Table of Contents
The correct sampling of ores is a subject of far greater importance than is usually conceded to it. Of the little which has been published on this subject, the recent paper, is the latest and best, and well worthy the careful perusal of all interested in accurate sampling, whether by hand or by machine.
It is doubtless true that thorough hand-sampling gives as good average results as can be obtained; but all hand-sampling is subject to the possible incompetence, carelessness, or dishonesty of the workmen employed. It is, moreover, tedious and expensive, requires large space, and usually entails considerable delay, both in unloading and in sampling. For these and other reasons, machine-sampling is now regarded with more favor than ever before.
So-called machine-sampling may be accomplished in two radically different ways:
- Part of the stream of material is taken for the whole time.
- The whole stream of material is taken for part of the time.
Under the first case the stream, as it issues from the delivery-spout of the crusher, is cut continuously in any given proportion, such as one-tenth, one-fourth, or one-half, by some fixed apparatus, which, as it contains no moving parts, is strictly speaking not a machine at all, but may be termed an appliance. The principle under which these appliances operate is now pretty generally conceded to be wrong, because of the practical impossibility of cutting such a stream continuously, in such a way as to obtain a proper proportion not only of the stream itself, but particularly of its “coarse” and “fine” parts. The leading exponents of this principle are the sampling-shovel and the pipe- or spout-sampler. The latter, which is the best instrument of its class, has the disadvantage of being very difficult to inspect and to clean; it is still in use in some places, but has been abandoned in others.
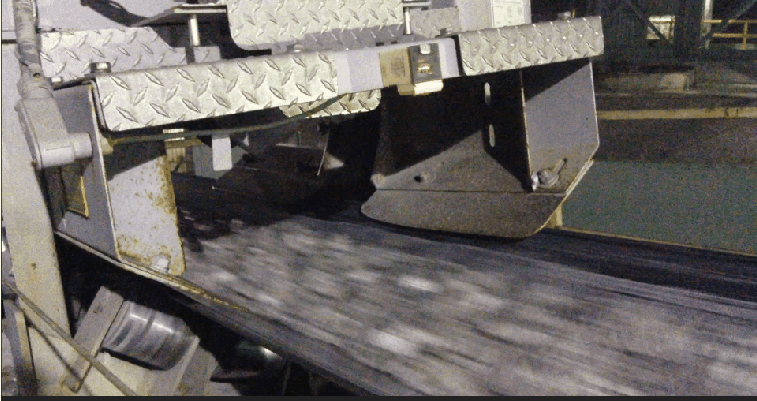
Under the second case, the stream is cut in such a way that the entire flow is diverted at certain stated intervals, yielding a sample in which both “coarse” and “fine” of the original lot are fairly represented. The samplers which effect this are the machines proper, and the best-known examples are perhaps the Collom and the Brunton, both of which have done excellent work.
In all sampling operations, whether by hand or machine, certain fundamental truths are recognized, the most important of which is doubtless the proposition that the more uniform the material sampled the truer will be the sample. Such uniformity may be natural (as in the case of solutions and of certain ores and products) or it may (and usually must) be produced by crushing and mixing. The finer the former and the more thorough the latter, the better the result. Some materials, carrying “ metallics,” horn-silver, etc., cannot thus be rendered uniform, and are particularly difficult to sample.
It is theoretically correct to precede each quartering or cutting- down by a crushing, coarse at first and finer with each succeeding cut. In practice, however, rarely more than two crushings are employed, and these are moderately fine, no matter how many cuts may be made. Some works screen their material as it is crushed, returning the “ coarse,” until all has been reduced to a certain maximum size. This is notably true of hard iron-ores. The writer believes this practice to be entirely wrong. The result of the screening is a more or less decided separation of the material into its component parts, as, for instance, into quartz and iron oxide, thus giving, not the desired more thorough mixture, but a practical undoing of the natural mixture already existing. Of course, re-mixing may be resorted to; but it would be preferable to crush the entire material once as fine as possible or as may be desirable, and then to sample it, permitting nothing to come between the crushing and the sampling. This latter point is always important, and hence sampling-machines should be set directly below the crushing-plant, thus avoiding much unnecessary cleaning and risk of “ salting ” subsequent samples.
The assertion that very wet ores can only be sampled by hand is an error. Anything that can be crashed can be sampled by a suitable machine, and material that is too wet to crash cannot be properly sampled, even by hand. Indeed, it is certain that crushing expense would be greatly reduced and better samples secured, whether by hand or machine, were the drying of original samples more frequently practiced than is at present the rule. The plant required is not particularly expensive, nor is much handling of the material necessary; while the heat to evaporate 10 per cent, of moisture from 100 tons of ore every 24 hours would be furnished by the exhaust- steam of a 60 or 70 horsepower engine.
Up to the present time no machine has been introduced which does more than the first portion of the work of sampling. It was the writer’s desire to remedy this deficiency by devising something which would give practically finished samples ; and the result of his efforts is the machine described in this paper.
Numerous designs were made, embodying the various possible combinations, and it is believed that the one adopted includes the best qualities of all; it is a rotary machine (as distinguished from an appliance) which takes the whole stream for part of the time, and which, in a single passage of the material through it:
- Gives two or more absolutely independent samples (double samples).
- Cuts down (quarters) each of these samples a sufficient number of times to give the smallest final samples desirable without re-crushing.
These two principal features are possessed by no other machine of this class, and are supplemented by the following hardly less important ones: - It is adjustable, to give different-sized samples, according to the grade and character of the material treated. The lower the grade, the more uniform the character, and the finer the size of the material, the smaller the final samples may be.
- All the passages being large and straight, its capacity is very great (from 15 to 25 tons an hour), and it will sample any material that can be fed to it. Ore carrying 10 per cent, and over of moisture offers no difficulties ; nor does the presence of strings, pieces of wood, and other extraneous substances affect the general result.
- The quickness with which the samples are obtained makes it possible to use the machine-samples for the determination of the moisture, as well as of the metallic and other constituents, which is, of course, a decided advantage.
- This quickness, moreover, makes it possible to sample all material as soon as received, with the consequent avoidance of demurrage on cars, and other expensive and annoying delays,
- The machine gives good results under any ordinary working conditions ; it takes its feed directly from crusher or rolls, regularly or irregularly, fast or slow, as the case may be; it requires no attention, except for cleaning out and for the removal of samples, and, in fact, it transfers the important function of sampling from the domain of watchful care and discretion to that of mere routine. Being perfectly impartial, and giving double samples, it removes ground for disputes, and renders “salting” practically impossible.
- It requires less than one-tenth as much space as hand-sampling, and delivers the discarded part of the sample in such a way that it can be disposed of by elevator or similar means, requiring no hand- labor.
- It is entirely self-contained, and very compact.
- It may be carefully and fully inspected while at work, without the necessity for the near approach of any person, so that the most suspicious ore-seller may easily assure himself of the fairness of the operation.
- It may be thoroughly cleaned by one man in 15 minutes or less, and, if desirable, may be washed out with a water-hose.
- It may be enclosed in a dust-case. This, however, is rarely necessary, as it is usually better slightly to moisten dry ores before crushing—these ores seldom requiring moisture-determinations. Should such moistening be undesirable, little harm can come of running the ore dry, as no men are about who can be injuriously affected, nor can the flying dust have any marked effect on the sample, and certainly not on any subsequent samples. Wet ores, of course, make little or no dust.
- It is very inexpensive, both to operate and to maintain, the total cost of sampling with this machine being only about one-tenth that of hand-work. It is provided everywhere with ball-bearings and graphite bushings, which require practically no lubrication (with its accompanying dirt and annoyance) and make it possible to run the machine with much less power than may be continuously exerted by one man. All parts exposed to wear are heavy, while ample provision is made for repairs, duplicate parts being readily obtainable.
- It is preferable to crush the material to 1 inch or less, but, if necessary, much coarser product may be run.
The intention has been to provide not only a first-class sampling- machine, but also a system which should give the machine its greatest effect by embracing all the sampling-operations, from the receipt of the material to the filling of the assay-bottles. To this end, the following machines and apparatus have been designed to meet the various requirements:
Size A. Sampling-Machine.—This gives double samples and three cuts (quarterings) on each sample. It is intended for original samples of any size, and gives final samples of 1 to 2 per cent, of the original weights. Its average capacity is about 20 tons an hour.
Size B, Sampling-Machine.—This gives a single sample and three cuts. It is intended for the smaller original samples and for work requiring only one sample, as, for instance, iron-ores and the various furnace supplies and products. It is also intended for use in cutting down the crushed final samples of the A machine. Its average rapacity is from 2 to 4 tons an hour.
Size C, Sampling-Machine.—This gives laboratory samples for all small work.
Mixer and Divider.—This performs the final preparation and distribution of the assay-samples.
Ore Sampling System A
This machine occupies a floor-space of 3 by 4 feet, and has a total height of 7 feet 6 inches. It is self-contained, requiring only to be bolted to the floor and to have feed-, discharge-, and belt-connections made. Fig. 1 shows the machine as it is built, while Figs. 2 and 3 give the diagraphic sections and details, some minor changes and omissions having been made for the sake of clearness. The machine consists essentially of three apportioned, I, II, and III, all driven by the one pulley, X (usually tight and loose pulleys), and three stationary, concentric receptacles, R1, R2, and H, so constructed that any material falling into them will pass out through the spouts T1 and T2 into the sample-buckets Z1 and Z2 or through the spout S, which discharges the rejected portion of the sample. Apportioned I and III revolve in the same direction, apportioner II in the opposite direction ; I at about 5, II at about 15, and III at about 45 revolutions a minute. That is to say, each apportioner moves actually three times as fast as the one above it, and in the contrary direction, or, relatively, four times as fast. By the use of this expedient of contrary revolution, the same relative speeds are obtained
as though, all revolving in the same direction, the actual speeds were respectively 5, 25, and 125, at which latter speed centrifugal force would become very troublesome.
The upper apportioner, I, consists of two concentric rings, divided by 8 partitions into 8 equal topless and bottomless compartments, L, from each one of which leads an adjustable spout, either as M-1, or as M-2, or as M-D. Set in rotation, spout M-1 would describe a certain circular path, 1-1; spout M-2 a certain other path, 2-2, and spout M—D a third path, W (see Fig. 3).
The intermediate apportioner, II, is merely a conical funnel, having, besides the large outlet W, four vertical shoots, N1-N1 and N2-N2, through its sloping sides, as shown in Fig. 3; each one of these shoots forms one-eighth of the circular paths covered by the spouts M-1 and M-2 respectively.
The lower apportioner III is of the same construction as II and bears the same relation to it that II bears to I.
An example will best illustrate the operation of the machine. It may be assumed that an original sample of 40,960 pounds (the 960 being added to avoid fractions) is to be put through the machine; that the time required will be one hour; that the speed of the machine is such that the upper apportioner, I, will make 320 revolutions in that time, and finally that the ore is of such grade and character as to only require the smallest sample that the machine will give. Under these conditions, one of the spouts, M, would be set as M-1, one (the opposite one) as M-2 and the remaining six as M-D (Fig. 2).
The machine would then be set in motion, and the flow of material, previously crushed to below one-inch in size, would be started through the feed-spout, F. The series of operations which would follow may be best understood by reference to the upper part of Fig. 5. This diagram, like other similar ones accompanying this paper, is drawn approximately to scale, as a graphic representation of the work done by the machine under the conditions stated.
It is evident that at each revolution one 320th part of the whole lot, or 128 pounds, will pass through the feed-spout, F. Of this amount six-eighths or 96 pounds will be discarded by the six spouts, M-D, passing down through W, W, H and so through the spout S and out of the machine, while one-eighth of the 128 pounds, or 16 pounds, forming the first cut of the first or outer sample, will pass through the spout M-1 and the remaining one-eighth, or 16 pounds, forming the first cut of the second or inner sample, through the spout, M-2.
These two first cuts will proceed side by side, by separate paths through the same series of operations, and whatever applies to the one, applies equally to the other; it will, therefore, suffice to follow
the first sample. This one-eighth or 16 pounds, having been cut from the mass by the partitions of the compartment L1 of which M-1 forms an extension, will drop nearly vertically through M-1 on its way to the sample box, Z1. As it leaves the spout, M-1, during the one-eighth of a revolution that is occupied by the said M-1 in passing beneath the feed-spout, F, it will be intercepted by the intermediate apportioner, II, which in the same time will have made one half-revolution (relatively to I).
Since the vertical shoot, N-1, occupies one-fourth of the semi-circumference of II passing beneath the spout, M-1, it follows that one-quarter of the 16 pounds, or 4 pounds, will drop vertically through this shoot as the second cut of the first sample. The remaining three-quarters, or 12 pounds, will pass down the sloping- sides of II and be discarded through W, W, H and S.
In precisely the same way the second cut of 4 pounds will be quartered by the lower apportioner, III, 3 pounds being discarded and 1 pound, as the third and final cut, passing through the vertical shoot P1 and the spout T1 into the sample bucket Z2.
In the same way a 1-pound portion, as the third cut of the second sample, will find its way to the bucket Z2.
This series of operations will occur at each revolution of the upper apportioner; and at the end of the hour each of the buckets Z1 and Z2 will contain 320 portions of 1 pound each, or a total final sample of 320 pounds, these two total samples being as independent of each other as though made at different times and places. It will of course rarely happen that this theoretical exactness of weights will obtain, which point will be considered later. Should the ore be of higher grade or more irregular in character, two or three or four of the spouts, M, may be set for each sample, giving final samples of 640, 960 and 1280 pounds respectively. The last case, in which nothing is discarded by the upper apportioner, is illustrated on the upper part of Fig. 6.
It will be noticed that only the discarded part of the sample is touched by the machine, the retained portions dropping nearly vertically and practically freely through the machine, until, in a finished condition, they reach the stationary receptacles R1 and R2 or the sample-buckets Z1 and Z2. The machine can have had, therefore, no influence on the constitution of the samples, and “ coarse ” and “fine” must be contained therein in the same proportion as delivered by the feed-spout, F.
It may be remarked in passing that the finer the material, the slower the feed and the greater the speed of the machine, the greater will be the distribution and presumably the better the samples. The conditions above given, however, are easily attained, depending only on the crushing-capacity at disposal, and have been found by experience to give satisfactory results, it being particularly desirable not to use a much higher speed. For light or wet ores it may be
necessary, in order to avoid an accumulation of material in the machine, to reduce the speed to half that given. This lower speed may of course be used for heavy materials also, the only practical difference between the higher and lower speeds (aside from the influence of centrifugal force) being the difference in the number of cuts made by the machine.
Ore Sampling System B
This machine occupies a floor-space of about 18 inches square, with a total height of about 36 inches. Being designed for cutting down the fine-crushed final samples from machine A, it gives but a single sample; but is otherwise similar in construction and operation to the large machine. The machine itself is shown in Fig. 4, its operation being graphically illustrated on the lower portions of Figs. 5 and 6.
For the sake of comparison, a graphic illustration of hand-sampling is given in Fig. 7, which, like Figs. 5 and 6, shows an original sample of 40,960 pounds, cut down to two (duplicate) samples of 320 pounds each ; these, after fine-crushing, being further reduced to final samples of 10 pounds each. These diagrams fully explain themselves, and no remarks are necessary, except to call attention to the very much greater number of cuts given by the machine than by hand, amounting for Fig. 5 to 320 x 3 + 4 x 3 = 972 cuts, and for Fig. 6 to 320 x 4 x 3 + 3 = 3843 cuts; while Fig. 7 shows only 7 + 5 = 12 cuts.
Figs. 8 to 13, which further illustrate hand-sampling, fairly represent good practice. Fig 8 shows the first finished pile, containing the entire original sample, and also illustrates the method of delivering each shovelful of ore in such a way as to distribute it evenly over the entire surface of the cone. To do this successfully requires some skill; the material must not be thrown as in ordinary work, but must be tossed vertically into the air, so that it will fall squarely upon the apex and spread uniformly over the pile. Figs. 9 and 12 show the pile partially spread out, and the manner in which this is accomplished; Fig. 11, the pile completely spread out; and Fig. 10 the same pile, with the two discarded quarters removed. Figs. 12 and 13 together, indicate the manner of beginning a new pile.
Ore Sampling System C
THE LABORATORY SAMPLER
This machine occupies a space some 14 inches square, and about 14 inches in height. It was designed for cutting down the ground
final samples of the B machine, and for the sampling of the many small lots of material weighing from 20 to 500 pounds that are constantly being received by most assay-offices. Its operation is as follows (reference being made to Fig. 15):
The material is fed either by hand, or (with large lots) from a suitably supported bucket, into the funnel, F, the divider, D, being first set in rotation by hand, clock work or any convenient power. The divider gives, as will be seen by inspection of the drawing, eight cuts to the revolution, four being delivered to the funnel 1, and four to the receptacle 2; that is, with uniform flow and speed, it cuts the material in half. The divider may easily run 100 revolutions per minute, giving in that time 800 cuts, a very much greater distribution and division than can be secured in any other way. The rejected sample passes down the outlet, O2, the retained portion through the outlet, both into suitable vessels. The retained portion, should it be too large, may be cut again and again, until of suitable size. The operation is very accurate and very rapid, being about as fast as the material will flow through a one-inch spout, and very much faster than is possible with hand-work or with sampling- tin, and of course not nearly as tiresome or expensive.
SAMPLE MIXER & DIVIDER
This apparatus, illustrated in Fig. 16, entirely obviates the tedious and often inaccurate methods (usually with oil-cloth and spatula) now in use, for mining and dividing the ground samples of ore, matte, slag and similar materials. An experience of several months has shown a decided improvement in accuracy, speed, and general convenience over the old way, the saving in time amounting to fully two-thirds. The operation is as follows :
The ground material is introduced into the large covered funnel (mixer), the outlet being first closed by thumb or finger as may be most convenient. Funnel and contents are well shaken for a few moments, and then, with opened outlet, passed to and fro over the set of distributing funnels (divider) and bottles as shown. With very finely ground or very light material the flow may be assisted by a slight shaking or tapping with the hand. The little skill necessary is readily acquired.
To test the efficiency of the mixer, a lot of 6 assay-tons of litharge, 3 assay-tons of soda and three-quarters assay-ton of argol (9¾ assay-tons altogether) was taken, well shaken, and divided by weight into three
lots of 3¼ assay-tons each, and these charges were fused separately in crucibles. The resulting lead buttons weighed 53.436, 53.416,53.398 grammes, which result should be conclusive as to the thoroughness of the mixing.
DO Automatic MILL FEED SAMPLERS WORK
Having considered these various devices as parts of a general system of ore-sampling, it may be well to return to the investigation of the large machine, paying particular attention to the results obtained. That it is theoretically possible to do good work with this machine may be taken for granted; but actual use must demonstrate that it will operate satisfactorily under any ordinary working conditions. Let the records show what it has done.
The first machine built, and so far the only one, has now been in operation, at the works of which the writer has charge, for something over a year. It is set below, and takes its feed directly from, a No. 2 Gates crusher, whose capacity, large as it is, is very much less than that of the sampler. The product of this crusher will not exceed three-fourths inch ring-gauge in size. No attempt whatever is made to secure any special regularity of flow, the man at the crusher feeding as may be most convenient for himself. The discarded portion of the sample is removed by bucket-elevator to storage-bins, the two final,samples (of 200 to 500 pounds each) alone remaining for further handling. These final samples are often obtained within half an hour after the last of the material is out of the car. They should be crushed to one-quarter inch or one-eighth inch ring-gauge and run through the smaller sampler. Having, however, heretofore had neither fine crusher nor small sampler, we have merely quartered them down by hand to, say, 20 pounds, passed them through a laboratory crusher, cut them down again with sampling-tin and “ bucked” them; the ground material being finally mixed and distributed by means of the mixer and divider previously described.
Prior to the introduction of this machine, our works had treated 54 car-load lots (about 30,000 pounds each) of copper matte, on which double samples were made by hand. The average assay-contents of these 54 lots were: 7.88 ounces gold; 168 71 ounces silver; 55.24 per cent, copper. The average differences between the two samples of each lot were 0.43 ounce gold; 3.77 ounces silver; 0.71 per cent, copper.
Since the introduction of the machine, 22 lots of ore and 138 lots of matte have been run, the latter being of the same general character as the hand-sampled matte, except that it did not, as a rule, carry so much “ metallics.” By reason of these “ metallics ” much
of this matte was very difficult to sample accurately, as will be easily understood. The weights of these 160 lots varied from 65 pounds to 42,000 pounds, averaging not less than 30,000 pounds.
Their average assay-contents were 0.71 ounce gold; 112.04 ounces silver; 51.75 per cent, copper.
The average differences between the two samples of each lot were 0.02 ounce gold ; 1.19 ounces silver; 0.23 per cent, copper.
Reduced to percentages for the sake of comparison we find the average differences as follows :
Certainly a creditable showing for the machine. The high percentage differences in the gold are accounted for by the multiplication of the inevitable error in weighing such small quantities.
In all of this work the upper apportioner was set to take one-eighth of the entire material for each sample, or one-eighth by one-fourth by one-fourth,equal to one one-hundred-and-twenty-eighth,for each of the final samples. Had the machine operated as intended, each of the latter should have weighed, for a 40,000-pound lot, 312½ pounds. Such exact results, however, are very rarely attained, as will be seen from the following weights of the two samples from 40,000-pound lots. This list was taken at random, and is believed to be fairly representative:
It will be noticed that sometimes one sample is the larger and sometimes the other.
Within about these limits, there seems to be no regularity in the weight of the samples; generally speaking, however, the two samples, be they heavy or light, do not vary greatly from each other. Some of the samples show as great a difference in weight as 250 pounds, which, compared with the weight of the samples themselves, is very large; compared, however, with the weight of the original
sample, say 40,000 pounds, it may be practically neglected. As frequently demonstrated by observation, it is certain that each time the sample shoots of the three apportioned come into proper position with relation to each other (that is, each time they line up as explained in the description of the machine), a portion of the material under treatment drops into one or the other of the sample- buckets, as the case may be. This portion will seldom be exactly the calculated quantity, but it will nevertheless be a practical sample of a small part of the entire lot, and consequently the total of these small samples will give a practical sample of the entire lot itself, whether the weights are theoretically correct or not.
When, therefore, there are two absolutely independent samples of this character, it is believed that an insight into the composition of the material is obtained that is possible in no other way. It may be remarked, in passing, that with hand-sampling the same number of cuts on each sample will give final samples with as great average differences in weight as are given by the machine. One cause for this irregularity in weight of the machine-samples is doubtless the lack of uniformity in the feed, this being particularly the case when the samples vary between themselves and when they weigh less than the theoretical quantity. The principal cause is less apparent, and is believed to be due to the manner of flow of the crushed material, as is explained by the following considerations.
In passing through the machine, the material may be conceived:
- As a shower of particles, nearly uniform in size, and completely filling the space. In this case the upper apportioner would take one-eighth, the intermediate apportioner one-fourth of the one- eighth, and the lower apportioner one-fourth of the one-fourth. That is, the machine would operate as intended, and each final sample from a 40,000-pound lot would weigh 312½ pounds.
- As concentrated into a single vertical line for each sample. In this case the speed-relations of the three apportioners with reference to each other would cease to be of influence. For instance, the upper apportioner makes 5 revolutions in one direction, while the intermediate apportioner makes 15 revolutions in the other; that is to say, moves relatively four times as fast, and, under the first case, one-fourth of the “ shower of particles ” which passes through the sample-shoot of the upper apportioner would be cut out by the sample-shoot of the intermediate apportioner. Under the second case, the “ line of concentration ” would be cut one-eighth by the upper apportioner, and this one-eighth would be cut one-third by the intermediate apportioner, exactly as though the upper appor-
tioner revolved in the same direction as the intermediate, and one-third as fast (that is, as 5 to 15). Under the first case, the motion of the upper apportioner influences the manner in which the stream is cut by the intermediate apportioner. Under the second case, it does not; and so far as the cutting of that portion of the stream which reaches the intermediate apportioner is concerned, the upper apportioner might as well not exist. The same reasoning would apply to the lower apportioner, and we would have for the cuts under this second case one-eighth by one-third by one-third, equal to one-seventy-second ; that is, each sample from a 40,000-pound lot would weigh 556 pounds.
In practice, the action of the material would lie somewhere between these two extremes, generally more nearly approaching the former. It is believed that a large share of the variation in weights is due to this cause.
It is obvious, however, that in either case a practically true sample would result, so that this whole question has little or no practical importance.
As showing the general adaptability of the machine, two extreme cases may be given :
I. As a test of capacity, 42,000 pounds of 50 per cent, copper matte, after preliminary crushing, was fed by hand directly to the machine, requiring the steady work of three good shovelers. The entire lot was put through in 66 minutes, the resulting samples weighing 501 and 300 pounds respectively.
II. 9900 pounds of oxidized copper-ore, carrying about 50 per cent, of copper and 7.5 per cent, of moisture (wet enough to ball in the hand), was fed directly from the crusher in 8 hours (as fast as the crusher could work, on account of the character of the ore), the resulting samples weighing 117 and 110 pounds.
In both cases the assay-results were satisfactory. From the above statements it will be recognized that in the somewhat varied and often difficult conditions under which this machine has heretofore worked, it has at least equalled in accuracy the best of hand-sampling, which is the accepted standard everywhere.
What it will do with the innumerable kinds and grades of ores and other products which form by far the larger portion of material subjected to sampling, is of course not definitely known at present. It is fair, however, to judge of the possibilities of the future by the performance of the past, and to state the general belief that, with any material that can be crushed (being neither too wet nor too metallic), or that is fine enough to need no crushing, the machine will give results equal in accuracy to any hand sampling at a small fraction of the expense, and in very much less time.
Nor must the fact be overlooked that the double samples, furnished without extra expense by the machine, offer an excellent safeguard against “salting” and against errors of every kind. The practical impossibility of “salting” the samples from this machine is shown by the fact that both samples would have to be salted alike, and as the weights of the two are never exactly the same, any attempt of the kind would be almost certain to result in detection. Moreover,
the result is obtained so quickly that it is easy to control any possible difference, either of fraud or of error, by re-sampling the lot while it is still intact.
It may be objected to the double samples that they increase the assay-work. This may be true, and if true should not be deemed a drawback, since the accuracy of results is increased in the same proportion. But it will not necessarily increase the work, for a single assay on each one of the two samples is certainly far better than a duplicate assay on only one sample. With proper appliances, as indicated in this paper, the extra labor in preparing the samples is very small.
In computing the relative cost of sampling with this machine and by hand, it is best to begin with the ore as it issues from the crusher, and to end with the delivery of the crushed and sampled material into its appropriate bin.
In the latter case, this delivery must be accomplished almost entirely by hand-labor (generally with wheel-barrows), while with machine-sampling it is done almost entirely by elevators or conveyors.
The large machine will readily handle 20 tons of material an hour, and it may be assumed that, for each lot of this size, the man in charge will require another hour to clean the machine and to run the samples through the small machine to their final size.
The expense for the two hours would be:
This has been shown by experience to be a very liberal estimate. Power and lubrication cost much less than is charged, while the wear resulting from a year’s work of the existing machine is practically nothing, although in this first machine all the parts are much lighter than in the ones now building. Moreover, the entire time of the man has been charged to sampling, whereas it is perfectly feasible to have him feed the crusher or do other work; in short, one man is sufficient to do all of the actual sampling-work of a mill handling not over 100 tons of sample or, say, 500 to 1000 tons of ore a day.
For the hand-sampling of 20 tons (of Original sample) there would be required at least:
This expense should give double samples. For a single sample the cost would be :
That is, the machine delivers double samples at one-seventh the cost of single samples by hand, or at one-tenth the cost of double samples by hand. Nor does this saving, large as it is, by any means represent the total gain from the use of this machine, for the numerous advantages elsewhere enumerated undoubtedly lead to important reductions of expense that are not so readily determinable. To all of which is added the satisfaction of always knowing exactly what is being done, and the additional satisfaction of knowing it promptly.
For the hand-sampling of 100 tons of original sample a day, a floor-space of at least 2000 square feet would be required, while for machine-sampling not over 200 square feet is necessary. An inspection of Fig. 14 will give an idea of the possibilities in this direction, a properly constructed works being there shown in elevation and ground-plan. An equally efficient plan may be made for level ground by arranging to deliver the entire sample from either the large car, F, or the small car, Q, directly to the crusher, which, with its rolls, should be set above the sampler if practicable. This arrangement avoids the necessity for bucket-elevators between the crushing-machinery and the sampler, thereby doing away with a great deal of vexatious cleaning and of risk.
Where it is not possible, to escape this use of elevators, the writer has designed a special construction in which both cleaning and risk are reduced to a minimum. The railroad car, F (Fig. 14), after passing the scales, X, is unloaded into any one of the bins, D, of which there may be any number. As the unloading proceeds, the portion required for sample (be it one-tenth or one-fifth or the entire lot) is delivered through troughs, S, which are located between each two bins, D, into one or more cars, Q, which, in turn, deliver into the hopper, B1. From B1 the material passes the crusher, C, the rolls, R, and the large sampler, H, the discarded portion (all but a few hundred pounds) passing into the elevator, E, and thence by cars, M, to the same bin as the rest of the lot, or to any other desired point. The samples in the buckets 1 and 2, weighing but a few hundred pounds each, are elevated by chain-tackle to the tilting- frame, T, whence they pass through the hopper, B3, the fine rolls, O, and the small sampler, N, the discarded portion going to the elevator, E, and the final samples, of a few pounds each, to the sample grinder, G, and thence to the assay-office.
Such a plant will secure not only the greatest economy, but also the greatest security from errors and from malicious interference with the samples.
As showing the adaptability of these machines, it may be mentioned that one of the largest smelting-works on this continent is now putting in a set of three, two large and one small. The entire sampling-plant is to be located adjacent to the main engine, the machines themselves being in a room excavated below the level of the crusher-floor. An ordinary sampling-floor could not have been so located by reason of the room required, and would have required, moreover, an independent engine. This saving in building and machinery will probably more than equal the entire cost of the sampling machinery. Either one of the large machines would be abundantly sufficient for all the work ; but two are to be employed, one for oxide and the other for sulphide ores, it being desirable to keep these two classes of material entirely separate, and cheaper to employ two machines than to do the transportation and handling which would otherwise be necessary.
In conclusion, it may be emphasized that this machine is no longer an experiment. Its record of over one million dollars’ worth of material purchased entirely on its samples, and from men who would tolerate no loose work, places it fairly in the category of accomplished facts.