Table of Contents
The use of a good Cement clinker grinding aid can be vital in today’s increasing material demands. Along with the obligation to process increasingly larger quantities of ores containing finely disseminated minerals, our limited energy resources and the rising costs of energy present a challenge to the process engineer. One research route that has been explored for about half a century is the development of additives to the grinding mill feed that substantially improve the efficiency of grinding. Such additives are termed grinding aids.
This section summarises and evaluates the results of this effort as well as its implications and points out areas where understanding is lacking and further research is needed.
Some of the distinctive features of the reported results on grinding aids and their proposed mechanism of action must be pointed out in order that the rest of this section be understood in the proper perspective. First, many of the reported results contradict each other. In many cases, the results must be evaluated with caution because of relatively inadequate controls on system variables during . experimentation. Incomplete system characterisation often makes it very difficult to draw any general conclusions (particularly about the mechanism of the action of grinding aids). Improvement of grinding efficiency by grinding aids appears to be well established, at least on a laboratory scale; the spectrum of hypotheses on their mechanism of action, on the other hand, is rather bewildering. The potential significance of grinding aids in reducing energy consumption in the grinding process is illustrated by the examples in Tables 4-15 and 4-16.
The unit operation of comminution, which is used extensively in a variety of industries, such as mineral processing, cement, ceramics, chemicals, pharmaceuticals, etc., has long been recognized to be energy-inefficient. Since large tonnages of materials are processed in many of these industries, the high specific energy involved in comminution acquires an even greater significance. In the mineral processing industry alone, the figures are very large. The annual energy consumption at ore concentrating plants in the United States currently exceeds 25 billion kWh, about half of which is attributable to the grinding step, in which it is known that only 1% or less of the energy input goes to the production of new surface area.
Considerably more effort has been expended in developing grinding aids for dry grinding systems than for wet grinding systems. Most of this work is oriented toward the cement industry, where huge amounts of cement clinker are dry ground in ball mills. Cement clinker is particularly difficult to grind, and the fine grinding of this material is one of the chief problems of the cement industry.
How Grinding Aids Affects Dry Grinding
The first commercial use of grinding aids in the cement industry came about 40 years ago. These grinding aids are usually organic liquids, added in amounts usually not exceeding 0.25Z by weight. They are used to increase the product fineness at a given production rate or to increase the production rate at a given product sire. In either case, the benefits of any grinding aid must outweigh its cost; furthermore, the grinding aid should have no detrimental effect on downstream processing or the finished product. Given these constraints, the firm industrial acceptance of grinding aids in the cement industry that followed over 10 to 15 years must be considered relatively rapid (Blanks and Kennedy, 1955).
Effect of Grinding Aids on Wet Grinding
A variety of additives have been shown to have grinding aid characteristics for grinding cement clinker. Typical among these are amines, organosilicones, glycols, resins, cod oil, kojic acid, carbon blacks, wool grease, calcium sulfate, urea, asphaltenes, etc.
Figure 4-26 shows a typical comparison between the grinding of cement clinker with and without a grinding aid. Grachyan and Tavlinova (1973) report that 0.1% of dior tri-ethanolamine increases the rate of clinker grinding by 22-29X, with glycerol and lower alcohols being less effective. A 25-50% increase in the production rate has been reported with glycol as the grinding aid (Schneider, 1969). The use of 0.05% propylene glycol in pilot plant grinding tests showed chat a 10% increase in production accompanied by a 10% decrease in energy costs is possible (Popovic, 1971). The addition of as little as 0.01-0.05% of organosilicones has been found to decrease grinding time by 70Z (Melnik, 1969).
The effect of grinding aids on the grinding of materials other than cement clinker has also been reported. These include, among other instances, the use of wool grease in the grinding of gypsum, limestone, and quartz (Hobday, 1946; Voznyuk, 1969)*, the effect of hydrocarbons on the milling of aluminum powder (Tripathi and Cruszek, 1973)*, the addition of silicone fluid in the grinding of corundum alumina briquets (Kukolev, 1973)1 the use of silicones in the ball mill grinding of quartz (Gilbert, 1962); and the use of acetone, carbon tetrachloride, benzene, and nitromethane in the vibratory mill grinding of glass, marble, and quartz (Zegler 1968). In addition, there are many reports in the Russian literature on the beneficial effects of various surfactants of unspecified chemical compositions on the grinding of a variety of materials (Kukolev, 1972; Dzyuba, 1976; Melnik, 1972; Tyagorr, 1971). It is quite clear therefore, that the efficacy of a broad spectrum of chemical additives in improving the efficiency of dry grinding is well demonstrated in the literature.
The results presented thus far indicate the applied nature of the research on grinding aids for dry systems. In other words, these results indicate the potential of a certain additive as a grinding aid for a specific material. However, even though additives have found successful commercial uses, as in the cement industry, the rational development and application of grinding aids requires a clear understanding of their mode of action.
Effect of Grinding Aids on Cement Clinker Grinding
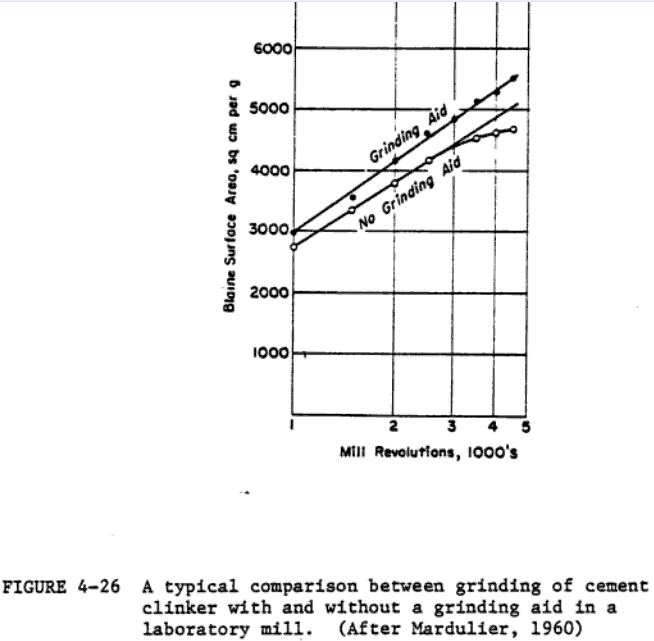
Relative to the effort put into the testing of additives, much less has been expended towards understanding the mechanism of action grinding aids in dry systems. Since comminution involves production of new surface, the energy required to produce a given amount of surface can be reduced by decreasing the solid surface energy. This mechanism was believed intuitively to be responsible for the improved efficiency resulting from additives in rock drilling, according to Rehbinder and Kalinkovaskaya (1932). Rose and Sullivan (1958) extended this theory of adsorption-induced decrease in surface energy to explain the mechanism of grinding aids in tumbling mills.
On the other hand, Westwood and Goldheim (1970) showed that adsorption of surfactants can reduce the strength of materials only when plastic deformation is important in fracture. Since grinding in tumbling mills is typified by brittle fracture, Rehbinder’s effect can hardly be responsible for the action of grinding aids in these systems. Furthermore, even with plastically deformable materials, the duration of stress, which roust be sufficiently long for adsorbed layers to influence material strength, is too short in a grinding mill, where impact fracture is dominant. Also, the crack propagation velocities in impact breakage in grinding mills are much greater than the spreading velocity (by diffusion into the cracks) of the surfactant molecules (Locher and Seeback, 1972; Somasundaran and Lin, 1972; Craichen and Muhler, 1975; Ocepek and Eberl, 1976). As indicated by the work of Locher and Von Seeback (1972), even vapors of the (liquid) grinding aid adsorbed on the solid surface cannot improve breakage efficiency by decreasing the surface energy of the solid. It is, therefore, very doubtful that adsorption-induced changes in surface energy can be responsible for the action of grinding aids.
According to Westwood (1966, 1968, 1972) and Westwood and Coldheim (1970), the adsorption of molecules of the grinding aid on the solid surface essentially blocks the motion of dislocations near the surface, rendering their motion under stress gradients very difficult. Material plasticity, which is due to dislocation movement, is thus greatly reduced and the solid is rendered brittle. This, these authors claim, is the mechanism of action of surfactants used in drilling. This mechanism applied to tumbling mill grinding is subject to criticism similar to that in the foregoing discussion on Rehbinder’s effect. Firstly, Westwood’s mechanism has been demonstrated only where plastic flow is important, which is certainly not the case in tumbling mill grinding. Also, the rate of dislocation movement is much lower than crack propagation rates in impact fracture. In fact, it has been demonstrated experimentally that, with single particles, grinding aids have no significant influence on particle fracture by impact (Graichen and Muhler, 1975). Locher and von Seebach (1972) have also given experimental evidence that Westwood’s mechanism is probably inoperative. They also conducted abrasion tests, with electron microscopic investigations of the abraded particles. The results indicated that abrasion and reagglomeration were taking place simultaneously. They found high abrasion rates in organic vapors, which they attribute to the prevention of reagglomeration of the abraded particle because of the adsorption of these vapors on the particles. These results are significant since abrasion is partly responsible for comminution in tumbling mills.
It has been suggested that molecules of the grinding aid might penetrate deep into the tips of preexisting cracks and exert pressure on the crack tips, aiding the fracture process (Lichtman et al.,1958). It is also very doubtful that this mechanism plays a role in impact fracture. Furthermore, as pointed out by Somasundaran and Lin (1972), the mechanism does not explain the effect of long-chain organic surfactants, which would have limited diffusion owing to their large size.
In view of the inability of theories based on adsorption-induced improvement of the breakage subprocess to explain the action of grinding aids, it has been postulated by many researchers that their effect is on the agglomeration and flow characteristic of material in the mill. The idea that grinding aids caused dry dispersion of material was suggested nearly 40 years ago when a considerable increase in dust was noticed in the early commercial uses of grinding aids in cement grinding (Kennedy and Mark, 1938). Observations like these over a period of time suggested that grinding aids coat the cement particles, shielding them from agglomeration forces and preventing the welding of particles back together.
It has been argued that grinding aids readily satisfy the valence forces produced by material fracture (Ocepek and Eberl, 1976; Mardulier, 1961; Ghiki and Rabottino, 1967; Beke and Opoczky, 1967). Since grinding aids usually are polar substances, they are preferentially adsorbed on specific sites where breakage of electrovalent or covalent bonds results in residual electrical forces. By the same token, at least part of the improved efficiency in wet grinding over dry grinding may be attributed to the polar nature of water. Experience has shown that polar grinding aids are more effective than nonpolar aids (Mardulier, 1961). In some cases, the adsorption of grinding aids on the particles might create similarly charged particles, and, therefore, the electrostatic repulsion between the particles could be responsible for their dispersion.
There is considerable evidence and concurrence of opinion on the prevention-of-agglomeration mechanism of grinding aid action in dry systems (Locher and Von Seeback, 1972; Graichen and Muhler, 1975; Ocepek and Eberl, 1976; Mardulier, 1961; Ghigi and Rabottino, 1967; Beke and Opoczky, 1967; Scheibe et al., 1974; Opoczky, 1975). It is believed, therefore, that grinding aids that chemisorb on solid particles would most effectively reduce adhesive tendencies between particles and thereby improve grinding efficiency. Since the adhesive forces are surface-area dependent, the relative improvement in grinding efficiency is greater, the finer the product size (Locher and Von Seeback, 1972; Graichen and Muhler, 1975). Thus, the economic application of grinding aids implies their injection into the mill wherever adhesive forces are obstructive, so that they may be used advantageously even for relatively coarser grinds if the influence of adhesive forces can be confirmed in this case (Locher and Von Seebach, 19 72).
At very fine grinds, the tendency of ground particles to coat the grinding media and mill liner becomes very pronounced and has long been considered to limit the effectiveness of the grinding process. There has been some diversity in opinion as to whether grinding aids are effective only in reducing ball and liner coating, but, as Mardulier (1961) points out, this can be considered a special and extreme case of agglomeration. Since media and liner coating occurs only with very fine grinding, it is possible that in certain situations the use of grinding aids is justified only when coating is present initially.