Table of Contents
Apron Feeders must always be employed to ensure that the feed to a crushing machine is drawn at a constant rate from the bin which serves it. Of the many designs in existence by far the most widely used are the apron and pan feeders, although the Ross Chain Feeder is coming into favour for handling coarse ore.
Aggregate production plants have components such as feeders and scalping units to direct material to be crushed, separated, or stored for later use. Feeders are used mainly to handle input material for the plant. They are of two types: the apron feeders and mechanical, or reciprocating-plate, feeders.
Apron feeders or grizzlies are generally used to feed quarry rock into a primary crusher. They are of a heavy-duty construction to take the shock from rocks dumped directly on them. To cushion the blow of material dumped on the feeder, a large hopper may be used to receive the dumped loads. The apron feeder consists of a series of overlapping pans or plates which form a continuous chain like a conveyor belt. They are generally installed on a slight decline and driven to throw material in the downward direction. Widths of feeders range from one to 15 ft and lengths vary from one (for the largest) to five times their width. Feeders are driven by less than one horsepower up to 40-hp motors, depending on feeder size and expected load.
The main point to consider in selecting a feeder is that it must provide an even flow of material to the primary crusher. The size of the feeder and its speed should provide a capacity 25-35% greater than the capacity of the crusher. It may be necessary to provide for hand Controls to regulate the feeder in the case of irregular dumping of the raw material.
Apron Feeders
The Industrial Apron Feeder is the ‘best of breed feeder’. Earlier I made a statement that feeders are stationary while the rock moves. There is a saying that there is an exception for every rule and this could be classed as that exception. An apron feeder is in fact a conveyor that is constructed from metal. It regulates the feed by carrying the ore to the delivery point at a controlled rate of speed.
The face of the conveyor is made from heavy armour plating, and works like the track on a crawler type tractor.
Due to this type of construction it is able to withstand high impact from large ore. This, coupled to the fact that the feeder can have a very large entrance opening, makes it a good choice to he put under stockpiles and equipment where the ore may have a long fall before it enters the feeder.
While the conveyor portion of the Apron feeder doesn’t have a high wear factor from abrasion, the sides, entry and exit points still do. These will have to be maintained.
Another problem associated with this type of feeder is that it doesn’t handle very fine material well. Dust will require special consideration in the design of the equipment, possibly a dust chute prior to the feeder or an easily accessible clean up area to handle spillage as it occurs.
The apron feeder illustrated in Fig. 2 consists of an endless belt made up of flat overlapping steel plates. The line of plates is carried on two roller chains, one on each side, the links of which are of the same length as the plates. Sometimes the inner links of each line of chains are made of angle steel, to which the plates can be bolted, or else lengths of angle are riveted to both sides of the plates and bolted to the corresponding inner links. Each link pin carries a flanged roller ; these run on two lines of rails, and at each end of their travel they pass over head and tail sprockets, the former being driven and the latter running free. Thus the chains take the strain of the drive and the plates have only to carry the weight of the ore. The ends of the plates are curved and fit into each other to prevent leakage through the joints, especially at the point where they begin to turn over the head sprocket. Instead of joining separate links with a separate pin it is common practice to use one long bolt to connect consecutive links on one chain with the corresponding set on the other ; this helps to stiffen the feeder as a whole.
It is preferable to drive each feeder with its own motor, which should be connected with the head sprocket through some device for varying the speed. The maximum linear speed of the plates is seldom required to exceed 20 ft. per minute.
The feeder is usually installed under an opening in the bottom of the bin and takes the weight of the column of ore resting on it. The plates, as they travel forward, draw out a continuous stream of ore, which is discharged as they turn over the head sprocket. The depth of the ore stream can be regulated by an adjustable gate placed immediately in front of the opening in the bin, but the clearance between the bottom edge of the gate and the plates must always be sufficient to allow passage of the largest lump likely to be encountered. If too much ore is being delivered when the gate is in its lowest allowable position, the quantity can be reduced to the required amount by adjustment of the speed regulator.
The apron type of feeder is not suitable if it has to work at an inclination greater than 15°, at which angle the ore will slip back down the slope. The pan feeder is designed to meet this contingency. It is constructed in the same way as the apron feeder except that the plates are recessed in the form of a pan, the depth of which varies according to requirements. Both types are made for normal purposes in widths from 24 to 60 in. and in lengths from 6 to 12 ft., and both dimensions can be increased, should conditions demand a larger size. They are suitable for ore of any size down to ¼ in., but below this size leakage through the joints becomes excessive and a belt feeder is preferable.
An apron or pan conveyor is sometimes substituted for a belt conveyor for very heavy duty. Its construction is the same as that of a feeder except that it is usually longer, and it is driven at a fixed speed which does not as a rule exceed 50 ft. per minute.
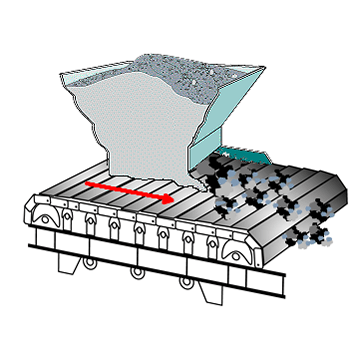
Apron feeder capacity formula:
T = 5 wds/c
where : T = tons of ore per hour,
w = effective width of feeder in feet,
d = depth of the layer of ore in inches,
s = speed of feeder in feet per minute,
c = number of cubic feet of broken ore per ton.
By giving d and s their maximum and minimum values the range of the feed rate can be obtained. The formula holds good for a pan feeder or conveyor if d is assumed to be the average depth of the layer of ore.
Traylor Apron Feeder And Jaw Crusher
A jaw crusher fed with an Apron feeder will increase capacity upto 40% by eliminating bridging and supplying a steady even feed.
Photo shows shop assembly of a 24” x 36” Traylor Type M Jaw Crusher and a 36” x 12’-0” Traylor All-Steel Heavy Duty Apron Feeder.
The Type M Crusher is built with a 50,000 pound TENSILE STRENGTH Meehanite Frame, with pitman shaft bearings fitted with removable water-cooled babbitted brushings; Cast Steel Swing Jaw and Pitman; Patented Swing Jaw Suspension fitted with removable bushings with greatly increased bearing area; and Manganese steel patented smooth face Curved Jaw Plates, which increase life of wearing plates up to 100% over Straight Crushing Plates and allow for finer settings. Write us for appointment to talk over this Crusher and Feeder Combination with you.
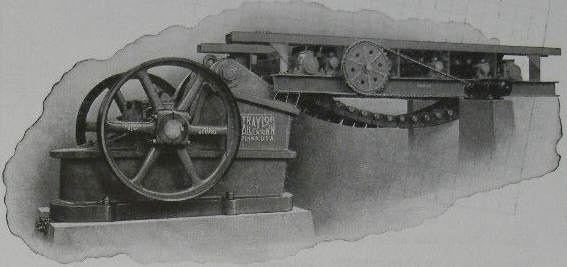
METSO Apron Feeder with Hagglunds Hydraulic Drive
For sale this Apron Feeder UNUSED (NOT USED) + Zero Leadtime…
All components are ready to be installed from their original packaging / crates
- Metso “World Class Series”
- Model: AF5-60MN-16.4-30HP
- Size: 5′ x 16′
- Brochure:
- Weight: 27,000 lbs
Hydraulic Motor
- Hagglunds (Bosch Rexroth) Severe-Duty, Direct-Drive
- Model: MB-283
- Torque Arm with S28—07033 Pivot Attachment
- (Prepared for long-term storage… Filled with Shell Tellus-68 w/ 5% Veto Anti-Rust Concentrate)
- Hagglunds MB-Series Hydraulic Motor Manual:
Hydraulic Power Unit Module
- Hagglunds (Bosch Rexroth) PBC Series
- Model: PBC-200-2.44-030-24-0011-01B-0000-0-460/60
- 30 Horsepower (480V – 60Hz)
- (Prepared for long-term storage… Filled with Shell Tellus-68 w/ 5% Veto Anti-Rust Concentrate)
Control Panel
- Hägglunds Spider 2 Control, Full Function
- Enclosure: NEMA 4,
- Size: 20 x 24 x 10
- Spider Control Brochure:
- Spider Control Manual:
The Hagglunds Hydraulic Power Unit Module is driving a torque arm mounted Hagglunds Hydraulic motor mounted direct on the headshaft of the Metso Apron Feeder.
The tractor-type apron feeder remains the preferred design throughout the world.
With over 125 years of combined experience in the application, engineering and manufacturing of heavy-duty apron feeders, Metso is truly the worldwide leader in the supply of this equipment. This is Metso’s “world class” apron feeder (which combines the best features of NICO apron feeder and Stephens-Adamson’s apron feeder), you will get the most rugged and reliable machine available for your operation.
Metso’s World-Class apron feeder is not a new design. As the originator of the crawler tractor-type apron feeder, Metso’s NICO® and Stephens-Adamson® brands have joined forces to combine the best features of their respective feeder designs. The result is a rugged and reliable tractor-type feeder that remains the preferred design throughout the world. Benefits of the Metso World-Class Apron Feeder put it in a class by itself. Metso offers a robust design with an intense commitment to quality and attention to detail. The main benefit to the end user is ruggedness and dependability for heavy-duty operations. The bottom line: reduced operating downtime and lower overall cost.
Recognized and respected around the world.
- Devours large lumps of abrasive and hard rock ores
- Protects downstream crushers, grizzlies and conveyors
- Handles severe impact conditions
- Prevents material choking
- Feeds at uniform rate
- Requires nominal maintenance
- Available parts inventory
- Primary, Secondary & Tertiary applications