Improving Crushing & Grinding Rates and Recovery Efficiency
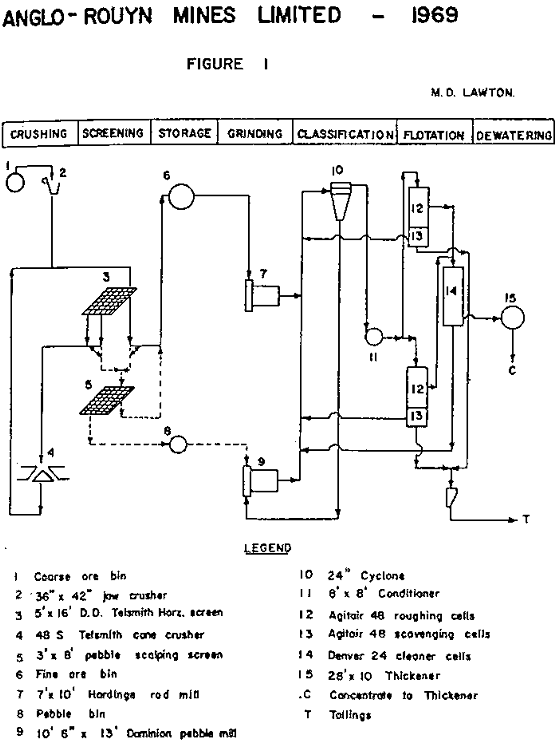
The crushing section was designed to supply approximately 100 tons per hour of -5/8 in. material to the Fine Ore Bin. Early milling results indicated that the ore was somewhat harder than expected and the 7 ft. x 10 ft. Hardinge Rod Mill was proving to be a bottleneck. The comparatively wet ore, sizing up […]
Grinding Circuits Simulation of Closed-Circuit Grinding
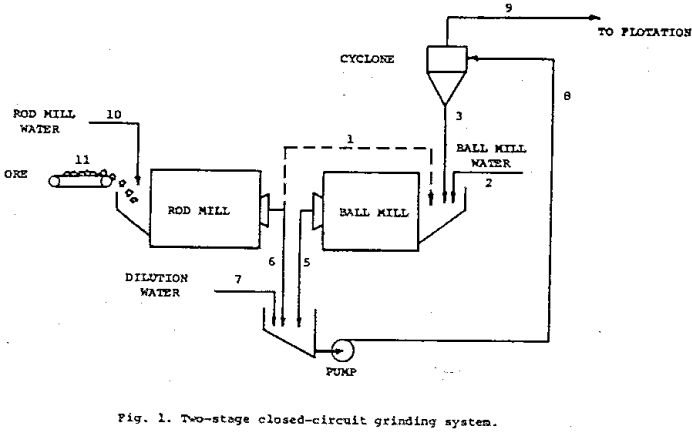
The data acquisition and modeling efforts are described first, followed by discussion of some of the simulation results. Observations pertinent to steady-state operation are presented followed by a description of the application of a dynamic model of the grinding circuit for synthesis and evaluation of grinding-circuit control. Data Acquisition and Reduction Eleven streams are identified. […]
Grinding and Classification Control
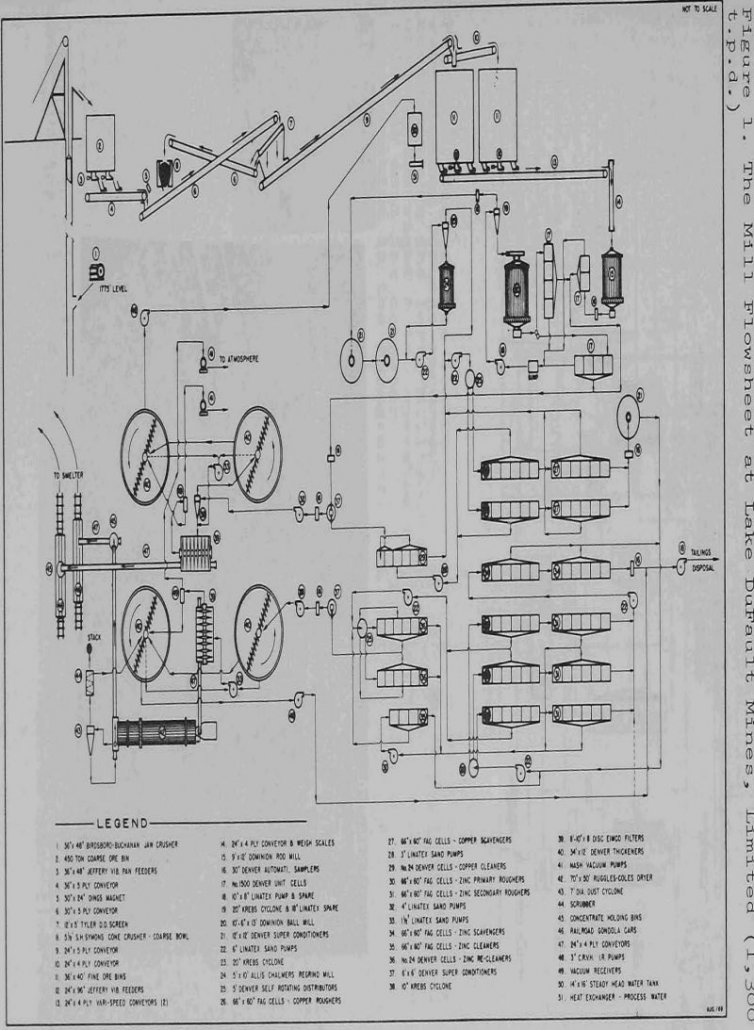
The ore milled from start-up until January, 1968, was mainly massive sulphides, consisting of a complex mixture of iron, copper, zinc and minor amounts of lead sulphides with important associated values in gold, silver and cadmium (average specific gravity 3.8). Description of the Grinding-Classification CircuitĀ The crushing plant product (presently -14 mm) is stored in […]
Fine Dry Grinding of Iron Ore for Pelletizing
Screening during the production of high-grade lump ore for blast furnace burden, particularly from recently developed ore deposits in Australia, South America, and Africa, has resulted in large tonnages of fine iron ore. Certain owners have decided to stockpile these fines until some later date; however, others have either sold these fines “as is” for […]
Iron Ore Crushing & Grinding Controls
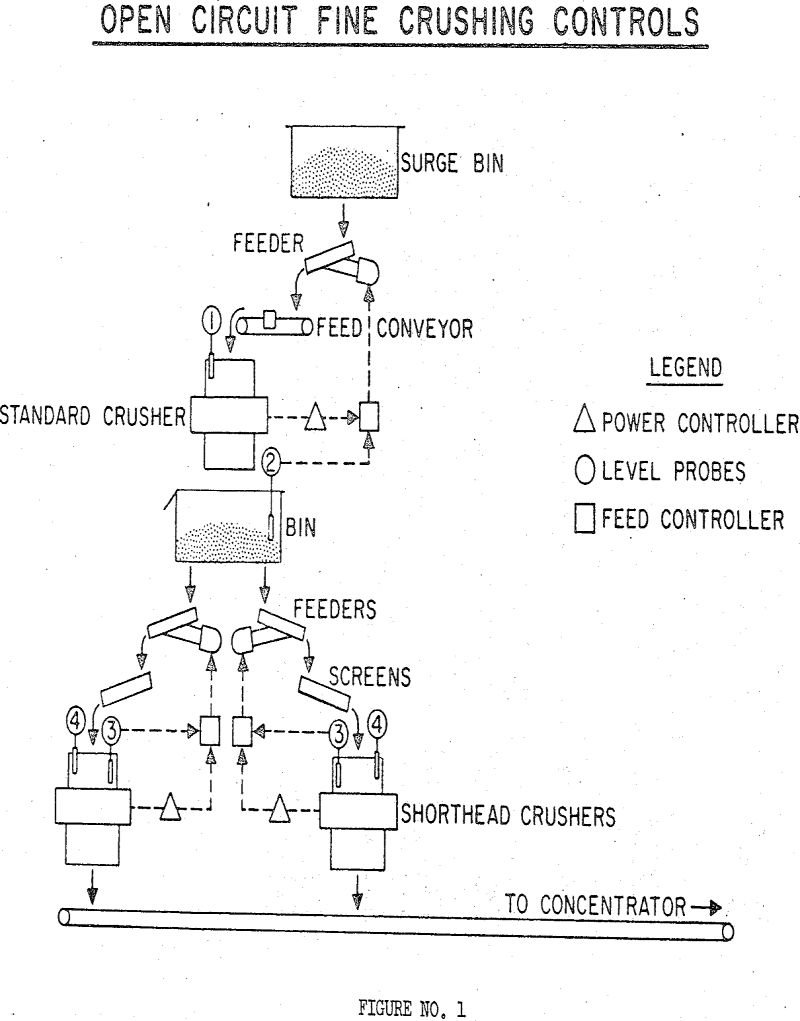
The Iron Ore Industry has perhaps seen more varied and drastic changes in its approach to crushing and grinding in the last 5 years than any of the other mineral industries. Multimillion ton per year plants have become common place. Centralized control and computers have become an established benefit. Autogenous grinding along with a variety […]
Grinding Circuit Control – South Africa
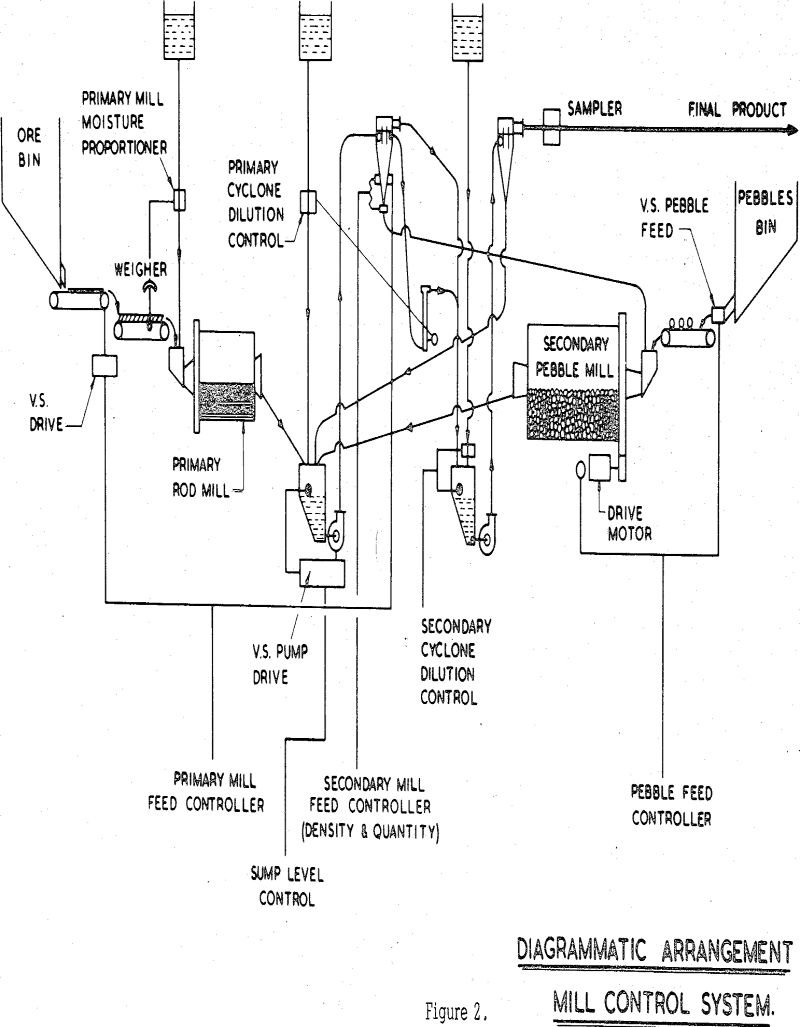
In a minerals-recovery context, the object of exercising control over milling operations must be threefold. To achieve maximum recovery at minimum operating costs and making maximum use of installed equipment. Milling is one of a sequence of operations which have as their objective the economic recovery of minerals from mined ores. All operations in the […]
Using a Crusher to Control Autogenous Grinding Circuit
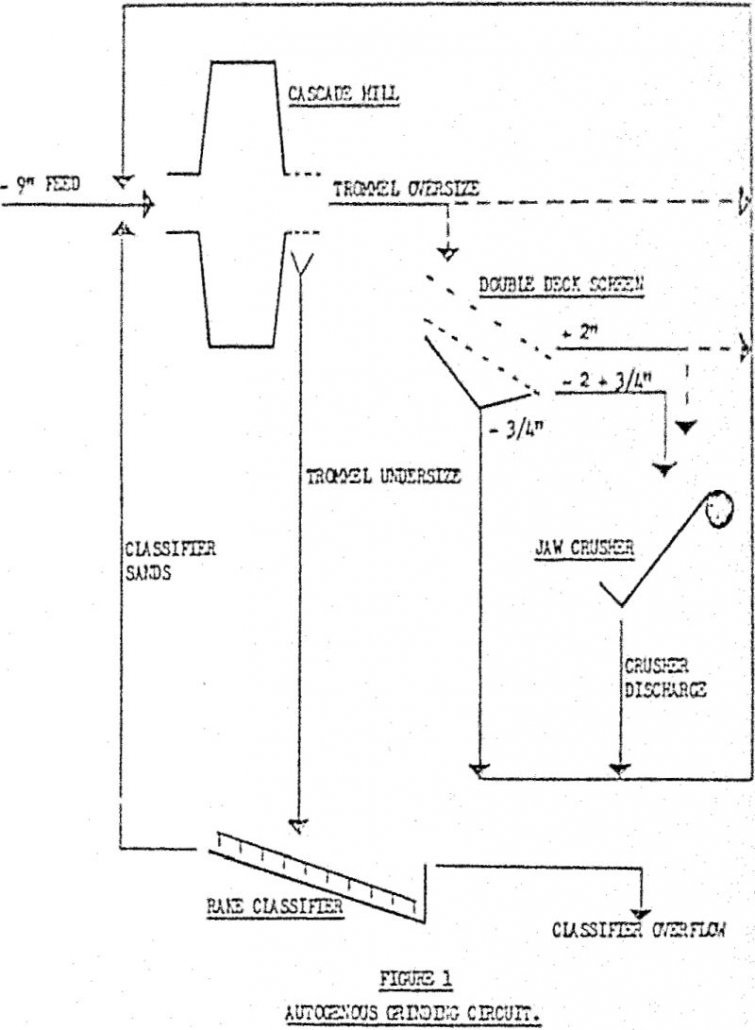
In an autogenous grinding circuit in which feed at approximately nine inches top size is reduced to a size suitable for subsequent processing, the build-up of a “critical size” fraction in the media causes problems. A “critical size” fraction has been defined as, “media too small to effect reduction by impact grinding of ore coarser […]
Feed-Forward Control for Grinding Circuits

Feed-forward control ( i.e. the forward flow of information in a control system ) is a simple and flexible approach to over-all control of a ball mill-rake classifier grinding circuit. The system described here uses mill power, feed rate, mill dilution water flow rate, and classifier dilution water flow rate only, to control mill load, […]
Population Balance Models for Predicting Grinding Mill Performance
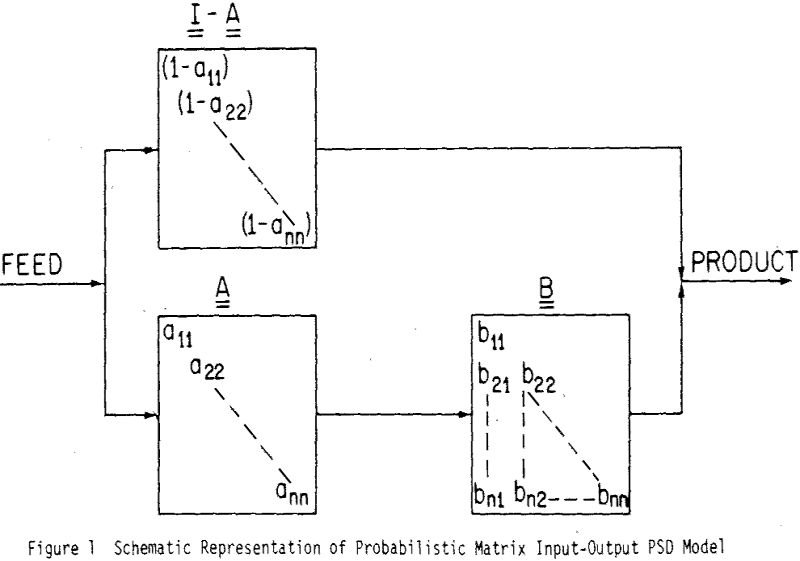
Comminution represents one of the major costs.of mineral recovery from low- grade ores. Efficient mineral recovery in a typical low-grade ore grinding-flotation process depends on grinding the ore small enough to liberate mineralization without producing excessive slimes, which would result in higher power and flotation reagent costs. Size criteria for efficient grinding should be stated […]
Aerofall Grinding System
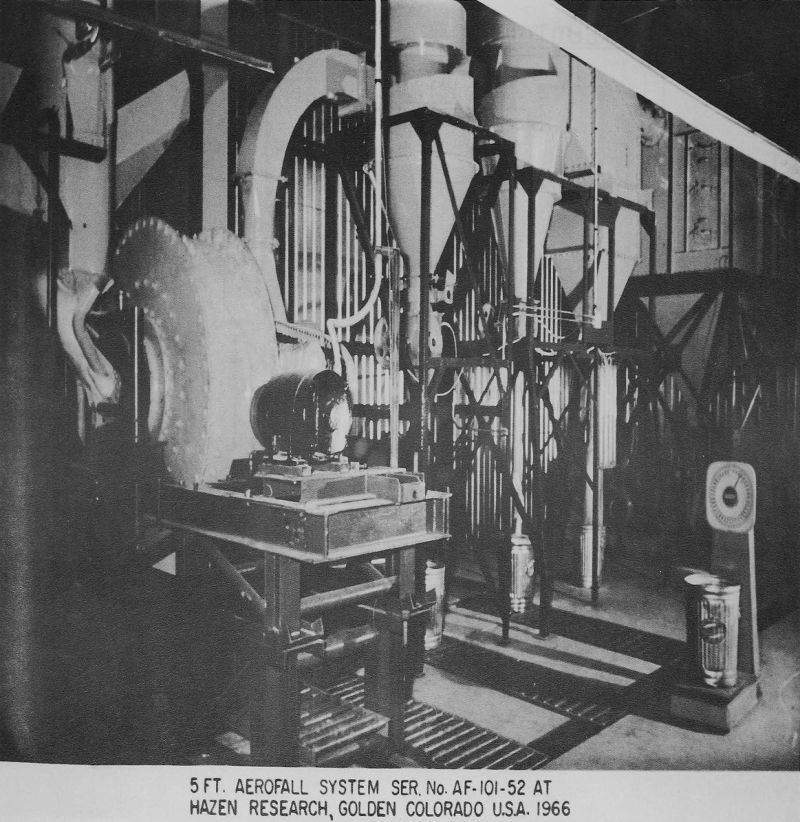
In any treatment process that requires a coarse feed material to be reduced to a fine size by crushing and/or grinding it must be determined whether a wet or dry comminution system should be utilized. All factors must be evaluated in reaching the decision. Among these factors are: Ecology and Plant Environment Operating Costs The […]