Cement Clinker Grinding Aids
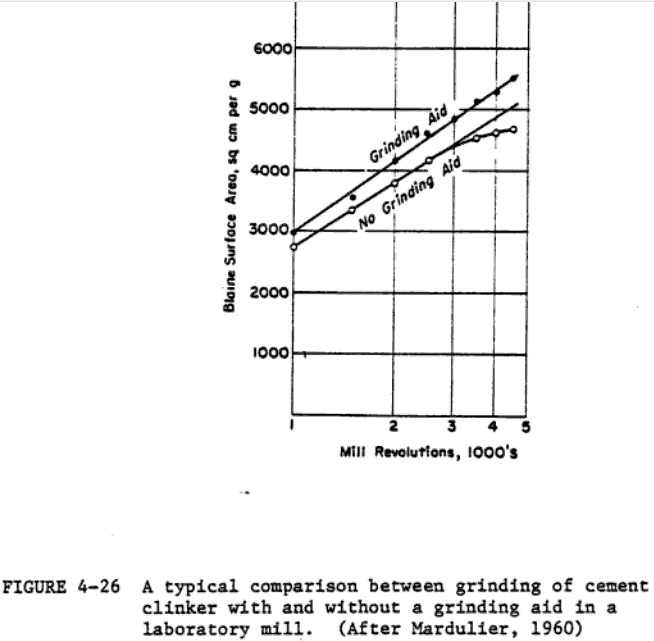
The use of a good Cement clinker grinding aid can be vital in today’s increasing material demands. Along with the obligation to process increasingly larger quantities of ores containing finely disseminated minerals, our limited energy resources and the rising costs of energy present a challenge to the process engineer. One research route that has been […]
Equipment Sizing: Crusher or Grinding Mill
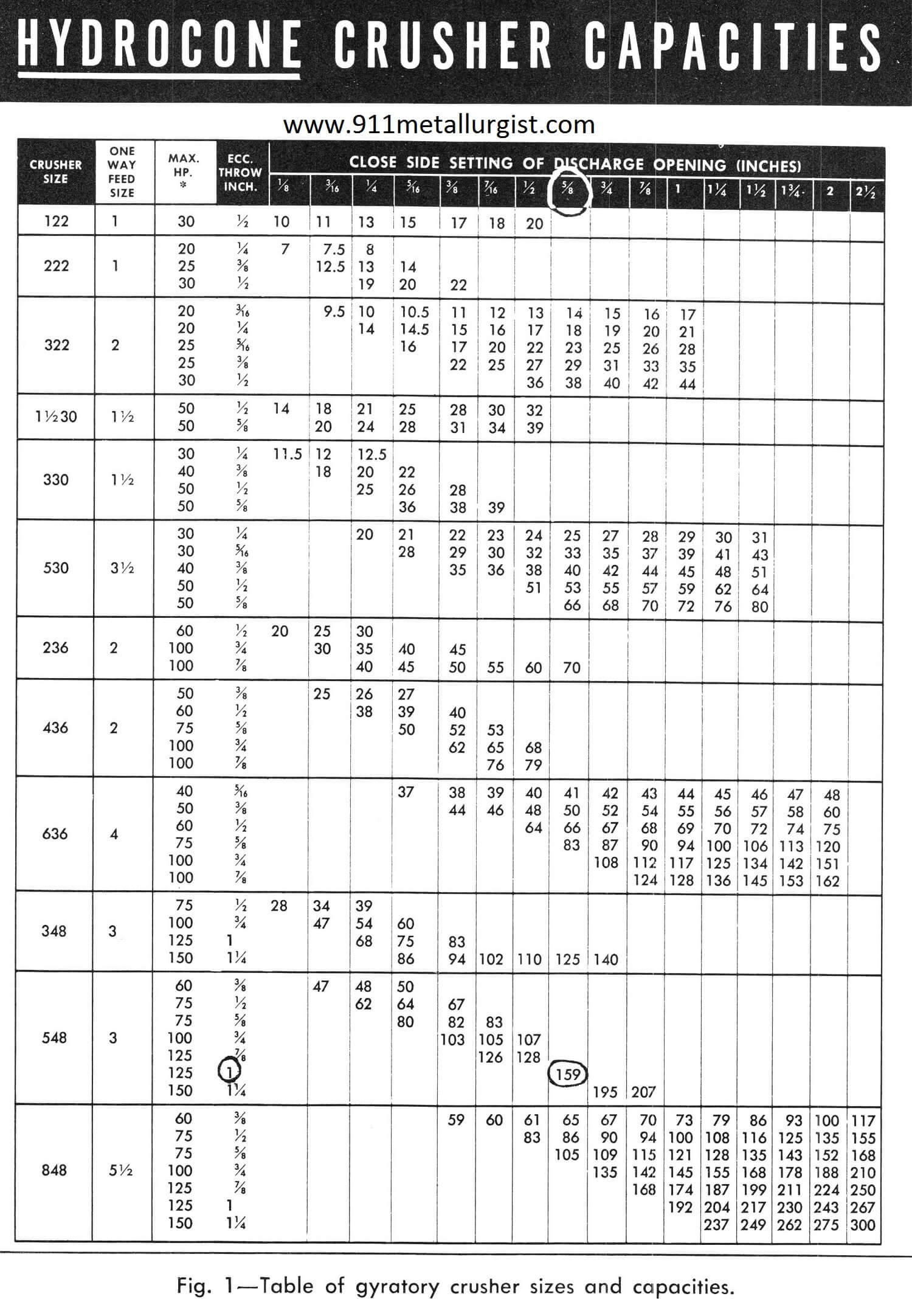
UNTIL THE THIRD THEORY OF COMMINUTION of “Work Index” method of determining crushing and grinding mill size was introduced, there was no way of accurately figuring the most applicable, most economical size of crushing and grinding mill. Naturally, with little or no factual operating data correlated in useful form, it was easy enough, even for […]
Arrastra
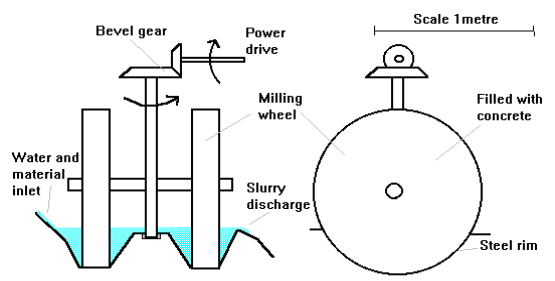
The Arrastra was also one of the earliest crushing machines in use in America, being introduced at the same time as the Patio process—i.e., about 1557—and is still in wide use in Mexico, although chiefly in the treatment of silver ores by the Patio process. It is a circular, shallow, flat-bottomed pit, 10 to 20 feet […]
SAG Mill Reline
https://www.youtube.com/watch?v=9JEko22980I
SAG Mill Liner Design
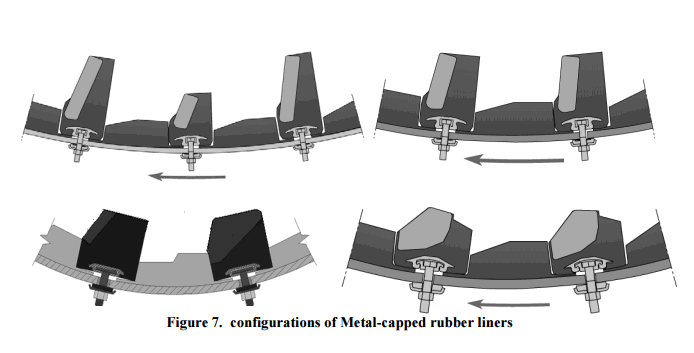
To a more significant degree than in other comminution devices, SAG Mill Liner Design and Configuration can have a substantial effect mill performance. In general terms, lifter spacing and angle, grate open area and aperture size, and pulp lifter design and capacity must be considered. Each of these topics has had a considerable amount of research, […]
SAG Mill Grinding Circuit Design
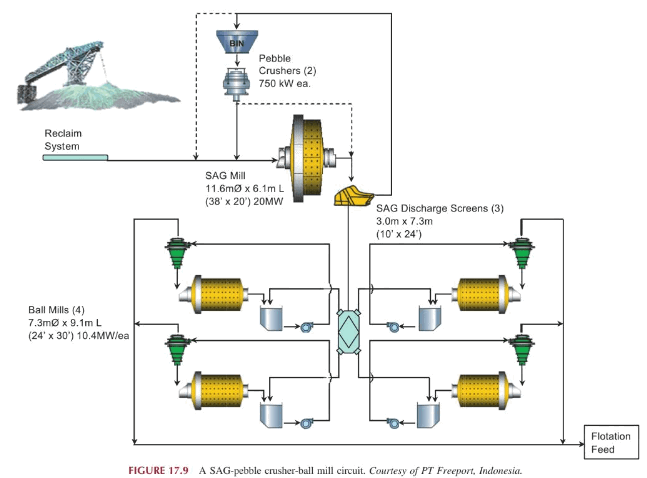
AG and SAG mills are now the primary unit operation for the majority of large grinding circuits, and form the basis for a variety of circuit configurations. SAG circuits are common in the industry based on: High single-line capacities (leading to capital efficiency) The ability to mill a broad range of ore types in various […]
Tower Mill Operating Work Index
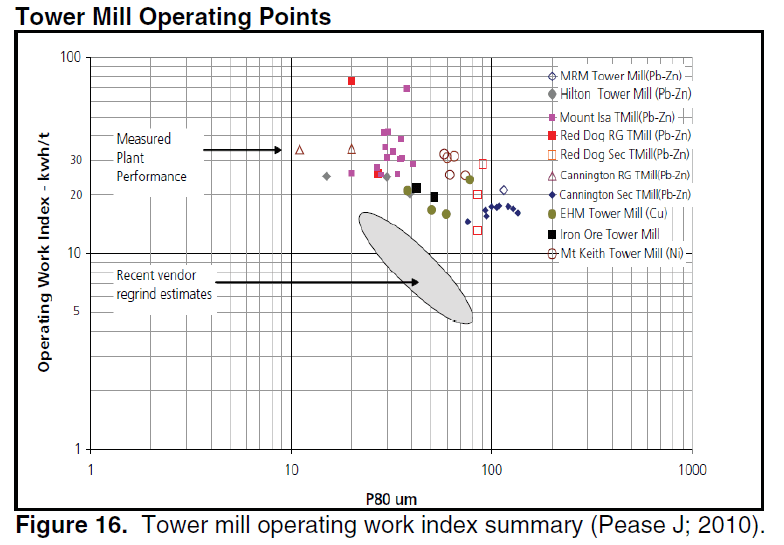
The principal method of grinding in a Tower mill is attrition (scrubbing of particles off material being ground), with the possibility of some shearing and compression breakage taking place due to the motion of the media charge created by the rotation of the helical screw enhancing the media pressure. The Tower mill is filled to […]
Screw-Spiral Classifier: Select, Size & Install
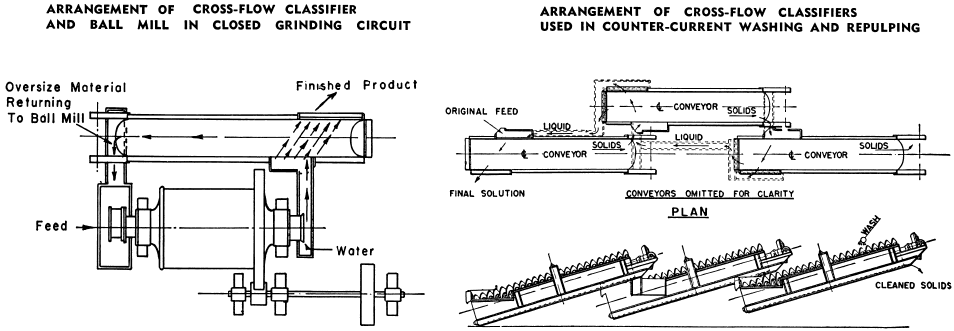
The size of mechanical classifier required for a particular job depends on the following factors: Tons of dry solids to be overflowed per 24 hours. This is simply a predetermined tonnage. Mesh size at which separation is to be made. The mesh size is determined by laboratory tests or is already known from previous experience. […]
Hydroclassifier
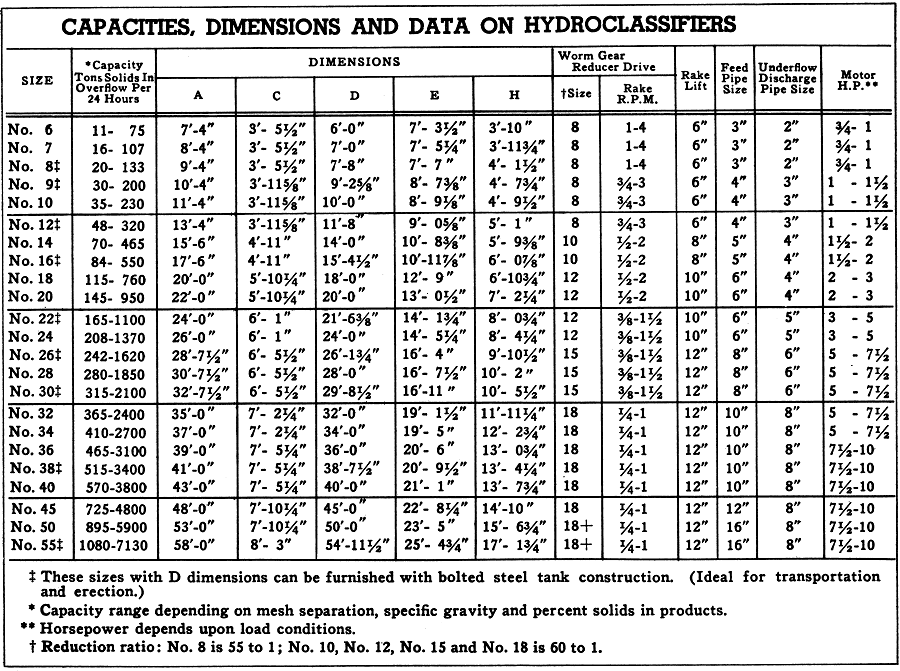
Hydroclassifiers are solving the most difficult fine sizing and desliming problems by combining high metallurgical efficiency in a rugged, well- built machine to accurately fulfill the exacting conditions required. Accurate separations can now be made in the 100 mesh range and finer. This fine separation requires considerable classification area per ton as well as minimum […]
Ball Mill Discharge Spiral and Trommel Screen
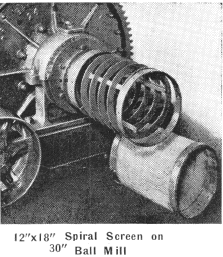
Ball Mill Discharge Spiral Screen The Ball Mill Discharge Spiral Screen is designed to make a sized product, particularly for “Sub-A” Unit Flotation Cells and concentrating tables. It is also used to screen out and return to the ball mill any oversize in a ball mill-classifier circuit when using a (Selective) Mineral Jig. This Ball Mill […]