Grinding Media and Liner Wear Rate
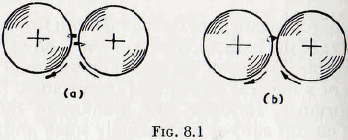
The cost of replacement of the metal worn from the working surfaces of the balls and liners of a mill often represents a considerable fraction of the cost of operation of the plant and so is of some real economical importance. In spite of this importance, however, the amount of information in available on this subject […]
Grinding Process
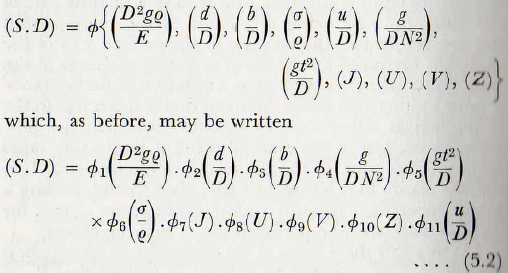
In the previous chapter, the various “laws” of comminution which have been propounded have been studied in relation to the physical process of size reduction and to the available results of experiments into the fracture of homogeneous and heterogeneous materials by impact and by slow compression. In this study it is seen that no satisfactory […]
Comminution
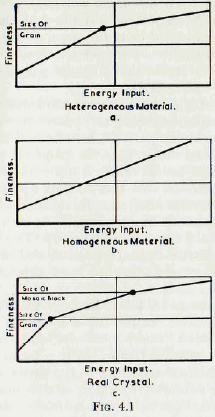
The problems associated with comminution of solid bodies in numerous and complex. In spite of the large amount of investigation which has been undertaken, the present state of knowledge is such that there is no theory by means of which the behaviour during fracture of even a single particle under the simplest possible mode of loading can […]
Grinding Media Charge Motion inside Mill
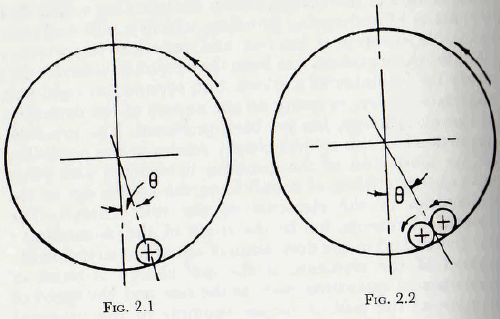
The motion of the charge, that is the grinding media and the material undergoing grinding, within a mill is of considerable theoretical interest and practical importance, and for these reasons, has been the subject of considerable study by a number of workers, but, even so, no rigid and complete theory, covering all the aspects of […]
Grinding Mills – Common Types
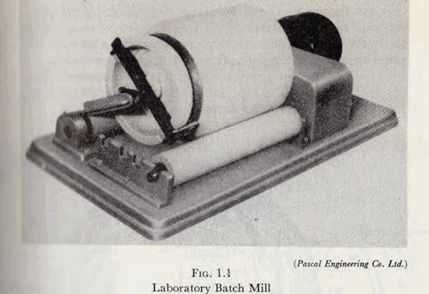
In many industries the final product, or the raw material at some stage of the manufacturing process, is in powdered form and in consequence the rapid and cheap preparation of powdered materials is a matter of considerable economic importance. In some cases the powdered material may be prepared directly; for example by precipitation from solution, a […]
Which Grinding Mill is Best for Regrinding by Types

Ball Mills and stirred mills are applied across a wide range of applications, but for each ore there is optimum efficient range. The figure to the left shows the typical application ranges for ball mills and stirred mill. The Vertimill is always more efficient than a ball mill with energy savings ranging from 30% to […]
DIY Ball Mill Plans – Homemade Rod Mill Drawing

By this drawing, it is suggested that a typical homemade laboratory rod mill or ball mill might be fabricated from 20 cm (8 inches) diameter schedule-40 type 316 stainless steel pipe and would be about 38 cm (15 inches) long. The plans show stainless steel grinding rods for this size of mill may be a […]
Tube Mills
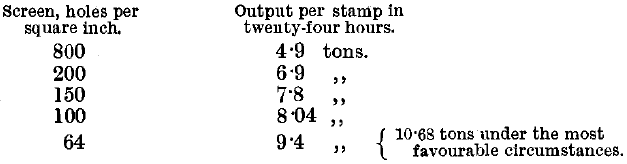
Tube Mills consist of revolving cylinders, the interior of which is perfectly plain. They contain a number of hard balls. They differ from ball mills essentially in having the inlet for ore at one end and the outlet at the other, and in the absence of provision in the machine itself for the return of uncrushed […]
Grind Size & Liberation for Optimum Flotation Recovery
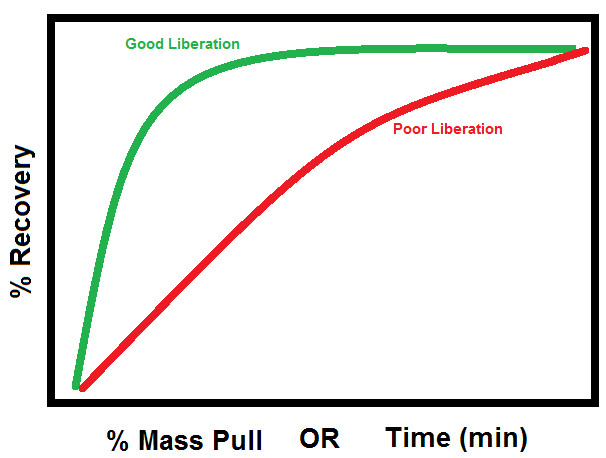
Here is a trick for knowing if your flotation feed grind size is fine enough to achieve adequate mineral liberation without doing a full mineralogy study. If your key mineral is sufficiently liberated, it should float and be recovered in the first few minutes in an initial %mass that stabilizes quickly = the green curve. […]
Roller Mills
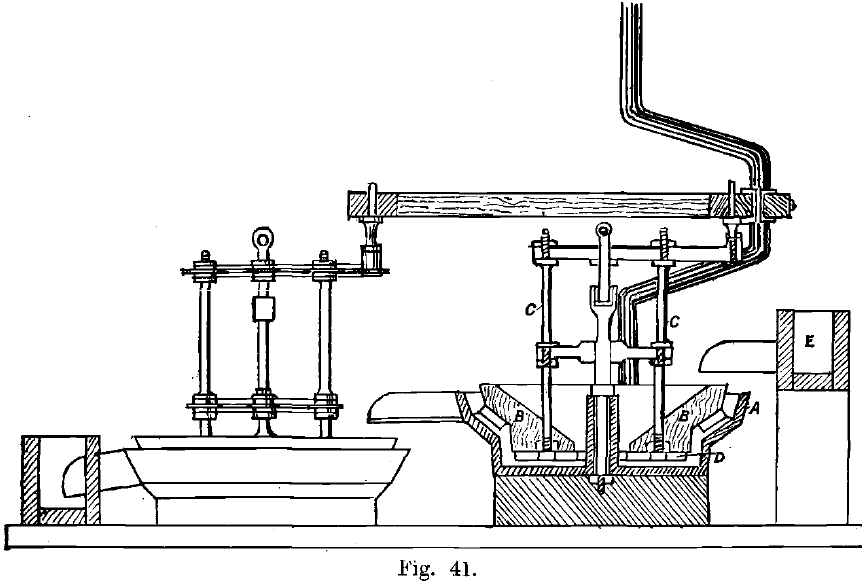
In the Griffin Mill, there is a single roller suspended in a similar way to the rollers in a Huntington mill. The roller is about 18 inches in diameter, and rolls on the inside of a die ring 30 inches in diameter. It takes material up to 1½ inches in diameter, and crushes either wet […]