Rod Mills: Efficient Grinding Solutions for Mining
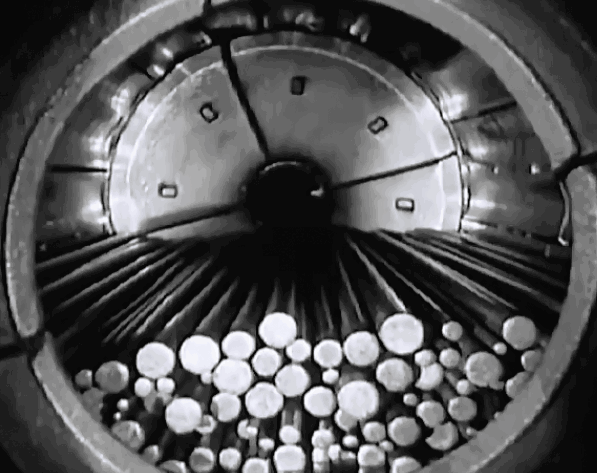
The Steel Head Rod Mill (sometimes call a bar mill) gives the ore dressing engineer a very wide choice in grinding design. He can easily secure a standard Steel Head Rod Mill suited to his particular problem. The successful operation of any grinding unit is largely dependent on the method of removing the ground pulp. The Steel […]
Acid Resistant Pot Mill

The Acid Resisting Pot Mill is recommended for grinding substances which contain acids such as sulphuric and hydrochloric or other highly corrosive mixtures or materials. This pot mill has a strong welded steel frame with a tilting device which locks the mill so that it can be rotated at the desired angle. This feature is […]
Tube Mill Capacity

The Tube Mill is widely used for the fine grinding of various materials in many industrial plants, as well as in ore milling where it is necessary to reduce the particles to 150 or 200 mesh. Even finer grinds can be obtained when operation is in closed circuit with a suitable classifier. This unit is […]
Laboratory Rod Mill
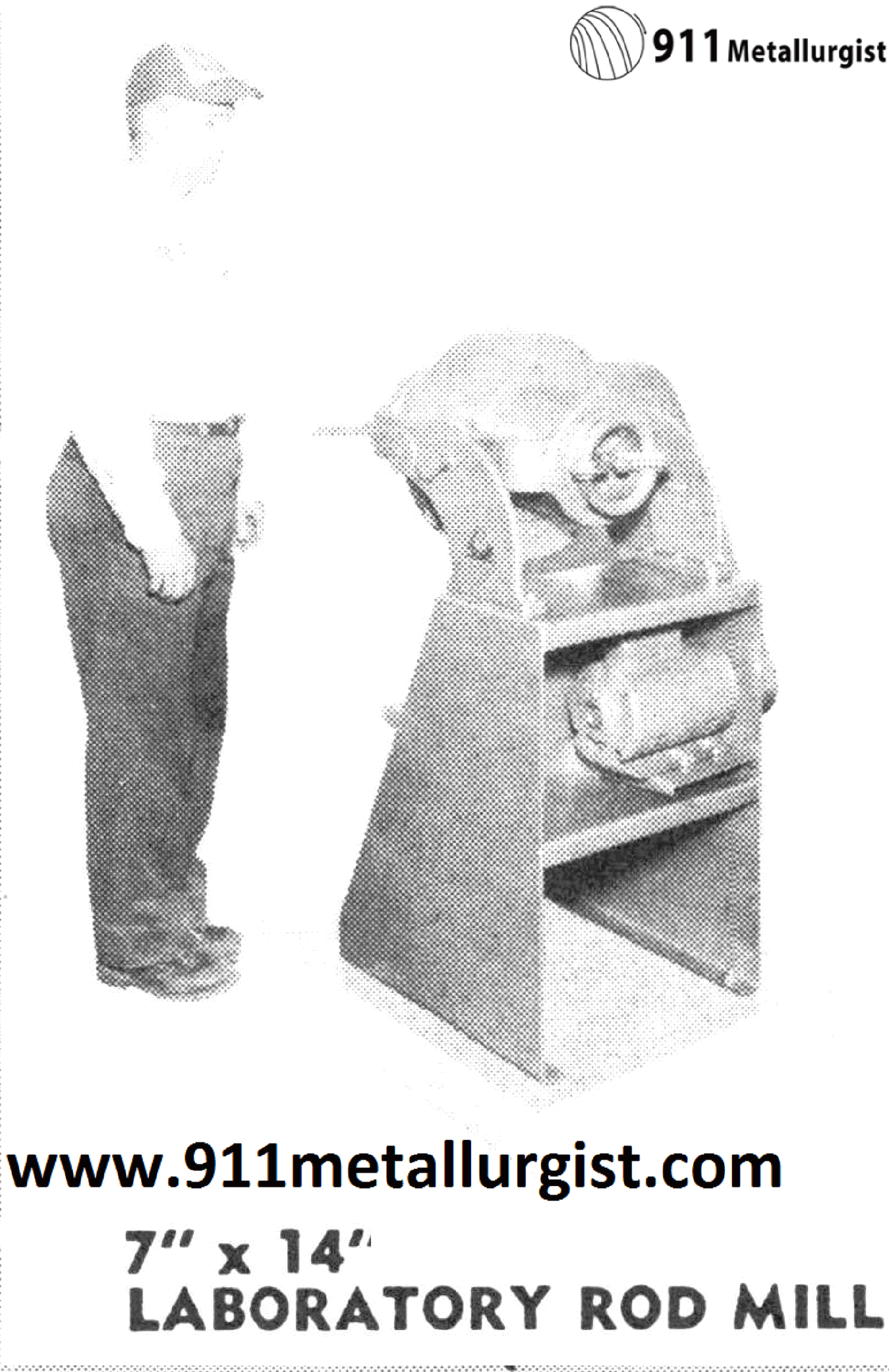
Many grinding problems requiring a minimum amount of fines can be solved by the Laboratory Rod Mill which assures a uniform product without overgrinding. It can be used as a batch ball mill or as a continuous grinding unit. The mill can be rotated at any angle, being held in position by the handwheel clamp. […]
Small Ball Mills

A PULP level sufficiently high to interpose a bed of pulp, partly to cushion the impact of the balls, permits a maximum crushing effect with a minimum wear of steel. The pulp level of these Small Ball Mills can be varied from discharging at the periphery to discharging at a point about halfway between the trunnion and […]
Talc Grinding
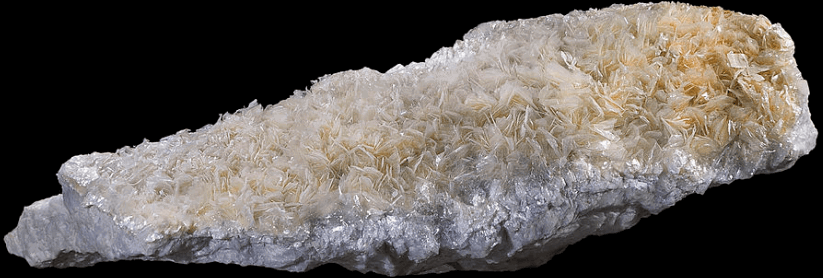
The milling of talc, as is the case with many non-metallic minerals, until recently, has not received adequate technical consideration, for the talc industry has become of importance only within the last decade. At first, talc was used only in the massive form, for foot warmers, griddles, and so on, and milling methods were unnecessary. […]
Crushing and Grinding Wet & Sticky Ore
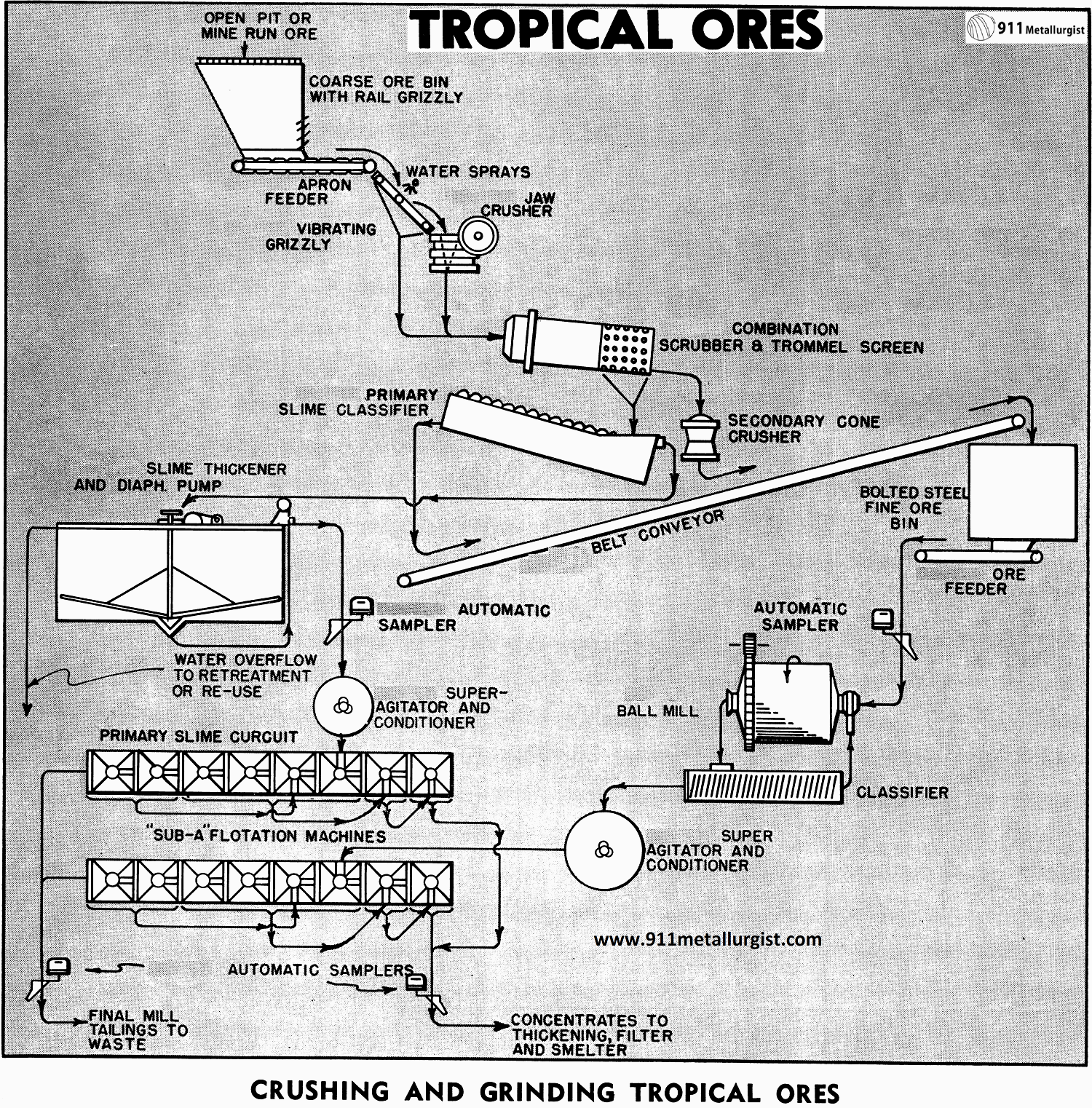
In the handling of wet, sticky ores such as encountered in tropical areas having distinct dry and rainy seasons, the crushing plant is a section of the mill which must be planned very carefully. Unless this is done, crushing becomes a constant source of trouble resulting in lost production and high milling cost. In some […]
How to Operate a Grinding Circuit

How hard a ball mill operator has to work depends partly on himself, and partly on the kind of muck the mine sends over to the mill. In some plants, the ore may change two or three times a shift, and a ball mill operator has to keep on his toes. That’s why it would […]
Signature Plot
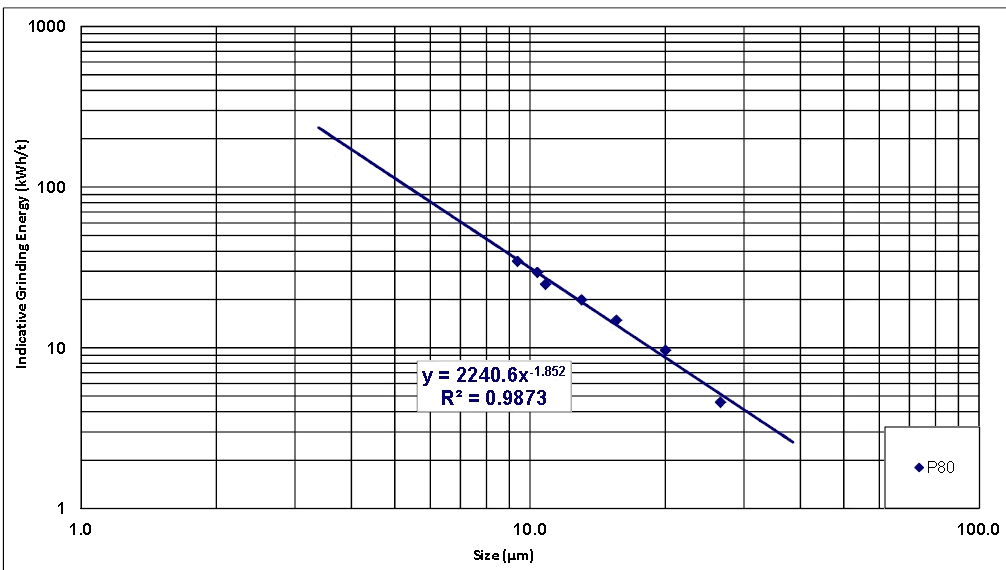
General Procedure for IsaMil Signature Plot The relationship between product size and energy input remains constant during scale-up of IsaMill™ technology. As the diameter of a particle is halved, the surface area of its progeny is doubled. Within reasonable reduction ratios, the log of size plotted against the log of energy produces a straight line. […]
Ball Mill & Rod Mill Design
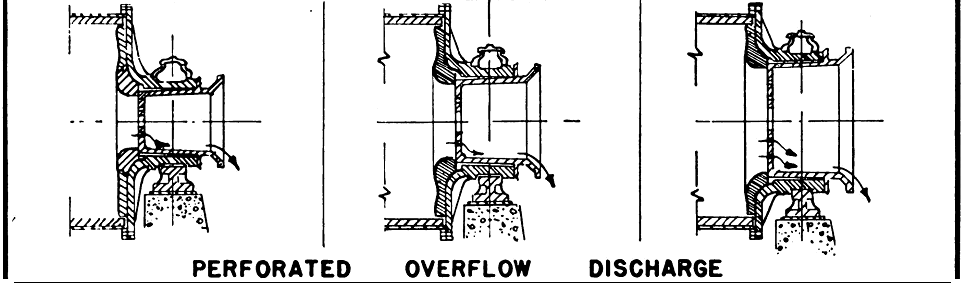
In all ore dressing and milling processes, including flotation, cyanidation, gravity concentration, and amalgamation, it is necessary to crush and grind, often with rob mill & ball mills, the ore in order to liberate the minerals. In the chemical and process industries, grinding is an important step in preparing raw materials for subsequent treatment. In present day […]