This Conkling Jig (ore-concentrating machine or jig), as it is called, is not entirely unknown, having been used at several places with more or less success; but as yet, I believe, no drawings of it or records of its work have found a place in print. Although the jig will be found to be merely an adaptation of old forms, there are several points which deserve attention, particularly the method of central discharge, of freeing the bearings from grit, and the rotation of the sieve or screen.
The ore-body at Lyon Mountain Iron ore mine consists of a bed of rather compact, granular magnetite, occurring in a gneiss formation. The side walls of the ore-body are not sharply defined, the ore on either side becoming gradually poorer as the distance from the central point of the body increases. It is this lean ore, which, before the introduction of the jigs, was thrown away as waste, that is now concentrated. The material treated consequently consists of magnetite, intermixed with the component parts of gneiss, viz. quartz, felspar, hornblende, and mica. Grains of trap also form part of this material. These come from dykes of trap, which cross the ore-body at intervals.
The ore which is to be concentrated usually contains from 30 to 40 per cent, of metallic iron. It is first crushed to the size of two inches, or less, by two large Blake crushers. The material from these crushers passes by a chute lined with screens, having holes ¾ inches in diameter, to a second set of four crushers, set so as to close to one inch. The product from this set of crushers, together with that which passes through the screens in the shute, is then taken by an elevator to the top of the mill, and passed through a revolving screen, perforated with ¼ inch holes. The ore which passes through the screen goes to the jig-hoppers ; that which passes over goes to a third
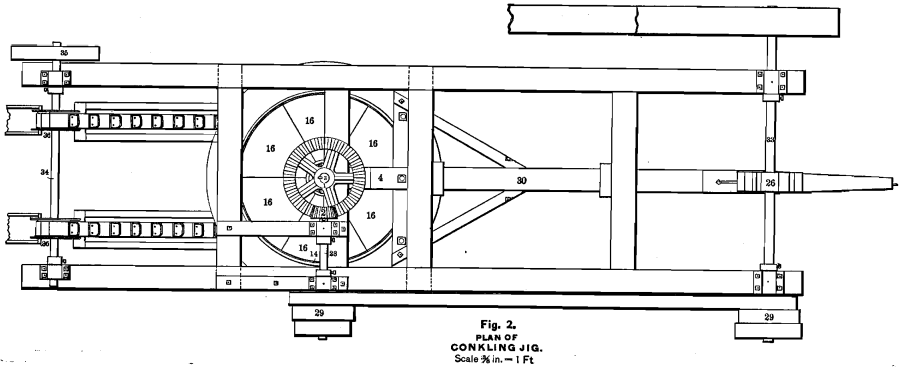
set of six crushers, set to ¼-inch. These are of the Blake multiple- jaw pattern, having three jaws.
The product from these third crushers is again screened through a double revolving screen, having holes ¼-inch in diameter. That which passes through goes to hoppers; what passes over goes to a fourth set of crushers. These are of the Blake multiple-jaw pattern, having six jaws, which are set so as to close to ¼-inch. The product from these last crushers is again screened, and the grains which are still too large pass again through the final crushers. All the material which passes through the ¼-inch holes goes to the jigs without further sizing. The ore is crushed dry, and goes to the jigs in that state.
The machine, as shown in the accompanying drawings, may be divided into four essential parts: 1. the frame; 2. the tub; 3. the jig; 4. the elevators. For the better understanding of the drawings, the following index of the names of the parts is appended, the numbers referring to corresponding numbers in Figs. 1 and 2.
Frame
The frame, which is shown in vertical section and elevation in Fig. 1, in plan in Fig. 2, and in horizontal section in Fig 3, is made of squared spruce or hemlock timber, 6½ x 6½ inches, and braced by cross-bracing, 3×4 inches, at the sides and ends. The upper string-pieces project 4 feet 5 inches beyond the first pair of uprights. The sills are 13 feet 8½ inches long and project 6½ inches beyond the front and rear uprights. The second pair of uprights is placed 3 feet 9 inches behind the first pair. The frame
is 4 feet 1 inch wide inside. There are an upper and a lower-cross piece at each pair of uprights except the rear, where the cross-piece is placed 3 feet 8 inches from the rear end of the string-piece. To the lower side of this cross-piece is attached the bumper for the lever- beam. The main driving-shaft is placed directly over the rear uprights ; and 9 inches from the forward end of the string-pieces is placed the shaft for the elevator-pulleys. Between the first and second cross-pieces is a cross-beam which carries the journal for the upright or jig-shaft. The front edge of this timber is set even with the centerline of the jig. From this timber to the forward crosspiece extend two timbers, 4×6 inches, as shown in Fig. 2, which
carry the boxes for the pinion shaft. To the second and rear cross pieces are bolted pieces 3×9 inches, and 2 feet high, which carry the spring-pole. On the front of the second pair of uprights 1 foot 6½ inches (to center) below the string-piece, are the journals which carry the lever-shaft. The whole is framed with mortise- and tenon- joints, and tied together with 1 inch bolts.
Tub
The tub is made of yellow pine 4 feet 11 inches inside diameter. The staves are 4 feet 8 inches high, 5 inches wide and 2 inches thick, rabbeted 1 inch deep, 3 inches from the lower edge, to receive the bottom. The staves are not dowelled. A door in the side having bevelled edges gives access to the interior. Four iron bands provided with tighteners binds the whole together. A hole near the bottom fitted with a plug serves to empty the tub for the
purpose of examination or repairs. The tub is set between the first and second pair of uprights, as shown in the drawings. Two troughs to allow for the passage of the elevator belt and buckets into the tub are let into the front side.
Jig
The jig consists essentially of a circular sieve, suspended from one end of a lever, being moved up and down by a cam striking the opposite end of the lever. The concentrates pass through the sieve to the bottom of the tub; the tails pass out by means of an annular opening around the jig shaft. The general arrangement is shown in Fig. 1. The parts are shown in detail in Figs 4, 5, 6, 7, 8, 9, 10, 11 and 12.
The spider (Fig. 4) is made in one piece of cast-iron, with a taper bore to receive the jig-shaft which is keyed into it. It is also supported by the standards from the flange, which may be moved by the upper and lower nuts. A sheet-iron hoop, 12 inches high, is bent around the spider, and fastened by the holding-down bands which are riveted to the rim, pass through the holes in the end of the arms, and are fastened below with nuts. The screen-plates rest on the arms of the spider and are held in place by U-bolts passing under the arms and through the holes in the screens. The screen-plates are ½ inch thick, made of cast-iron, in segments of 1/6 of a circle; the holes are 5/16 inch in diameter on top and 7/16 inch below.
Beneath and bolted to the spider is the cone (Figs. 5 and 20, Fig. 1) under that is the water-sleeve (Figs. 6 and 21, Fig. 1) which slides up and down in the water-box (Figs. 7 and 22, Fig. 1). This water- box, and also the lower elevator-box (Figs. 9 and 23, Fig. 1) are the inventions of Mr. William Hodson, Superintendent of the mill at Lyon Mountain. All the water which is to be used in jigging passes through these two boxes, and flowing out through the annular openings, keeps the bearings free from grit. Previous to the introduction of these improvements, the water-sleeve would wear out in a very short time. The water, under pressure of 8 feet head, enters through the 3-inch pipe (41, Fig. 1) provided with a valve (42) to regulate the quantity.
The jig is suspended in the tub from the end of the lever-beam (30, Fig. 1). The trunnion-piece (Figs. 11 and 7, Fig. 1) is kept in place by the upper and lower collars which are provided with set screws. The links (Figs. 11 and 5, Fig. 1) connect the jig with the lever-beam. The jig-shaft (Fig. 8) passes up through the horizontal bevel-gear wheel (1, Fig. 1) by which it is rotated ; the shaft moves freely up and down, but is provided with splines in which fit keys attached to the gear-wheel. The pinion is driven by belt from the rear driving-shaft (33, Fig. 1). The pulleys to transmit the rotary motion are conical, reversed in order to change the speed. The cam-wheel (Figs. 10 and 26, Figs. 1 and 2) is provided with six cams, and is keyed to the shaft which is driven by a belt 8 inches wide, passing over the 36-inch driving pulley (27, Fig. 1). The cam-wheel makes 43 revolutions per minute, giving about 260 jars per minute
to the jig. The lever-beam is set to move the jig up and down about 3/8 inch, giving a slow up- and a quick down-motion. The jig makes seven revolutions per minute.
Elevators
The lower elevator-box, shown in detail in Fig. 9, is provided inside with wooden bearings. The box is bolted firmly to the bottom of the tub. The elevator-pulleys (Fig. 12) overhang somewhat, to give free exit to the water which passes through the box. The elevator-belt is rubber, 4 inches wide, and the buckets are riveted to it. The elevators travel at a speed of 10 feet per minute.
Jigging
The crushed ore is brought from the hoppers to the jigs by chutes provided with gates at the lower end, just above the screen plates. The screens are first covered closely with pieces of heavy ore about the size of hickory-nuts; the crushed ore is then spread over this until it is level with the collar of the spider, about
2½ to 3 inches deep. The spring-pole is connected with the lever-beam by the strap, the water turned on, and the jig started. The
water flows upward through the screen-plates and over the collar of the spider, carrying the gangue to the tail-race; the ore settles through the screen, is collected at the bottom of the tub, and thence raised by the elevators to bins. The rotation of the jig produces an equal distribution of the crushed ore on the screen-plates, and also forces the particles to traverse a path longer than the radius of the sieve. The crushed ore is allowed to fall on the screen as near the outer periphery as possible.
The jig has a capacity of treating 5 tons of ore per hour, requiring 135 gallons of water per minute, or 1620 gallons per ton treated. One man or boy is sufficient to attend to two jigs, his duty being to see that the jig is properly supplied with material to secure a uniform depth on the screen ; that the water is flowing in the proper quantity (a depth of ¼ to 3/8 of an inch over the collar being suffi-
cient), and that the concentrates are free from gangue. If there is too much gangue in the product the attendant lets out a hole in the strap from the spring-pole to the lever-beam, to make the shock less violent.
An examination of the bed on the screens during the process of jigging showed the ore lying just above the screen, the greatest depth and largest pieces being near the edge of the screen, gradually thinning out and becoming finer toward the center of the jig, the gangue increasing in depth toward the central point of discharge.
An analysis of samples, taken on October 10th, 1887, gave the following results, the samples being analyzed for iron only :
which shows a saving of only 47.4 per cent, of the iron contained in the stock.
The chief impurity contained in the concentrates appears to be silica in fine grains. An examination of the tailings shows the lost ore principally in two forms: very fine ore or “slimes;” and small particles of ore imbedded in the larger pieces of gangue. The causes of this loss may be summed up as follows:
- The material is delivered to the jigs dry; hence the fine ore, almost in the condition of dust, is carried over into the tail-race on the surface of the water.
- There is no classification according to size; and the ore, being friable, is crushed finer than the gangue. Hence, without sizing, there is not sufficient difference in the falling-time between the fine ore and the coarse gangue to produce a good separation, and fine ore goes over with the gangue into the tailings. A larger saving would probably be effected by a sizing into at least two classes; still, this would not save the ore which is lost through being embedded in the grains of gangue.
- The loss last noted is due to the fact that the material is not crushed fine enough to free the ore from the gangue. The remedy is, of course, a finer crushing; but this would produce a larger percentage of fine ore or slimes, which is not desirable.
A better arrangement for treating this class of ores with this jig would probably be as follows:
- A wet crushing with stamps, say to the size of ¼ inch. The Ball steam stamp would probably work well in this connection, and produce a smaller percentage of fine ore than dry crushing.
- A first jigging on a set of jigs arranged for this size, practically like those at Lyon Mountain.
- A screening of the tailings from first jigging by a screen with 1/8 or 3/32-inch holes. The material above that size to be recrushed, either by being sent back to first stamps or by a second stamp.
- A second jigging of the tailings from the first jigging which pass through the 1/8- or 3/32-inch screen.
If it may be supposed that the second jigging will be as perfect as the first this arrangement will probably result in the saving of an additional 20 or 25 per cent, of the iron contained in the stock.
The economical practicability of this arrangement may be questioned on the ground of expense, taking into consideration the comparatively low price of the product obtained. As I have no means of knowing either the cost of treating per ton of material, or the price obtained for the product, I must leave this point in doubt.
There seems to be considerable room for improvement in the arrangement of the jig. As it now is it is a somewhat clumsy arrangement, and occupies a space 10 x 24 feet (allowing 2 feet of working space around the frame). This could easily be reduced to 10 x 10 feet by doing away with the lever, spring-pole, etc., and giving the motion to the jig-shaft by means of a cam working on a horizontal shaft just back of the jig-shaft. The spring-pole could be replaced by a coil-spring on the vertical shaft, with an adjustable nut to regulate the jar. A suitable bumper could be arranged either above or below the bevel-gear wheel. The action of such an arrangement would be similar to that now produced, with the advantage of economy of space and material.