Stoping cost is one of the largest of the items comprising the total cost of producing ore. The cost per ton of ore mined is important but may be overemphasized if the more important cost, that per unit of metal recovered, is thereby overlooked. A given stoping method may give a low cost per ton of ore but, by reason of high dilution involving the handling, hauling, hoisting, and treating of a large amount of barren rock, may result in a high cost per unit of metal. Low cost per ton may involve loss of ore or excessive dilution with waste and a low-cost-per-ton method may not, therefore, be the most economical one in a given instance.
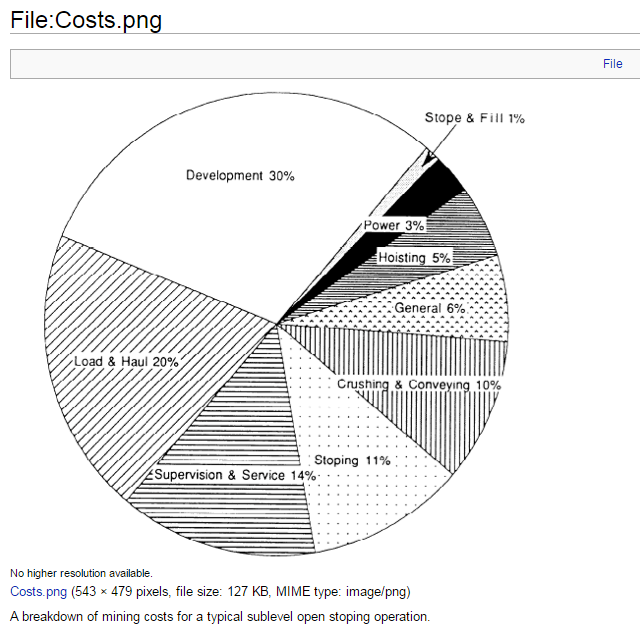
Table 38, giving stoping costs per ton of ore mined, should be considered with the foregoing important fact in mind. The tabulated costs do not include any development, haulage, hoisting, or pumping unless so indicated but are direct-stoping costs only. Wide differences, as between mines, in the distributed costs shown in the tables are partly explained by differences in accounting methods, but the total stoping costs in the last column are believed to be comparable except where otherwise noted.
In figure 119, direct stoping costs are plotted against approximate vein or stoping widths, in feet, for a number of mines employing, respectively, open stoping, shrinkage stoping, and cut-and-fill stoping, and thus indicate the effect of width upon direct stoping cost per ton of ore. High costs in narrow stopes are due principally to reduction in tons broken per foot of hole drilled and hence per man-shift.
Analysis of the curves emphasizes other factors affecting the cost. Thus, at A a high-cost open-stope operation is shown, caused by great irregularity of ore outline, numerous displacements of the ore body by faulting, and mining of much thin ore around the margins. At B, a higher than normal cost may be attributed to the fact that although the stopes are about 25 feet wide, much of the ore is very thin. At SS, T, and T are shown higher than normal cut-and-fill stoping costs. T and T represent mines where the stringer-set-and-fill method, using large quantities of timber, is employed under very heavy hanging-wall conditions that require cautious mining. At SS the higher cost is due to the use of considerable square-set stoping in conjunction with cut-and-fill stoping.
The effect of resuing, involving the breaking of considerable wall rock and resulting in low tonnage per man-shift, and added costs for sorting in the stopes, is indicated by the costs R-R-R.
The points used for determining the shrinkage-stoping curve are seen to be quite erratic in their distribution, few of them actually falling on the approximate mean curve. This may be interpreted to show that with shrinkage stoping, in particular, other factors such as hardness of ore, tonnage mined per month or year (affecting supervisory and other distributed costs), and the physical peculiarities of individual ore bodies affect the costs to an extent that clouds the effects of width. The high cost shown at C is due to irregularity of ore bodies, the use of some cut-and-fill stoping, and the necessity for considerable secondary blasting.
In general, the curves indicate that stoping costs vary considerably with the width for widths of less than about 8 to 10 feet, whereas for greater widths they are influenced only slightly by the stoping width.
Costs of square-set stoping (not shown in the figure) do not appear to be influenced greatly by width of ore, largely because individual stoping rounds usually are drilled to break only one square-set of ground at a time, regardless of the dimensions of the ore body. With caved-stope methods the ore must be wide enough to cave readily, and this usually means that limiting widths must be greater than those at which there is much variation in costs with different widths of ore. Wide ore (or stopes), whatever the method of stoping, obviously makes possible a higher production rate from the mine and thus reduces general and distributive costs. The effect of rate of output upon total unit production costs will be considered later.
Sorting of ore in the stopes adds considerably to the cost per ton if much sorting is required but may result in a reduced cost per unit of metal. Although only rarely is sorting carried to the degree illustrated by the practice at Cold Springs mine, the effect of sorting on the cost per ton of sorted ore and upon the cost per unit of metal is emphasized by the following computations covering practice at that mine.
The cost of sorting 1 ton of $68.64 ore from the run-of-mine product is $1.95. Expressed in another way, the sorting cost per ton of run-of-mine ore is 1.95/6.51 or $0.30. The cost of mining 1 ton of run-of-mine
ore is $2.34. The cost of transporting ore from the mine to the mill on contract is $1 per ton. The milling cost of run-of-mine ore is taken as $2.85 and the cost of milling the sorted product is $3.22 per ton. The mill recovery on the unsorted ore is estimated at 80 percent, and the recovery on the sorted ore is 87 percent.
The profit per ton of ore without sorting is shown in the following calculation:
The profit obtained by sorting is shown in the following calculation:
Therefore, the additional profit obtained by sorting, as based on 1 ton of run-of-mine ore, is 22.37/6.51 or $3.44, and the total profit is 38.32/6.51 or $5.89, as against $2.45 obtained without sorting.
The economical limit of sorting—namely, the amount that can be paid for sorting before the profit will fall below that obtained without sorting—is calculated as follows:
Where $2.45 = profit per ton of run-of-mine ore without sorting,
$3.44 = additional profit by sorting,
$0.30 = cost of sorting per ton of run-of-mine ore (1.95/6.51)
and X = the maximum amount that can be paid for sorting 1 ton of run-of-mine ore.
Then, 2.45 = 3.44 + 0.30 – X
X = $1.29, or the economical limit which can be paid for sorting 1 ton of run-of-mine ore.
The foregoing analysis reflects the importance of sorting when dealing with narrow veins. It should be mentioned, however, that sorting, to be effective, requires careful supervision, as it may result in actual loss if not properly done.
In the above cost analysis of sorting it is assumed that the cost of mining per ton of run-of-mine ore is the same whether or not sorting is practiced. Actually, however, if the waste obtained from sorting were not utilized for support the cost of mining would be appreciably higher if all the run-of-mine material were sent to the mill, because of the necessity of providing support for the stopes.
Table 39 presents stoping costs in terms of man-hours of labor in stopes per ton of ore mined.