The principal method of grinding in a Tower mill is attrition (scrubbing of particles off material being ground), with the possibility of some shearing and compression breakage taking place due to the motion of the media charge created by the rotation of the helical screw enhancing the media pressure. The Tower mill is filled to a level with grinding media until developed power equals 80% of motor nameplate rating. The Tower mill has a definite use in comminution. It can be used for:
- secondary grinds following ball or rod mills;
- regrind circuits;
- preparation of limestone slurry for flue gas de-sulfurization;
- lime slaking, requiring no grit rejection system;
- grinding and mixing of lime slurry for treatment of acid mine drainage;
- grinding and leaching, as in gold cyanidation circuits;
- preparation of coal-water and coal-oil mixtures;
- grinding coal tar sludge; and
- ultrafine grinding.
Given the proper feed and the requirement for a fine grind, the Tower mill will show a power savings of up to 50% over a conventional tumbling mill.
The Tower mill can be installed for a fraction of the cost of an equivalent kilowatt (horsepower) ball mill. The Tower mill develops very little dynamic forces. Therefore, its foundation can be a concrete floor slab designed for dead load only, whereas a cylindrical ball mill requires a reinforced concrete submat with a minimum of two times the mass of the rotating parts.
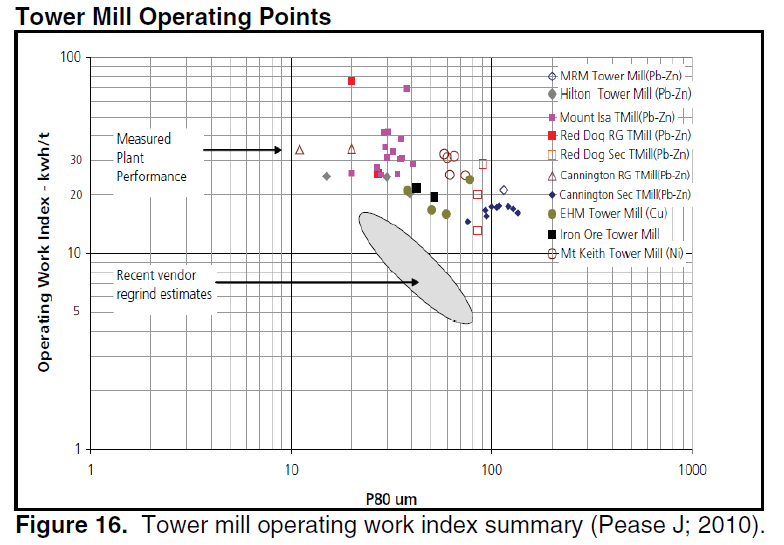
The operating work index was also calculated for all available full scale mill data and is shown in Figure 16. There is no design data included in this but it should serve as a guide as to what the mills are actually capable of. Recent regrinding designs falling in the lower area of the graph have significantly under quoted actual operating mills. You can discuss and get help on regrind mills here.
The Tower mill, consists of a vertical, cylindrical body with support legs on smaller units or a flat base plate on large units. The body has vertical columns on its sides to support a single helical or planetary gear reducer driven by an across-the-line high starting torque induction motor. Special drives such as variable frequency drives, wound rotor motors, and clutches can be used where starting inrush currents cannot be tolerated.
The drive turns a helical screw suspended in the body of the Tower mill. The screws in smaller units or high temperature applications are fabricated from steel, with flights hard-faced by weld overlay to resist abrasion.
IsaMills, Tower Mill and Verti Mill
Ultrafine Grinding in a Tower Mill
The Tower Mill is a vertical “stirred” ball/pebble mill recently introduced in the Western Hemisphere. This device offers a significant power savings on wet fine grinding applications when compared to conventional tumbling mills. This paper describes the laboratory application of this mill wet grinding hydrated alumina to products of 50 percent passing 2 to 6 microns.
The basic grinding action in the Tower Mill is abrasion. The absence of impact limits practical feed size to 5mm. Because there is greater pressure between media and less production of heat and sound, the device consumes less energy than a tumbling mill to perform the same work. The normal top size of balls in a Tower Mill is 25mm. For ultrafine grinding, much smaller media can be utilized.
A summary of some of the ultrafine applications follows:
- Talc from 9 microns average to 1.9 microns average particle size.
- Silica from 37 microns average to 1.7 microns average particle size.
- Barite from 2.8 microns average to 1.55 microns average particle size.
- Limestone from minus 74 microns to 3.1 microns average particle size.
- Limestone from minus 4000 microns to 2.4 microns average particle size.
- Ferrite from minus 1680 microns to 2 microns average particle size.