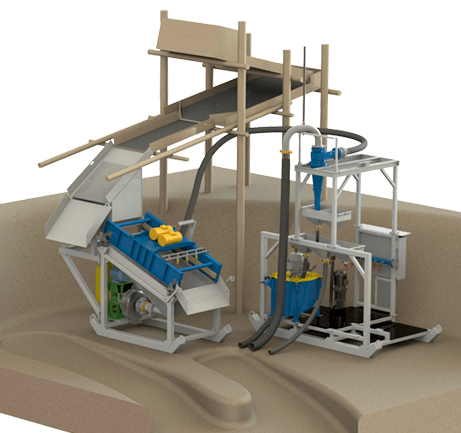
Flour gold can be defined as ultra-fine gold found in a low micron size fraction, often smaller than 74 microns or 200 mesh. Reality is that with today’s fine gold recovery equipment, this is a low ways away from the elusive microscopic gold small prospectors want to know how to recover. Falcon’s iCon gravity concentrator, in conjunction with a conventional shaking table, can recover in excess of 85% of GRG gold. A screen analysis of the gold particles has show test samples with as much as 44% of the gold in the -74 microns (-200 mesh) size range. High metallurgical efficiencies of concentration within the size ranges of 1.5 mm (-10 mesh) to about 37 microns (-400 mesh) allows recoveries of trace quantities of contained high specific-gravity minerals from what would otherwise be “plant tailings”.
The iCon i150 and i350 are, for a small miner, high capacity gravity concentrator designed for feed throughputs of 1 to 15 TPH, for feed material finer than 2 mm (-10 mesh) in size. The high-G cones operate at feed pulp densities of 60% to 65% solids (by weight) and as low as 5%, with have excellent recovery efficiencies for high specific gravity minerals down to about 37 microns (-400 mesh). The only moving part of this fine gold recovery machine is the spinning cone concentrator. Material flows through the cone by gravity, and the concentration of the heavy minerals is achieved by stratification in the flowing pulp. The high feed pulp density reduces the turbulence of the pulp flow, and allows the gold particles and other heavy minerals to stratify very efficiently. Removal of coarse particles (+2 mm) from the feed reduces the turbulence and disturbance factors in the flowing pulp, enhancing the separation of the high specific gravity minerals. The internal flows of the cone system allows repeated upgrading of the concentrate products as well as retreatment (scavenging) of the “tailing” streams before the final discharge of products from the cone. The concepts incorporated in the cone greatly enhance the chances for recovery of the high SG particles into the concentrate product compared to other sluice-type devices.
Recovering Flour Gold
Some gold deposits have been documented to have fine flour gold with a diameter-to-thickness ratio of about 10:1; a 200 mesh particle could therefore have a diameter of about 74 microns, and might be about 7 microns thick.
Small deposits of relatively high-grade values have been mined successfully by individual miners, but production-type commercial operations have not been successful. Equipment did not exist which could process substantial volumes of material and achieve significant recovery of the gold values.
Common installation of small gravity concentrators in a placer gold recovery system come in as equipment installed as “add-on” to an existing aggregate plant. The small aggregate operation, using semi-portable crushing and screening equipment, had a low throughput on bank-run gravel. The gravel, mined with a front-end loader, was crushed and washed through the shaking screens to produce several sized fractions. The smallest size, containing the gold values, was a nominal -3/8″. The fine gold recovery system was installed to treat the -3/8″ fraction.
The gold recovery circuit consists of two static DSM-type screens to remove the +0.83 mm product from the -3/8″ circuit feed, two hydrocyclones to densify the screen undersize (-0.83 mm), the gravity centrifugal cone concentrator, and a single-deck full-size shaker table.
The iCon concentrators are high-capacity gravity concentrators designed for throughputs of 25 to 300 tons per day solids. The attractive features of those fine gold recovery devices include: the high-volume, low operating costs of the units; generally speaking, low tonnage systems have not considered incorporating cone concentrators into the circuit design, as other conventional equipment was available for handling low tonnages.
To obtain sufficient pulp volume within the cone, a high recirculating load is maintained. The circulating load, in addition to providing proper loading within the cone system, tends to buffer variations in about 2 tons per hour, produces concentrate at a rate of about 0.1 to 0.2 tons per hour. The cone concentrate is gravity-fed to the RP4 shaking table. The table concentrate, containing the black sands and fine gold, is fed to a small amalgamation drum for recovery of the gold. The black sands are stock-piled for further treatment, if required. The table tailings are recirculated back to the cone feed circuit. Tailings from the fine gold recovery circuit consist of the -3/8″, +0.83 mm screen oversize, the iCon tailings, and the overflow from the densifying cyclones. Only trace quantities of gold have been detected in the circuit tailings.
The Flour Gold Recovery in some circuits have been calculated to be in excess of 85%, based upon the known values in the bank-run gravel and the quantity of bullion recovered. Metallurgical balances of the circuit are difficult as the quantity of gold in the tailings is too low for accurate analysis.
A sample of black sand concentrate and gold was collected from the shaking table and subjected to laboratory flotation tests to produce a clean gold concentrate. A screen analysis was made on the gold concentrate to determine the size distribution of the gold particles.
The gold particles are flat and very thin. The figures above reflect the largest dimension of the particles.
The plant described has proven to be economically and metallurgically successful. The aggregate plant and fine gold recovery system are operated with only two men; one operates the front end loader, and the other operates the plant. Gold recovery has been sufficient to operate the plant solely for recovery of flour gold.