Density, if you recall is the ratio of ore to water and is measured as a percent of solids in the water. It will control the grind in two ways. It affects retention time and helps distribute the ore through-the mill so each piece of rock will come in contact with the surface of the rods. To maintain a proper balance between these two is critical. What water does is kind of provide a mode of transportation for the ore.
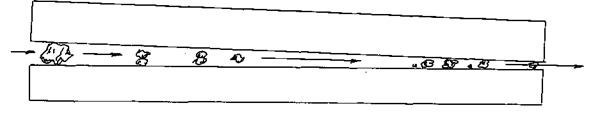
It works in this way, as the rock and the water enter the mill the water will wash the finer particles deeper into the mill leaving the coarse material at entrance of the rod load. As the larger rock begins to be ground they lift and separate the rods from one another leaving an open area for the fine material to flow along until it reaches a point where it must he ground. If there is too much water in the mill the water will wash the larger rock deeper into the mill separating the rods even further. This, of course, does not allow the fine material to come into contact with the surface of the rods so they can he ground. Remember what goes into a mill must come out at the same rate. So as you add water, it will be coming out of the mill at the same volume, earring the ore with it. If the rate of flow is too great the ore will not get the opportunity to be ground before all the fine material has been washed away. Soon there will only be the large and intermediate size of feed left in the mill.
Mill slurry characteristics affect grinding efficiency because of their influence on slurry rheology.
Slurry characteristics can be manipulated and tested to determine their effect on grinding efficiency. There are three mill slurry characteristics which you should note. The % fines in the rod mill feed. For the purposes of rod mill performance analysis, “fines” can be arbitrarily defined as particles finer than 75 microns (200 mesh). Rod mill feeds which contain less than approximately 10% fines are good candidates for fines addition testwork.
The % solids by volume of the rod mill discharge. Rod mill grinding efficiencies have been shown to increase in the range of 5 to 15% with more dilute discharge slurry (i.e., increased feed water) at least down to the range of 45 to 50% solids by volume. The higher the discharge % solids in the plant rod mill, the better the candidate for feed water addition rate test work.
The grinding action will not be good due to the poor cascade caused by a light density and a distinct possibility of equipment damage will be present.
Density is one of the major controls for the entire concentration process, in a mill it has a very positive effect on the manner in which the rods tumble and roll. This type of movement is where the rods obtain their grinding action. To understand the clues that the mill gives, as to how it is performing, it is necessary to know the movement of the rods in the mill and to understand how the performance is affected by different patterns of movement made by the grinding media.