Conical Ball Mills VS Chilean Pan Mills
In view of the prominence which the conical mill has attained in the fine-crushing field within the few years since its introduction, the following comparison with its more mature forerunner, the Chilean mill, based on extensive tests, is submitted in the interest of the milling profession. Soon after designing the concentrating plant, the conical Ball mill […]
Hardinge Conical Mill – Grinding Efficiency Compared
Nearly every mining and metallurgical engineer will recall his early experience and method of producing step- or stage- reduction in preparing ore-samples for assay, in which he employed idea, step- or stage-reduction simply because it was a self-evident fact that it would be easier to break coarse ore with a hammer than it would be […]
Difference between Crushing and Grinding
When making comparisons of the efficiencies of different grinding and crushing machines it is desirable to be able to estimate the work actually done in crushing the ore from a given size of feed to a given size of product, the screen analysis of both feed and product being determined. Messrs. Klug and Taylor, in […]
Ball Mills

In all ore dressing and milling Operations, including flotation, cyanidation, gravity concentration, and amalgamation, the Working Principle is to crush and grind, often with rod mill or ball mill, the ore in order to liberate the minerals. In the chemical and process industries, grinding is an important step in preparing raw materials for subsequent treatment. […]
Wooden Ball Mill
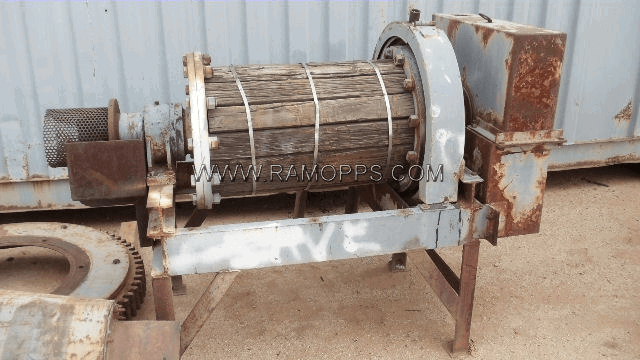
Can I use BWi Bond Work Index to Size a Regrind Mill: Fine Grinding Modelling

Many power-based grinding models exist, and most operators are familiar with Fred Bond’s “third theory”. Bond’s model is most commonly used to describe primary and secondary grinding to product sizes above, for example, 100 µm. Operators sometimes use Bond’s equation to describe grinding in situations where it is not appropriate, such as fine grinding […]
Effective Hardness & Abrasive Efficiency of Corundum
The Relation Between the “ Effective Hardness ” of Corundum and its Content of Water: A specimen of corundum from Acworth, Ga., which was reputed to be of markedly inferior quality for the manufacture of corundum-wheels, was received by the Geological Survey of Georgia, with the request that it be analyzed, in order to ascertain whether this inferiority was associated […]
Stamp Mill Performance Diagrams
The object of the present paper is to call attention briefly to a novel method of analyzing the action of the ordinary gravity stamp, which has not only thrown much light upon the exact motion of the stamp-head, but promises also to be of value in determining the efficiency of a new mill before setting […]
Basic Ball Mill Grinding Circuit
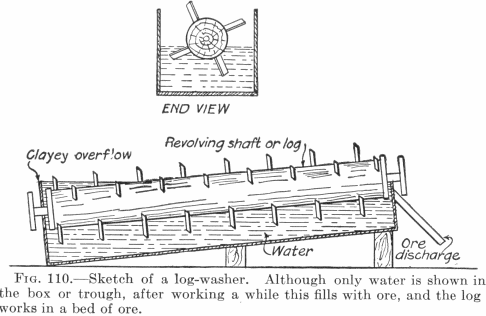
A mill consists of a steel shell supported at each end by a hollow trunnion running in a bearing, lined with steel plates, and driven by belt and gears or by motor and gears. The mill is set at a slight slope and is fed with finely crushed ore and water through one trunnion. When […]
How Much do Steel Grinding Balls Weigh
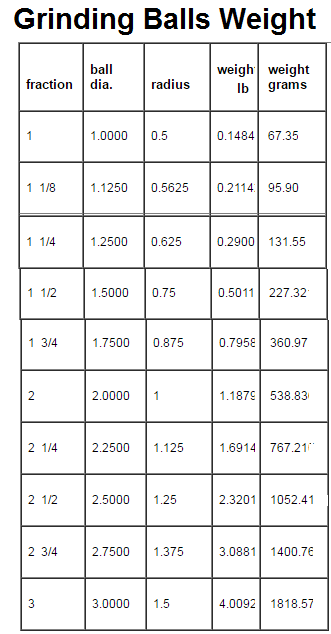