About six years ago the writer had occasion to visit a large magnetic iron-ore concentrating-plant, and then saw for the first time rubber belts employed for conveying-purposes. These Conveyor Belts were from 20 inches to 30 inches in width, and some of them were as long as 500 feet between centers. When I spoke of the enormous amount of material they handled with a small expenditure of power, the superintendent assented, but at the same time complained that although he bought the best quality of belts, the abrasion of the ore wore them out very rapidly, causing continually very large bills for repairs and renewals.
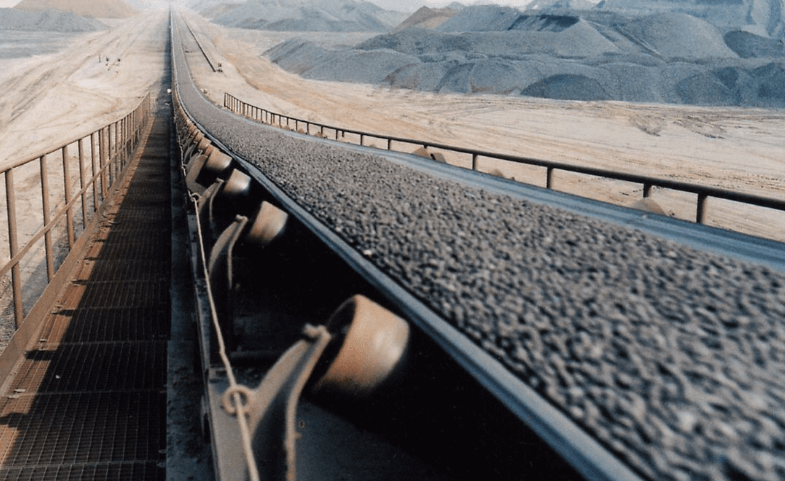
On close examination several interesting points were discovered
- It was noticed that the thin layer of rubber which covered the belt resisted the abrasion much longer than did a corresponding thickness of the cotton duck which formed the body of the belt; in fact, the life of the cover represented about one-half the life of the belt, although forming less than one- fifth of the total thickness.
- Each layer or ply of duck wore out more quickly than the one preceding it, showing that the fibers were cut more easily when under tension, and, of course, the tension on each fiber increased as the number of fibers bearing the tensile strain diminished.
- The wear was greatest in a line along the center of the belt. Frequently this part would be so quickly destroyed as to cause the belt to split in two longitudinally, though at the same time the portion nearer the edges was almost as good as new.
Noticing these facts, it became obvious that the functions of the cotton duck should be solely to give the belt tensile strength, and that it ought to be so protected by some abrasion-resisting cover that it would not be injured by contact with the material conveyed. It is also evident that this protecting cover ought to be of extra thickness over the center of the belt, in order to stand the harder work forced upon that part. Being engaged then, as now, in rubber manufacture, it was a simple matter to make a belt with a heavy rubber cover on the carrying side and thicker in the center than at the edges.
This reinforced cover renders the resistance to wear equal in all parts of the belt, and although being merely the anticipation of a patch, like the brass toe-cap on the schoolboy’s shoe or the two-ply seat in his trousers, it was, like them, deemed patentable.
The ideal conveying-belt would be like the celebrated “ one hoss shay,” which disintegrated so evenly and completely when its work was done that there was nothing left to repair or regret.
Wishing to ascertain what particular compound of rubber would make the most durable carrying-surface, I made a lot of small samples, each mixed differently, and exposed them to a very powerful sand-blast, which in its effect approximated the conditions to which the compound would be subjected in actual use, but it was more convenient for a large number of tests, being much quicker. The result of the first series of experiments indicated what grades of gum and what adulterants had better be left out, and also showed something that was very gratifying, namely, that there were certain adulterants which could be used in sufficient quantities to bring the cost down to a reasonable figure. I then made a second set of samples, following in the mixture the formula used in the more successful ones of the first set, but each new one was an attempt to improve upon its prototype. Some of the samples, owing to more intelligent methods in mixing them, proved so durable that the sand-blast test became too tedious, and a more severe and expeditious one was needed. This was found in exposing a disc of the rubber 6 inches in diameter by 1/8 of an inch thick to a heavy falling stream of crushed ore. The ore averaged about ¾ of an inch in size, and was delivered in a compact and heavy stream from the end of a very fast-moving belt. The sample was so fastened to a board as to receive the whole stream of ore and immediately deflect it. In this way the rubber came in contact with 200 tons of ore per hour, of which each fragment was delivered with considerable force full upon it. At first it was easy to see the comparative loss of weight after the sample had been exposed to the ore for an hour or two. In the next series results were very apparent after a day’s run, but later, as results were developed which I was willing to accept as final, it became necessary to weigh each disc before and after the exposure, and thus learn the percentage of loss.
The figures relating to the last set of compounds are as follows :
This test lasted for 12 hours’ steady running under the conditions stated above.
Having at last decided upon the proper compound for the carrying-surface, I applied it to the belts, and I may say that every belt made since that time, which was in 1892, is in good order to-day. In many cases, too, the belts which they replaced had been completely destroyed in three months’ time under exactly similar conditions.
There are four principal methods of supporting conveying-belts.
First we will consider the oldest method, in which the belt lies flat upon a straight-faced, horizontal pulley, as shown in cross-section, Fig. 1. On account of the liability of the material to roll off the belt, this form is only suitable under certain conditions (e.g., in carrying grain). The belt cannot be heavily loaded, and the feed must be so regulated that an even amount may be delivered to the belt at all times. If the material is below ¼-inch in size, the speed may be as high as 300 feet per minute. In carrying larger stuff on flat belts the speed must be lower; but the most necessary thing is to keep the belt very tight, that the material may not be jarred off in passing over the idler pulleys. This, of course, increases the strain on the bearings, and from that fact, together with their low efficiency compared with systems to be described later, we may consider flat-running belts as out of date for most purposes.
The second method (Fig. 2) is somewhat like the first, but with the addition of skirt-boards at the sides to increase the capacity of the conveyer.
This method of rigging belt-conveyors is in great vogue among brick-makers and others who handle clay. It will be easily seen that the material must, collect between the skirt- boards and the belt, and that, as it hardens, it will cut a strip off each side. The common practice is to start with a wide belt, and move the skirt-boards in as fast as these strips are cut off. When the width is so reduced as to render the conveyer totally useless, wheelbarrows are called into play until a new belt can be procured, and the entire process recommenced. This method is so entirely bad, that I refrain from further description. It is only fair to say, however, that the skirt-boards
fill one useful purpose, as it is the practice of the men shoveling into the belt to rap their shovels against the boards in order to get rid of the sticky clay. A board for this purpose can be applied, however, to a much better form of conveyer, and in such a way that it cannot interfere with the belt. (See Fig. 5.)
The third method is a slight improvement upon the last, in that a trough is made by raising the sides of the belt instead of using boards as described above. The conical pulleys used for this purpose are shown in Fig. 8.
This method has an obvious fault, owing to its bad design. By reason of the difference between the two diameters, the outer edge of the pulley goes twice as fast as the inner edge. This causes a slip which soon wears out the under surface of the belt. For belts not wider than 14 inches this form is not bad, for, with small belts, the weight on the pulleys is light, and the effect of the slipping is consequently less severe.
The fourth, and best form of belt-support, is composed of three pulleys, one carrying the middle or bottom of the belt, and one on each side with its axis at an angle of about 45°. The shafts of all three pulleys are held in a pair of combination bearings which can be adjusted to different widths of belt. I never supply any other form of support for belts wider than 14 inches, and when I refer to troughed belts in this paper, it is to be understood that the sides are raised by means of these angle- pulleys, one common form of which is shown in Fig. 4.
There has been no mention hitherto of the means of supporting the empty part of the belt on its return. This is done by a single flat pulley of the kind shown in Fig. 1, or with a pair of smaller pulleys with an interval between them, as shown in the lower part of Fig 4.
It is sometimes possible to save money in constructing a long conveyer by combining the first and last methods of belt-support referred to. If the belt were run flat the whole distance, it would need to be so wide that the extra cost of the belt would be about equal to the money saved in using the cheaper flat form of pulley; but by placing a set of troughing pulleys between every fourth and fifth set of flat pulleys, or at such other interval as may be found advisable, the load is so centered on the belt at each of these points that it has no time to overflow before it is again centered between the next pair. The use of a very wide belt thus becomes unnecessary.
On some conveyers, it is often advisable to have at intervals a pair of idlers, running on a vertical axis, or inclined inward, so as to make a right angle with the edge of the belt. These will serve to keep the belt straight on the pulleys if there is any tendency to run toward one side (See Fig. 6); but they are not needed with a good belt and strong, true supports.
The large pulleys at the end of the belt should be slightly crowned on the face, and the pulleys should not be lees than 4 inches wider than the belt. The driving-pulley ought never to be less than 30 inches in diameter, and in the case of long wide belts 48 inches is advisable, as it allows the first return pulleys to be so placed as to give the belt a very large arc of contact on the driving pulley. (See Fig. 7.)
Whenever it is possible, it is better to have the driving-pulley at the delivering end of the belt; but if it must be at the receiving end, a triple set of pulleys connected by gears can be easily arranged, which renders slipping impossible with the longest and heaviest loads. This scheme was first used by Mr. S. H. Edwards, Superintendent of the Magnetic Iron- Ore Co., at Benson Mines, New York. (See Fig. 8.)
The proper distance between the sets of idler pulleys is an
important factor in the economical running of the belt, as will be referred to later. The troughing-pulleys should be from 4 to 6 feet apart, according to the weight of the load, and that for the return belt there should be pulleys placed under every alternate set of troughing-pulleys, which would make the lower pulleys from 8 to 12 feet apart.
To me, one of the most wonderful things in connection with this subject is the exceedingly small amount of power required to move enormous quantities of material. The power required, in one case, to run a conveyer, which carries 1000 tons per day a distance of 180 feet, and elevates it 40 feet while doing so, is all transmitted by a torn and frayed little 5-inch belt, which takes its power from a pulley on the shaft, and transmits it to a pulley alongside the head-pulley of the belt. The power is here divided, part of it going over a sprocket-chain to help drive a large dumping-apparatus. Yet the entire amount of power employed for both purposes does not exceed four horse-power.
It is impossible to give any rule for determining the exact number of horse-power required for conveying-belts running under different conditions, owing to the number of variable quantities which make up the load. One of the most important of the elements involved is based upon the distance between the sets of troughing-pulleys. If they are too far apart the belt sags down between, which materially increases the load. If, on the other hand, the idlers are too near together, the extra number of bearings makes another sort of resistance to be overcome. No general rule can therefore be made by which the required horse-power can be accurately determined.
It is a simple matter to determine the necessary belt-width and speed to perform certain duty when the weight per cubic foot of the material is known. If the belt is troughed it is safe to estimate that the load itself will cover one-half of the belt’s total width, and that the depth in the center will be one-quarter of its own width. The area in inches of a cross section of the load (which we may consider an inverted triangle) will when multiplied by 12, give the number of cubic inches of material borne by the belt on each running foot of its surface. Multiply this result by some estimated speed to get the quantity in cubic inches that the belt will deliver per minute, and then reduce this to the number of feet, yards, pounds or tons delivered per hour, or to other convenient terms. (See Fig. 9.)
For example: To find the number of tons of material weighing 100 pounds per cubic foot that can be delivered by a 24-inch belt running 250 feet per minute:
As the belt is 24 inches wide we may safely consider the load as being a triangle standing on its apex and having a base 12 inches wide and a height of 3 inches. Therefore, the area of its cross-section will be 18 inches, and there will be 18 x 12 = 216 cubic inches on each foot of the belt. As the speed is 250 feet per minute, there will be delivered from the end of the belt 250 times 216 cubic inches, or 54,000 cubic inches per minute. This is equal to 31¼ cubic feet per minute, or 1875 cubic feet per hour, weighing 187,500 pounds, or about 93 tons per hour.
To save some of the steps referred to above, the following formula may be used. If we let A = width of belt, then 3A²/8 =
number of cubic inches carried on each running foot of the belt. If a belt is run flat it will carry about one-third as much, or A²/8. It is well to remember that when the width of a belt is doubled it will carry four times as much material, and when it is tripled it will carry nine times as much.
The table on page 89 will be found of service in determining the capacity of conveyer-belts.
In regard to this table I wish to say that the results shown are based upon a continuous and even delivery of fine material to the belt. As this is often unattainable in practice it is well to prepare for uneven and large pieces and for irregular feed by allowing a margin in either belt-width or speed, the two factors which govern the capacity of the belt. The widths of belting in most common use are 22, 24 and 26 inches, and the average speed is about 300 feet per minute. I am inclined to favor higher speeds, especially for elevating at an angle, as it seems to require less power to lift a small load at a high speed than the same amount of stuff per hour in a larger load at a low speed. A good speed for level work is 450 feet per minute; at an angle 650 feet is not at all too fast; and I have seen belts working smoothly at 900 feet per minute and at an angle of 27 degrees. Such speed as this, however, is hard on both the belt and idlers.
Having decided upon the proper width of belting for the duty to be performed the next points to be settled are the proper thicknesses for the belt and for its protecting cover.
The following table shows the suitable number of plies for different widths of conveying-belts:
Belts 20 inches wide and less should be 4-ply
Belts 22 and 24 inches wide and less should be 8-ply
Belts 26 and 28 inches wide and less should be 6-ply
Belts 30 and 36 inches wide and less should be 8-ply
The thickness of the rubber cover should be based upon the character of the stuff to be carried. For hard material weighing over 50 pounds per cubic foot the cover should not be less than ¼ inch in thickness. With the patent reinforced cover referred to above, it is possible to have this thickness at the center where it is needed, allowing it to taper off to 1/16 inch or
1/8 inch at the sides where the work is lighter. This, of course, makes the cost lower than if the same thickness of cover extended the whole width of the belt. The belt with the reinforced cover referred to is shown in Fig. 10, A. There is now an improved form of this belt with stiffened edges, which make the belt bend properly at the center and preserve its troughed shape, while giving it such firmness at the edges that a mere
touch against the steering-idlers keeps it running true. This stiffening is done by running two or three plies of duck a part of the way in from the edges, giving all the advantages of a heavier belt but at a lower cost. This form will also be patented. (See Fig. 10, B.)
At the point where a belt receives its load it gets as much wear as in all the rest of its journey. A few points should be borne in mind in connection with this part of the conveyer. The material should not be allowed to drop vertically upon the belt but should instead be so guided by an in-
terposed chute as to strike the belt with as nearly as possible the same speed and, of course, in the same direction as that of the belt itself. This is much the same principle as that which causes a man who wishes to board a fast moving car to run along a few feet before jumping upon the step, except that in the former case it is the wear-and-tear upon the vehicle or belt which is avoided instead of injury to the passenger.
If ore or rock is carried, there is bound to be wear wherever it touches. It is well, therefore, if it has to fall any distance to let its force be broken by striking first against an accumulated
pile of itself and then roll off on to a chute, whence it may slide quietly upon the belt and not move until it reaches the end of its journey. See Fig. 11, which shows the device in use at the N. J. and Penn. Concentrating Works, Edison, New Jersey.
The chute should be made of cast-iron with sides, and should be so wide that the ore or other metal cannot get jammed, as it is very apt to do. The objection to a wooden chute is, that the broken stone or ore does not slide properly upon it, but runs down in a succession of jumps, that are as apt as not to carry it over the side of the chute or off the belt.
A device is shown in Fig. 12 for loading a belt under a crusher, from which falls both coarse and fine stuff. The line A represents a grizzly or screen of iron bars which allows nothing larger than 1 inch to go through. The small stuff slides down the chute, B, and forms a bed on the belt to protect it from the impact of the heavier pieces.
There are many ways of joining the ends of carrying-belts, the most common being by the use of metal belt hooks consisting of a set of teeth cast together with a metal back. These have to be destroyed if the belt needs taking up, and a better plan is shown herewith in Fig. 13. The thin steel plates are laid upon a strip of thin leather or canvas which covers the opening in the belt and thus prevent leakage. Staples are driven through the holes in the plate and clinched. In breaking the joint the staples are easily cut with a cold chisel but the plates themselves can be used an indefinite number of times.
The simplest method of lubricating the bearings is by means of compression grease cups which are dust proof and very economical. They are screwed into the ends of hollow shafts and a man without stopping can give the handles a turn as he walks along the belt, and this only has to be done once a day at most. Grease costing about four cents a pound is generally used.
Some of the purposes for which conveying-belts are used are the carrying of trap-rock and limestone in stone-crushing plants, charcoal and ashes in sugar-refineries, ore in concentrating-plants and mines, ore, fuel and flux in smelters, earth and stone in large excavations, blocks and logs of wood in pulp-mills, clay in brick-yards, moulding-sand in foundries, coal in breakers, yards, large power-plants and culm-piles, tobacco in process of manufacture, customers’ packages in large retail stores, grain in elevators and flour-mills, boxed goods in coffee-mills, phosphate-ore in the southern mines and chemical fertilizer in plants all over the country. These are only a part of their uses, but the list of other purposes for which, though not employed, they are equally suited, and must some day be applied, would be a very much longer one.
Belts generally cost less to install than any link-belt or other metal conveyer; and the cost of maintenance is so much less that there is simply no comparison between them. In addition to this, they run noiselessly, instead of making a perpetual and deafening racket, and no owner’s ears can become oblivious to a banging and crashing of which every vibration means wear and depreciation, as well as loss of power.
You may say, “If this belt method of conveying is all that this man claims, why hav’nt we heard more about it? Why isn’t it used more widely ? ” My answer is this: The various systems of sprocket-chain, metal-pan, trough- and screw-conveyers and the over-head cable-systems have all been owned by manufacturing concerns who make them known by advertising, undertake their construction and installation, and guarantee them. As to conveying-belts, no fundamental patent on the principle could be secured; and because a belt-conveyer is composed of two parts which are about equal in value and the products of entirely separate kinds of manufacture (I refer to, first, the iron pulleys and other supporting parts and second to the belt itself), no iron man felt like pushing the sale of a conveyer when he knew that some rubber manufacturer would share equally in the profits, and the rubber man would doubtless have felt the same if, with his less extensive knowledge of machinery, the thought ever occurred to him at all. And so, between them, the belt-conveyer has been neglected except where its merit compelled the recognition of a few wide-awake and self-reliant engineers. It has been the property of no one. Nobody’s living depended upon its exploitation. It was to the interest of no one to stand sponsor for it; to develop, push it and perfect it. There are no data published about it, and each man who uses it to-day is practically the inventor of his own apparatus, which he has brought to its present state only after an expensive and vexatious experience. If an engineer to-day has a conveying-problem to solve and the thought of a belt occurs to him, immediately after come the questions: What kind of a belt ? What width ? How should it be run ? On what ? At what speed ? Where can I find out ? Being unable to answer any of these questions, and not caring to try experiments, his natural inclination is to state his needs to the well-known manufacturers of conveying apparatus and make a contract with one of them, thereby shifting the responsibility as soon as possible. The load of responsibility is apparently charged for along with the apparatus, but even the high price of the latter contains no suggestion of the great and continual expense incurred in running and keeping it in order.
I do not wish to appear as condemning universally the use of all metal conveyers, for there are indeed some conditions for which they are better suited than are belt-conveyers. I may mention, for instance, places where the point of delivery must be constantly and quickly changed. With iron conveyers this is accomplished by the removal of a section of the iron trough, while a belt requires a movable frame-work containing two pulleys. This dumping-apparatus can be moved to any point in the belt’s length, but it is neither as cheap in construction nor as quick in operation as the plan adopted with metal conveyers.
Nor do I condemn the great ingenuity which, has made possible even the poor performance, by metal conveyers, of duties for which by their very nature they are unfitted. That is business. I only want to show that there are many places where other conveyers are now used for which belts could be substituted with economy.
The other day a man pointed to what he called a “ real conveyer,” which was dragging and scraping its load along (and apparently protesting against its own design and unfitness for the task), and observed: “ Oh, this does the work cheap enough.” It may be cheap, compared with manual labor; but it seems to me that with the competition of the present day nothing is cheap enough if there is anything cheaper. The object of these notes and sketches is to facilitate the use of belt-conveyors. I have gone into details, in order that any one who wishes to do so may construct a conveyer suitable for his needs.