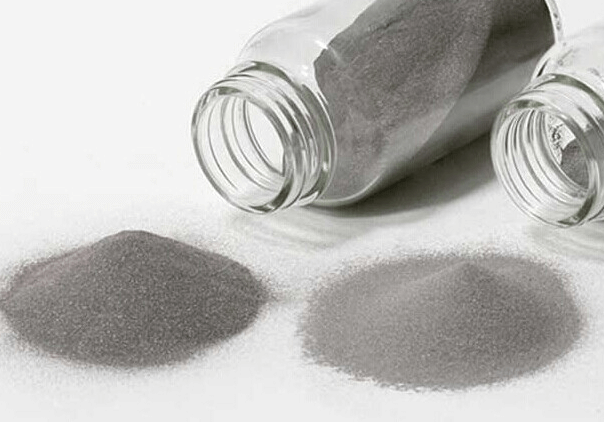
The metallurgy of ores of titanium, titaniferous iron-ores (that is, iron-ores containing a notable amount of titanic acid, TiO2, say not less than 5 per cent., generally 10 to 20 per cent., and frequently more, up to 40 per cent, or thereabout), occur all over the world in immense quantity, “ in mountain masses,” constituting in some localities, as in Sweden, Norway, Canada, the Adirondacks (N. Y.), in North Carolina and other States of the Union, the geological formation itself, the igneous rocks having, in many places, been so permeated with the metallic oxides as to justify their being called iron-ores.
As a rule they are Bessemer ores, quite free from phosphorus and sulphur, though not invariably so. When the percentage of titanic acid is very high, that of the iron is low, but the proportions do not necessarily vary in the same ratio; that is, a rich ore may contain more titanic acid than one lower in iron. The percentage of iron varies, being as low as 35 to 36 per cent, in real ilmenite. It is more generally not less than 50 to 55 per cent., reaching often an average of 58 to 60 per cent., and as high as 63 to 65 per cent.

It is obvious that if these ores were to be considered in the same light as other iron-ores, equally rich in iron, they would form an excellent stock for blast-furnaces for years to come, as their supply might be called inexhaustible, and they could take the place, in part or wholly, of other iron-ores free from titanium, of which the exhaustion, in a comparatively short time, in certain districts can be foreseen, owing to the tremendous demands made on them by our modern monster blast-furnaces. In this sense we are justified in saying that the metallurgy of titanium is one of pre-eminent importance, as it implies the use of these ores, which may justly be called the resources and reserves of the future, when they will be appreciated at their full value, and the prejudices against them will be removed, as gradually they are getting to be. “ The verdict against them,” as has been said by others than ourselves in the discussion of some of our papers on the subject, read before the American Institute of Mining Engineers, “ is unjust, based on entirely insufficient grounds, and far from creditable to the progressive spirit of American metallurgy.”
Generally low in silica, free from impurities, such as phosphorus and sulphur, they are particularly well adapted in the blast-furnace for the production of a stock well suited for the open-hearth process (either acid or basic), which is gradually supplanting, at least competing more seriously with, its rival, “ the pneumatic or converter process.”
Some of the objections raised against the use of these ores in the blast-furnace are so unreliable, so contradictory, so much in opposition to actual facts, that it is really puzzling to find out on what ground they were originally founded.
Opinions in this respect seem to have been taken already made, without any personal control or even desire to ascertain the authenticity, reality or importance of certain statements, and handed down from one to another.
We have not been able to find one metallurgist who could tell us he had used these ores, or that, using them, he had experienced any trouble thereby. They have brought forward the stereotyped objections and rested there: “Sit pro ratione voluntas !”
These objections have appeared in many scientific publications (easily quoted), and often simultaneously with their refutation by actual experiments on the subject. For instance, to mention one of them, it has been stated that the presence, in a blast-furnace slag, of 1 per cent, of titanic acid, or thereabout, was sufficient to render it so infusible as to transcend the heat capacity of the blast-furnace, the slag being so pasty as to render its tapping impossible, or practically so; and still, slags containing 25 to 35 per cent, of titanic acid have been run for over twenty years from blast-furnaces put up in the Adirondack wilderness some fifty years ago, and thousands of tons of such slags, which we have seen and analyzed, form, at the present day, an embankment around the cast-house of the old furnace, of 15 tons daily capacity, still standing as a testimony that this statement as to infusibility of titanic slags cannot in any manner be sustained.
For seven years blast-furnaces have been run in England, at Norton-on-Tees, with ores containing 40 per cent, of titanic acid and 35 to 36 per cent, of iron, making 200 tons of pig-iron per week. Analyses of the slags have been published by the chemist in charge, as well as all the data as to composition of ores, charges in coke, ore and fluxes. The slag contained, on an average, 36 per cent, of titanic acid.
We ourselves have run for several months a small blast-furnace of 3 to 4 tons capacity, put up at Buffalo, to demonstrate the economy of the smelting of this class of ores when properly dealt with. We have tapped hundreds of tons of slags containing 32 per cent, of titanic acid, which ran 50 feet from the furnace perfectly liquid. In crucible tests that we have made in a furnace with “ natural draft,” compounds containing 63 to 64 per cent, of titanic acid were obtained, which we have been able to cast in molds.
We give below an analysis of the slags mentioned above as an illustration :
- Slag run at Norton-on-Tees from Norwegian ilmenite containing 40 per cent, of titanic acid, 35 to 36 per cent. iron. Analysis by chemist in charge. Wm. M. Bowron.
- Slag run in Adirondacks. Average specimen from several hundred pounds of slags picked up from the cinder-bank. Analysis by Ledoux & Co.
- Slag run in the small Buffalo furnace, at the New York Car-Wheel Works, by A. J. Rossi. Analysis by the chemist of the works.
- Compound made in crucible in a furnace with natural draft and poured out in molds. The ores used contained 15 per cent, of TiO2, and on an average 58 per cent, of iron.
Other objections, such as “ titanium deposits ” in the boshes, according to some, in the hearth, according to others, have been advanced against the use of these ores; and to accept the “ sworn testimony ” of some blast-furnace managers in a suit in which we were called as expert, “ ¾ of 1 per cent.,” “ ¼ of 1 per cent.,” mere “ traces ” of titanic acid in an iron-ore, are as sure to produce these deposits as larger percentages. I had been for twelve years technically in charge of the blast-furnaces of Fuller, Lord & Co. (called the Boonton Iron Works). Our ores contained normally from ¾ of 1 per cent, to 1.25 per cent, titanic acid, and never did we observe such deposits in our two furnaces. We did not even at that time attach importance enough to the presence of titanic acid in the ores to determine it in our analyses otherwise than as a curiosity.
As regards larger percentages of titanic acid, the successful and continuous running of the Adirondack furnaces for twenty years, that of the English furnace at Norton-on-Tees for seven years (as attested by a mention of this furnace in a paper read before the British Iron and Steel Institute at their annual meeting), and that of our own small blast-furnace at Buffalo for some months, ought to dispose of these objections, or at least limit them to special cases, as when, by accident, the objectionable phenomena might have been observed in an abnormal and deranged working of a furnace, smelting, possibly unknowingly, a mixture of ores in which titanic acid was present; and it might well be asked whether such derangement was not post hoc rather than propter hoc.
It is well known that obstructions of a similar character, and composed almost entirely of lime, have been observed in the smelting of ores free from titanium. One of these infusible blocks in a blast-furnace was stated to weigh 30 tons. The cause of their formation has been attributed to the excess of limestone charged as flux and of lime in the cinder, very basic silicate of lime being quite infusible per se. In such conditions titanium deposits may have contributed to the obstruction without being the cause of it.
Some twenty-five or thirty years ago the chemist was a luxury in a blast-furnace plant. A good practical rule of thumb was followed with sufficiently constant success with ores varying but little year after year ; but when the demands of industry justified an increase in the number and size of furnaces, and consequently necessitated a more abundant supply of ores, new ores had to be mixed with those generally used; and the presence of titanic acid being likely ignored, as well as the manner of dealing with it properly, fluxes may have been indiscriminately added, causing trouble, and the titanic acid was conveniently made the scapegoat. When we say fluxes, we mean calcite, as, for many years, limestone (calcite) was considered the only admissible or safe flux in a blast-furnace. Indeed, Percy himself, in his admirable and classic book on metallurgy, states that, “ as magnesia increases the infusibility of a slag, dolomite as a flux, instead of limestone, should obviously be avoided.”
This is another prejudice which has lasted for years, and has been exploded only within the last twenty years, or thereabout. As every metallurgist knows now, dolomite is preferable to calcite as a flux, as it increases the fluidity and fusibility of the slag, at the same time removing sulphur fully as efficaciously if not actually better than lime.
Titanate of lime is more infusible still than silicate of lime, and the addition of lime in excess, on general principles, may possibly, with ores very low in silica and containing a large amount of titanic acid in the mixture, have caused the slag to prove less fusible; but we should not forget, however, that a silico-titanate of lime, containing about equal percentages of silica, titanic acid and lime,—“ sphene,” as it is called,—is as fusible in a blast-furnace as any good foundry-iron slag, and considerably more fusible than silicate of lime; so that the presence of titanic acid should have increased the fusibility, if a sufficient amount of silica was present, instead of diminishing it. We may refer to Analysis No. I. of the slags run at Norton-on-Tees as an example.
As to “titanium deposits,” strictly so called, that is, formations of nitrides and cyano-nitrides of titanium of a copper-red color, or of a metallic titanium, as it was claimed by some, they may have been possible in a serious derangement of the working of a blast-furnace occurring under circumstances independent of its presence, and due to causes entirely foreign to it; the titanic acid being then an “ accessory after the deed,” and conveniently assumed to be the principal cause of the mischief.
We have seen in Pittsburg a very fine large specimen of such titanium deposit; it was copper-red and kept religiously under a glass case. But the well-known metallurgist who had it was conscience-stricken, and owned frankly to us that he had had the curiosity to have it analyzed, and that it was found to contain 98½ per cent, of copper. As is well known, for many years, and until the researches of Wohler, it was believed that titanium was a red metal, like copper.
In short, titanic acid, properly dealt with in the blast-furnace, will not necessarily prove the cause of trouble. Slags containing some 35 per cent, of titanic acid will run as fluid as silica slags; and if in an iron-ore the titanic acid be treated as so much silica, and be depended upon and calculated to form one of the principal elements of the slag, with such amount of silica as will be necessarily and unavoidably contributed to the slag by the limestone, the ores and the ashes of the fuel, and if a dolomitic stone be used as flux instead of a calcite, titano-silicates of lime, alumina and magnesia will be found to form a very fluid fusible and good slag, and no titanium will remain in the furnace to cause any trouble in a normal or ordinary running.
It is this addition of dolomite as a flux, instead of calcite, that we have successfully experimented with in our small furnace at Buffalo. (See analysis of slag III.) Both in the Adirondacks (analysis II.) and in England (analysis I.) at Norton-on-Tees, the composition of the slag was different, in this sense, that titanic acid was present to nearly an equal percentage with lime and silica, reproducing practically the composition of the mineral sphene perfectly fusible in the blast-furnace—a silico-titanate of lime.
In England it was obtained by the addition to the ore, of which the composition is given below, of siliceous flux, in the shape of old bricks, besides the calcite addition, considered indispensable at the time.
In the Adirondacks, siliceous fluxes were also added, but they were furnished by the Labrador feldspar, costing nothing, and saving a corresponding amount of limestone. The ore, on average, contained:
We have published on these questions several papers, to which we refer the reader for more complete information. In one of them will be found all the data of the run of the small experimental furnace erected at Buffalo.
We should remark, here, that all that we have said above applies to ores really titaniferous, containing, say, not less than 5 per cent, titanic acid, smelted alone. As to ores containing 1 per cent of titanic acid or thereabout, our practice of twelve years in Boonton, N. J., and that of other furnace-men who bought from us ores like those we used (or similar ones of Morris county, in which the average of titanic acid is from 0.55 to 1 per cent., such as those of the Hibernia mine, Mount Pleasant), and are using yet, cannot leave any doubt that ¾ per cent, to 1 per cent, of titanic acid in the ore mixture can be completely ignored, so far as affecting in any manner the run of the furnaces or the charges.
But, even assuming an inferior limit of 0.50 per cent, of titanic acid admissible in a mixture, it is difficult to conceive why ores from North Carolina and elsewhere, containing 64 per cent, of iron and 5 per cent, of titanic acid, cannot be used to the extent of 10 per cent, in mixture with ores free from titanic acid, since by so doing the mixture would contain only 0.50 per cent, of titanic acid, an amount present in the charges of a number of blast-furnaces we could quote, and immense deposits of excellent ores thus be made available as blast-furnace stock.
But prejudices are difficult to eradicate when they are deeply rooted, even if arithmetic is resorted to demonstrate their fallacy.
There is another objection, more specious than real, which has been raised against the smelting of titaniferous iron-ores, namely, that of the relative economy offered. There is no doubt that, with such ores as were used in England at Norton-on-Tees, and which contained only 36 per cent, of iron with 40 per cent, of titanic acid and 10 per cent, of other gangue (in all, 50 per cent, of barren materials), the addition, as flux, of as much lime and as much silica as there was titanic acid in the ores, there must have been about 4½ tons of slag to melt per ton of iron smelted, and the process may not have proved economical as to fuel; but would it have been any more so with ores free from titanium but containing such an amount of gangue and 40 per cent, of silica ? In the Adirondacks, the ores being much richer and containing so much less titanic acid (15 per cent, instead of 40 per cent.), the addition of rock as flux did not very materially affect the economy; but in our small furnace at Buffalo, as no other flux but dolomite was added (the titanic acid being treated as so much silica), the smelting proved as economical (as the record of the run showed) as that of any other ore free from titanium and containing the same amount of silica as the Adirondack ores contained of titanic acid.
But this question of economy of fuel, even assuming it were real when dealing with such ores as we might contemplate smelting without admixture, that is, rich ores containing a moderate amount of titanic acid, is of but little importance, if, as we shall presently see, the properties of the pig-metal yielded by this class of ores are such that it commands a much higher price on the market than an ordinary good foundry-iron.
It is the consensus of opinion, admitted even by those most obstinate in their prejudices, that the pig-iron smelted from really titaniferous ores smelted alone, or in important proportions with other ores, is “ strong,” “ wonderfully good,” “ a splendid iron,” “ all that can be desired,” for such are the expressions met with at every step when one is referred to the literature of the subject. The iron made at Norton-on-Tees, it is said in the Journal of the Iron and Steel Institute, “ went to Sheffield for armor-plates on account of the toughness that this iron not only possesses but imparts to others in admixture.”
It is essentially an open-hearth stock. Analyses of the pig-iron made by us at Buffalo and that of the Adirondacks (the same ores were used in both cases) showed phosphorus, traces ; silicon, 0.11 to 0.13; carbon, from 1.86 to 3.50, practically all combined; the fracture had very much the appearance of that of steel. It is eminently a chilling-iron, well adapted for car-wheel mixtures. Introduced in such mixtures, not only does it increase the strength of the metal constituting the body of the wheel, but it gives at the tread a deep, strong and hard chill, resisting attrition and shocks remarkably well, as was attested by parties interested in this line of manufacture, and for whom and with whom we have made extensive tests with this special iron.
Briefly stated, the results were as follows: The addition of 5 per cent, of titaniferous pig to a normal mixture for wheels increased the chill on chill-blocks from 1.062 inches to 1.375 inches, and the transverse strength from 3250 pounds to 3775 pounds per square inch. The addition of 10 per cent, of titaniferous pig brought the chill to 1.562 inches, with a transverse strength of 3600 pounds per square inch; and the addition of 25 per cent, of this titaniferous pig, white or mottled white as it was, without affecting the original strength, raised the depth of chill to 1.750 inches.
In another establishment the wheel-mixture showed a tensile strength of 24,500 pounds, and a transverse strength of 2500 pounds per square inch. The addition of 10 to 15 per cent, of titaniferous pig to a cheap grade of foundry pig, showing only 18,500 pounds tensile strength and 1900 pounds transverse, raised the strength to 25,500 pounds and 2780 pounds, respectively, per square inch, with a much deeper chill than in the wheel-mixture, and at a cost of several dollars less per ton.
Strange as it may appear at first, this titaniferous pig-iron does not contain titanium to any important extent. Rarely does it contain more than a few tenths of 1 per cent.; more generally only a few hundredths of 1 per cent. The influence of titanium in the smelting would seem thus to be one of purification, by eliminating obnoxious elements, more than a direct one; but we shall see later on that it is not necessarily always so. Titanic acid is not reduced by carbon at the temperature attained in a blast-furnace, contrary to what happens with silicon. It requires the high heat of the electric furnace to secure such a reduction. If titanium is found in the pig-iron, to some small extent it is due to certain special reactions, possibly to the presence of alkaline cyanides formed in the vicinity of the tuyeres, forming small quantities of cyano-nitride of titanium, which is carried out by the iron, coating it superficially, as has been observed in some furnaces, and giving to the pig-metal a copper-colored hue. This may possibly explain why titanium is found in such small percentages, and why it is not found in the free metallic state in the analysis, but as carbide and cyano-nitride, or both. That titanic acid is not reduced directly by carbon in the blast-furnace, and, if at all, but to a very small amount, seems to be proved by the fact that ores containing as much as 40 per cent, of titanic acid yielded a pig-iron containing titanium 0.00 to 0.03 per cent, (analysis of pig-iron smelted from ilmenite, made at the School of Mines of Paris), while the pig-iron smelted from the Adirondack ores containing 13 to 15 per cent, of titanic acid (TiO2) analyzed 0.07 to 0.12 per cent, of titanium. The conditions of running of the furnace in both cases seem to have had more to do with the reduction, small as it was, than the percentage of titanium in the ores.
The question suggests itself: Since pig-iron smelted from titaniferous ores, though containing but very small amounts of titanium, and that not in the metallic state, but as carbide or combined with nitrogen and carbon as cyano-nitride, what would be the effect of the presence of titanium as metal, in more important percentages, in such products as cast-iron or steel ?
We know that nickel added to steel, to the extent of 3 to 5 per cent., imparts to it valuable properties; that added even to- cast-iron it increases the strength, though at a material increase of cost. We know, also, that chromium and molybdenum have special influences on the properties of steel. Could not titanium, as a metal, impart valuable though different or similar properties ? But since pig-iron does not appear to contain titanium to any available extent, and the amount present is not in the form of free titanium, and since, whatever this quantity may be, it disappears in the process of refining pig-iron for making steel, the only way to secure the presence of titanium to any important extent in pig-iron or steel is to add it to the finished product in the state of alloy, as ferro-titanium, in the same manner as ferro-chrome or ferro-nickel or ferro-manganese is used to incorporate these metals in steel. Such alloys we have manufactured last year by the ton, and of this manufacture we will now briefly speak:
Professor Moissan, in his well-known experiments on the reduction of refractory metallic oxides, has been able to obtain small quantities of metallic titanium by the reduction of purified rutile (titanic acid, TiO2) by carbon, in a lime or magnesia crucible, under the influence of the heat secured by a powerful electric current. Moissan’s method of using a small furnace, with horizontal electrodes, between which the electric arch was started above the materials to be reduced, and not in contact with them, has become classical. But the product obtained contained carbon, and was indeed carbide of titanium for a great part, and had to be purified by repeated treatment with fresh quantities of titanic acid. Such experiments, although of great interest in the laboratory, could not, of course, form the basis for the production of commercial titanium alloys, as the low price of a product is a sine-qua-non of its practical use. Furthermore, titanium carbide, as obtained by Moissan experimentally, on a small scale, and which can be obtained on a larger scale much more easily than the metallic titanium, contains titanium combined with carbon in definite proportions. It has special properties, principally of hardness, which it may impart to mixtures; but however valuable these may be, they are quite different from such properties as could be expected from titanium introduced in a metal (such as cast-iron and steel) in the free metallic state, as is nickel, for instance.
By the method we have followed we have manufactured alloys of titanium and iron containing from 10 per cent, to 75 per cent, of titanium, and either practically free from carbon or, if containing carbon, containing it in the graphitic state; so that the titanium was present as free metal alloyed with iron, and not in the state of carbide.
As the percentage of titanium in these alloys increases, their fusibility diminishes. Thus, 10-per-cent, titanium alloys do not melt at the temperature of fusion of cast-iron and steel, and they are incorporated in the molten mass by a sort of dissolution, just as platinum, infusible at the above-mentioned temperatures, “ will fuse in contact with steel at a temperature at which even the steel itself is not affected, alloying in all proportions with iron,” as shown by the results obtained by Faraday and Stoddart. Ten-per-cent, titanium alloys containing carbon (graphite) present the appearance of a No. 1 graphitic pig-iron, the particles of graphite shining brilliantly through the mass; they are soft under the hammer, forging and flattening, though quite resisting. However, when once torn apart, so to speak, in small fragments, they flatten to such an extent as to admit of their being easily pulverized. The powder, sifted through an 80-mesh sieve, showed by analysis the same percentage of titanium as the solid piece itself, thus demonstrating a very even dissemination of the graphite through the mass. As the percentage of titanium increases, the grain of the fracture becomes closer, the other characteristics remaining the same.
The titanium alloys, free from carbon, are of a silver-white color, exhibiting a coarse crystalline structure, when the titanium is low (about 10 per cent.), the grain becoming finer as the titanium percentage increases. With 35 per cent, of titanium the fracture is that of a solid mass, showing no crystallization, at least to the naked eye. The color is of a dull silver-white when the alloy contains over 45 per cent, to 50 per cent, of titanium.
All these alloys, the carbon alloys as well as the others, are much lighter than cast-iron, their specific gravities varying with the amount of titanium. We have found it to be 5.60 for a 25- to 30-per-cent, alloy free from carbon, and about the same (5.74) for a 10- to 12-per-cent, alloy with carbon; metallic titanium having a specific gravity of 4.87, cast-iron one of about 7.00, and wrought-iron one of 7.788.
It would carry us too far to describe in detail the manufacture of these alloys, and we refer the reader to the article on this subject which has appeared in Vol. IX., Mineral Industry, 1901. We will briefly recapitulate its salient points:
The electric furnace we used was of the well-known type of the Siemens furnace, modified to some extent for our purpose. It consisted essentially of a large block or parallelopiped of agglomerated graphite. A cavity in the block formed the crucible or hearth; and in this cavity, by means of a proper system of chains, pulleys, etc., the vertical carbon electrode, or cathode, formed of one or several carbons bunched together, could be worked up and down. The graphite block was connected at its lower part with one of the terminals of the current and formed thus the anode, while the vertical carbon, by means of flexible cables, was connected with the other pole; the materials to be reduced being charged in the cavity of the furnace, and the vertical carbon lowered to almost a contact, the arc was started through the materials of the charges, and the reduction proceeded until completed. The product could be removed at the end of the operation, or the alloy (when liquid) tapped off.
According to size of cavity or crucible, intensity of current and percentage of titanium desired, we could make from 150 to 250 pounds of alloy in about two hours with about 200 horse-power. When making alloy containing carbon, the charges consisted of the titaniferous oxides mixed with the proper amount of carbon, the materials being used in powder and strongly compressed. Some of the ores used were the Adirondack ores mentioned above, which could yield readily an alloy containing from 12 to 13 per cent, of titanium. By using Canadian ores containing 35 per cent, of titanic acid and about 35 per cent, of iron, we obtained alloys containing as much as 35 per cent, of titanium. The use of rutile—natural TiO2—nearly pure, and containing about 90 to 95 per cent, of TiO2, would, of course, have given us alloys as high in titanium as might have been desired; but, until the late discoveries of special, extensive and geologically interesting deposits of rutile in Virginia about one year ago, its cost, $250 to $350 a ton, excluded its use, from the standpoint of economy. Even now, and though rutile has fallen in price to half of what it was, its price is still considerably higher than that of titaniferous ores high in titanium (40 per cent, of titanic acid), which can be had at the cost of ordinary iron ores.
We have obtained from the Adirondack ore containing 58 per cent, of iron and 15 per cent, of titanic acid (TiO2), or say 9 per cent, of titanium, alloys of 75 to 80 per cent, of titanium by the special method which we have followed,—a sort of igneous concentration, as we call it. The method consisted in submitting in our furnaces a mixture of these Adirondack ores with a quantity of carbon sufficient to reduce the iron oxides, but not the titanic acid, it contained, to a heat but a little higher than that attainable in the blast-furnace, adding to the ore a small quantity of lime or good limestone, so as to form practically, with the titanic acid of the ores, a titanate of lime, with such small amount of magnesia and alumina (or silica) as the Adirondack ores could contribute to the slag. We thus obtained, as a by-product, a titaniferous pig-iron, containing but a few hundredths of 1 per cent. (0.032 per cent.) of titanium and possessing all the valuable properties of the metal smelted in the blast-furnace from this class of ores, and at the same time, as slag, a concentrate of the titanic acid of the ore to the extent of 56 to 58 per cent, of TiO2 (corresponding in round numbers to 33 or 35 per cent, of titanium) with no more iron than is ordinarily met in a blast-furnace cinder, that is, about 2 per cent. Thus, by treating 100 parts of this concentrate as we did the ore, we could theoretically obtain an alloy containing, say, 31 parts titanium, 2 parts iron, or 94 per cent, titanium; or, by mixing it with proper quantities of iron-ore, secure an alloy containing any percentage of titanium desired. But, as we shall see, this concentrate proved of particular value in the making of alloys free from carbon.
All the alloys made with carbon, as reducing agent, contained from 7.50 to 8.50 per cent, of carbon, and occasionally even 9 per cent., of which 0.10 per cent, or less was combined carbon, the remainder graphitic carbon. In order to obtain alloys free from carbon, or practically so, we used a method based on the well-known property of aluminum to reduce metallic oxides. This property has formed the subject of many experiments in the laboratory for over fifty years; but it has been considered necessary, for success, to use the aluminum in the form of an impalpable powder, and to mix it, in that state, with the powdered oxide to be reduced.
In recent years Dr. Goldschmidt has succeeded in utilizing industrially, to a certain extent, the reducing power of aluminum in pulverulent form. His method consists, after having mixed intimately together the powdered aluminum and the powdered oxide, in placing in the mass a primer formed of powdered aluminum and an oxide capable of readily yielding a portion of its oxygen, such as sodium or barium peroxide, and starting the primer itself by igniting an inserted ribbon of magnesium. The heat of formation of alumina (in the primer), the aluminum oxidizing at the expense of the oxygen of the oxides, is so intense that, by contiguity, it is imparted to the whole mass, and the reduction proceeds instantaneously, so to speak, often tumultuously and dangerously so, without the intervention of any external heat. It is not for us to discuss the value of this process any further than to say that the rapidity of the reaction itself creates in the metal or alloy obtained a certain uncontrollable amount of aluminum which cannot be removed without a remelting of the product, and that some of the materials of the vessel in which the operation is carried on also pass into the product—silica, if a clay vessel be used; carbon, if a graphite one be resorted to; it cannot be claimed that strictly pure alloys or metals are produced. But the main drawback to its industrial use on a large scale, aside from the manipulations required, is the original cost of the aluminum in powder, which is several times that of aluminum in ingots or scrap.
We have found that it is not necessary to use the aluminum in powder to secure the reducing action, but that if a bath of aluminum be maintained at the proper temperature, in an electric furnace, for instance, like the one mentioned above, the metallic oxides (in this case the titanic acid and the iron oxides charged in the bath) will be reduced, the temperature rising from the heat of formation of alumina to such an extent as to allow the moderation of the external source of heat first applied until the reduction is complete, or nearly so. The metal or alloy obtained can then be kept liquid by increasing the intensity of the current before being tapped, and easily deprived, by a fresh addition of oxide of iron, of the aluminum it may contain, or, by proper additions, of any other impurities it may be considered desirable to remove.
Furthermore, in the Goldschmidt process, if titaniferous iron-ores are used as raw materials, the amount of powdered aluminum to be added must be such as to reduce also the oxides of iron, which is paying rather dear per pound of iron reduced (as it requires nearly one-half pound of aluminum per pound of iron), and if rutile be used, then its price comes in as a very important factor.
By using, in starting, the titanic concentrate mentioned above as containing about 30 per cent, of titanium and only 2 or 3 per cent, of iron, we have to add aluminum to reduce the titanic acid only, and if lower alloys are wanted, dilute, so to speak, the high alloy obtained, in a bath of iron. In this way we have manufactured alloys of titanium containing from 10 to 75 per cent, of titanium and from 0.10 to 0.60 per cent, of carbon, or thereabout, at a cost not materially higher than for carbon alloys.
In the tests we have made of the titanium alloys for seasoning cast-iron, we have invariably used the carbon alloys, and, by preference, alloys containing 10 to 13 per cent, of titanium. In an experiment with steel we have used the alloys reduced with aluminum and practically free from carbon.
We have added the carbon alloy to cast-iron in the crucible in lumps; in the ladle in small pieces or in powder; in the cupola in large lumps, and also in powder, and the results have been practically the same. An addition of 2 to 3 per cent, or thereabout of a 10-per-cent. titanium alloy appears to be amply sufficient to secure such results as an increase of 20 to 30 per cent, in the tensile strength of cast-iron, and proportionately as much in transverse strength. Results of such tests have appeared in papers read by us before the American Society of Mechanical Engineers (Milwaukee Meeting, May, 1901, Vol. XXII. of Transactions) and at the Annual Meeting of the American Foundrymen’s Association, June, 1901, Buffalo (Vol. X., Transactions, Part I.), to which papers we refer the reader.
Since then we have made other equally successful tests in different establishments, car-wheel works and others. We will briefly recapitulate them:
In general, the results of tests of 100 square bars 1 by 1 by 12 inches between bearings, and round bars 1 1/8 in. in diameter by 18 inches in length, or thereabout, showed that by adding in the cupola, in good-sized lumps, 3 per cent, of a 10-per-cent, alloy, or the same amount in powder in the ladle, we could bring the original strength of a good No. 2 coke-iron, showing 24,500 pounds tensile and 2450 pounds transverse strength per square inch, up to that of an excellent Scotch charcoal pig-iron or higher (in fact, 28,800 pounds tensile and 2900 pounds transverse); and that by a similar addition of alloy to this Scotch charcoal pig we could bring the strength to some 32,500 pounds tensile and nearly 3300 pounds transverse strength. As the price of this charcoal pig-iron was $29 a ton, while that of the coke-iron was $15 at the time, and as they were used in mixture for special foundry purposes, it is clear that a mixture of the coke-iron treated with the alloy and of the coke-iron itself not treated could be used with great advantage as to cost of mixture for the same strength secured; the addition of the alloy to the extent mentioned to the coke-iron increasing the cost of the latter but a fraction of the difference of prices ($15 and $29) between the two original pig-irons.
Our tests with steel have so far been limited to crucible steels, and enough has been observed to show that the influence of titanium, introduced into steel in the metallic state, has been to increase considerably the ductility, as proved by the remarkable elongation, contraction of area and limit of elasticity observed in high-carbon steels containing 1.25 per cent, and even 2 per cent, of carbon. The quantity of titanium found in the steel by analysis varied from 0.89 per cent, and 1.01 per cent, to 0.10 per cent. As the effect of even such small quantities as the latter (0.10 per cent.) was very marked, and as, in these cases, 0.10 per cent, did not represent what could have been expected from the addition of the alloy, the question arises : Has not titanium, when thus added to steel, an indirect action besides a specific one ?
It has been suggested that, in the same manner as manganese removes oxygen from steel in the Bessemer process, and also in the open-hearth and even in crucible steel, titanium may act not only as a deoxidizing agent, much more powerful still than manganese, but may also remove from the steel the nitrogen it undoubtedly contains, and which has an unfavorable influence on its strength. (The odor of ammonia so noticeable in the open-hearth process proves the presence of nitrogen very decidedly ; and as is well known, titanium burns in nitrogen at 800° C. with incandescence, just as iron burns in oxygen.) If this is so, a use for the alloy, even when containing carbon, might well be found in the open-hearth as also in the converter, since it could be used as a recarburizer, on account of the high percentage of carbon it contains; as a deoxidizer (with or without ferro-manganese); and as a denitrogenizer, so to speak; and, in the case of small converters for steel castings, the heat of formation of titanic acid, which is much higher than that of silica, would prove of advantage in raising the temperature of the bath even were but a small percentage of titanium to remain ultimately in the finished product. If by such use open-hearth and converter steel could be so improved as to compare better as to strength with crucible steels, and the latter be also improved to the extent it appears to have been in our first tests, there would be opened for these alloys a large field of usefulness, and for these titaniferous ores a very important application.
In tests made in some establishments we have used simultaneously the titaniferous pig and the alloy in the cupola, with such a resulting toughness combined with a remarkable hardness and strength of chill in car-wheels that it has justified the statements of some manufacturers as to the importance of these products in the iron industry, when better known. To obtain them cheaply—and we mean by that at such a price that their use would prove economical in view of the results secured—has been our aim.
We may remark here, that if the thickness of a casting can be diminished without impairing its strength—on the contrary, leaving it stronger—the cost of the material which has secured such a result may well be compensated for, and more, by the advantages obtained.
We are continuing our tests along these lines for different establishments, and we may be justified in saying, as a conclusion, that if these tests and those carried on by outside parties (to whom we are willing to extend all facilities to make them), justify our claim, as those already made have done, the importance of the metallurgy of titanium cannot be ignored or overlooked much longer, and that these titaniferous ores, as we said at the outset, will constitute a valuable resource and reserve for the future, both for blast-furnace stock for the manufacture of pig-iron and for metallurgy in general for the production of valuable alloys. Titanium may be found to form alloys with other metals than iron, or with iron and other metals possessing special and valuable qualities. We have had no trouble, by following our aluminum method, in making alloys of titanium and copper, as well as ferro-tungsten, ferro-chromium, ferro-molybdenum (practically free from carbon), and compound alloys of chromium-titanium-iron, etc., of which we are now studying the properties.