Optimising Ball Mill Liners to Maximise Tonnage
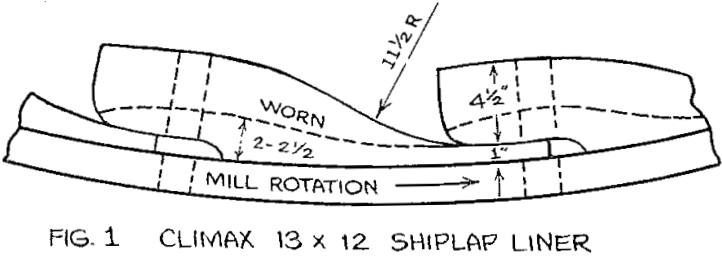
Mill liner design is an important factor in grinding. Testing and selection of the optimum liner profile for a given set of mill operating conditions can improve mill capacity, liner life, and liner wear rate. In testing four mill liner profiles for 13′ x 12′ overflow ball mills. Climax found that an improved design increased […]
How to Grind Finer
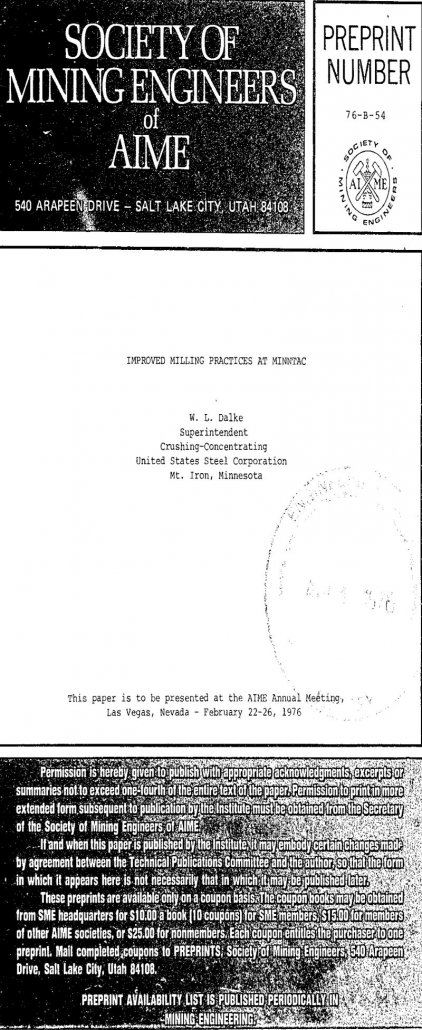
The minntac complex is a facility for production of iron ore pellets located on the mesabi range at mountain iron, minnesota. It consists basically of a mine, crushing plant, concentrator, and a pelletizer producing twelve and one-half million tons of pellets annually. This paper deals with some of the aspects of the grinding circuits; but […]
Waagner-Biro ASL Liner System
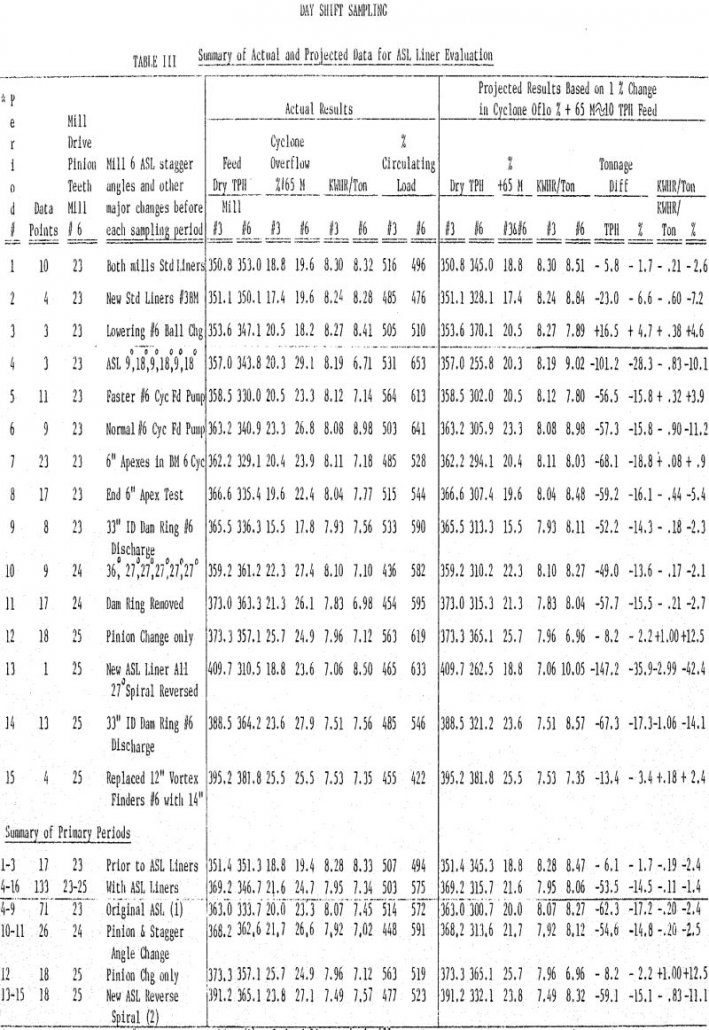
A unique type of grinding mill liner has been developed by Waagner-Biro A.G. of Austria. This liner system, termed an angular spiral lining (ASL), was successfully tested by Magma Copper Company’s San Manuel concentrator in both their 10 Ft x 10 Ft (3.05m x 3.05m) and 12 Ft, 6 In x 14 Ft (3.31m x […]
Gearless Warp Around SAG Mill
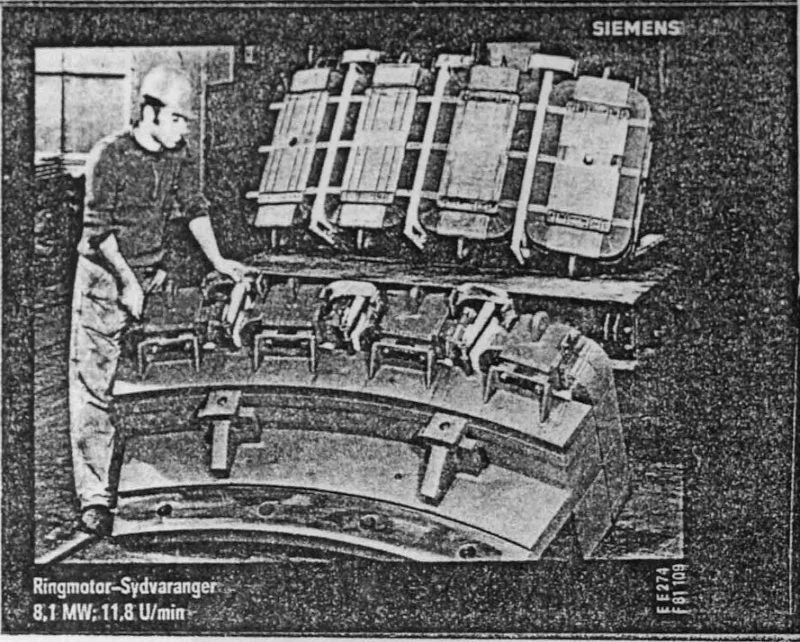
For almost a decade now, very good operating experiences have been gained with a total of 28 gearless ring motor drives in the cement industry, driving tube mills with diameters of 2.5 to 4 meters with drive powers ranging from 3000 to about 5000kW. Why then did the mineral ore processing industry hesitate till 1980 […]
Testing Failure Criteria for Grinding Mill Structures
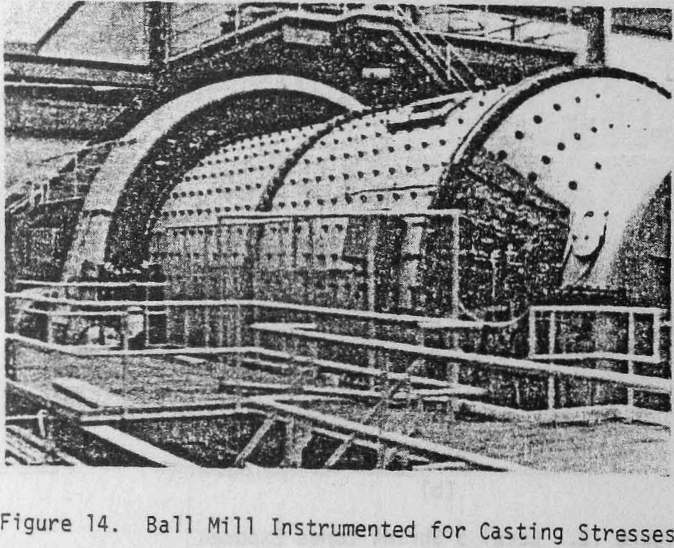
The trend of the past five years toward larger mill sizes shows no signs of reversal. Indeed, the current view of capital requirements for projects, coupled with decreasing ore grades, indicates at least a constant if not accelerating demand for the use of the larger mill, rather than several smaller ones for a given size […]
Mineral Processing Circuit Simulator
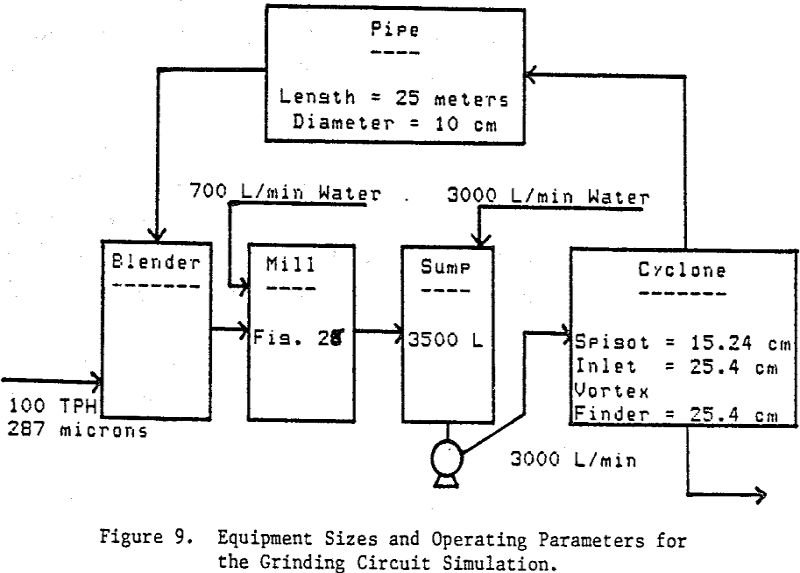
The fundamental design philosophy was based on meeting three criteria: flexibility, modifiability and usability. Flexibility refers to the ease of using the simulator to study a variety of flowsheets. A stream and unit operation numbering scheme was developed as a means of meeting this requirement. This scheme, in conjunction with modularized unit operation programs, made […]
Grinding Mills for Remote Mining Sites
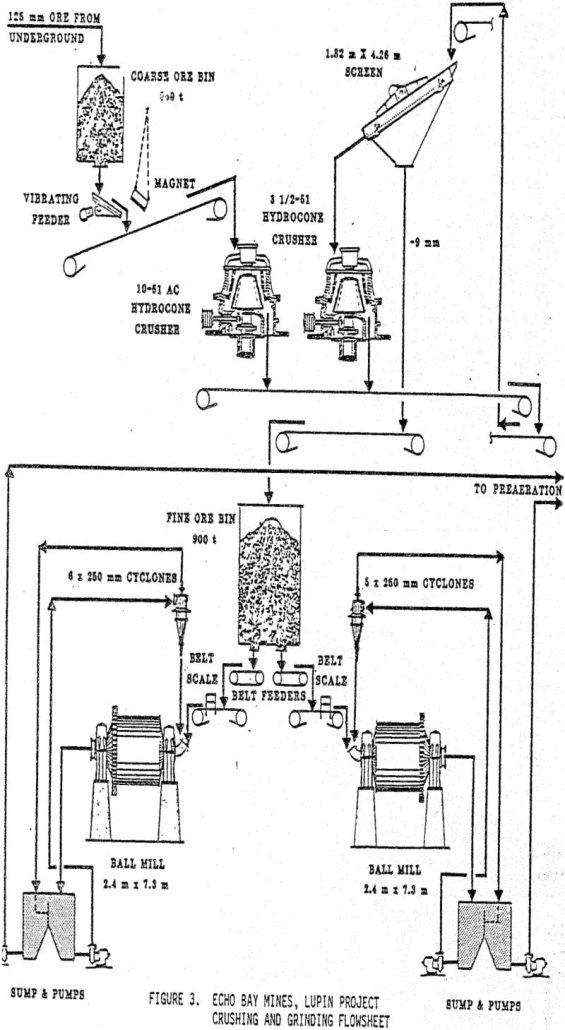
A number of challenges are faced when a mine is established at a remote site in northern Canada. The distance from suppliers, accessibility to the site, constraints on transportation of men and materials, and mining frozen ore are considerations which influence design. Mine Sites The Polaris Project of Cominco Limited of Vancouver is located on […]
How to Reduce Risk in Mineral Processing Plant Design
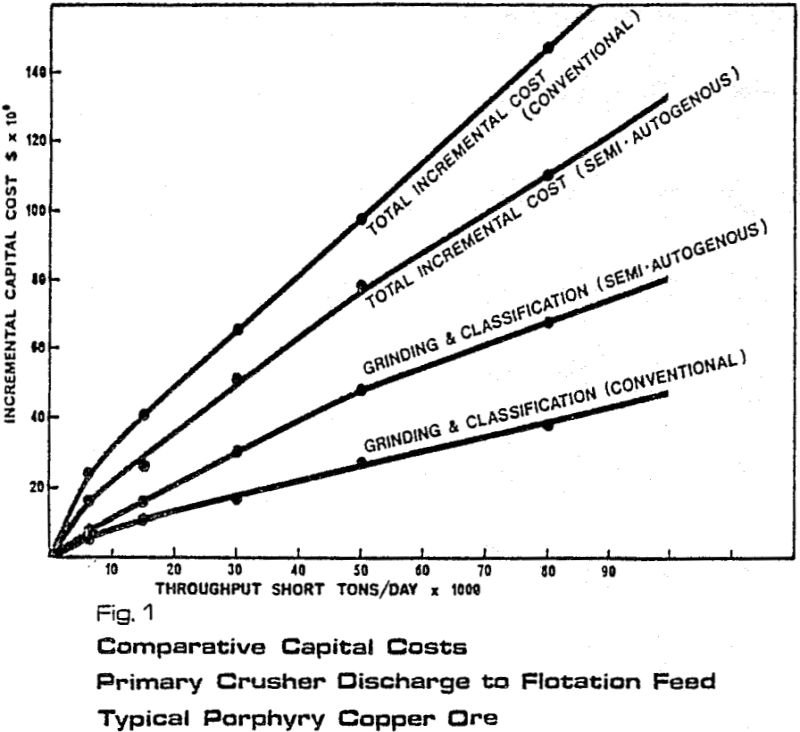
Assuming that ore grade is on target, the milling rate is the most significant parameter, next to mineral recovery, which is watched closely by senior executives and financial managers. It governs the sales of the mining company in terms of pounds or ounces of metal sold. If recovery is not impaired by increasing throughput, then […]
Grinding Mill Cost
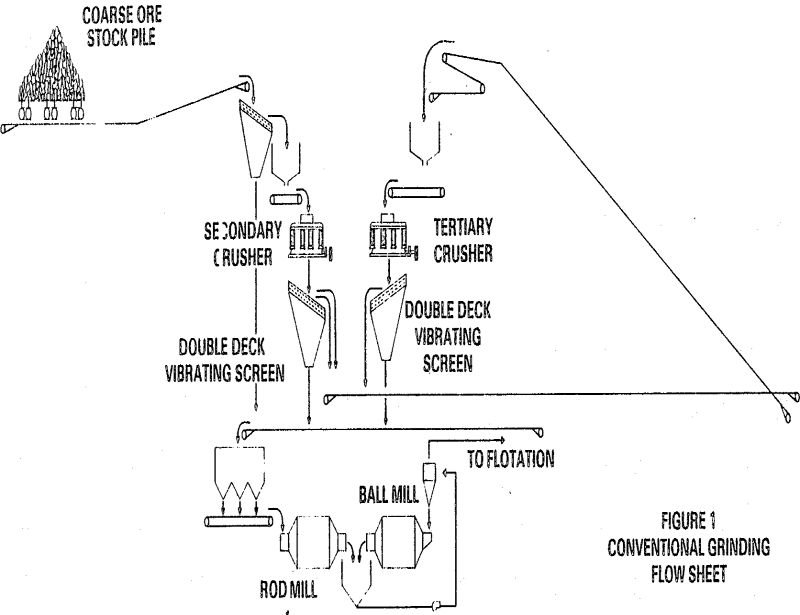
A comminution circuit is an important integral part of a mineral processing plant. Nearly 40% of the capital cost and 30 to 40% of the operating cost are taken up by the crushing and grinding circuit. Therefore, considerable care should be given to the design and selection of this circuit. Autogenous, semi-autogenous, and conventional grinding […]
Commissioning Variable Speed SAG Mill Gearless Drive
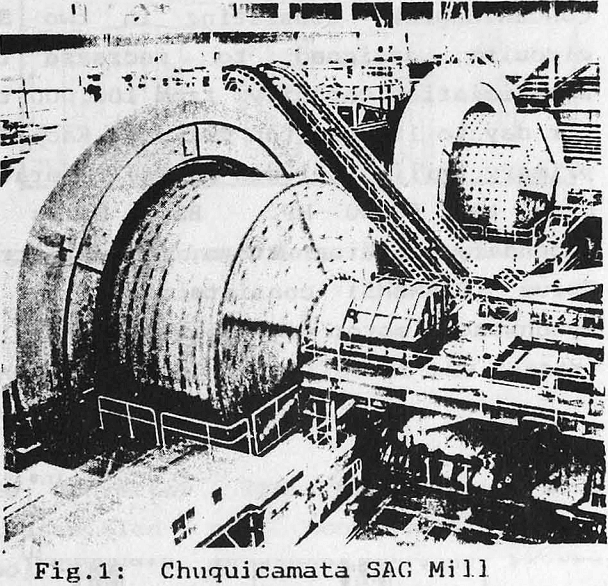
The electric operation and design features of the 11,000 H.P. variable speed SAG mill gearless drive is presented. The function of the frequency-converter, control system drive and lubrication systems are described. An analysis of the harmonic characteristic in the Supply System and Motor is presented, and the dynamic development of the stator current, speed and […]