These machines consist essentially of a floating structure, supplied with a powerful pump of centrifugal type, raising sand and water through a suction pipe. Characteristic types of suction dredges are the Ball and the Welman. The Welman patent pump is in many respects similar to a centrifugal pump; the runner, however, is differently constructed, the vanes or blades being merely solid cast-iron junks instead of thin, and, on the inside, greatly curved blades. The runner employed at the Waipapa’ Welman dredge in New Zealand in 1889—90 was 2 ft. 3 ins. in diameter and about 8 ins. wide between the flanges, with four solid vanes greatly curved, on the back, but almost straight on the other face. On one side, the flange was solid, having slight ribs on the outside to strengthen it; while, on the other side, there was a circular opening, about 15 ins. in diameter, to allow all the water and material to pass through the runner. This runner was keyed on to a shaft, which was about 2 ins. in diameter, and had a cast-iron casing over it of about 1½ ins. in thickness, and revolved at the rate of 430 revolutions per minute. This forms the Welman pump.
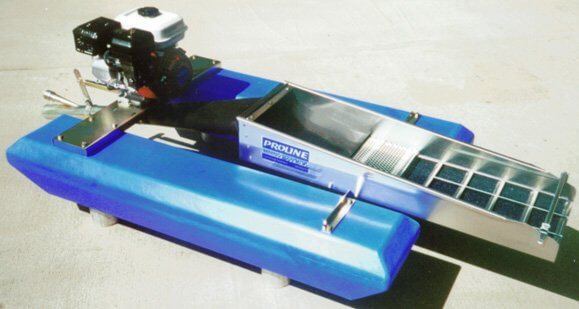
The hull or punt of this dredge was 50 ft. long and 15 ft. wide, and, on each side of this punt, there were three pontoons, the four end ones being 4 ft. and the centre one 6 ft. wide. These pontoons were placed alongside the main punt on each side, end on end, and were held together by longitudinal beams lengthwise, and to the main punt by heavy cross-beams, which crossed the deck, extending from 7 ft. to 8 ft on each side. This admitted of these beams being bolted to the longitudinal beams which held the pontoons together so as to form a platform to erect staging for the washing tables. There were also two pontoons at the stem of the dredge, fastened by beams to the main punt, to carry the staging for the end of the washing tables and tail boxes, which delivered all the water and waste material on to the ocean beach, the tailings being prevented from banking up, to any great extent, by the waves.
The pump was placed on the main punt, and from it there was a horizontal pipe with an elbow to join on to the casing, and fit on a projecting flange on the runner. This horizontal pipe, after passing to the front end of the punt, was fitted with a universal joint, so that the pipe outside the punt could be lowered, raised, or moved from one side to the other. On the end of the outside pipe, there was an elbow turning downwards, and having a bell-mouthed sleeve over the end. The suction and delivery pipes were 12 ins. in diameter; but in order to prevent stones jamming in the pipe, there was a ring fixed inside the bottom end of the suction pipe, thus reducing its diameter to 10 ins.; therefore, any stone which came through this ring could easily pass through the pipe, but there was still a danger of its jamming in the runner. The dredging pipe was lifted and lowered by a steam winch, the derrick being placed directly at the front end of the punt and dredging round on a pivot, so that the pipe could be made to describe an arc of about 160 degs.; by this means a cut or paddock could be excavated from about 45 ft. to 50 ft. wide. After taking up one cut, the dredge was shifted back again and another cut begun. There was a vacuum-gauge attached to a pipe, leading from the top of the universal joint of the dredging pipe, and this gauge showed the man that guided the dredging pipe how it was working. If everything was going on smoothly, the gauge registered 5 lbs. pressure per square inch, but if a stone got into the bottom end of the pipe, it immediately rose considerably above this, or, if a stone jammed near the runner, the gauge fell below the 5 lbs. By this means the man conducting the dredging operations could at once tell what was the matter, and remedy it accordingly. The dredge was designed to lift 80 tons per hour, but it did not lift more than about 35 tons. The height of lift was 15 ft. above water level.
As regards the value of suction dredges, it may be said that, for gold-dredging purposes in rivers, they have had their trial, and mostly failed. For sand or slurry, the centrifugal pump has proved its value; but, for river gold dredging, it has certain practical defects. In the first place, the large volume of water it raises tends to flood the tables and sluices, and prevent the gold settling. Sluices also, of the breadth needed for the large flow of water, are expensive to make, difficult to maintain in equilibrium, and troublesome to clean up. In the third place, the suction force being intense near the pipe- mouth, and decreasing rapidly a short distance away, is apt to draw the sand and gravel away, leaving the heavier gold behind. A centrifugal pump, therefore, is of little use to raise coarse, heavy gold, especially on a hard, uneven bottom. It obviously cannot disintegrate and raise hard ground. An attempt has been made to remedy this defect by fitting the suction pipe with a chisel or plough blade, adapted to loosen the ground. But cutters of this description are ineffective, and lead to further trouble, since the gravel is disturbed by the cutting and the gold separated from it. Inability to deal with the tightly-cemented ground caused the failure of the Welman dredge on the Manuherikia River. Again, a suction dredge is subject to frequent interruptions owing to the grating in front or the pipe itself becoming choked with stones, weeds, &c. Mr. D. Wilson, of New Zealand, has devised a sectional grating box for protection against choking by weeds, and the trial is said to have been satisfactory. Lastly, suction pumps cannot work on viscous clayey ground, nor economically raise coarse material, as a runner construction capable of passing large stones involves great loss of efficiency. Possibly this difficulty may be overcome, but at present the suction dredge can deal economically only with fine material, as in the case of the Welman machine at Waipapa, where the great bulk of the stuff, or about 95 per cent., was sand and fine shingle. At Saltwater Creek, Paeroa, New Zealand, in 1889—90, Messrs. Brown & Co., of Wellington, erected a dredge with a cataract pump for lifting sand and shingle; but, though this pump was highly spoken of as an efficient dredge by people in America, it proved suitable for raising only material up to about 3 ins. in diameter, and was therefore quite unfitted for dredging the bed of Saltwater Creek. This inability to deal with coarse material largely restricts the utility of the machine. Tempted by its success for harbour and river channel work, and its apparent suitability for operating over rough ground, where obstacles abound, several companies have tried the suction dredge on the rivers of British Columbia, the Upper Fraser, the Quesnelle, &c.; but there, as at almost every other place, it proved to be utterly useless. Among the more recent witnesses to this fact may be cited the following : Mr. J. Bowron, Gold Commission, Cariboo District, writes: “ I feel safe in saying that in this district the suction dredges have proved a failure.” Mr. G. C. Tunstall, Gold Commissioner, Yale Mining Division, states : “ The Fraser River Consolidated Gold Company has operated on the bars of the Fraser River, between Ruby Creek and Hope, with a powerful dredge on the suction pump principle, which, so far, has not been successful. Alterations will shortly be made by the substitution of buckets for the present system.” Mr. G. Wilson, reporting to the Minister of Mines, New Zealand, mentions that: ” Dredging for gold by means of suction dredges has also been tried to a considerable extent in New Zealand, but has proved a failure in every case. There have been sixteen suction dredges put upon different claims, including two fine plants sent out by Messrs. J. H. Gwynne, of London, and in no case have they proved profitable investments. There is a considerable amount of wear and tear on the pumps, and the power required to drive them is so great that the fuel account is out of all proportion to the amount of work done. In hard wash, where the best gold is generally to be found, the suction pump appears to be almost useless, for it will not lift the wash without some kind of a cutter to disturb it, and, so far, no cutter has yet been made in New Zealand that will stand in the wash or gravel.” Again, in the official report for 1899—1900, Mr. Warden Poynton states: “ The suction dredge erected on one of the Waiau claims is now being altered to a bucket dredge.” And, in the “New Zealand Mines Record,” November 16, 1904, p. 142, it is stated: “ Campbell’s Creek, near Castlemaine, was at one time the scene of operations of a suction-pump dredge, which did not pay. Now a Melbourne company has a bucket dredge working the same ground, and, it is understood, with fair results.” From reports issued by the Mines Department of Canada, it seems that suction dredges have also been tried there, but from the published returns in their reports they do not seem to be very successful. A writer in the “ New Zealand Mines Record,” discussing the working of the sea beaches between Hokitika and Greymouth, on the west coast of New Zealand, observes: “ Some twelve years ago suction dredges were tried, but were not a success.” As the rivers of British Columbia and the sea beaches of New Zealand offer the conditions presumed to be most favourable to these dredges, it may be safely assumed that, at present, they are unsuitable gold-savers for river or beach work.
On the other hand, for operating on banks and river flats, by what is known as land-dredging, the suction or centrifugal pump is in common use. For this, however, there are special reasons, discussed elsewhere by the writer.
Although the suction-dredge is generally condemned, it is possible to imagine conditions under which a suction-pump might form a useful addition to the grab or to the bucket dredge. In December 1904, Messrs. W. Simons & Co., Limited, Renfrew, Scotland, launched such a combination dredge, the Murihiku. Besides being fitted with a special set of buckets for dredging rocky ground, the vessel was fitted with a sand suction-pump. The buckets, as well as the suction pipe, were made to dredge to a depth of 40 ft. The hopper was arranged in such a manner that the dredgings could be relifted from the hopper and discharged over the side by a special patent arrangement of the builders, and delivered ashore through a long line of floating pipe for land reclamation, or into barges moored at the side of the dredger. Ordinary hinged doors were also fitted to the vessel’s own hopper, so that the material could be deposited at sea when required. The machinery consisted of two sets of triple expansion engines and two cylindrical boilers of 160 lbs. working pressure. All the latest appliances, including water heater, evaporator, filter, and electric light installation were fitted on board. The Murihiku was constructed to the order of the Agent-General for New Zealand, under the direction of Messrs. Carruthers & Elliot, Consulting Engineers, London, and Mr. R. M. E. Ashworth, Resident Inspector.