Table of Contents
- Barite Beneficiation Flowsheet
- Barite Ore Crushing Section
- Grinding and Barite Flotation Section
- Barite-Fluorspar-Zinc Beneficiation Plant
- Barite-Fluorspar-Zinc Ore Crushing
- Barite-Fluorspar-Zinc Ore Grinding
- Barite Flotation
- Fluorspar Flotation
- Barite Thickening and Filtration
- Barite Beneficiation Process
- Mining Methods Barite Recovery
Barite (barium sulphate) often occurs as large veins or beds, as gangue mineral in various mineral veins, in limestones, sandstones and like deposits. The ores are generally low grade and require concentration by flotation to meet market specifications.
Barite, which has the ability to influence other materials with its basic characteristics, makes this heavy spar indispensable in maintaining the high specifications and uniform viscosity needed in all rotary drilling fluids. The Barite Beneficiation Process is one of flotation, it is used as an ingredient in “heavy mud” for oil-well drilling, for which purpose specifications demand a material meeting the drilling “mud” specifications.
- Fineness: 98% finished product must pass through 200 mesh. (90-95 % will pass through 325 mesh screen.)
- Specific Gravity: required is 4.3 or better. This product contains 90% or more BaSO4.
- Viscosity: Maximum viscosity allowed is 60 Centipoise. The usual weight is 16 lbs./gal. on the mud scale.
Barite Beneficiation Flowsheet
Wet grind the material to final fineness requires (less than 5% plus 324 mesh), liberating the mineral from the gangue; then concentrate by means of flotation to obtain the purity.
Barite Ore Crushing Section
Crush enough ore in 8 to 10 hours for 24-hour operation. The ore is dumped over a 10″ grizzly ahead of the coarse ore bin to control size pieces handled by the crusher. The rugged 36″x 10′ Apron Ore Feeder, especially designed for the severe service under the feed hopper, has a variable speed drive for controlling the feed to the jaw crusher, thus assuring maximum crushing efficiency.
A 2′ wide by 6′ long Shaking Grizzly is operated from the eccentricity of the jaw crusher bumper. The grizzly set at a slope of 15-20° from horizontal saves headroom and with 1.5″ clear openings eliminates the undersize; while oversize material goes to a 15″ x 24″ Jaw Crusher, which reduces the 10″ pieces to approximately 1.5″.
A permanent magnet head pulley on the conveyor removes tramp iron present in the ore.
A 3’x6′ Single Deck Vibrating Screen removes the minus fraction from the feed of the 30″ cone-type secondary crusher.
Grinding and Barite Flotation Section
Crude ore is drawn from the fine ore bin by means of a 24″ x 14′ Adjustable Stroke Belt Ore Feeder and reduced to 100-150 mesh in a 6’x12′ Steel Head Ball Mill, charged with 3″, 2.5″, 2″ and 1 diameter balls.
The ball mill discharge and spiral screen undersize is classified at approximately 100-150 mesh separation in a 48″ x 26′-9″ Crossflow Classifier. The classifier sands are returned to the ball mill, while the overflow is pumped by a 3″x3″ SRL Rubber Lined Sand Pump to a 12′ diameter Hydroclassifier for final separation ahead of flotation.
The -200 mesh fraction at approximately 20% solids overflows the Hydroclassifier and flows by gravity to the Super Agitator and Conditioner.
The coarse fraction settles, is raked to center discharge cone of hydroclassifier and removed with a 4″ Duplex Adjustable Stroke Diaphragm Pump. (The adjustable feature on the classifier acts as a control on the size material overflow.) A restriction plate, in the hydroclassifier tank cone, disperses the added water which tends to eliminate the. “fines” or undersize fraction which might be mechanically trapped in the “coarse” size.
The coarse fraction hydroclassifier sands are metered to a 6’x6′ Steel Head Ball Mill charged with 1″ diameter balls which give more efficient grinding on the fine feed. The ground fraction from the regrind mill is returned to Hydroclassifier with a SRL Sand Pump.
This two stage grinding affords added flexibility by controlling grind. Some ores require feed to conditioner to be thickened, which sometimes eliminates troublesome soluble salts and effectively controls the density of the pulp in the conditioner and flotation circuits. Flotation can sometimes be done at 40-50% solids without detriment; yet flotation at higher percent solids produces a more finished product in flotation cells, so this thickener is often included.
A 16″ Cutter Travel Automatic Sampler, with a wet type cutter between the Hydroclassifier and Conditioner, gives an accurate head sample.
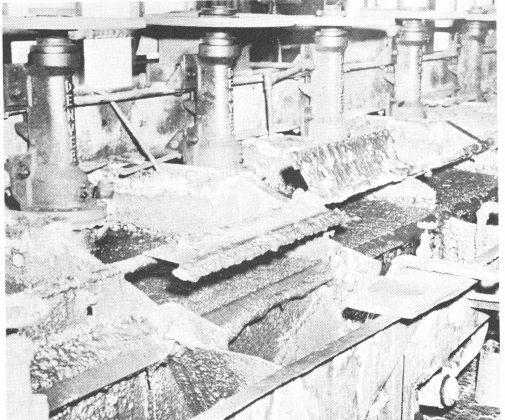
The hydroclassifier overflow, or thickener underflow is conditioned with necessary reagents for flotation. If caustic soda is not added in the ball mill, it is added with sodium carbonate to the conditioner for regulating pH from 8.0 to 10.0. Sodium silicate is sometimes added to liberate slimes; while the collector is usually a refined tall oil acid or similar product. It can be added to conditioner or in stages.
An 8-cell No. 21 “Sub-A” Flotation Machine, non-metallic flotation type, equipped with multi-bladed moulded rubber or neoprene impeller and diffuser wearing plates, produces rough flotation concentrates. These rougher concentrates are further upgraded by two stages of cleaning. Each stage consists of 3-cells of the 6-cell No. 21 (38 x 38) “Sub-A” Flotation Machine. In the rougher cells the pulp level in each cell can be controlled either by wood weir blocks or hand wheel operated weir gates. The flotation tailings are sampled by a Automatic Sampler fitted with a wet type cutter. The tailings are then pumped by means of a SRL Pump to the tailings pond.
On the cleaner flotation machine, froth is moved from stage 1 to stage 2 of cleaning via gravity, and the middling rejects from cleaner circuit are returned to the conditioner.
A 5″ x 5″ SRL Sand Pump elevates the final flotation concentrates to the 30′ x 10′ Spiral Rake Thickener; the thickener underflow is reused in the flotation circuit. The thickened product is filtered on a 6′ x 6-disc Disc Filter.
A 9″x 10′ Screw Conveyor feeds the filtered product to the 5′ x 50′ Countercurrent Dryer with dust collection system. The dried product from the dryers is moved to the Chain Type Bucket Elevator by means of an enclosed screw feeder, and discharged into a dust tight surge bin for a bagging machine; or into a storage bin for loading hopper cars.
Barite-Fluorspar-Zinc Beneficiation Plant
The flowsheet in this study is for a plant to treat economically 100 tons per 24 hours of ore containing approximately 37% barite, 37% fluorspar and 1.5% zinc as sphalerite and to yield marketable concentrates of barite, assaying in excess of 95% BaSO4, and acid grade fluorspar. The close association of the minerals and their similar response to the reagents require careful testwork to determine the exact reagents and treatment process. Overgrinding must be avoided.
The flowsheet incorporates standard equipment for both low cost and operating service. Units illustrated are for a specific tonnage but illustrate a typical flowsheet. The crushing section operates only 1 shift per day.
Barite-Fluorspar-Zinc Ore Crushing
For the average mine up to 100 tons per day, primary crushing is usually sufficient. Since over 90% of the operating problems of a jaw crusher come from the bumper bearings, an all anti-friction bearing crusher has been selected. Larger tonnages require primary and secondary crushing sections for maximum efficiency in size reduction for subsequent grinding operations. The grizzly ahead of the crusher provides greater crushing capacity since the undersize material by-passes the crusher.
Barite-Fluorspar-Zinc Ore Grinding
The ore for treatment is of such a nature that conventional grinding to —65 mesh using a ball mill classifier circuit results in excessive overgrinding of the barite. To avoid this condition a rod mill is used instead of a ball mill for reducing the feed for flotation. This circuit, consisting of a combination of spiral classifier and cyclone, actually results in a slight undergrinding of the fluorspar but this does not prove detrimental in the coarse flotation circuit. Reagents for zinc flotation are added to the grinding circuit and the pulp is then conditioned to obtain maximum contact of the reagents for effective activation of the sphalerite.
Flotation and CaF2 Concentrate
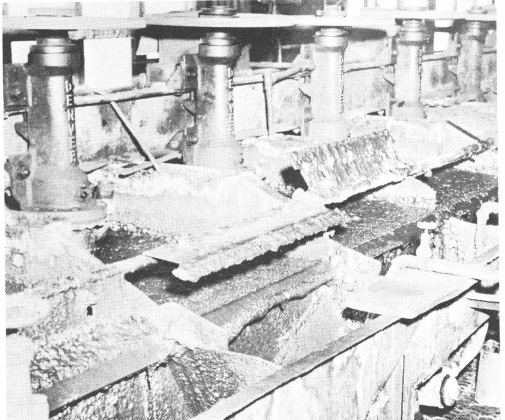
The classifier overflow at approximately 30% solids is subjected to rougher flotation in a “Sub-A” Selective Flotation Machine, followed by multiple cleaning of the rougher concentrate. Cell-to-cell “Sub-A” Flotation Machines are best for this service. The tailing from the zinc flotation section is pumped to a thickener which overflows the collodial slimes to waste. The thickened pulp is metered to barite conditioning and flotation. The discarding of collodial clay slimes, if present in the ore, is necessary to prevent excessive reagent consumption. The thickening operation also provides for uniform feed rates to the barite section.
Barite Flotation
The zinc tailings thickener underflow, at approximately 40% solids, is conditioned with barium chloride and citric acid in the first conditioner, and a barite frother and collector is added in the second conditioner. A Super Agitators and Conditioners with standpipes around the shaft provide for pulp recirculation and prevent froth buildup in the conditioner tanks. A fairly lengthy conditioning period is required to obtain the maximum effect of the reagents. The barite rougher flotation is rapid and the addition of a small amount of reagent towards the end of the circuit assures ample froth for the scavenger operation. The rougher concentrate is cleaned three times, using plenty of clean spray water to cleanse the froth and obtain satisfactory slime rejection. The barite tailing is pumped to a thickener to density the pulp to approximately 40% solids for fluorspar conditioning and flotation.
Fluorspar Flotation
The underflow from the barite tailings thickener is metered at 40% solids to the first of two conditioners where a depressant and sodium silicate are added for gangue depression. Fluorspar collectors are added to the pulp in the second conditioner. The conditioned pulp is subjected to rougher flotation followed by multiple cleaning of the rougher concentrate.
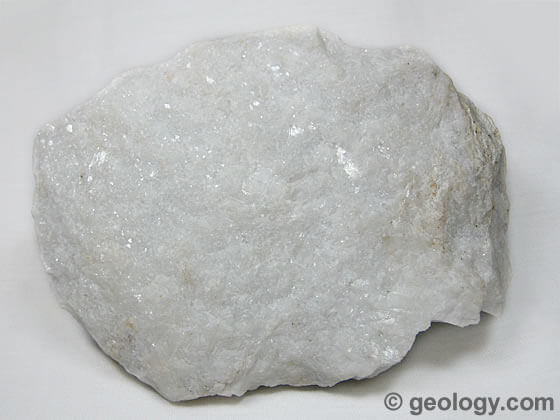
Barite Thickening and Filtration
The fluorspar and barite flotation concentrates do not present any difficulties in thickening and filtration. The thickeners are of sufficient capacity to handle the tonnage and to provide some concentrate space in the event of minor filter or dryer interruptions. Froth retaining overflow launders and sprays are desirable on the thickener tanks. The small amount of zinc in the ore does not warrant thickening prior to filtration; instead, a filter with sufficient area for filtering the concentrates direct from the flotation machines is used. The zinc and barite concentrates are filtered, using a Disc Filters and the fluorspar by a drum type Fluorspar Filter with stainless steel filter media.
Concentrate Handling
The filtered zinc concentrates drop directly into a concentrate bin. The barite and fluorspar concentrates from the filters pass to rotary dryers which are provided with dust collecting systems. The dry concentrates are then conveyed to air tight surge bins for bagging or storage silos for loading into hopper cars.
Sampling
An Automatic Samplers are used extensively for mill quality control. Variations in the feed or balance of any of the circuits requires that reliable samples be available.
Metallurgical Results
The recoveries of base metals, barite and fluorspar in acceptable products varies with the type ore and degree of association of the various components in the ore. Coarse mineralization with minimum amounts of slime will generally result in higher recoveries. The reagents and conditions for treating ores of this nature can be determined only by batch or pilot plant testing programs.
Barite Beneficiation Process
Market Specifications
Most of the barite produced by flotation is used as an ingredient in “heavy mud” for oil-well drilling, for which purpose specifications demand a material with minimum specific gravity of 4.30. When sold for production of lithopone and barium chemicals, lump or jig concentrate with minimum BaS04 of 95 per cent and maximum Fe2O3 of 1.0 per cent is specified.
Production Problems
When sold for drilling mud ingredient, the barite needs to be ground to less than 5.0 per cent plus 325 mesh, which requirement necessitates either grinding the crude ore to this fineness before flotation or regrinding the concentrate produced at a coarser initial grind. Gravity concentration is sometimes advantageous in conjunction with flotation, as by this means products may be obtained that will meet the requirements of more than one market. Some of the anionic reagents commonly used to float the barite are detrimental to its use as drilling mud and must be removed from the particle surfaces by heat during the drying stage.
Reagent Combinations
Barite is readily floatable by fatty acids in an alkaline pulp, usually oleic acid with soda ash or caustic soda. Sulphonated petroleum products are also satisfactory. The trend in development of new reagents is to overcome the need to heat the concentrate to a high temperature to remove the reagent.
Barite Geology
Source: This article is a reproduction of an excerpt of “In the Public Domain” documents held in 911Metallurgy Corp’s private library and a link provided by Mr A. Rawle.
Barite Processing
Mining Methods Barite Recovery
Any discussion of barite mining is virtually. impossible without considering, almost in the same breath, the many other variables, such as beneficiation, transportation, infrastructure and location that impact the economics of a particular barite orebody. My comments will be limited to just the mining aspects of barite orebodies and these observations must be considered in proper context with all other parameters affecting exploitation of a barite property prior to final decision on economic feasibility. In many instances low-cost mining situations are more than offset by high-cost beneficiation requirements. Likewise, there are cases of relatively high-cost mining associated with no or low-cost beneficiation requirements thus permitting economic exploitation.
Barite orebodies and occurrences are almost as varied as the number of occurrences. As in most mining situations, the design of a mine plan and implementation of a proper exploitation program must be approached on a case by case basis. Proper and sufficient geologic control of a barite orebody must precede the development of a mine plan.
Generally speaking, barite orebodies can and, at many times, do “strange” things; pinch with depth; almost never increase in size with depth, overturn, fault-off, change grade, etc. Due to the extreme variable nature of most barite orebodies, a mine plan and its implementation must be as flexible as possible. The ability to quickly adapt to variable conditions will greatly enhance the economics within a particular barite mining environment.
Although a significant quantity of the world’s barite production comes from underground mines, the world’s largest producing barite mines are surface mines. Virtually 100% of current barite production in the United States and Canada is from high productivity surface mines. Generally speaking, only in those areas of the world that have an abundance of low cost labor is the exploitation of barite by underground mining feasible at today’s economics.
Two of the largest underground barite mines in the world were located in North America. Both were shut down in the early seventies with appreciable reserves remaining at depth. The costs associated with underground mining of barite attributable to the much lower productivities of underground mining relative to surface mining dictated the closure of these two mines prior to the depletion of reserves.
Open Pit Barite Mining
Open pit mining of barite orebodies is generally no different than most other open pit mining environments. As in all other sectors of the mining industry, the increasing costs of labor and the decreasing trend in productivities will dictate the use of ever larger and more productive mining equipment.
Just 10 years ago 4 cu-yd. loaders and 20-25 ton trucks were the largest sizes commonly employed by barite producers. D8’s were generally the largest dozers used. Today 35-40 ton trucks with 7-8 cu.yd. loaders are common.
The next generation will see the larger surface mines employing 50-60 ton haul units coupled with 8-10 cu.yd. loaders.
Generally speaking, most barite orebodies amenable to open pit methods are of the size where flexibility of equipment employed is of prime importance. It is common practice to use the same equipment for both stripping and mining, thus permitting much greater flexibility in day-to-day operations, generally better equipment utilization, and commonly lower equipment acquisition and maintenance costs.
Stripping ratios of surface barite mines are increasing and the movement of large volumes of overburden are becoming more and more critical to the overall economics of an operation. One could initially conclude that the higher efficiency of scrappers, draglines, or shovels for overburden removal and truck-loader combinations for the mining phase would be the most economic approach. In practice, most barite orebodies do not lend themselves to complete separation of the stripping and mining functions. Most barite orebodies are not amenable to using scrappers, draglines or large shovels for the actual mining phase and the ore must be selectively mined at least to the extent that larger stripping equipment would create unacceptable mining dilution. Likewise, many barite orebodies do not lend themselves to continuous, simultaneous mining and stripping. The flexibility afforded by truck-loader configurations generally outweighs the loss of productivity over scrappers. Most barite orebodies lend themselves best to cycles of mining, stripping, mining, etc. , and together with market, weather, and geological conditions, the flexibility of readily switching from mining to stripping or back to mining generally provides the best possible utilization of manpower and equipment.
As the higher grade, larger barite orebodies become depleted, deeper lower grade orebodies will naturally be exploited, and the prime consideration in mining will become the removal of larger volumes of material at the least possible cost. Selective mining reduces productivities in any given situation. The greater the degree of this selectivity the lower are resultant productivities and resultant costs can escalate rapidly. The trend now and in the future will be to less selectivity in mining with consequent improvement and enlargement of the beneficiation sector to offset the increased dilution from mining. The key to low cost mining and stripping is volume; the greatest amount of material moved in the least amount of time. Increased equipment size with its inherent increased productivities coupled with improved, larger crushing and beneficiation facilities will become the norm in the mining of large barite orebodies.
Underground Barite Mining
Economic exploitation of barite orebodies by underground methods in the United States and Canada at today’s economics would be most difficult if not impossible.
As alluded to earlier, the large underground barite mines at Malvern, Arkansas and Walton, Nova Scotia were most unique. Most barite orebodies do not occur in sufficient size or grade to permit underground mining with methods that lend themselves to high productivity mining techniques. Both the Malvern and Walton orebodies were exceptions. Both were multimillion ton orebodies of sufficient tonnage and dimension to permit exploitation by highly productive mining methods.
Unfortunately, the vast majority of barite occurs in narrow veins of varying degrees of strike and dip and lend themselves only to mining by lower-productivity, narrow-vein-type mining systems. Fortunately most barite ore-bodies are competent and occur in relatively competent geologic environments. The author is familiar with attempts to undercut and block-cave barite, but the extreme competency of the barite prevented natural caving even after massive undercutting of the ore zone. Open storing and shrink-stoping methods are commonly employed, and technical problems are generally no more complicated than encountered in most other narrow vein mines. Competency of the ore-body, hanging and footwall, together with mine water will be the most important considerations. Extensive support systems and the handling of appreciable water volumes will obviously seriously impact mining costs. Narrow vein barite mines are not large producers. One of the most common problems in narrow vein systems is under-development.
Mining volumes are in direct proportion to the number of people that can be efficiently employed within a mine. Consequently, the number of working faces available within a mine system relates directly to the capacity of that system. Generally speaking, it can and normally does take up to or over a year from primary development of a stope to final ore extraction in a shrink-stoping operation.
Annual production is dependent on the number of stopes that can be developed, mined and pulled in a year. Generally narrow vein barite mines are not or cannot be developed to the level required for large volumes. Unless multiple working faces are created by multiple level development within the same or closely associated vein systems, sufficient stopes cannot be developed to allow continuous, high volume production. Under-development creates periods of low production during development cycles, followed by spurts of production when stopes are mined and pulled, again to be followed by low production periods when the mine again has to “catch-up” with development. This can create havoc with costs not only in mining but in all phases of the operation through marketing.
Exploitation of narrow vein barite orebodies by underground mining methods are common and practical in countries with lower cost labor. Even so, mining costs are the significant factor as most orebodies currently being mined are of sufficient quality to require little or no beneficiation and resultant costs are competitive. Many of these mines are being forced to improve productivities and have remained competitive only by virtue of conversion to the more productive trackless systems employing large, fast, rubber-tired underground equipment. Narrow-vein underground mining of barite requiring extensive beneficiation in order to produce marketable quality material would in most cases be prohibitive at today’s economics.
General Considerations
The single most important factor associated with the development and mining of a barite orebody is people. Generally speaking, approximately 50A of the cost of barite mining is labor cost. Naturally, this will vary but is generally a workable “rule of thumb.” Not only is the direct cost of labor important but, in certain situations, the indirect costs of labor become virtually prohibitive. A certain percentage of the labor force in all mining situations must be skilled and in the more remote locations of the world the costs of labor can become one of the most important factors in the economics of a barite property. Unlike the ferrous and non-ferrous metals industry, barite mines are extremely small in comparison (the largest in the world are commonly less than 500,000 tons per year capacity) and infrastructure costs of housing and facilities can become prohibitive.
The recent proliferation of governmental regulatory interference in all phases of industry are impacting costs in all areas. Safety, environmental, and permitting regulations on both the federal and state levels are significantly lowering productivities of barite mining. As barite mines are small in comparison to most mines, the impact of recent training regulations and punative fines on the part of MSHA will have a greater effect on unit costs of production. The days of “throwing together” a small producing unit at nominal cost have just about had it. With stringent noise, dust, safety, training and permitting regulations, the costs of “getting in” to production are much greater, the reserves must be sufficient to justify the initial capital and preproduction development costs and production volumes must be large enough to offset, on a unit cost basis, the impact of the recent proliferation of “zero-productivity” cost impacts.