There is one precipitation house and refinery common to all the leaching buildings. The method of precipitation is by zinc shavings, which, with slight modifications, answers admirably for all strengths of solution, the strong solutions ranging from .70 per cent. KCy to .25 per cent. KCy; the weak from .25 per cent. KCy to .10 per cent. KCy, and the wash-waters from .10 per cent. KCy to .02 per cent. KCy and less.
Each kind of solution is conducted to a separate receiving tank, to ensure that each zinc-box gets its proper share of solution, and then passes slowly through the zinc-boxes into the sumps and to the storage tanks after being strengthened to the required standard.
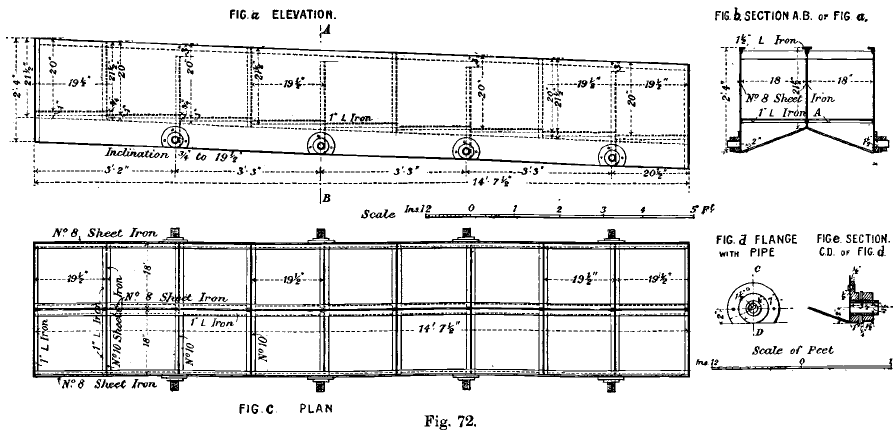
There are three precipitation boxes for each kind of solution. The “ strong ” boxes are very large, each being capable of dealing with 120 to 150 tons of solution per day, but the weak and the wash-water boxes can deal with only 50 tons each.
The zinc-boxes are made of sheet steel shows the details and dimensions of a 50-ton box used for weak solution. Those used for strong solution and wash-water are similar in principle, but differ slightly in detail and capacity.
The precipitation in the boxes generally reduces the amount of gold contained in a ton of solution as follows:
Strong, 1.25 oz. Au to 0.01 oz. Au;
weak, 0.30 oz. Au to 0.02 oz. Au,
and the wash-water 0.080 oz. Au to 0.002 oz. Au.
The zinc shavings are turned by hand on a lathe from discs of zinc of 15 gauge, 12 inches in diameter, with a 1-inch hole for the mandrel.
Great care is taken in this department in order to get as thin a shaving as possible with a minimum of dust, for on this in a great measure depends the purity of the resultant gold slimes. A clean-up is made of the strong boxes once a week, of the weak boxes once in two weeks, and the wash-water once a month.
Cleaning-up
In order to make a “clean-up,” the solution is turned off each box in sequence. The coarse zinc is then removed by hand, the workman wearing rubber gloves. Before taking the coarse zinc out, it is rinsed by “ sousing ” it up and down in the solution left in each compartment.
The solution and slimes left in the boxes are then drawn off by opening valves at the bottom of each compartment and conducted to a sheet steel vacuum filter tank, fitted with a false bottom, on which are laid several thicknesses of cotton flannel. There is also a suction pump connection underneath.
When the compartments of the zinc boxes have been washed with a jet of water until all slimes have been driven into the filter, the valves at the bottom of the compartments are closed, the old zinc is replaced, beginning at the top compartment and finishing with any new zinc that is wanted in the lower ones, and the box is ready for another week’s run.
The slimes in the filter tanks are drained, washed, and sucked free of water by the suction pump, then placed in shallow iron pans (3 feet square), and roasted at a red heat in a muffle furnace overnight.
It requires in this way about 0.9 lb. zinc to each ton of ore treated, or 0.5 lb. zinc to each ounce of bullion precipitated.
The roasted zinc slimes are cooled and treated in a lead-lined sheet-steel pan, with common commercial hydrochloric acid (one part acid to two parts water) until all action stops.
The resultant slimes of gold and silver are filtered, washed, and filtered again as dry as possible, and after being dried in shallow iron pans, are ready for smelting. This smelting is done in large graphite crucibles, the mixture used having approximately the following composition:
The sand is increased if the slimes contain more zinc than usual, but, as a rule, the acid dissolves most of the zinc and in this way greatly reduces the bulk of the slimes. In one case thirteen pans of roasted slimes (one week’s clean-up) were reduced to five pans of treated slime ready for drying by using about 750 lbs. of commercial hydrochloric acid.
The lumps of bullion are taken from each casting and all remelted and cast into ingots or “ bricks ” of about 1,000 ozs. each. From such a week’s clean-up as described above two such ingots would be obtained. The ingots are sampled as accurately as possible and sold to one of the mints.
By this method of treatment, and by “ working ” or refining the molten bullion with suitable fluxes in the final melt, the grade is kept up and the gold is usually malleable. This bullion was considered for years to be the best grade of cyanide bullion sent to the mint, and little difference is found either in gold or silver between the assays made at the mill and those made at the mint.
As a rule the bullion is about 850 fine in gold, 100 in silver, and the rest consists of zinc, copper, and tellurium.
The slags are partially cleaned by re-melting, the mixture used consisting approximately of:
The slags from this melting are saved and sold to the smelters. The lead bullion is saved and sold periodically to the refiners.
Changes in composition of the solution in passing through the zinc boxes inn Fig. 73. Each double compartment contains 35 inches of zinc, and the solution was analysed when passing from each compartment to the next. The gold is seen to be precipitated mainly in the first compartment, and the amounts of alkali and zinc in solution to increase most rapidly at the same time. No reason is assigned for the shape of the curve of alkalinity, and the existence of subsidiary maxima and minima may perhaps be doubted. The cause of the precipitation of the lime is difficult to explain. It is, however, probably in existence in the solution largely as cyanide of calcium, CaCy2. Exposure to air causes this to oxidise and the hydrate is then precipitated, a saturated solution in water at 15° containing only 0.13 per cent. CaO, and less at higher temperatures.