Table of Contents
Brinell Hardness of Babbitt Bearings at Increasing Temperatures
- Brinell tests at progressively increasing temperatures are given for a representative lead-base and a representative tin-base Babbitt Bearings, showing that the former has superior resistance to deformation at the working temperatures of bearings.
- Small squares of bearing bronze, tinned and then babbitted with a representative lead-base babbitt and a representative tin-base babbitt were subjected to compressive loading. The lead-base babbitt showed loss average compression than the tin-base babbitt. Compression did not materially increase the Brinell hardness of the babbitts.
- A process and a tool are described for giving smoother and more accurate surfaces to bearings than has heretofore been possible.
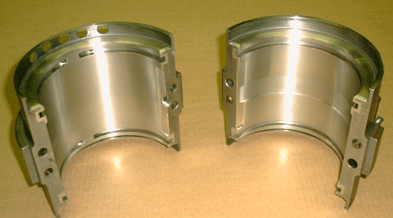
The following experiments have recently been carried out in the chemical laboratory of the Westinghouse Electric and Manufacturing Co., Pittsburgh, Pa. While the work is incomplete, it is described at the present time because data on the comparative merits of lead-base and tin-base babbitts are of interest in connection with the present shortage of tin.
Bearings fail because of wiping, of deformation. Hence tenacity is desirable in a bearing metal, especially tenacity at high temperatures. The Brinell test is commonly regarded as a measure of tenacity. In fact, it has recently been proposed to substitute for Brinell hardness number the expression “tenacity number.” It seemed, therefore, that the Brinell test was especially adapted for the tests described.
Disks, 4 in. (101 mm.) in diameter and 1.5 in. (38 mm.) thick, were made of the babbitts to be studied, designated A, B, C. They were poured into metal molds, pyrometer leads being soldered in the center of each disk. The composition of the babbitts was as follows:
The disks were heated by an electric hot plate, the heating being controlled by suitable rheostats. The thermocouple leads were connected with a Leeds & Northrup potentiometer, for measuring the temperatures. The disks were well insulated to prevent radiation losses, and after the desired temperature was reached it was held for several minutes to guard against variations.
The Brinell hardness tests were made on the bottom surfaces of the disks, a light machining cut being taken from each sample in order to secure a perfectly plane and smooth surface. Fig. 1 gives a sketch of the apparatus used for the test. The Brinell hardness numbers were plotted, giving the curves shown in Fig. 2.
At 35° C., the hardness of the A and C babbitts is identical, but above this temperature the lead-base babbitt has the greater hardness.
The curves for babbitts B and C are almost parallel, and not far apart; it is seen that the C curve is slowly approaching the B curve. Complete results from the various testing departments of the Westinghouse company, covering a number of years and a great variety of motors, confirm the superiority of the lead-base babbitt. The number of wiped bearings that had to be rebabbitted was about 100 per month with the A babbitt, but not more than six per month when the C babbitt was used.
These practical results have led to the adoption of the C babbitt for all classes of machines, and the complete elimination of A or tin-base babbitt. Both experimentally and practically the lead-base babbitt has shown greater resistance to wiping or deformation at working temperatures than the tin-base babbitt.
The hard, genuine babbitt B, the test of which is shown in Fig. 2, while not regularly used, has been found very serviceable in the Kings-
bury step bearing and other situations where the bearing pressures have been rather high. While the Brinell hardness shown in Fig. 2 for the A and C babbitts is not far from the average hardness found for these alloys when using the standard hardness test piece, the hardness observed for the B babbitt is much below normal; it should be about 38. The reason for the low Brinell hardness of this babbitt is probably the fact that it is difficult to prevent the large amount of copper in this alloy from segregating, even when it is kept very hot and stirred continuously. The B formula is almost the same as the genuine babbitt of the Society of Automobile Engineers. It is also similar to the alloy known as Fahrig metal, that is much used for lining aeroplane bearings abroad.
As it is the common belief among mechanical engineers that the addition of even a small amount of lead to a genuine babbitt renders it inferior, similar tests to those described above were run on the A babbitt, to which 1, 3 and 5 per cent, of lead had been added. The addition of 1 per cent, of lead to the A babbitt made a decided improvement in its resistance to deformation at increasing temperatures. Additions of more than 1 per cent, of lead did not increase the hardness in the same ratio.
The results of these tests are shown in Fig. 3, and are in harmony with the observations frequently made by users of babbitt, that when a small amount of lead has been added accidentally to a tin-base babbitt, its hardness and anti-frictional qualities have been much improved.
https://www.youtube.com/watch?v=wZh2VZbqQiI
Effect of Compression on the Brinell Hardness of Babbitts
After a babbitted bearing has been bored out nearly to size, it may next be scraped until an accurate fit is obtained. This is a tedious operation and demands a skilled mechanic; hence reaming or broaching are often used instead of this method. A reamer can be passed through a number of bearings so that they will all be lined up in one operation. Reaming, at its best, however, is a rather violent operation, especially after the reamer becomes dull. Broaches are pushed through the bearing by a hydraulic press until the required dimensions are reached. In the case of large bearings, peening or compressing the babbitt by hammering is often specified. The last two operations, in particular, are supposed to compress the babbitt in a bearing and harden it so that it will give better service. The following experiment was made to ascertain the effect of compression of babbitt on its Brinell hardness.
Two phosphor-bronze plates (Cu, 80; Sn, 10; Pb, 10; P,0.5 per cent.), 2 in. (50 mm.) square by ½ in. (12.7 mm.) thick, were machined all over
one face was then tinned and babbitted with ¼ in. (6.3 mm.) of babbitt, B babbitt being used on one sample and C babbitt on the other. The babbitt was machined to ¼ in. and the samples subjected to a compressive test in the apparatus shown in Fig. 4, so designed that the load would be distributed as uniformly as possible. The successive loads and the corresponding Brinell hardness tests are given in Table 1.
The lead-base babbitt withstood compression better than the tin-base babbitt. When the load was increased to 30,000 lb. per square inch, however, the latter presented the better appearance, as the babbitt had flowed uniformly in all directions over the edge of the bronze square, while the lead-base babbitt compressed more on one side than on the other, and the sample tilted in spite of the rocker device. At a load of 30,000 lb. per square inch, the bronze also flowed appreciably.
These tests show that broaching, peening, etc., do not appreciably increase the hardness of babbitt, and that hardness must be obtained by quick cooling of the lining by water-cooled mandrels, etc.
Microscopic examination of a lead-base babbitt discloses a matrix or groundmass of several eutectics in which are embedded hard cubical
crystals of tin antimonide. These crystals, being relatively low in specific gravity, tend to be more numerous in the upper portion of a babbitt lining. This lack of uniformity is guarded against by pouring a thin lining and chilling quickly. The secret of obtaining good bearings consists in keeping this matrix tough and hard. The same remark applies to the tin-base babbitts, although in these there is less tendency for the tin antimonide crystals to rise to the surface, owing to the lower specific gravity of these babbitts.
Rolling of Babbitted Linings by the Mills Micrometer Roller
As the above test of Brinell hardness of babbitt after compression showed practically no change in hardness, it was concluded that the various methods of finishing babbitted bearings, such as peening, broaching, and reaming, did not improve the hardness of the babbitt. As, after these operations and the final scraping, it is still necessary to make a test run of bearings until the shaft is seated, it seemed possible to introduce improvement in the usual method of procedure. The so-called glass-like surface of old bearings is considered very desirable. Even if the babbitt is no harder than when cast, all inequalities of the surface have been smoothed out and friction has been reduced to a minimum. It occurred to the writer that, by a rolling or burnishing operation, this desirable finish could be given to babbitt linings so that a machine could be operated at full speed as soon as finished, without any trial run.
A tool, Fig. 5, designed by I. Mills, seems capable of doing this work satisfactorily. It was made for securing a better seat for the ball-bearing races of a small aeroplane wireless generator. A variation of 0.0007 in. (0.018 mm.) was found in the bearings, which could not be corrected by reaming or machining. With this tool, the seats in the aluminum alloy end brackets can be rolled to suit the individual variations of the ball bearings. A girl does the rolling, and the bearings can then be inserted or removed with the fingers. If the work is done by reaming, bearings may fit tightly at first, and after having been taken out may be quite loose, because burs, etc., have been removed.
While the Mills micrometer roller has been made only in a very small size as yet, it can be made in larger sizes and would then be capable of exerting much greater pressures. The present instrument is made for a diameter of 1¾ in. (44.5 mm.) and has a range of 5 mils plus and minus. It consists of 10 rolls which can be expanded by a micrometer screw through the medium of two tapered cylinders which give a parallel outward movement to the rolls. The essential feature of the instrument is that the rolls are not equally spaced, as this would cause them to flute the rolled surface.
A trial of this method of rolling babbitted linings is being made on two sets of connecting-rod crank-shaft bearings of the Liberty engine, one set being filled with the lead-base babbitt C, and the other with the tin-base babbitt B. A description of the difficult conditions that are encountered in the bearings of the Liberty engine, due to its great power, are given in a very interesting paper, “The Metallurgist and the Aircraft Program” by Lieut. H. F. Wood, U. S. Army, Signal Corps.
About 16,000 tons of tin is used annually in the production of white metals. The real reason for using the so-called genuine babbitt, which is a high-tin base babbitt, perhaps in the majority of cases, is that tin has always been a high-priced metal and people naturally believe that what they pay a high price for must be good. Mr. Jones has shown that the common metal, lead, is a superior base for most purposes for which babbitt metal is used. The addition of lead is often looked upon as adulterant to genuine babbitt, and specifications for this reason rigidly restrict the lead content.
A sub-committee of the Society for Testing Materials, at the meeting in June, presented tentative specifications on babbitt metal, in which were included twelve formulas, containing from zero to 20 per cent, of tin, and several containing from 65 and 92 per cent. Babbitts containing from 21 to 64 per cent, of tin soften at slightly elevated temperatures, and so are not as good as the babbitt metals that are strictly of lead base and which carry but a small percentage of tin. However, these intermediate babbitts can be cast in very thin sections, owing to their low melting point. Experience has now proved that the very best kind of bearing is one having a bronze back and a very thin lining of babbitt, and the thinner the better. Babbitt metals with a fairly high melting point must be cast rather heavy and afterward machined out; there is a possibility that these intermediate babbitts might be cast thin enough to avoid the necessity for boring and then gotten down to a fine bearing surface by simply reaming or hobbing.
It is not altogether a question of the desire to use a high-priced material, for its fluidity has a lot to do with the adaptability of a babbitt. Tin-base babbitts are quite fluid and you can cover a large area with a rather thin lining. The viscosity of a lead-base babbitt at the pouring temperature is such that it requires skill to pour a thin lining into a bearing that has very much of an area. But if a lead-base babbitt is highly refined, fluid, and properly poured by trained men, you can get a good solid lining, free from blowholes, and in every way equal to the tin-base babbitt lining. The necessary care and supervision are well repaid on account of the difference in price between the lead-base and the tin-base babbitt.
So far Dr. Frary’s alloy of lead, hardened with barium and calcium, has not proved very practical. With bearings of considerable area, the alloy must be poured in sections of about ½ in. (12.7 mm.) in order to get it to run, and the oxidation loss is considerable. If the temperature is kept down to avoid the oxidation loss, there is lack of fluidity. Of course, by reducing the amount of barium and calcium, the fluidity is increased, but you do not get the hardness, and it is necessary to have the hardness also. The first samples submitted were of about 16.5 Brinnell hardness as cast, and hardened, in a few weeks, to about 19 or 20, We asked for material of higher Brinnell hardness but it proved too sluggish to run into thin linings.