Table of Contents
List Equipment Required to Perform of a Standard Bottle Leach Test
- Winchester bottles, with tops
- Plastic tape to seal tops of bottles
- Flexible air lines for possible aeration requirements
- Magnetic or mechanical stirrer for agitation
- Timer, pH meter, thermometer and weighing device
- Leachants, i.e. acid, alkaline or neutral solutions, or specific solutions
- Filter: vacuum or pressure
- Titration systems
Procedures
- Dry the ore and crush it to minus 2380 pm (or as specified, otherwise).
- Prepare the solution of required concentration (e.g. 1M H2SO4 requires 52 ml of con. H2SO4/litre of water).
- Place 50 gm sample in the leach bottle and add 250 cc of prepared solution.
- Allow leaching to take place for 1 hour under stirred conditions, ensuring the right conditions of pH, temperature, % solids, etc.
- After leaching, discharge contents of leach vessel into clean pressure or vacuum filter without washing the vessel.
- Filter pulp, and collect pregnant leach liquor undiluted.
- Wash ad dry the residue and record it weight.
- Analyse residues and pregnant liquors for relevant metal content.
Precautions
- When handling concentrated acid, always wear eye protection, and always add acid to water. If water is added to concentrated sulphuric acid, the heat generated could vaporize the water and cause an explosion; by adding the acid to water, the heat is generated more slowly and is rapidly dissipated by the water.
- Residues should be thoroughly washed of leaching reagents.
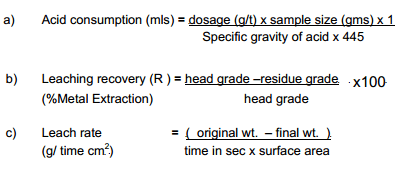
Bottle Leach Procedure for Cyanidation.
Be sure to use at least 500g, but 1000g per test is better. Be sure to use a big enough bottle. You need to lay it on its side to use it on the roller while having a small hole in the lid to allow air inside. Alternatively you can use an air bubbler during the leach. We normally run a kinetic test where we take the bottle off the roller and sample the solution at 2, 4, 6, 24 hours and each 24 hours afterwards until the leach is complete. During that time, after you take your sample, you can sparge the sample with air or oxygen to simulate the air added during the process. Measure the dissolved oxygen if you can. There really is no substitution for measuring the DO, the redox or ORP can be informative but it is not equivalent. Even if you have sufficient cyanide the leach can stop if there is not sufficient oxygen.
I suggest you conduct kinetic leaches. They are a little bit more tricky because you need to replace the liquid you remove and then account for the gold removed in the balance. I have attached a balance you can use. You should use at least 3 points for your kinetic curve. The time represented by the second cyanide addition point in your circuit at CIL tank 4, then the end of the circuit, plus another lot of time that is convenient to the technician. You don’t want to die wondering if the leach would have got a higher recovery if you just had more time, so add more time. The balance provided has 8 points.
At the kinetic sampling points measure the cyanide. Your metallurgist and operators know the cyanide titration procedure. Add enough cyanide to bring the concentrate back to the desired point. The current circuit starts at 600-650 ppm then adds cyanide part way to 300-350 ppm.
Ok, that is the preamble. Prepare your sample. Homogenization is your friend. If you don’t split your lab test samples representatively then you will have a mysterious time with your test program. Sample from the existing circuit, the flotation tail, and ensure your lab procedure reproduces the actual results. Do a few repetitions, check the effect of the water you are using. Perhaps filter off the existing water and add the water you intend to use during the lab testing. Make sure you do enough tests where you have a good idea of what the results are supposed to be for your circuit. Consider this a calibration. If you are not confident of how your lab tests reproduce your actual circuit performance then take care when reviewing your conclusions. Make sure your heads match with each test. You should be able to reproduce a 95% match, you can loosen to 92% knowing that you have coarse gold and it may be difficult to reproduce the head. Use duplicate tests to build your confidence.

A test program starts with using your current conditions on the new ore. If the recovery is good then you are done, congrats. If not then you change one variable and do another test. I would suggest running a sample you know along with your new sample, and a another new sample with a higher cyanide concentration. Running 1 test a time is a bit slow because these can take a week to get results. More than 6 at a time is difficult for 1 technican. Although a good tech can handle 20, they have to be really prepared.
Be aware of the First Aid Treatment for cyanide poisoning. Do not mix cyanides with acids: deadly cyanide gas will result.
- Tare an empty clean glass leach bottle on an electronic scale. Record the bottle weight on the Cyanidation Test Form.
- Place the dry ground or pulverized test sample into the tarred bottle using a powder funnel. Record the mass of the sample on the Cyanidation Test Form.
- Calculate the amount of water required to achieve the target pulp density using the formula given below:
Example:
% Solids = Dry Solids Weight * 100/ (Dry Solids Weight + Weight of Water)
OR
Weight of Water = (Dry Solids Weight * 100 – Dry Solids Weight) /% Solids
- Re-zero the scale with the bottle containing the test sample on the platform. Add the calculated amount of water into the bottle containing the test sample. Record the volume of water added and the percent solids.
- Weigh the bottle containing the test sample and water on the scale. Record the total weight of the bottle containing the sample and water.
- Agitate the slurry in the bottle. Measure and record the natural slurry pH.
- Add lime (CaO or Ca(OH)2) to the slurry to achieve protective alkalinity (pH > 10). Record the amount of lime added and the slurry pH.
- Add sodium cyanide (NaCN) to the desired concentration (g/L) of solution. Record the amount of sodium cyanide added.
- Place the bottle on the bottle roller machine and start the roll. Record the cyanidation start date and time.
- Monitor and maintain pH levels.
- At the end of the predetermined time intervals (ie: after 4, 8, 24, 48 and 72 hours), remove the bottle from the bottle roller machine and set it on a table in the Assay Laboratory.
- An Assay Technician will pipette a sample of the cyanide leach solution from the settled slurry and filter it. The filtrate sample is analyzed for residual lime and cyanide and assayed for elements of interest by atomic absorption spectroscopy.
- When the Assay Technician has completed sampling and analysis, add lime and cyanide to the slurry, equivalent to amount consumed during the time interval. Measure slurry pH and record. Record weight of the fresh lime and sodium cyanide added to the test.
- Zero the scale and weigh bottle containing the slurry. Add water to the slurry (if required) to reach the original (time zero) total weight of the bottle containing sample and water.
- Place the bottle test on bottle roller machine and start the rolls. If more than one cyanide leach test is in progress, add a sleeve onto the neck of each bottle, then lower each bottle to allow air into the bottle when it touches the bottom of the top bottle on the rolls.
- At the end of each timed interval, repeat steps 11 through 15.
- At the end of the test, vacuum filter the final cyanide leach slurry through a Buchner funnel containing filter paper into a filter flask.
- Wash the final filter cake a minimum of three times with three 1000 ml volumes of hot water to wash the soluble metals from the cyanidation tailing solids. Depending on the client’s request, the final filtrate wash solution is either retained or discarded.
- Label and dry the cyanidation tails for sample preparation and assay.
- Fill out an Assay Request/Report Form and submit it to the Sample Preparation department.
Laboratory leaching procedures
Laboratory leaching procedures include studies of dissolving metal ions with an acid, a base or cyanide. Although not so common today, gold amalgamation may also fall in this category. The testing may involve field tests on ore in place, broken ore in stopes, ore and waste in dumps or crushed ore in vats and laboratory tests of ground ore, concentrates or calcines in agitators. The technique may be used to effect the selective solubilization of a desirable component such as copper, uranium or gold or the purification of a product to remove impurities such as MgO from zinc concentrates, copper from molybdenum concentrates or iron from silica sands.
Very little laboratory testing can be done on ore in place so that the research team will have to depend on descriptions of the deposit from the geologist, mineralogist and miner, tests on coarse rock samples and knowledge of the characteristics of the ores of the region involved. Leaching tests on rock samples of any size from 20 cms to 1 cm can.be simulated in columns of adequate diameter and height.
The metallurgist should choose a large enough diameter that there is no adverse “wall effect”. Non-corrosive materials of construction such as asbestos or plastic pipe should be utilized for the columns so that maintenance in the lab will not be high and undesirable constituents of the pipe will not enter the leachant.
The bottom of .the column should be fitted with a suitable filter media. A positive circulating, corrosion-proof pump and reservoir system should be employed – usually using plastic tubing for solution transfer. The most important variables to monitor when leaching ores are time, temperature, feed size, additive requirements, density and leachant concentration and consumption vs. extraction of desirable and undesirable components.
Agitation leaching of ore, concentrates or calcines may be easier to test than static leaching but liquid-solid separation of the residues may be a problem and should be included in the testing. Consumptions of reagents may be higher than in static column tests so that the extra operating costs would have to be justified by higher recoveries. One is not liable to discover that elevated temperatures and/or pressures would be economic today with high energy costs in treating low grade ores by leaching’ but this statement may not be • true with some high grade ores or when treating, high value metals such as uranium or higher grade materials such as concentrates or calcines.
Certain additives such as lime during precious metal cyanidation and oxidants during uranium leaching will be important reagents to monitor.
“Old” Gold Leaching Method
Experiments with small quantities of material in the laboratory will usually determine the maximum extraction that can be looked for. The weight of ore taken may be from 100 to 200 grammes. It is placed in a funnel or lamp glass, fitted with a perforated cork and filter bed, and washed with water, or, perhaps better still, shaken with distilled water in stoppered bottles and filtered. The filtrate may contain soluble salts of iron, copper, and tests are applied for these and also for acidity, and for soluble sulphates and chlorides. The water filtrate may also be mixed with cyanide solution to determine how much cyanide, if any, is decomposed by it. In this way the value of the water wash on the particular ore is determined.
Preliminary tests as to the amount of alkali which it is necessary to add, and the amount of cyanide decomposed are made as follows:
(a) Alkali.—200 grammes of washed ore are made into a paste with water in a porcelain basin, and tested with litmus paper. If an acid reaction is observed, a titrated solution of caustic soda is run in, little by little, until the mixture is neutral. It is convenient to make the alkaline solution of such a strength that each c.c. corresponds to one pound of caustic soda per ton of the ore which is being tested,
(b) Decomposition of Cyanide.—100 grammes of the ore are shaken in an 8-oz. stoppered bottle with 50 to 100 c.c. of a solution of KCy for fifteen minutes, then left undisturbed for twelve hours, and finally shaken again for five minutes. The available cyanide in the separated solution is then estimated and compared with that in the original solution. By merely shaking for a few minutes, most of the decomposition of cyanide is made to take place, but not the whole.
Cyanide solution of 0.1 or 0.2 per cent, is then passed slowly through the ore drop by drop, or shaken and left in contact with it for some time, and then drawn off and the filtrate tested for soluble sulphides, ferrocyanides, sulphocyanides, copper, zinc, and for its reducing power. The tests recommended are:
- Add hydrochloric acid. A white turbidity may indicate the presence of soluble sulphides or of zinc.
- After adding the acid in slight excess, add a few drops of K4FeCy6. A brown coloured precipitate indicates copper, a white flocculent precipitate may indicate zinc.
- Add lead tartrate dissolved in excess of NaOH; a brown or black colour indicates soluble sulphides.
- Acidulate with H2SO4 and add dilute K2Mn2O8 drop by drop. If it is decolorised, reducing power of the solution is indicated, and aeration may be necessary.
The percentage of extraction by cyanide may then be tried by passing solutions through the ore, washing thoroughly by filtration, and assaying the residues to find what quantities of the precious metals have been removed, checking the results by recovering the gold from the filtrate.
The consumption of cyanide may be determined by titrating the solution before and after use. In this way, the maximum extraction of gold and silver from an ore which has been crushed to different degrees of fineness, with solutions at different strengths, acting at various temperatures and for different lengths of time, may be determined. The best proportions of solution to ore may also be determined. Such data will be of great value in determining the degree of suitability of the process to any given ore, but the results obtained cannot usually be repeated on the large scale. Mechanical difficulties preclude fine crushing beyond a certain point; the relative amount of solution used in practice must be less than the large quantities giving the best results on a small scale. Moreover, the washing and filtering is more perfectly performed in the laboratory than in the mill, but, on the other hand, the consumption of cyanide may be less in the latter case than in the former.
We recommend tests on ore crushed to 10, 20, 30, 40, and 60-mesh size, with solutions of 0.01, 0.05, 0.1, 0.2, and 0.5 per cent, of KCy, amounting to 1, 1¼, 1½, 2, 3, and 4 A.T. of solution per A.T. of ore in successive washes, remaining in contact with the ore for 1, 2, 3, 4, 7, and 14 days.