Huntington Mill
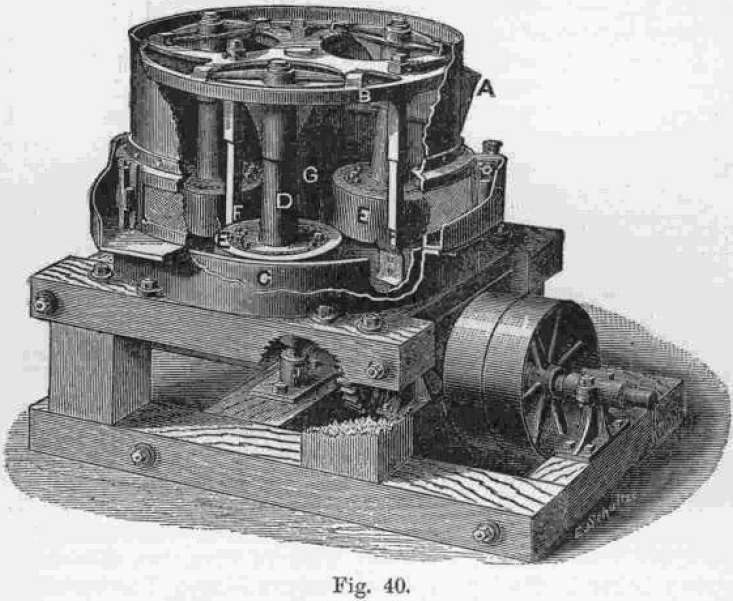
The Huntington Roller Mill, here described as a type of the many good roller mills now in use, is best suited for the fine crushing of ores which are not too hard. It consists of an iron pan, at the top of which a ring, B (Fig. 40), is set, and attached to this are three […]
Ball Mill Gear
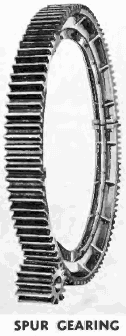
Two general classifications of gearing are used for ball Mill drives. These are the spur gear and the helical gear. Helical gearing may be either of the single helical or double helical (Herringbone) design. SPUR GEARS These are generally furnished on the smaller diameter mills using V-belt drives or reducer drives. Spur gears and pinions […]
Ball Mill Drives
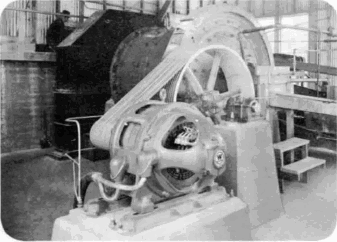
Several types of ball mill drives can be furnished, made up of various combinations of gearing, motors and transmission equipment. The correct combination to be selected takes into consideration power requirements, gear ratings, floor space, interference from other plant equipment and motor characteristics. The main types are described and illustrated on these pages. Motors considered […]
Ball Mill Feeders
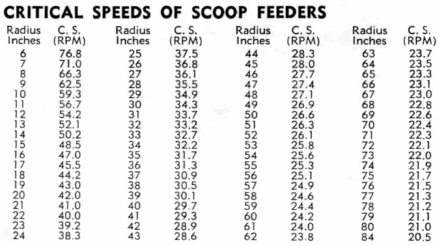
Each application dictates the selection of proper feeding arrangement. This depends upon whether the grinding will be open circuit or closed circuit, and dry grinding or wet grinding. The size of feed and tonnage rates are also important factors. Speed of scoop lip is important. Listed below for your convenience is a table showing critical […]
Pebble Mill Grinding
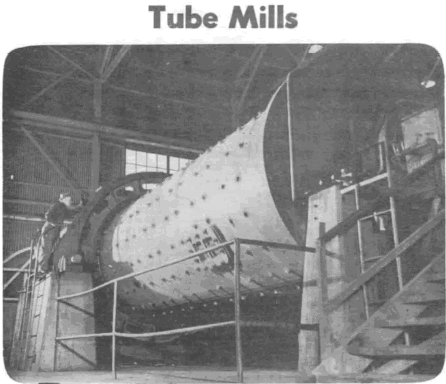
Essentially tube mills and pebble mills may be considered as ball mills, the basic difference being that the ratio of length to diameter is greater. Usually the shell length is between 2 and 5 times the diameter. These mills are primarily used to grind various materials to 100 mesh and finer. The Tube Mill uses […]
Cement Grinding
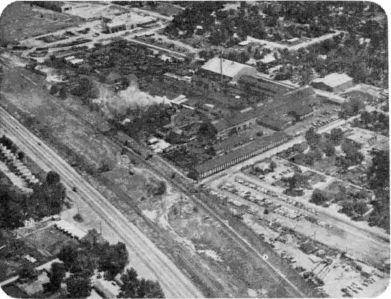
The principle of Grate Discharge grinding is nearly universally adapted in the cement grinding industry. Grate Discharge Ball Mills are the rule rather than the exception. Rod Mills for raw and finish grinding begin to enter the picture. Larger and larger diameter mills become common. Lengths tend to shorten. Cement grinding using Grate Discharge principles developed in […]
Comminution Theory & Process Equipment
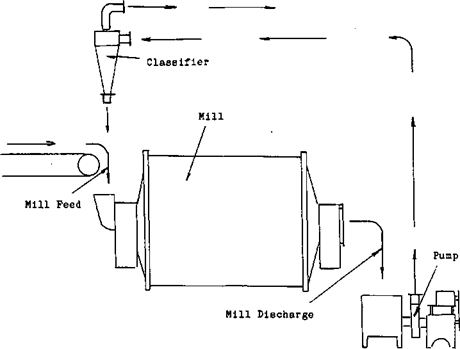
This page is devoted to the subject “From the Comminution Theory to Practice by selection of the correct Process Equipment” by taking you step by step through some of the variables encountered in the specific part of Comminution called grinding and how each of these affect your operations. Should it be possible to reduce all of these variables to […]
Grinding Balls & Rods
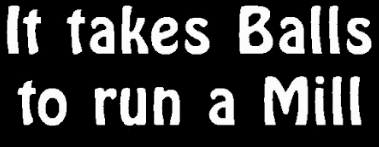
The subject of grinding media (grinding balls & grinding rods) is still controversial. The following information is general and based upon facts gathered from many operations. General statements can be made and are worthy of consideration when selecting grinding media. For the best results it has been found that the smallest diameter ball or rod […]
Industrial Ball Mills
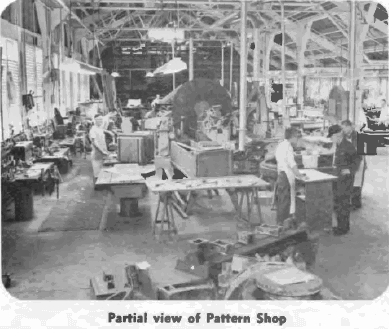
A symbol of dependable quality ore milling machinery manufacturing, industrial and mining equipment, ball mills and rod mills as well as supplies created for your specific needs. During this period thousands of operators have experienced continuous economical and unequalled service through their use. As an industrial ball mill manufacturer and supplier, we have continuously accumulated knowledge on grinding […]
Rod Mill & Ball Mill Manufacturer & Supplier of Grinding Mills
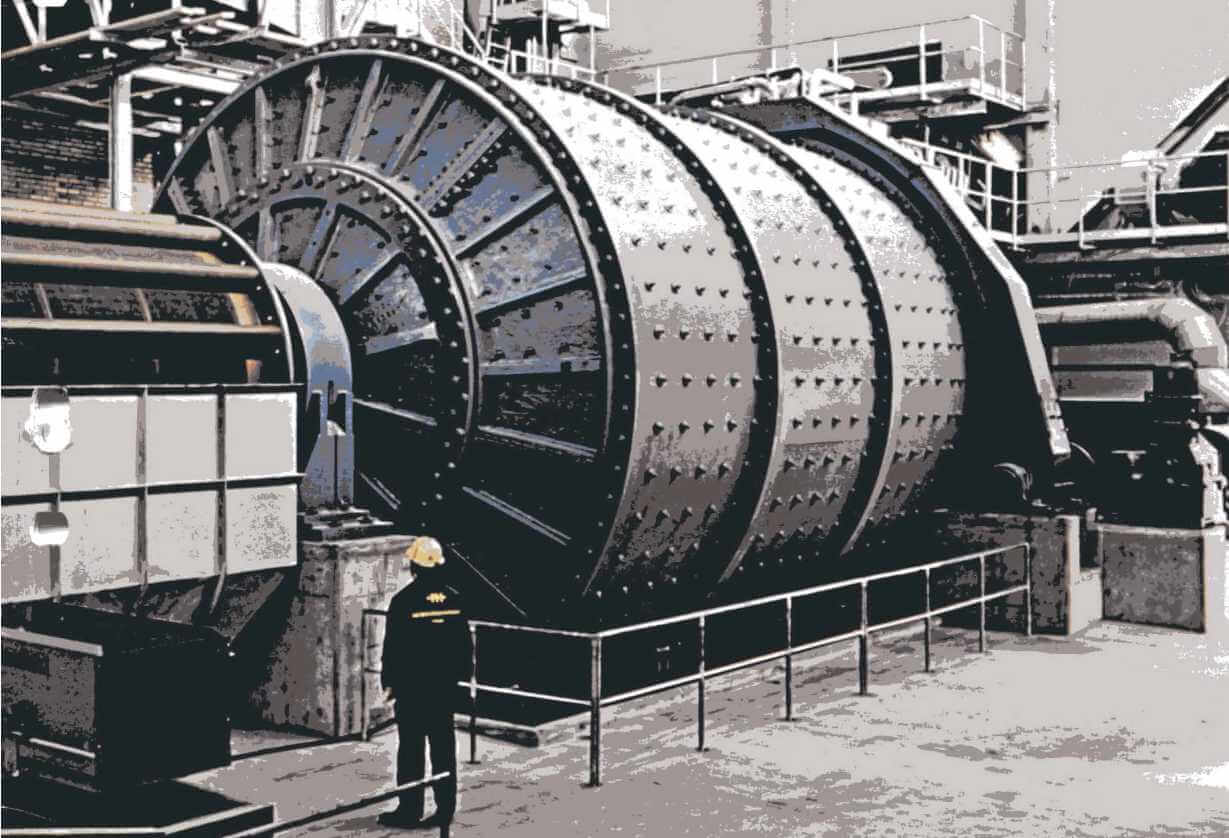
All Ball Mill Manufacturers understand the object of the grinding process is a mechanical reduction in size of crushable material. Grinding can be undertaken in many ways. The most common way for high capacity industrial purposes is to use a tumbling charge of grinding media in a rotating cylinder or drum. The fragmentation of the […]