As it is my opinion that deep alluvial mining methods in Victoria and in the Murray Flats in New South Wales are practically in their infancy, and considering that we, the old school, of alluvial miners, who have thirty or forty years’ experience to guide us, must in the natural order of things hand over the management of our mines to the younger and less experienced generation of miners, I thought that as our Association has been formed for the purpose of disseminating information and the exchange of ideas, a few notes on the practical working of alluvial mines might be of some service to aspirants for the position of mining manager.
The greatest difficulty the alluvial miner has to contend against is the immense quantity of water contained in the drifts overlying the wash in the gutters or ancient river beds, and to cope with this water successfully and economically is the point to be aimed at by our mining managers; and if they thoroughly understand this part of their business in all its details, they will not only win kudos for themselves, but will be the means of saving large sums of money to the companies they represent, and, in many instances, will make a success of a venture which otherwise might be stopped for want of funds before it is properly proved.
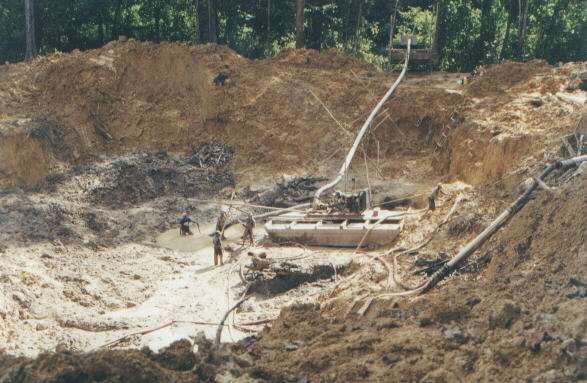
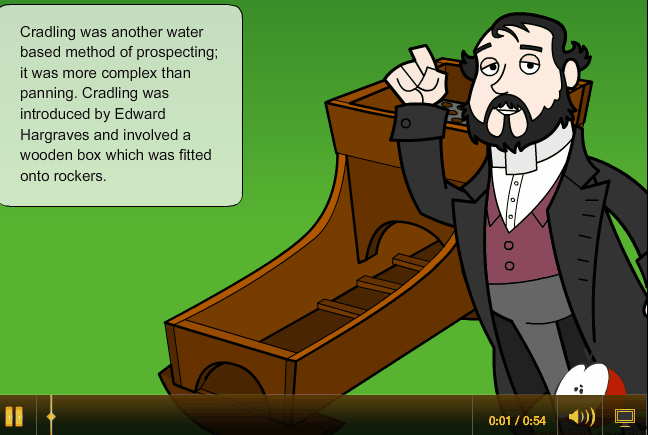
At the present time, although we have had over forty years’ experience in draining the deep leads of the colony, I regret to say that a large amount of ignorance still prevails amongst both directors and managers as to the best means to be adopted to tap the water in the mine and raise it to the surface. We will take the question of machinery first, and I may say that I have been pleased to see during the last five years that a start has been made to supplement the old one cylinder pumping engines with compound condensing engines; the first one put in in the colony being by the Chalk’s No. 3 Company at Carisbrook, where with a 20 in. lift in each end of the shaft (size 15 ft. x 6 ft.; two winding compartments 6 ft. x 3 ft. in the middle and plunger chamber 2 ft. x 18 ft. for 25 ft. in depth, and 26 ft. 6 in. for 35 ft. in depth), the water has been pumped 30 per cent, cheaper than any other class of engine, including the Cornish Beam, has ever pumped water in the Creswick or Maryborough district. The high-pressure cylinder is 16 in. and the low-pressure 28 in. dia., 4 ft. stroke, with horizontal condenser. There are three Cornish boilers 26 ft. x 6 ft. 6 in., working at a pressure of 110 lbs. per square inch, which gives ample steam to raise the water 270 feet.
This class of engine has been improved upon by the Spring Hill and Central Leads Company in the Creswick district, and by the Duke United and Victorian Gold Estates in the Maryborough district with very satisfactory results. The Spring Hill and Central Company’s engines consists of three cylinders, 11½, 16 and 30 inch diameter, 5 feet stroke, horizontal condenser: It is supplied with steam by three Cornish boilers, 26 ft. x 6 ft. 6 in., working at a pressure of 140 lbs. per square inch, and is designed to work two 18 in. lifts to a depth of 500 feet. To show the advantage of the triple expansion engine, compared with the old class of single cylinder without a condenser, I may slate that some years ago the Lord Harry Company, at Allandale, had a 26 in. non-condensing engine working an 18 in. lift of pumps on a 7 ft. stroke, 9 strokes per minute, to a depth of 600 feet, and they burnt 90 cords of firewood per -week. Whereas, the Spring Hill and Central Companies worked an 18 inch and a 15 inch lift same stroke and same speed, about 340 ft. deep, and consumed 30 cords of firewood per week, or, in other words, did nearly the same duty at one-third of the expense.
As fuel is becoming a very expensive item, every manager should do all that lies in his power to encourage the substitution of high-pressure condensing engines in place of those so long and expensively used in our deep mines.
The old Cornish Beam has still a few advocates who claim superior advantages for it over the horizontal engine, the principal of which are the greater length of stroke and the small amount of wear and tear on the working parts. These must be admitted, but it also has its disadvantages compared with the triple expansion engine, which are, a larger consumption of fuel to a given amount of work and the expense of a separate driver in each shift to attend to it, as it is in a house to itself and requires careful watching when running at a high rate of speed. The matter of first cost is also in favour of the triple expansion.
As to the question of the best means of draining our deep leads, I may say that our most experienced managers agree that it is not advisable to cut the water in sinking, if it can be avoided, except in basaltic rock where the water can be brought away free from sediment and without danger to the shaft. In that case it can be pumped more cheaply, as it would not require to be lifted so high as it would be were this water tapped after the mine had been opened up. But, of course, the quantity of water in basaltic rock is always an unknown factor before the shaft is started.
What should be aimed at, and which is of paramount importance in laying down the plan for opening up an alluvial mine, is to carefully locate by boring the position of the deepest channel of wash, also both banks of the old river, and note the depth of drift and gravel overlying the wash, as the quantity and pressure of water likely to be encountered depends largely upon the amount of drift met with. While mentioning drift, I may say that experience has taught us that frequently that which appears to be sandy clay in a bore has given as much trouble in sinking a shaft as heavier bodies of drift.
https://the-great-australian-gold-rush.wikispaces.com/Tools+and+techniques+to+Mine+Gold
I can safely say that all our managers and directors who have had experience in sinking a shaft through drift country, are agreed that the cheapest and safest course to pursue is to select a site for a shaft on either one side of the gutter or the other (the side having the steepest reef or bank being preferable, if possible, as the distance to be driven would be shorter), and clear of all drift, as immense sums of money have been expended in sinking through drifts from 50 to 100 feet thick, and in some cases, shafts have had to be abandoned and large and expensive machinery removed owing to the impossibility of surmounting the difficulties presented by the boiling nature of the drift.
The matter of driving a few or many hundred of feet is of little consequence, and will cost infinitely less than sinking a shaft through more than 10 or 15 feet of drift, which, however, can generally be accomplished with a properly constructed drift box. As I have never seen a description of a sinking box in print, I think it is well to give a short account of one. The box is formed to suit the size of the shaft being sunk, and should be made large enough to admit another box inside of it which would be the ordinary size of the shaft, as the first box might become immovable before the required depth be attained. The box to be made of steel plate three-quarter to an inch thickness according to size of shaft; depth of plate to be 3 feet; the sides to be in two pieces, joined together by a vertical plate about 12 in. x 1 in. riveted to one part and bolted to the other with 7/8 bolts and rivets ; the end to be in three pieces, the two corner pieces to be, say, two feet wide, to be riveted to the sides with 4 in. angle iron ; the centre piece of end to be bolted to the corner pieces with 4 in. angle iron, another piece of angle iron being riveted to corner piece; a 4 in. angle iron to be riveted all round within three inches of the bottom of box, and timber 16 in. x 6 in. to be bolted, with 7/8 bolts 18 in. apart, on top of angle iron, on which to place screw or hydraulic jacks; all rivets to be 7/8 and placed not more than 4 in. apart, and countersunk at back of box. Bolted all round on top and at the back of this box, is a plate 3 ft. 6 in. x ½ in., with 7/8 bolts 9 in. apart, butted close at the corners. This part of box stands up behind the slabbing of shaft, the slabs being cut to fit close up to the plate so as to prevent the drift finding its way between the plate and the slabs. Plates the full depth of box, if procurable, make the best job. The sides, all complete with corner pieces forming the ends, can be lowered into the shaft in one piece and placed in position ; the two end pieces then sent down and are bolted to corner pieces and the box is complete, with the exception of strong centre pieces, which should not be overlooked.
The depth of lead having been ascertained by boring, and about 20 feet added in case there should be deeper ground between the bores, the shaft should be sunk sufficiently in the bed-rock to allow for a rise in the bottom of main level of about two inches in each hundred feet, and permit of the lead being worked, say, a mile down the lead or to the boundary if less than a mile. I have found that the above fall is sufficient to provide a good road for the trucks travelling each way. It also serves as a good water lodgment when the road is laid properly, and does not form a man-trap for the workmen in the manner that drives driven at a steeper gradient do in wet alluvial mines, as there might be enough water in the chamber to drown a man, when the drive a few hundred feet from the shaft would be clear of water; it also means that all the silt would find its way back to the shaft instead of settling along the main level, where it could be easily and cheaply removed.
In addition to the under level in our deepest and most difficult alluvial mines, an upper level should be constructed in the bed-rock, for three very important reasons. First, to provide an escape for the men in case the mine should be flooded; secondly, as a return air course; thirdly, to tap the water by boring, at a higher level, where the pressure would naturally be lightest.
Many years ago it was considered the correct thing to drive in the wash and meet the water in the face, or to put up small rises or bleeders ; but this course proved so disastrous in many cases when going into a gutter for the first time, that this system has been abandoned by all managers of experience in favour of a series of tubed bores from the back of the drive up to the wash. I may say that boring for water in this manner is a matter that requires some experience and a good deal, of care, but the precautions necessary to be taken depend somewhat upon the nature of the bed-rock through which it is intended to bore. Unless the country is hard, from 5 to 10 feet of 4 inch tubing is forced with a jack into a hole bored slightly smaller than the tube. The tube is then wedged round tightly at the back of the drive. A hole is then bored with a smaller augur or bit, just large enough to admit a 3 inch square thread tube, the joints of which have been fitted to run easily, and the leading tube made egg end, leaving an opening at the top end of about 1½ inch. The tube should also be perforated with ¾ holes for about 3 feet from the top, so as to act as a filter when the tube has been forced up into the wash. The best length of tube is 5 feet, with a few shorter lengths for matchings. A large nut is screwed on to the male end of tube to protect the bottom thread while the tube is being forced. It is necessary, in soft country especially, to exercise great care not to bore the hole too large for the tube, as the water would then get outside the tube, and should there be much pressure, the water would scour the hole large enough to permit an inburst of sand. By this system of tubing, in anything like firm country the water can be drawn off in quantities equal to the capacity of the pumps ; and should anything happen to the machinery necessitating a stoppage, it would be found that part at least of the tubes could be locked without fear of causing the water to flow outside instead of inside the tubes. But we know that “the best laid schemes of mice and men ang aft aglee,” so it is necessary to make provision so that should an inburst of water and sand be met with unexpectedly, the pumps may be protected from being starved by sand. This is done by constructing strong locks or doors at intervals along the drive. The ground is cut out about 2 feet into the sides, back and bottom of the level, and a heavy frame set, with two centre pieces in it, placed in the excavation, and boarded up close on each side. A door about 6 inches thick, and lined with iron in some cases, is hung with strong hinges in such a way that a man can close it easily behind him. These doors are not made air tight, as the compressed air in case of an inrush of water would blow them out. But experience has shown that where there are a number of these doors along a level, a large accumulation of sand may be found between the doors nearest the face, but the sand will not as a rule reach the pumps. But in case the unexpected were to happen and the men should leave the mine hurriedly and forget to close the doors, it is as well when fixing the pumps to make provision to turn the plunger into a drawlift, where the plunger is fixed on a level with the bottom plat, by inserting immediately above the top clack, and under a bottle piece to receive a drop clack (working barrel to be placed immediately over the latter), a casting about 2 ft. 6.in. high and about the same width as the H piece, one half of which projects towards the end of the shaft and contains a valve, equal in area to the other valves, with short rose piece directly under. A lever is attached to spindle of valve and fixed in such a way that strong rod, with rigid joints, can be attached to the end of lever and continued up the shaft above water level. In case the lift should get starved, this valve could be raised sufficiently to allow the lift to take its water above the level of the cap-piece of chamber. Then all that would be required would be to lower a drop clack into bottle, piece, and the drawlift rod in the usual way, and then pump the water down to the level of the cap. The rose would then be taken off and a hose attached long enough to unwater the mine.
This I may say is how I have arranged the 26 in. lifts of the Victorian Gold Estates.
When the mine has been drained, or at least the great pressure of water taken off, and not till then is it practicable to open up the gutter in a systematic and profitable manner; but managers have frequently found it difficult to convince directors and shareholders of this fact, so that they have been forced to drive into the wash, with disastrous results to all concerned.
When it has been decided to go into the wash for the first time, it is advisable to be extremely cautious and attend to everything likely to ensure the safety of life and property.
A short crosscut should be driven off the main level at a point outside the deepest run of wash, and a door hung near the opening. A rise should then be constructed near the end of the crosscut and opened out in bedrock, the back of the drive being slightly above the level of the deepest wash proved by boring over the back of the main drive. About twelve feet from the top of the rise or jump-up, another door should be hung, so that in case of a rush of water the men could close the door and so be enabled to descend the jump-up safely.
As soon as the water is sufficiently reduced so that the successful opening of the mine is placed beyond a doubt, permanent jump-ups maybe constructed off the back at the main level in the usual manner.
It is from this stage onwards that the knotty question of ventilation demands the attention of the management. But if two levels have been brought in from the main shaft, and the upper one connected with the pump shaft only, and powerful blowers and large air pipes (larger the better) supplied, I have no fear of the air proving very troublesome. Provided that, as the mine is opened up, an air drive be driven on the course of, well back from, and on a level with, the lead, and connected with each jump-up by a crosscut, so that the natural current of air will have a free course along the bottom level and up the last jump-up—the others all being covered with doors—and then diverted with canvas brattices to every working face and then back through one of the crosscuts to the air course. If the natural current is not sufficient, a powerful exhaust fan should be connected with the upcast shaft. Where there are two pump shafts, the fan should be so arranged that it could be connected with either one of the shafts, so as to enable the pitman to attend to the pumps at one end of the shaft while the fan is drawing through the other. But, before, the pitman went into the shaft, I would connect the pump shaft with the down cast at the bottom, and partly open the connection with the fan at the top, so as to purify the air in the pump shaft.
I may say that it has been proved beyond a doubt that it is not possible to ventilate a large mine with air pipes alone, neither can an alluvial mine be properly ventilated with an air course alone, but the one is the natural correlation of the other.
I have heard it argued that an air course and upcast shaft are not effective where carbonic acid gas has to be contended with, but my reply to this is that I am not aware of a single case where the system, in all its details as I have described it, has been tried in any of the worst of our large alluvial mines. But I have known two main shafts to be connected and a very large current of air to pass from one shaft to the other without benefiting the workmen employed in the washdirt faces in the slightest degree. At this I was not surprised, as no means were adopted to divert the current of air through the different crosscuts where the gas was known to exist, the workmen and the gas being many hundreds of feet outside the current of air between the two shafts, so that it was not possible for the fresh air to dilute the gas sufficiently to be of any benefit to the workman. It may be of interest to state that I saw the effect of a current of air on carbonic acid gas while I had charge of Chalk’s No. 3 Consolidated at Carisbrook. We had a strong current passing from our shaft to the shaft of the Chalks Junction, and we had two parties pannelling about 300 feet outside the air course, an the air from a No. 4 Root’s Blower going into these two faces; at times the gas would not allow us to get within 100 feet of the faces, while at other times a candle would burn at the mouth of the pipe, but would go out directly under the pipe, the same as if it were dipped in water. Shortly afterwards we connected a crosscut, which had been driven to divert the current of air, with the pannelling faces, and we then found that air pipes were unnecessary, neither was the gas met with at any time afterwards.
As an argument in favour of air courses (although no argument should be necessary, seeing that all the principal coal mines in the world, where all the worst gases have to be contended with, are ventilated by air courses), it may be as well for me to state that I ventilated the Prentice Freehold Mine at Rutherglen, for over two years, where we had 300 men employed, and never had an air pipe in the mine, except in the reef drive and leading washdirt drive which were ventilated by the blower. The only difference between the system adopted there and the one I have described being that we had a separate air shaft, without an exhaust fan. The fan was not required, as there was not so much gas as there is in some other districts, still we found that a short distance outside the air current, carbon dioxide was very prevalent.
In conclusion, I must say there are two essentials to the successful working of any mine, and they are good roads and good ventilation. And I maintain that if a mine will not pay to expend sufficient money to provide all the means I have stated to secure good ventilation, it will not pay under any circumstances, as it is impossible for a man to do a fair day’s labour where the conditions are against him, and where his health is being gradually undermined in a gaseous and vitiated atmosphere. Good air means more work, and more work means larger dividends.
[I wish I could by some means cause the words I have placed in italics to sink deep into the minds of the directors of our mining companies, as I am satisfied that many of them have little conception of the daily loss to their company in consequence of an insufficient supply of air to their miners.]