Increase Plant Throughput by Mill Expansion
Shortly after start-up, it was apparent that it would be difficult to obtain the plant design throughput. The ore sample that had been used for grinding test work was found to be much softer than that of the orebody in depth. This had led the designers to design without a crushing stage and to designate […]
Rod Mill & Ball Mill Grinding Circuit
This Rod Mill —Ball Mill grinding team is in operation at a new 500 ton-per-day, base metal, selective flotation mill. Preliminary Grinding Tests Without Charge Mill size and specifications are determined by experienced engineers who study your grinding problem in detail and take into account the effect of grinding on your total milling circuit. Laboratory […]
Mill Bearing Strength & Grinding Mill Design
First, let us look at the mill itself. Fig. 1 shows that there are four basic components – The shell, the heads, the ring gear and the trunnions. The heads are usually bolted to the shell. The trunnions are secured to the heads by bolts or made integrally with the head. The ring gear is […]
Automatic Grind Control
The “best” control strategy for a given plant is the strategy that most closely fulfills the overall operating objectives. The best strategy will likely not be “optimum” for any given specific goal but rather will involve a series of trade-offs made in consideration of the many factors that influence the operation in any significant way. […]
Grinding Mill Power
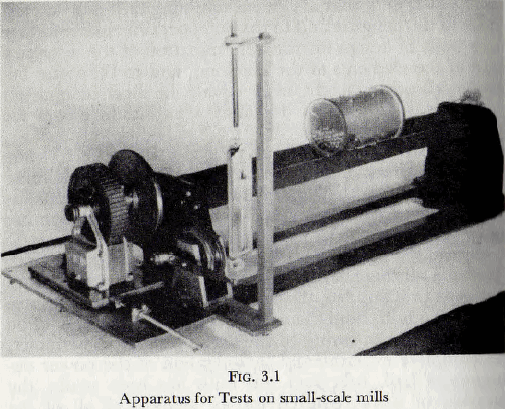
The power required to drive a tumbling mill is of interest both to the designer and to the mill operator: to the former as a basis of design for the determination of the necessary size of the elements of the machine; and to the latter because all other factors being equal, the most economical machine is […]
Grindability of Various Ores
During the last few years, one of the great problems in the milling of all ores has been that of grinding. This subject involves not merely the cost of the operation, but also the selection of the proper degree and character of grinding to yield the best metallurgical results on the given ore. Considering the […]
Grinding Media Wear Rate Calculation in Ball Mill
In the previous discussion the fact was established that the work done by a ball when it strikes at the end of its parabolic path is proportional to its weight and velocity; then, since the velocity may be considered as constant for all the balls in the mill, the work done by a ball is […]
Ball Mill Grinding Theory – Crushing Motion/Action Inside
Testing Plant Equipment: In order to determine, among other things, the operating conditions of the ball-mill when working on this rock, a test mill of about 300 T. daily capacity was erected at Duluth, Minn. The fine-crushing plant contains a Hardinge 8-ft. by 22-in. (2.4-m. by 55.8-cm.) conical mill, a 6- by 27-ft. (1.8 by 8.2-m.) […]
Ball Milling
These notes are based on observations made while on a recent trip through the West, for the purpose of studying the practical operation of the ball mill. The writer takes this opportunity to express his thanks for courtesies extended at the many plants visited as well as for the valuable data received. While there are […]
Hardinge Conical Mill Capacity
The following conclusions on the work of the Hardinge mill are based on data furnished to the writer by the Hardinge Conical Mill Co. in the form of the mesh cards hereto appended. Energy units (E. U.) and relative mechanical efficiencies (R. M. E.) are computed by the “volume method” of Stadler. Screen apertures used […]