In the history of crushers, both chronologically, and by virtue of its standing in the field of heavy-duty crushing, the Blake jaw crusher stands first in the list. All of the large, heavy-duty primary crushers of the jaw type are built around the Blake principle which, for simplicity and brute strength, is unsurpassed by any mechanism thus far devised for rock and ore breaking.
A sectional view of a jaw crusher which incorporates the Blake double-toggle mechanism is shown below. The Blake crusher in common with all machines of the jaw family is built into a rectangular frame, at one end of which is located the crushing chamber; in fact, the end of the box-frame constitutes the stationary jaw. The movable or swing jaw is suspended from a cross-shaft (swing jaw shaft) at its upper end, this shaft in turn being supported at each end in bearings at the top of the two sides of the crusher frame.
The actuating mechanism consists of the eccentric-shaft (also supported in bearings in the sides of the frame), the pitman, and the pair of toggles, which span from swing jaw to pit-man, and from pitman to rear end of the frame. The motion of the eccentric-shaft is transmitted through the pitman to the inner ends of the toggle pair, and through their action to the lower end of the swing jaw, which pivots around the supporting shaft at its upper end. The motion is similar in one respect to that of the standard gyratory crusher, in that it is greatest at the discharge opening, and gradually decreases toward the upper part of the chamber.
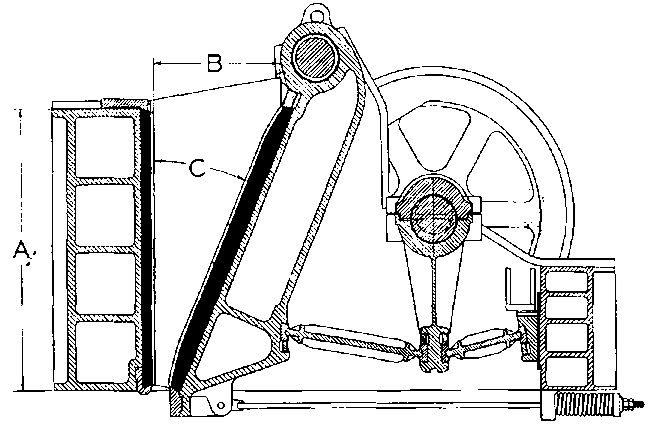
The Blake Jaw crusher frames have been the subject of considerable variety in details of design and have been built of several different materials. Originally all frames were of cast iron, as was the case with all of the early gyratory machines. Then, as larger sizes were developed, cast steel became the common medium for all large and medium size crushers. When the Superior line was designed, semi-steel was selected for the frame, and steel rods extending through the side members from end to end were provided to absorb the tensile stresses. This type of construction is used in all sizes of this line, except in the 84″ machines, where cast steel has been used exclusively up to the present time, these cast-steel frames being reinforced for heavy-duty applications in the same manner as the semi-steel frames of the smaller machines. Of recent years the trend has been very definitely toward the use of welded design, with side members of rolled steel plate, reinforced by stiffening ribs.
In past years both chilled cast iron and manganese steel were used in jaw plates for the Blake crusher, depending upon the kind of rock to be crushed. The chilled iron plates did not possess the requisite strength to resist breakage, even when used on comparatively soft rock; in our case we have abandoned them in favor of manganese steel on all of our jaw crushers, regardless of size.
This crusher is representative, in its general proportions, of the prevailing practice in Blake crusher design for a number of years. In this respect it is probably just as well entitled to be classed as a “standard” type as the gyratory crusher which goes by that title. ‘It is true that refinements have been made in almost every detail, as compared to early models, but the basic action and the general proportions of the crushing chamber are much the same.
As a matter of fact, aside from these refinements in mechanical details, the only important departures from the original Blake design that had been tried, until quite recently, consisted of:
- alterations in the relative positions of stationary and swing jaws with respect to the vertical;
- the introduction of curved (non-choking) jaw plates.
The original Blake crusher was designed with a vertical stationary jaw. Probably the first departure from this arrangement was an 84 X 66″ crusher, built in 1914. This machine conventional design, in that the swing jaw was made vertical. Later, when the Superior line was developed, a compromise between these two extremes was used in several of the sizes; that is, both jaws were sloped. Each of these three arrangements has certain features which are advantageous, and others which are unfavorable. Present indications are that the original arrangement, with vertical stationary jaw, will continue to hold a leading position.
Crushing angles in standard Blake-Type machines generally run in the neighborhood of 27 deg, at the minimum open-side discharge setting. The ratio-of-reduction at minimum recommended settings and with straight jaw plates average about 8:1, in the range of sizes from 15- x 10-in., to 60- x 48-in,, inclusive.
Allis Chalmers Machinery Booklet