DESCRIPTION
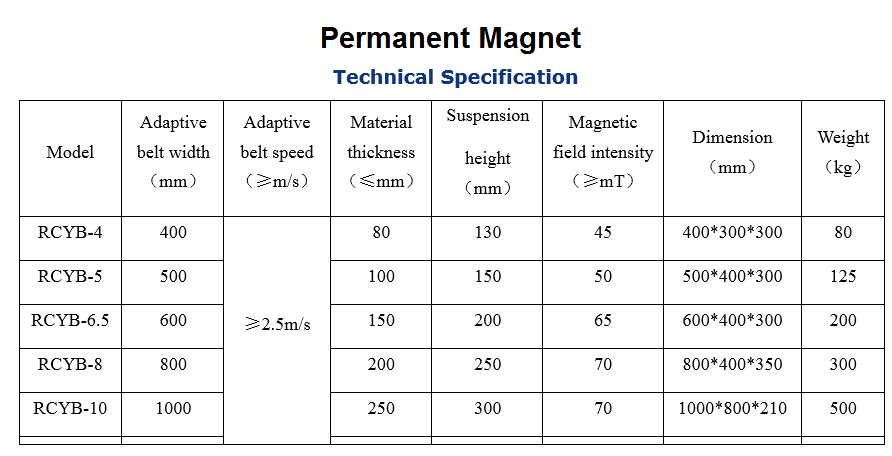
HOW TO REMOVE TRAMP IRON FROM BURDEN CARRIED ON CONVEYOR BELT
Advancement in automation intensifies the need to remove tramp iron from bulk materials being processed and carried on belt conveyors. Although magnets have long been employed for this purpose, it becomes increasingly necessary that magnetic equipment of appropriate types and sizes be selected and advantageously installed – if maximum benefits are to be derived.
Tramp iron present in bulk materials consists of ferrous trash, such as wire, bolts, nails, equipment parts, tools, and machine cuttings. The results, if the iron is not removed, are damaging to equipment having close clearances, explosions, or fire, in the case of flammable materials, production downtime losses, and contaminated products.
Approximately 70 per cent of the magnetic, separators used for tramp iron removal in heavy industry are best installed in conjunction with belt conveyors. Here, the materials are usually opened up, or spread evenly and sufficient room exists to accommodate the installations.
For removal of heavy or medium sized tramp iron from relatively dry and porous material having a burden depth, not more than 25 per cent of pulley diameter, and with belt speed not exceeding 200 feet per minute, first consideration should be given to a permanent magnetic head pulley. Permanent magnetic pulleys are available with consistent magnetic fields greater than electromagnetic pulleys in small diameter sizes and comparable to electron in many other sizes.
For removal of small tramp iron .from dry and porous material, burden depth should be kept at 2 inches maximum, or preferably less, with belt speed within a range of 100 to 200 feet per minute, depending on pulley diameter. It is far more difficult to remove small tramp iron than medium or large sizes due to its slight mass and inability to “fight” its way through material burden to the magnet.
One big advantage of magnetic head pulleys – both permanent and electro – is their continuous self-cleaning feature. As tramp iron is separated, it automatically drops behind a divider plate into a chute or container. However, magnetic pulleys should not be considered for processing sticky materials that require a scraper on the underside of the belt to prevent product carryover, as tramp iron will be scraped off along with the product.
The real separation work horse for heavy industry’s faster belt speeds and greater burden depths is the suspended electromagnet a double air gap, rectangular type, made specifically for tramp iron removal. Air-cooled, compound-filled, and oil-filled designs are available. They can be incorporated in cross-belt or in-line, self-cleaning units which continuously and automatically discharge iron collected by the magnet.