100 to 125 TPD Process Plant Design & Equipment
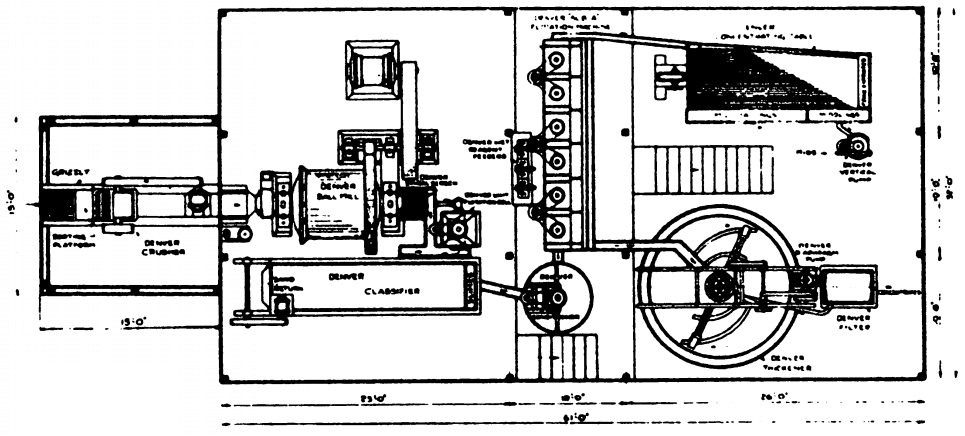
The 100 to 125 Ton/Day Mill is arranged along the same standard lines as the smaller mills, and a large oversize forced feed crusher is recommended for primary crushing. An intermediate crusher can be installed later if necessary. Changes can be easily made according to your local conditions. Here too, a Selective Mineral Jig may be […]
Small 50 to 75 TPD Process Plant Design & Equipment List
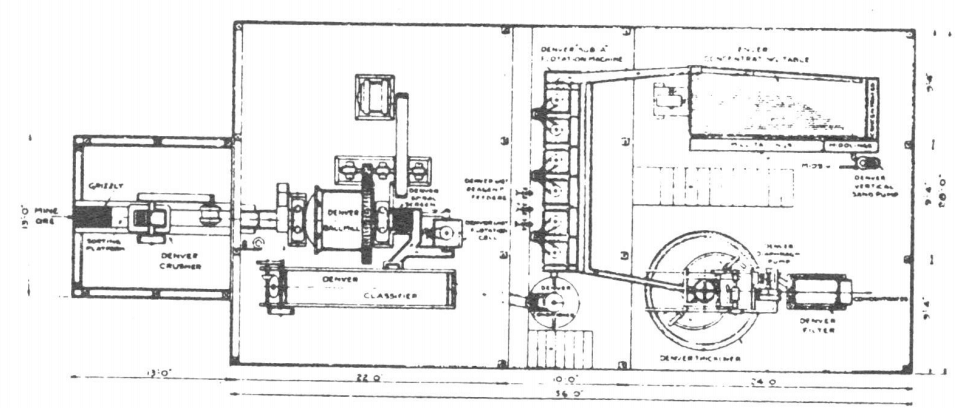
The 50 to 75 Ton per Day process plant is the most practical size for the average milling plant. The 9″ x 16″ Jaw Crusher (forced feed) produces enough crushed ore for the ball mill on one eight hour shift to run the balance of the mill for twenty-four hours. Oversize primary crushers are recommended for […]
Process Equipment List for a 50 Tons Per Day TPD Flotation Plant
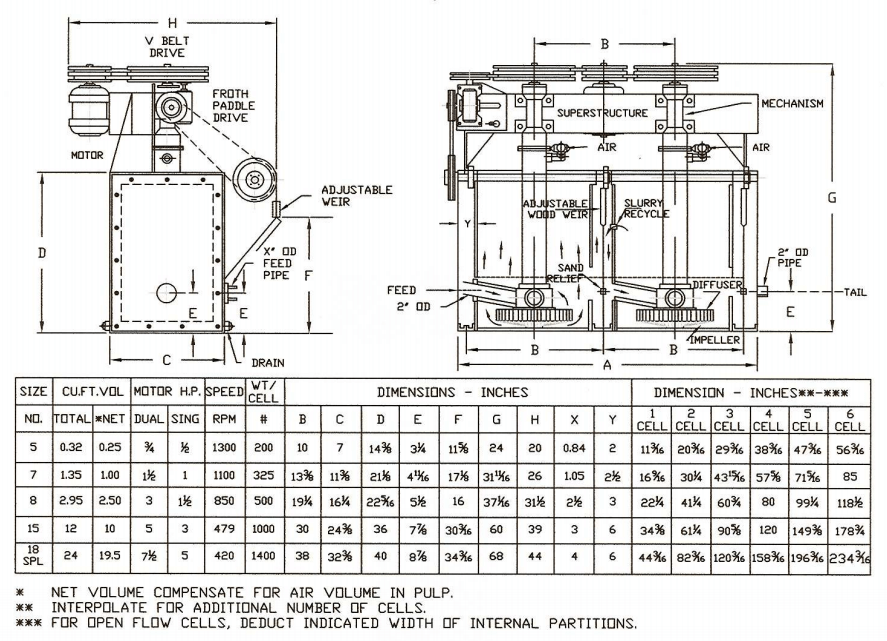
Here is an example process equipment list you’d need to build a small 50 TPD flotation plant to recover metals like copper, lead, zinc or even nickel and most sulphides be froth flotation. Process Plant Equipment Approximate Motor H.P. Crusher 10 x 16 20 Fine Ore Bin Belt Ore Feeder 20″ x 10″ 2 Ball […]
Gold Leaching Plant for Sale

FLOWSHEET CY3, COUNTER-CURRENT DECANTATION CYANIDE PLANTThe following estimates are for counter-current decantation cyanide circuits and are based on average grade ore requiring average treatment time. These include precipitation and accessory equipment. The equipment required for a cyanide plant will vary considerably with the value of the ore, the settling rate, the chemical composition of the […]
Base Metal Ore Processing Plant & Equipment (Copper & Lead+)
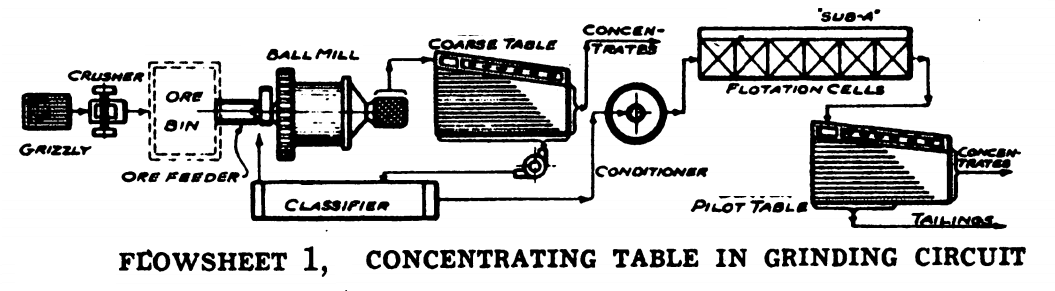
These 5 following estimates on flotation mills cover standard practice as used on base metal and non-metallic ores where the majority of values are recoverable by flotation, and where there is sufficient freed mineral in the ball mill discharge to warrant recovery by means of process Equipment like either a Unit Flash Flotation Cell, a […]
Small Gold Ore Processing Plant
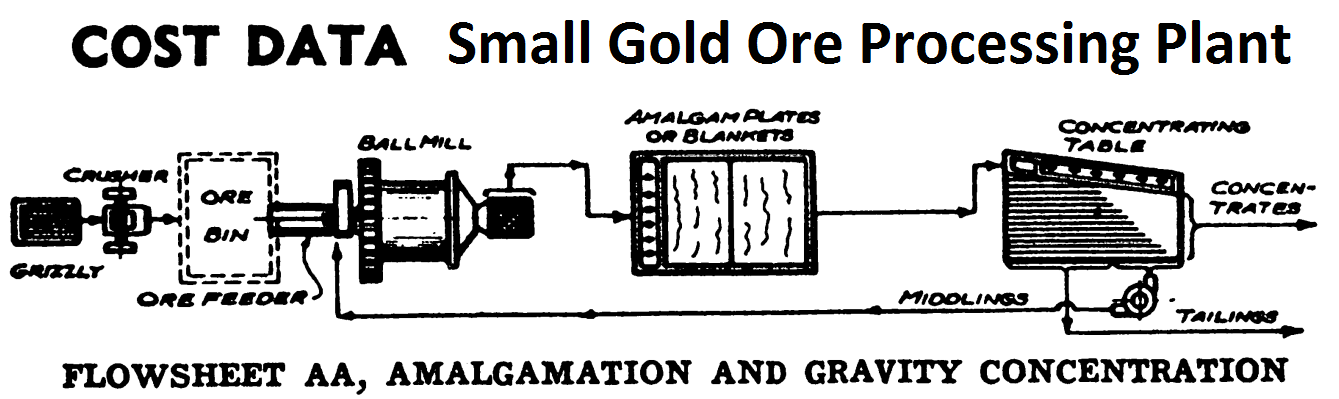
These five illustrated flowsheets fully described in the article “Small Gold Ore Processing Plants” follow a natural sequence. These start with a very simple. Flowsheet AA, and then by the addition of the more extensive equipment, it is possible to take care of slight changes in the ore as well as improve recovery. The following […]
Cyanide Processing Equipment and Plant Options

The Jig, placed between the ball mill and classifier, is one of the most valuable and affordable improvements in cyanidation in recent years and was developed by the metallurgical engineering and Mining Equipment Companies. This Mineral Jig has the marked advantage of removing a large portion of the metallic values without excessive dilution, and water […]
Gravity Recovery or Flotation ahead of Gold Cyanidation

Process Flowsheet NO. CY-3 is shown one of the outstanding improvements made in cyanidation whereby the coarse metallic minerals are removed from the grinding circuit by means of the Mineral Jig. The hutch product from this jig is amalgamated with a Amalgamator or Clean-Up Pan and thus the coarse mineral values, such as metallic gold, are […]
Counter Current Decantation Cyanide Gold Leaching

The Process Flowsheet CCD CY-1 shows (below) the continuous counter-current decantation system, in which all the ore is first reduced to a very fine state in the grinding mill-classifier circuit, in a cyanide solution. The slime overflow of the classifier, usually 70%—200 mesh, or finer, is sent to the first thickener, known as the primary thickener. […]
Gold Cyanidation Circuits

The principle of dissolving gold and silver values in solutions of potassium or sodium cyanide is old and has been thoroughly carried out in practice for many years. There have been only a few changes in the chemical procedure and also few changes in the type of equipment used. The gold and silver are dissolved […]