Kaolin is an important industrial mineral having numerous uses and requiring various market specifications. High brightness kaolin clays represent a continuing challenge to the producer. An advancement in this field of Kaolinite Clay Beneficiation has been a patented process developed by Minerals and Chemicals Philipp Corporation and termed Ultra Flotation. Contaminants that are 1 micron and finer are separated from a feed which is virtually 100% finer than 3 microns and 48% finer than 0.5 microns. Removal of the contaminations by conventional froth flotation has never been commercially successful previously.
Ultra Flotation is a new concept of mineral separation that extends the flotation principle to the submicron range well beyond its present limits. The key to Ultraflotation is the increased surface available for floating fine particles by the addition of a suitable carrier mineral usually in the —325 mesh range. In conventional flotation air bubbles alone do the job. In Ultra Flotation the reagent loaded slime particles to be floated attach themselves to the carrier mineral and are readily floated as a froth product.
Production advantages are that the process uses conventional equipment and ordinary flotation reagents. Minerals such as calcite, fluorspar, silica, barite, sulphur, etc., are possible carriers.
The Flowsheet
The first step in processing kaolin clay is to slurry it in a blunger with water and a dispersing agent. Degritting using screens, cyclones and hydro-classifiers is the next step. The minus 325 mesh degritted clay is fractionated using centrifugal sizers to produce the fine fractions demanded by the various markets. Bleaching, filtering, and drying complete the general processing steps.
The flowsheet in this study follows the general steps outlined above but Ultraflotation is included to produce a high brightness product from the fine fraction. Bleaching alone will not produce the desired brightness.
The Ultraflotation feed (90-94% finer than 2 microns) is stored in a holding agitator and then pumped through a density and flow control apparatus to three Conditioners arranged in series. The mineral carrier (ground limestone, 200-400 lbs. per ton) and ammonium sulphate (4-8 lbs. per ton) are added to the first conditioner. The discharge from the final conditioner containing 20% solids is fed directly to a six cell High Energy Conditioner. An emulsion of tall oil (3-5 lbs. per ton), neutral calcium petronate (3-5 lbs. per ton), aqua ammonia (2-4 lbs. per ton), and water are added to the first cell of the high energy conditioner. The conditioned pulp has a pH of 9.0. Fuel oil (6-10 lbs. per ton) is added to the fourth conditioning cell.
A total of 24 “Sub-A” Flotation Machines (cell-to-cell design) are used for the flotation separation. The conditioned pulp is first floated in a six-cell machine and then this froth, which contains the mineral carrier and color contaminants, is successively refloated in stages using a six-cell machine for the first stage and four-cell machines for the second and third cleaning stages. Dilution water is added to each stage of flotation to maintain dilute pulp conditions. The rougher tailings and reflotation tailings are combined and scavenged of any additional contaminant in a 4-cell “Sub-A” Flotation Machine. The tailings from this final flotation step represents the beneficiated kaolin and is pumped to a thickener. Sulphurous acid is added to the pump to produce a pH of 2.8 to 3.0 for flocculation.
The froth products from the reflotation and scavenging steps are combined and impounded. The principal contaminant removed in the Ultraflotation process is a titaniferous mineral which does not bleach and imparts a yellowish-brown cast to the finished kaolin if present. Typical results of the Ultra-flotation separation are shown in the table.
In brief, the thickened kaolin from the thickener is bleached, filtered, dispersed and dried. The Ultra White 90 product is then shipped in bulk or bags or as a 70% slurry in tank cars.
The Fe2O3 content, which affects the brightness of the clays is controlled by careful mining and by the reducing bleach using zinc hydrosulphite. The ferric iron is reduced to the ferrous state and the slip washed to remove soluble salts.
In general, Ultraflotation enhances the brightness of the kaolin by more than 5%. By incorporating bleaching for additional color improvement, the beneficiated product (Ultra White 90) has a brightness of 90-92. Brightness is a measurement of light reflectance by a standard method of the Technical Association of the Pulp and Paper Industry.
PROPERTIES AND USES OF ULTRA WHITE 90 CLAY
Brightness (G.E. brightness range)…………………………………………………..90-92%
Particle size percent finer than 2 microns…………………………………………90-94%
Maximum screen residue wet, 325 mesh…………………………………………..0.005%
Refractive index…………………………………………………………………………….1.56%
Specific gravity………………………………………………………………………………2.58
pH range………………………………………………………………………………………6.3-7.0
Ultra White 90 is a pre-dispersed premium clay that has applications in the filling of high quality papers to reduce TiO2 requirement for brightness and in coatings for high brightness, easier finishing, gloss improvements and ink holdout. It is available in bulk, slurry, or bags and is produced by the Ultra-flotation process developed by Minerals & Chemicals Philipp Corporation.
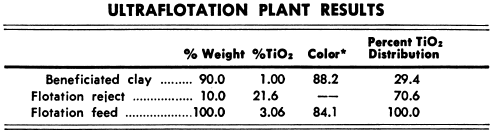
Source: This article is a reproduction of an excerpt of “In the Public Domain” documents held in 911Metallurgy Corp’s private library.
Kaolin Beneficiation
Kaolin clay is one of the yeoman minerals. It sees duty in almost every aspect of our lives:
-in and on most paper products (from modern newsprint to National Geographic and packaging board) sometimes as much as 25% (by weight) of the product, 40% of the tile (ceramic, rubber, and linoleum) you walk on, and 15% of the tires you ride on.
Kaolin’s status as a yeoman pigment arises from its versatility. It is white, inert, fine-grained, soft, and relatively abundant.
The most common origins of kaolin were from the alteration of such source minerals as feldspar, granite, and gneiss during the warm, wet environments between the early Tertiary (50 million years) and Cretaceous (135 million years) Eras. Kaolin is found in primary (or insitu) and secondary (sedimentary) sites on all continents.
The viable air-float producer has a customer list consisting 200-300 locations, each purchasing one or more of its 6-20 products. Product differentiation is by the type of crude as it is found in the ground, blending of these different crudes, and degrees of cleanliness.
The air-floaters primary tools are slicers, dryers, and mills of the either the roller-type or the impact-type, and a lean, aggressive management style. Most office-holders cover two-or three jobs, R&D is a part-time function at best, and routine high-capital activity (such as stripping and hauling) is contracted.
The typical water-washed operation has a capacity of + 1.0 million mTpA and employs +600 persons. It has a heavy commitment to R&D and customer service, especially on applications development. Its customer list would extend to 1000 locations for its +50 basic products.
Anxious to exploit a tightening supply and rising prices, usually all four majors will increase capacity. As a general “rule” all expansions are completed within the same 6-8 months – putting the industry, once again, back in over supply.
In the air-float segment, the chronic oversupply situation results from the relative ease of entry, with new players having added about 400,000 mTpA of new capacity in recent years, putting the air-floaters at almost 100% over-supply. Market and managerial skills have pushed most of the over-supply onto the new entrants, so they operate at less than 30% of their capacity. They in turn create tremendous pricing pressure which has the effect of shutting down the less provident air-floaters. In the last ten years, four producers have left the field, mostly those affiliated with water-washed producers.
By tacking on a calcination step at the end of the ultrafine product line, the price can be increased by ca. $200/mT for a cost of $70/mT plus $50/mT in depreciation. Calcination consists of finely deagglomerating the ultrafine product and roasting it at temperatures of between 1000°C and 1100°C. This is followed by another deagglomerating step to counter the formation of abrasive mullite or cristobolite generated locally in the process. In calcination of kaolin the water of hydration between the gibbsite and silica sheets is driven off, in effect generating two more air interfaces and thereby enhancing brightness a couple points and opacity.
Another current challenge to the kaolin industry has been the quality “movement.” Typically kaolin producers strived to attain threshold specifications i.e., specifications which required the brightest product or the lowest viscosity. This tended to produce consistency, mainly around a performance-ceiling. But today quality means reliability in meeting not only these requirements but also additional “arbitrary” specifications. They are “arbitrary” in the sense that they occur along the spectrum, not at the edges of the range. And the primary concern of the customer is a narrow consistency.