Table of Contents
In many industries the final product, or the raw material at some stage of the manufacturing process, is in powdered form and in consequence the rapid and cheap preparation of powdered materials is a matter of considerable economic importance.
In some cases the powdered material may be prepared directly; for example by precipitation from solution, a process which is used in the preparation of certain types of pigments and drugs, or by the vacuum drying of a fine spray of the material, a process which is widely adopted for the preparation of milk powder, soluble coffee extracts and similar products. Such processes are, however, of limited applicability and in by far the greatest number of industrial applications the powdered materials are prepared by the reduction, in some form of mill, of the grain size of the material having an initial size larger than that required in the final product. These processes for the reduction of the particle size of a granular material are known as “milling” or “grinding” and it appears that these names are used interchangeably, there being no accepted technical differentiation between the two.
Why is Ore Grinding Necessary
The reasons for the grinding of industrial materials are numerous but the principal reasons may be summarized under the following headings:
- The liberation of an economically important material from the un-required constituents of a mixture.
- The exposure of a large surface per unit mass of material in order to facilitate some chemical process.
- To reduce the material to the desired form of the final product.
- To satisfy market requirements.
Examples of the first two classes occur in mineral dressing, in which size reduction is used to liberate the desired ore from the gangue and also to reduce the ore to a form in which it presents a large surface to the leaching reagents.
Under the third heading may be classed many medicinal and pharmaceutical products, foodstuffs, fertilizers, insecticides, etc., and under the fourth heading falls the size reduction of mineral ores, etc.; these materials often being reduced to particles of moderate size for ease in handling, storing and loading into trucks and into the holds of ships.
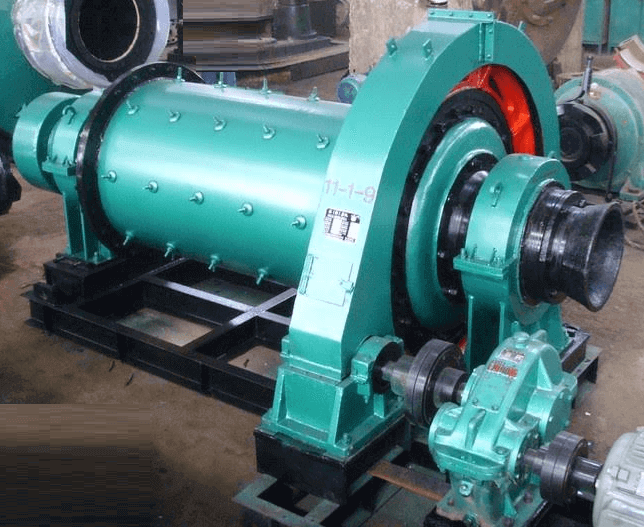
The quantity of powder to be subjected to such processes of size reduction varies widely according to the industries involved, for example in the pharmaceutical industries the quantities involved per annum, can be measured in terms of a few tons, or in the case of certain drugs, possibly a few pounds; whereas in the cement industry the quantities involved run into tens of millions of tons; the British cement industry alone having produced, in round figures, 12½ million tons of Portland Cement.
For the preparation of small quantities of powder many types of mill are available but, even so, the ball mill is frequently used. For the grinding of the largest quantities of material however, the ball, tube or rod mill is used almost exclusively, since these are the only types of mill which possess throughput capacity of the required magnitude.
Thus, it is the extremely wide range of applications, and the great industrial importance, of the mills which constitute the “tumbling mill” family which forms the justification for the present work.
The great range of sizes covered by industrial ball mills is well exemplified by Fig. 1.1 and Fig. 1.2. In the first illustration is shown a laboratory batch mill of about 1-litre capacity, whilst in Fig. 1.2 is shown a tube mill used in the cement industry the tube having a diameter of about 8 ft and length of about 45 ft.
![]() |
![]() |
In Fig. 1.3 is shown a large ball mill, designed for the dry grinding of limestone, dolomite, quartz, refractory and similar materials; this type of mill being made in a series of sizes having diameters ranging from about 26 in. to 108 in., with the corresponding lengths of drum ranging from about 15 in. to 55 in.
At this point it is perhaps of value to study the nomenclature used in connection with the mills under consideration, but it must be emphasized that the lines of demarcation between the types to which the names are applied are not very definite.
Common Types of Grinding Mills appears to be:
- Ball mills.
- Tube mills.
- Rod mills.
- Ρebble mills.
Ball mill
The term “ball mill” is usually applied to a mill in which the grinding media are bodies of spherical form (“balls”) and in which the length of the mill is of the same order as the diameter of the mill body; in rough figures the length is, say, one to three times the diameter of the mill.
Tube Mill
The “tube mill” is a mill in which the grinding bodies are spherical but in which the length of the mill body is greater in proportion to the diameter than is the case of the “ball mill”; in fact the length to diameter ratio is often of the order of ten to one.
Rod Mill
The rod mill is a mill in which the grinding bodies are circular rods instead of balls, and, in order to avoid “tangling” of the rods, the length to diameter ratio of such mills is usually within the range of about 1·5 to 1 and 5 to 1.
Pebble Mill
The pebble mill is the name associated with a mill in which the grinding bodies are natural pebbles or possibly ceramic bodies; the general proportions of the mill being as for a “ball mill”.
It will be noticed that the differentiation between ball mill and the tube mill arises only from the different length to diameter ratios involved, and not from any difference in fundamental principles. The rod mill, however, differs in principle in that the grinding bodies are rods instead of spheres whilst a pebble mill is a ball mill in which the grinding bodies are of natural stone or of ceramic material.
The types of mill normally encountered can further be classified according to the method of feeding the raw material to, and the removal of the final product from the mill.
These classes are:
- Batch mills.
- Grate discharge mills.
- Trunnion overflow mills.
- Air-swept mills.
The principles of these mills are illustrated in Fig. 1.4 and Fig. 1.5.
Batch Mill
As the name implies, in the batch mills, Fig. 1.4a, the charge of powder to be ground is loaded into the mill in a batch and, after the grinding process is completed, is removed in a batch. Clearly such a mode of operation can only be applied to mills of small or moderate sizes; say to mills of up to about 7 ft diameter by about 7 ft long.
In the three other types of mill a continuous supply and removal of the powder is maintained, and these methods are applicable to mills of the largest sizes.
Grate Discharge Mill
In the grate discharge mill, Fig. 1.4b, a diaphragm in the form of a grating confines the ball charge to one end of the mill and the space between the diaphragm and the other end of the mill houses a scoop for the removal of the ground material. The raw material is fed in through a hollow trunnion at the entrance end of the mill and during grinding traverses the ball charge; after which it passes through the grating and is picked up and removed by the discharge scoop or is discharged through peripheral ports. In this connection, it is relevant to mention that scoops are sometimes referred to as “lifters” in the literature. In the present work, the use of the term “lifter” will be confined to the description of a certain form of mill liner construction, fitted with “lifter bars” in order to promote the tumbling of the charge, which will be described in a later section.
Trunnion Overflow Mill
In the trunnion overflow mill, Fig. 1.4c the raw material is fed in through a hollow trunnion at one end of the mill and the ground product “overflows” at the other end. In this case, therefore, the grating and discharge scoop are eliminated.
![]() |
![]() |
![]() |
![]() |
A variant of the grate discharge mill is shown in Fig. 1.4d, in which the discharge scoop is eliminated by the provision of peripheral discharge ports, with a suitable “dust” hood, at the exit end of the mill.
Air Swept Mills
Within the classes of mills enumerated above there are a number of variations; for example there occur in practice mills in which the shell is divided into a number of chambers by means of perforated diaphragms and it is arranged that the mean diameter of the balls in the various chambers shall decrease towards the discharge end of the mill; such an arrangement being shown in Fig. 1.6. The reason for this distribution of ball size is that, for optimum grinding conditions, the ratio of ball diameter to particle diameter should be approximately constant. In consequence smaller balls should be used for the later stages of the grinding process, where the powder is finer, and by the adoption of a number of chambers in each of which the mean ball diameter is suitably chosen an approximation is made towards the desired constancy in the ratio of the ball size to the particle size.
The problem of the optimum distribution of ball size within a mill will be dealt with more fully in a later chapter, but at this point it is relevant to mention a mill in which the segregation of the balls is brought about by an ingenious method; especially as the mill carries a distinctive name, even though no principles which place it outside the classification given previously are involved.
The Hardinge mill, Fig. 1.7, uses spheres as a grinding agent but the body is of cylindro-conical form and usually has a length to diameter ratio intermediate between those associated with the ball mill and the tube mill. The reason for this form of construction is that it is found that, during, the operation of the mill, the largest balls accumulate at the large end of the cone and the smallest balls at the small end; there being a continuous gradation of size along the cone. If then the raw material is fed in at the large end of the mill and the ground product removed at the smaller end, the powder in its progression through the mill is ground by progressively small balls and in consequence the theoretical ideal of a constant ratio between ball size and particle size during grinding is, to some extent, attained.
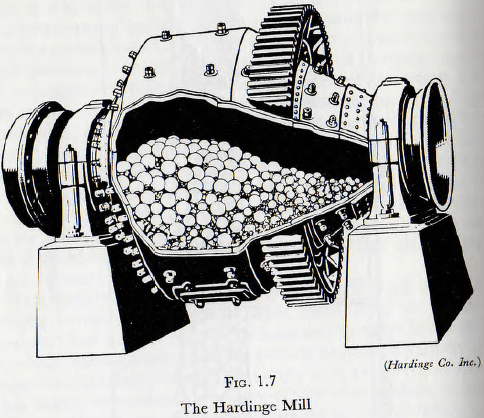
The type of ball mill illustrated in Fig. 1.3, incorporates a peripheral discharge through line screens lining the cylindrical part of the mill. Heavy perforated plates protect the screens from injury and act as a lining for the tumbling charge; sometimes also the fine screen is further protected by coarse screens mounted directly inside it. This type of mill, which is often known as the Krupp mill, is of interest since it represents a very early type of mill which, with modifications, has retained its popularity. The Krupp mill is particularly suited to the grinding of soft materials since the rate of wear of the perforated liners is then not excessive. At this point it will perhaps be useful to discuss the factors upon which the choice between a ball a tube or a rod mill depends.
When a mill is used as a batch mill, the capacity of the mill is clearly limited to the quantity which can be handled manually; furthermore the mill is, as far as useful work is concerned, idle during the time required for loading and unloading the machine: the load factor thus being adversely affected. Clearly then, there will be a considerable gain in throughput, a saving in handling costs and improved load factor, if the mill operation is made continuous by feeding the material into the mill through one trunnion and withdrawing it either through the other trunnion or through discharge ports at the exit end of the mill body.
Since, however, the flow of powder through the mill is now continuous, it is necessary that the mill body is of such a length that the powder is in the mill for a time sufficiently long for the grinding to be carried to the required degree of fineness. This, in general, demands a mill body of considerable length, or continuous circulation with a classifier, and it is increased length which gives rise to the “tube mill”.
In the metallurgical industries very large tonnages have to be handled and, furthermore, an excess of fine material is undesirable since it often complicates subsequent treatment processes. In such applications a single-stage tube mill in circuit with a product classifier, by means of which the material which has reached optimum fineness is removed for transport to the subsequent processing and the oversize is returned to the mill for further grinding, is an obvious solution. Once continuous feed and a long mill body have been accepted, however, the overall grinding efficiency of the mill may be improved by fairly simple modifications.
As has already been mentioned; for optimum grinding conditions there is a fairly definite ratio of ball size to particle size and so the most efficient grinding process cannot be attained when a product with a large size range is present in the mill. If, however, a tube mill is divided into a number of compartments and the mean ball size of the grinding media decreases in each succeeding compartment; then the optimum ratio between ball size and particle size is more nearly maintained, and a better overall performance of the mill is achieved; this giving rise to the compartment mill shown in Fig. 1.6. The tube mill has the further advantage that, to some extent, the grinding characteristics of the mill are under control; for example, an increase in the size of the balls in the final chamber will reduce the rate of grinding of the finer fractions but will leave the rate of grinding of the coarser fractions sensibly unchanged and so the amount of coarse material in the final product will be reduced without any excessive overall increase in fineness.
The principal field of application of the rod mill is probably as an intermediate stage between the crushing plant and the ball mills, in the metallurgical industries. Thus, material between about 1-in. and 2-in. size may be reduced to about 6 mesh for feeding to the ball mills. Rod mills are, however, being used in closed circuit with a classifier to produce a product of less than about 48-mesh size, but such applications are unusual.