Ball & Rod Mill Density – How Water Impacts Grinding
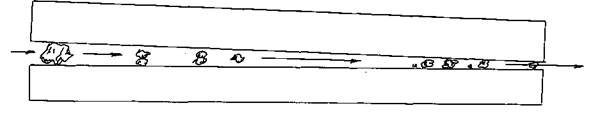
Density, if you recall is the ratio of ore to water and is measured as a percent of solids in the water. It will control the grind in two ways. It affects retention time and helps distribute the ore through-the mill so each piece of rock will come in contact with the surface of the […]
Grind Calibration Curve -Laboratory Test
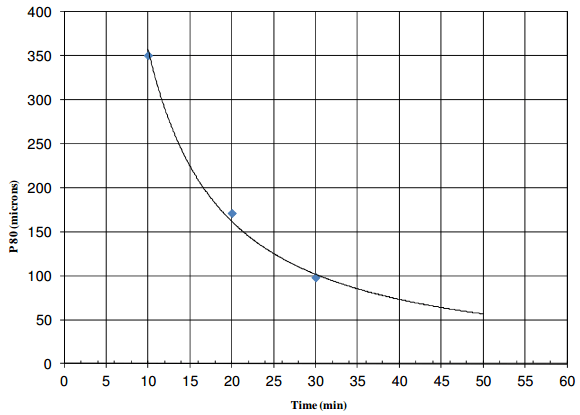
Before doing multiple laboratory flotation bench tests in which you need P80 grind controlled or predicted, you need to build a Grind Calibration curve following this short procedure. You will consistently add sufficient water to the mill to achieve a pulp density of 67% solids (Example: 1 kg solids + 0.5 kg water or 2 kg […]
Molybdenum Grind Size & Liberation VS Collector Dosage for Recovery by Flotation
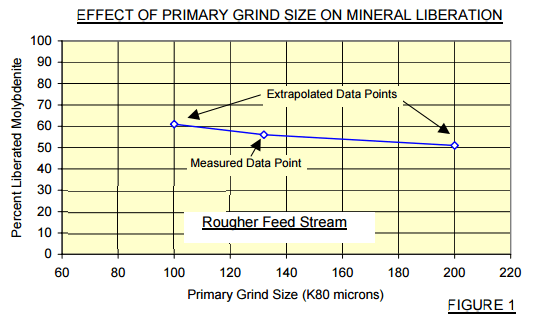
In an effort to evaluate the metallurgical results of an operating plant, 3 process stream samples (red points) provided were subjected to detailed modal analysis using protocols established for mineralogically similar ores. This method of analysis provides quantitative estimates of the mineral composition and of the mineral fragmentation characteristics. This data can then be used to […]
Ore Feed Size * Work Index Hardness: Crushing & Mill Tonnage

The single most common reason for an increase or drop in the production of fines is the WORK INDEX of the ore. If you remember, the work index of the ore is a method of measuring the degree of hardness. As the ore becomes harder the fracture lines in the rock become cleaner or sharper […]
Feeder Control -Ore Feed Size and Mill Tonnage
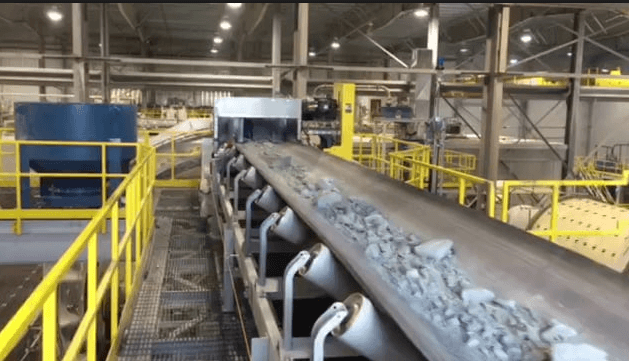
One area of major importance for the identification of impending problems are the feed belts. By visually estimating the PHYSICAL CHARACTERISTICS of the ore it is possible to have advance warning of change in many of the variables. Feed size is the most apparent, if the crush is supposed to be minus 3/8 of an […]
Operating a Grinding Circuit -How to Operate
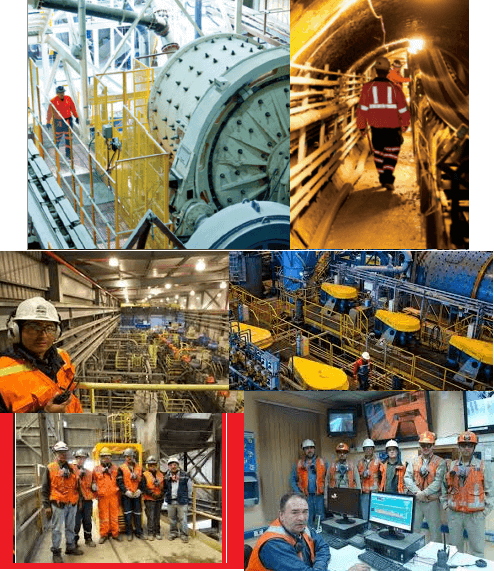
What I would like to do now is expand upon the grinding theory involved. Bring all of the earlier information together and show you how it relates to the operation of a mill and make you capable of Operating a Grinding Circuit correctly. Then I will explain the differences between Rod mills, Ball mills, SAG […]
Effect of Water & Density on Grinding Mill

The Time that the ore spends in the grinding mill is called, RETENTION TIME. This is a very important variable, the longer the retention time, the more the ore comes in contact with the rods, the better and finer the grind becomes. To understand this important control it must be remembered that any volume that […]
Grinding Mill Gear Assembly
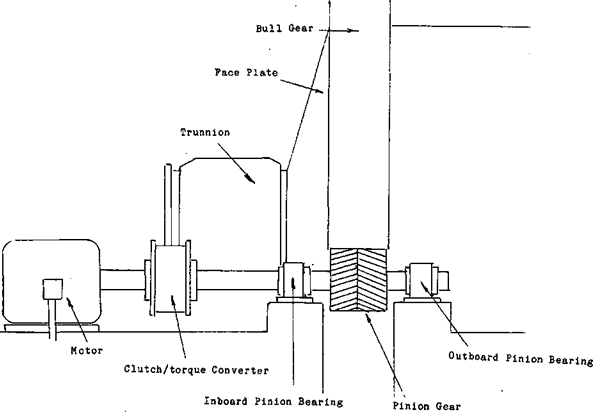
We will begin with the mill’s bull gear assembly and work towards the motor, The BULL GEAR, sometimes called the RING GEAR is designed to turn the mill transforming the energy of the motor into motion for the mill. By mill we refer to Ball Mills, Rod Mills and SAG Mills. Anything gear and pinion […]
Trunnion Bearing Assembly Ball Mill & Rod Mill
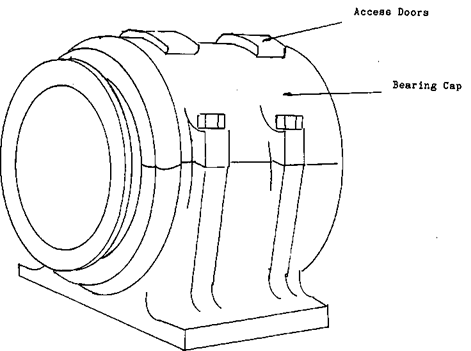
The first part of the mill that we will look at is the TRUNNION BEARING. This is a HYDROSTATIC BEARING which is a slow moving bearing that carries a heavy load. Usually it is constructed from Babbitt’s metal. If you happen to remember the introduction to this course Issac Babbitt was the man who devised the […]
Grind to Liberate Mineral Grains
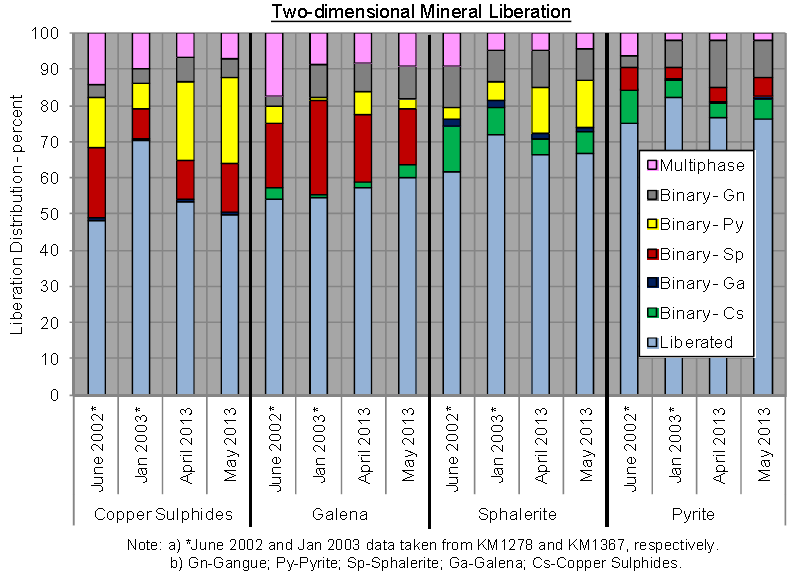
The next piece of information that is of value to the operator is to know the hardness of the ore. The WORK INDEX, as the hardness is referred to, is calculated on the amount of electrical energy that is required to grind the ore to a predetermined size. Said in another way, it is the […]