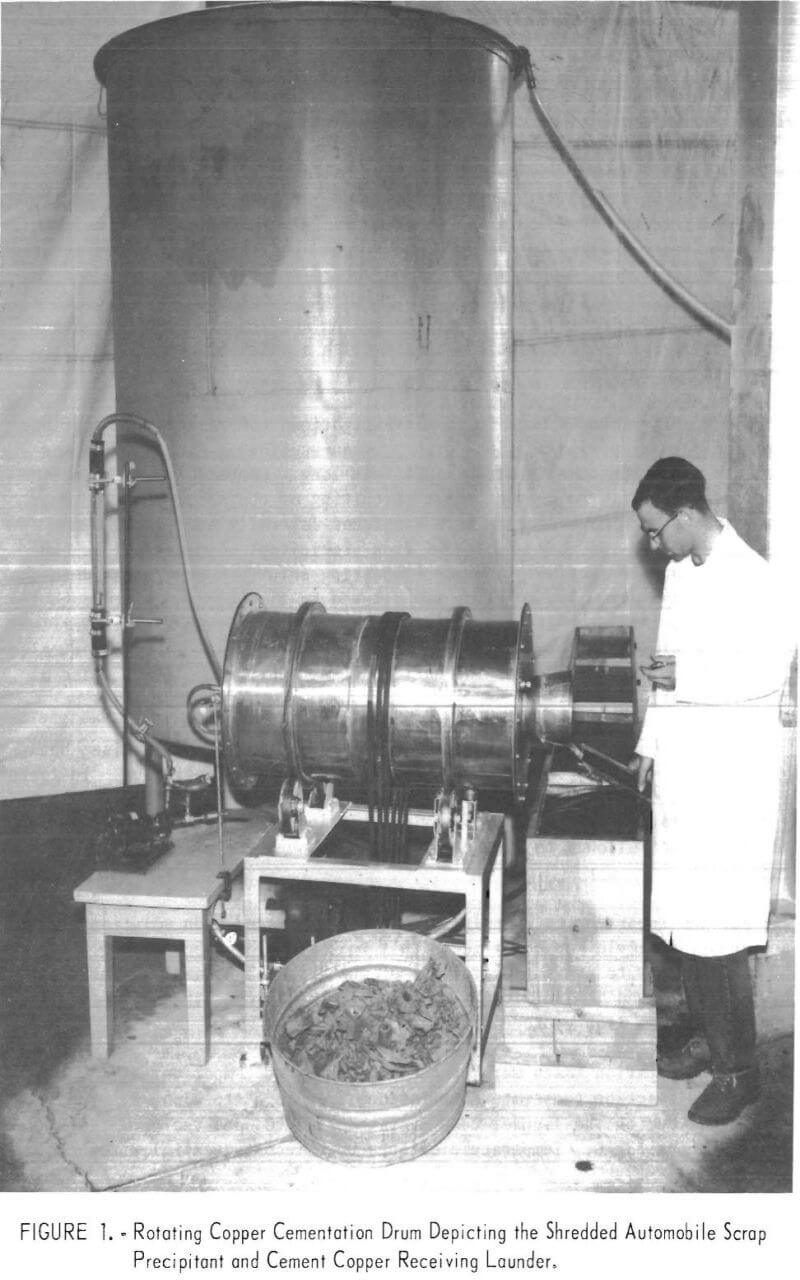
Copper Cementation with Automobile Scrap
Effects of variations in the operation of the drum were determined. Based upon this information further tests were conducted to define a set of operating conditions for optimum copper recovery.
The extent of copper precipitation by iron is dependent upon surface area rather than weight, and for comparable test results equivalent iron areas must be used. In the preliminary phase of the investigation, equal-weight samples of the same type of iron were used as an indirect means of maintaining equal surface areas. Copper recoveries varied as much as 8 percent. The differences in recovery were attributed to variations in surface area per unit weight of each sample of iron. However, the repeated use of the same iron sample without additions to compensate for loss in iron weight gave copper recoveries within 1.8 percent for five consecutive tests with equivalent test conditions. The latter procedure was used throughout the investigation to minimize the effect of variations in iron surface area.
Rotating Drum Operating Variables
The effects of maintaining a reducing atmosphere in the drum, the location of the discharge orifice, variations in the revolving speed, and variations in the solution feed rate were determined using 60 pounds of 6- by 6 -inch pieces of iron free from paint and rust. Results of these tests are presented in table 1.
Open Versus Closed Drum
Tests 1 and 2 were conducted to determine the effects of maintaining a reducing atmosphere in the drum. This was accomplished by closing the drum in test 2 with rubber gaskets and slip joints and retaining the H2 evolved by the reaction of metallic iron with the acid in the copper-bearing solution. The open drum used in test 1 allowed air to circulate freely during the reaction period. The copper recoveries of 74.9 and 74.5 percent showed that there was essentially no difference in results from the two procedures.
Peripheral Versus Center Discharge
Comparing the results from tests 1 and 3 shows the effect of discharging the cement copper pulp from the center of the drum, in contrast to discharging from the periphery through an adjustable orifice. In both cases the drum volume was maintained at 10 gallons. Copper recoveries increased from 74.9 to 80.6 percent by changing from peripheral to center discharge. Chemical analyses of the respective cement copper products showed less iron in the center discharged product. Apparently, the cement copper and abraded iron were retained in the drum longer, and more complete precipitation was attained with the center discharge.
Drum Rotating Speed
The effect of the drum speed is demonstrated by tests 3 and 4 and/or 5 and 6. In both examples increasing the drum rotating speed increased copper recovery. Apparently the greater agitation enabled more complete contact between solution and clean iron surfaces and also led to a more complete consumption of abraded iron, thereby lowering the iron content of the cement copper.
Solution Feed Rate
Tests 3 and 5 and/or 4 and 6 indicated the effect of variations of the solution feed rate. In these tests the solution feed rate was the independent variable, but the dependent variable of solution retention time was more causally related to copper recoveries. With a drum capacity of 10 gallons, the retention times were 20 and 10 minutes for feed rates of 0.5 and 1.0 gallons per minute, respectively. Copper recoveries increased with solution retention time.
Drum Operating Conditions
The next phase of the experimental work was designed to determine a set of operating conditions that would ensure a high copper recovery. Two methods were examined; namely, repeated passes of the solution through the precipitator and charging the maximum amount of iron to the drum. In addition, the solution feed rate and/or rotating speed were varied when using the maximum iron charge.
Stagewise Cementation
For this test a 60-pound sample of 6- by 6-inch clean automobile scrap was charged to the drum. The solution feed rate was maintained at 1 gallon per minute, the drum rotating speed was set at 8 rpm, and the solution passed through the drum three times. The cement copper was recovered between the stages and was not returned to the system. The results of this test are presented in table 2. The first of the repeated passes through the drum extracted about 78 percent of the contained copper. Extractions decreased markedly in the next two passes , the iron consumed per pound of copper precipitated (iron factor) increased, and the grade of the product decreased. These results indicate the repeated-pass procedure is ineffective for achieving a low iron factor and maximum recovery of a high-quality product. Future work will examine the possibility of recycling portions of the cement copper product to achieve better utilization of the iron.
Copper Cementation with Shredded Automobile Scrap
Shredded automobile scrap from a commercial source was used to determine the behavior of this type of iron in the drum precipitator. The precipitant was the magnetic fraction of the shredded automobiles. It was partially oxidized and still contained minor amounts of fabric, rubber, etc. Bulk density of the shredded scrap was 66 pounds per cubic foot. The initial scrap charge weighed 120 pounds. Both the solution feed rate and the drum rotating speed were varied to determine the conditions that would yield an optimum copper recovery. A recording wattmeter was connected to the drive motor to measure the power consumed. Test conditions and results are given in table 3.
Comparison of the results of tests 1 and 2 (table 3) indicates that the drum had an appreciable overcapacity at a solution feed rate of 0.57 gallon per minute. Copper recoveries decreased only from 95.2 to 94.4 percent with a two-thirds greater flow. With a drum solution volume of 10 gallons, the respective solution retention times were 17.6 and 10.5 minutes.
Chemical analyses of the cement copper products indicated a decrease in iron content when the speed of the drum was increased from 8 to 12 rpm, and an increase when the speed was increased from 12 to 20 rpm. The iron content of the copper product decreased from tests 1 to 3 because readily abraded but unreacted rust and scale on the iron was almost completely removed and included with the cement copper in tests 1 and 2. However, tests 3, 4, and 5 showed the effect of drum rotating speed upon the copper recoveries and the iron content of the cement copper products without the rust and scale initially present on the iron. The results indicated that, as the drum speed was increased, recoveries remained the same and the iron content of the respective copper products increased. Apparently, the iron was abraded concurrently with the cemented copper, and its only effect was to contaminate the product.
The power requirement per pound of copper recovered varied with the test conditions. In tests 1 and 2 where the drum speed, weight of iron used, and power consumed were the same, the power required per pound of copper recovered was inversely proportional to the solution feed rate. The conditions employed in tests 3, 4, and 5 precipitated essentially the same amount of copper, but the power consumption increased with increased rotating speed. Above 12 rpm, the only effect was the needless consumption of power.
Iron Consumption
As previously noted, the chemical reaction for copper cementation is
CuSO4 + Fe → Cu + FeSO4………………………………………………(1)
One pound of copper is precipitated by 0.88 pound of iron stoichiometrically.
In actual practice, iron factors normally range from 1.5 to 2.5. The reactions responsible for the excess iron consumption are
Fe2(SO4)3 + Fe → 3 FeSO4……………………………………………………(2)
and H2SO4 + Fe → FeSO4 + H2…………………………………………….(3)
These three reactions occur simultaneously, but the reduction of copper and ferric iron is rapid when compared to the dissolution of iron by the acid.
Except for the three-stage test, the iron factors defined in this study, which were based on solution analyses, ranged from 0.92 to 1.11, These values, which are lower than those of commercial operations, can be attributed to the low ferric iron content of the compounded leach solution.
In a series of tests with conditions similar to test 3 (table 1), the iron precipitant was removed between each test and the weight loss was determined. The iron factors determined by this procedure were 1.10, 1 11, and 1.12 pounds of iron per pound of copper recovered. These figures were slightly higher than the iron factors determined on the basis of solution analyses. Apparently hydrolysis of the dissolved iron decreased the iron content of the solution samples.
Another test within this series used a solution to which 1.53 grams per liter of Fe+3 had been added in the form of Fe2(SO4)3. The resulting iron factor was 1.58 pounds of iron per pound of copper recovered. The excess over the experimentally determined 1.11 pound of iron per pound of copper was consumed by the reduction of ferric iron. The conversion of copper to cement copper was 67.7 percent, and the conversion of the ferric iron to ferrous iron was 71.6 percent. Thus, it appears that reactions 1 and 2 proceed simultaneously and at essentially the same rate when copper and Fe+3 ions are present in about the same concentrations.
Cement Copper Purity
A previous investigation has shown that the solubilized impurities in dump leach solutions do not appreciably contaminate the cement copper produced. Therefore, synthesized solutions approximating average dump leach solutions were used in this study. The previous investigation also showed that the main source of contamination of cement copper is insoluble material associated with the iron precipitant. The commercial shredded automobile scrap used in the current investigations resulted in cement copper products which contained 83.2 to 90.8 percent copper. The insoluble content of the initial cement copper product was 0.67 percent which decreased to 0.10 percent in a 24-hour cementation period. The indicated median insoluble content was 0.37 percent, which compares favorably with industrially produced cement copper which contains between 1.0 and 3.0 percent insolubles.
Use of precleaned automobile scrap iron as the precipitant resulted in the production of a higher grade cement copper. Chemical analyses of the products reported in table 1 were 90.5 to 94.3 percent copper, 0.10 to 0.80 percent iron, and 0.05 to 0.10 percent insoluble material. Most of the remaining impurity was oxygen that had reacted with the copper during drying.
To determine the extent of oxidation, a dried sample of cement copper from test 5 (table 1), was reduced with hydrogen for 1 hour at 700° C. Iron and insoluble material remained at 0.10 and 0.08 percent, respectively, but the copper analysis increased from 92.3 to 99.7 percent. Spectrographic analysis showed the presence of 0.01 to 0.1 percent Al, Ca, Ni, Pb, and Sn and 0.001 to 0.01 percent Cr, Ge, Mg, Mn, Mo, and Ti in the final product.
Comparison with Shredded Tinplate-Gravity Launder Procedures
For the shredded tinplate-gravity launder test, the previously described 12-cubic-foot launder was charged with 206 pounds of shredded material. A copper-bearing solution was metered to the launder at a rate of 0.93 gallon per minute. The solution flowed by gravity through the bedded iron and overflowed the other end of the launder. The bulk density of the iron was about 19.0 pounds per cubic foot, the average solution contact time was 97 minutes, and the duration of the test was 21 hours. Analyses of starting and ending solutions indicated that copper recovery of 95.5 percent was attained. Iron consumption was 1.09 pounds iron per pound of copper.
Observations made during the test revealed that the cemented copper formed a loosely adhering spongy mass that subsequently was easily removed from the iron. Duration of the test was insufficient to completely consume the iron or to disclose any problems associated with the buildup of cement copper in the bedded iron.
A comparison of the shredded tinplate-gravity launder test results with data from a representative test using automobile scrap in the drum (test 3, table 3) shows that slightly more copper was recovered in a much shorter reaction time by the latter procedure. The respective copper recoveries were 95.5 and 97.2 percent, and the reaction times were 97 and 10 minutes. Also the amounts of iron precipitant charged were 206 and 120 pounds, and the iron factors were 1.09 and 1.06 pounds, respectively. With the drum precipitator, the cement copper was removed from the iron and recovered continuously, whereas with the launder the copper was removed from the iron manually and recovered as a batch operation at the completion of the test.
Cost Evaluation
Costs for copper cementation by the automobile scrap-rotating drum method and the shredded tinplate-scrap-gravity launder procedure were compared. Laboratory data were used to estimate costs for the automobile scrap-tumbler method of cementation, and published operating data from current periodicals were used to derive the cost for the detinned tinplate-scrap-gravity launder procedure. Plants producing 10 and 50 tons of cement copper per day were evaluated as typical small and intermediate-size operations. The comparison of these cementation procedures was based only on the cementation and dewatering steps. Costs were estimated on the basis of requirements for constructing and operating these units, including their proportionate share of the plant utilities and facilities. All costs were for 1966 and the equipment costs corresponded to a Marshall and Stevens equipment cost index of 252.5. Operating costs were estimated on the basis of a 350-day, rated-capacity operating year. Average operating labor cost was taken to be $3 per hour. The plant was depreciated on a straight-line basis over a life of 12.5 years. Prices used in the evaluation of shredded auto¬mobile scrap and tinplate scrap were $32 and $55 per ton, respectively.
An important factor in determining the economics of the rotating drum method was the cost and replacement life of a tumbler lining. Because no data were available on the life of linings under the tumbling action of the sharp sheared edges of automobile scrap, several lining materials were considered. A 1-inch urethane lining was selected upon recommendation by a company with considerable knowledge and experience in lining equipment for various applications. Based on their judgment, this lining was assumed to require replacement every 3 years
Cost estimates for the 10-ton-per-day (tpd) operation were based on using two urethane-lined steel tumblers, 12 feet in diameter by 27 feet. For the 50-tpd operation, 10 such tumblers were used.
The flowsheets for producing 10 and 50 tpd cement copper are similar. In the rotating drum method, a solution containing about 15 grams per liter copper is pumped into a urethane-lined drum containing automobile scrap. The precipitated copper and barren solution are discharged from the tumbler, and cement copper is thickened in a cone thickener, filtered, and shipped. In the gravity launder method, the 1.5-gram-per-liter-copper solution is pumped into a series of cementation cells containing shredded tinplate. The precipitated copper is washed and drained into settling tanks. After the cement copper settles, the clear water is decanted and recirculated for leaching. The cement copper is further drained, air-dried to 15 percent moisture on drying pads, and shipped.
Capital requirements and operating costs based on 12.5-year depreciation for the 10- and 50-tpd operations are summarized in table 4.
Cost evaluation shows the capital costs for the tumbler method to be considerably greater than those for the gravity launder method. The lower cost of automobile scrap compared to shredded tinplate scrap decreases the operating cost, but the high cost of relining drums partially offsets this advantage.
For the 10-tpd plant, the unit production cost is $138 per ton of cement copper, using the tumbler method, compared with $135.14 per ton by the gravity launder method. For the 50-tpd plant, the unit production cost is $119.54 per ton of cement copper by the tumbler method and $128.51 per ton by the gravity launder method.
At 10-tpd capacity, the gravity launder method is more economical than the rotating drum. The higher investment required for the rotating drum method would be offset by the lower production cost of this method for the 50-tpd plant at a return on original investment up to 9.4 percent. At higher return, the gravity launder method would be more economical.
Rotating Drum for Copper Cementation using Automobile Scrap
Conclusions
Automobile scrap is an effective and efficient precipitant for copper when used in a tumbling device. The cementation reaction is enhanced by the tumbling action which abrades the cemented copper and leaves fresh clean iron surfaces.
A rotating drum precipitator with a center discharge is superior to a peripheral discharge through a restricted orifice. Higher copper recoveries, lower iron factors, and a higher grade copper product are attained. Apparently fine-sized abraded iron particles are retained in the center discharge drum long enough to be consumed by the cementation reaction.
With precleaned automobile scrap as the precipitant, a high-grade cement copper product can be produced. A dried and partially oxidized sample of cement copper that contained 92.3 percent copper was reduced with hydrogen, and the resulting product was 99.7 percent copper.
Comparison of the shredded tinplate-gravity launder procedure with the automobile scrap drum precipitator indicated that higher copper recoveries were attained in less reaction time by the latter procedure. The cement copper was recovered as a batch process from the launder, whereas the copper was recovered from the drum precipitator as a continuous process.
The fixed capital costs for the rotating drum method are considerably higher than those of the gravity launder method, This adverse factor, however, is offset somewhat at higher copper production tonnages by the lower cost of automobile scrap as compared with tinplate scrap., This general evaluation of the drum precipitator method is not conclusive because of lack of data on wear of the drum lining. However, based on the assumption that a 1-inch uretnane lining will have a replacement life of 3 years, the rotating drum method has an economic advantage if a 9.4-percent return on original investment is adequate for a 50-tpd plant. This return would amount to a 21-percent return on the average investment during the depreciation life of the plant.