Table of Contents
During construction work at a mill, the metallurgical engineer in charge, ran a series of experiments on settling. His tests proved that deep settling tanks were not ordinarily necessary. The use of tanks 2 or 3 ft. in depth was suggested. Later experiments demonstrated that the following principles of settling applied to Tigre pulp.
- In settling dilute pulp, settling rates are independent of pulp depth.
- In settling thick pulp, settling rates are approximately proportional to pulp death.
- The critical dilution, or the boundary between dilute and thick pulp, in the application of the above principles, is the highest dilution at which channels form in the pulp; clear liquid reaching the surface through the channels.
It is gratifying to note that these principles, tentatively announced 4 years ago as applying to Tigre ore, are now proved, by the comprehensive tests of Coe and Clevenger, to have universal application.
The formula, suggested at that time for solving problems of area, was likewise similar to that adopted by these gentlemen.
Area = 0.0222 (Dry Tons) (R1-R2)/Settling Rate, in Feet Per Minute
R1 and R2 were the moisture ratios respectively of feed and discharge. The settling rate was that of the feed, as determined by laboratory tests. This method of calculation was shown to give results which closely approximated those of actual settling, operations in the plant.
In subsequent investigations at El Tigre, improved methods have been devised for the laboratory determination of settling rates, and for the calculations of the required area and depth of settling tanks. Also many interesting new principles have been developed concerning the effect on settling phenomena of various changes in temperature and percentage of lime in solution. The details of these investigations are discussed at length below.
Thickener Design
Definitions:
In order to avoid confusion, the nomenclature employed by Coe and Clevenger is used as far as possible in this paper.
Settling rate is expressed in terms of the depth in feet of clear liquid formed per hour; or the rate in feet per hour at which the pulp surface moves downward.
Dilution is expressed in terms of the ratio by weight of liquid to solids, and is termed, for short, “The L:S Ratio.” In tables, charts and formulas, the first factor only of the L : S ratio is used. Thus the figure 5 designates a dilution of 5 :1.
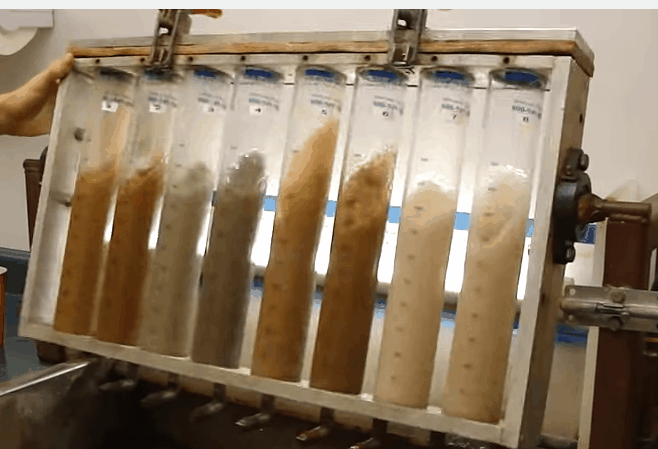
Natural slime is defined as minutely divided particles of pulp resulting from the disintegration of kaolin, talc, or other similar constituents of ore which occur minutely subdivided in nature.
Slime is empirically defined, for the purpose of this discussion, as the finer particles of pulp that will remain suspended for 5 min. in a 100 :1 mixture of fresh water and ground ore; the temperature of separation being 60° F. (16° C.). The term covers all the natural slime occurring in the pulp and also a considerable portion of extremely fine sand.
Sand is the relatively coarse material of the pulp, resulting from grinding quartz, calcite, feldspar, or other massive gangue matter. It may vary from the size of a pea to impalpable powder.
Flocs or floccules are aggregates of slime particles, caused by attraction or cohesion between the particles. Flocculation may be increased by the addition of electrolytes, such as lime hydrate, magnesium sulphate, glue, etc., and may be decreased by the introduction of deflocculating agents (sodium carbonate, sodium hydrate, etc.). Temperature and dilution have marked effects on the rate at which flocs form.
The free-settling zone is the horizon of evenly flocculated dilute pulp in the upper part of a continuous-settling tank. In this zone, the flocs do not press one upon the other, and settling rates are independent of pulp depth.
The critical dilution is the dilution at which flocs begin to touch. It is the highest dilution at which channels or tubes form in the pulp, the channels or tubes furnishing passageways to the surface for the clear liquid set free in the bottom of the vessels.
The thickening zone is the zone of thick pulp in the bottom of a continuous-settling tank. In this zone, the flocs rest one upon the other, and liquid is eliminated chiefly through the channels mentioned above. Settling rates, in the thickening zone, are approximately proportional to pulp depth. The same principle is expressed by Coe and Clevenger in the words: “Elimination of water is a function of time” (in the thickening zone). The term, “ zone of compressions ” is used by Coe and Clevenger, on the assumption that the introduction of the time element, as a function of settling, is due to compression caused by the depth of pulp. I believe that this assumption is open to dispute and have hence adopted a more general term for designating the zone.
https://www.911metallurgist.com/settling-calculate-thickener-capacity
Theoretical Considerations:
Investigations indicate that cohesion or attraction between the flocs is responsible for the fact that elimination of water in the thickening zone is a function of time. Only a positive tensile force, like cohesion, could form channels and keep them open afterward. In the absence of channels, elimination of water in the thickening zone is a function of area and not of time. This fact is illustrated in Table 3.
Cohesion plays an important part during all settling operations. In the free-settling zone it causes the slime particles to aggregate into flocs. In the first stages of thickening, it causes the flocs to draw together, thus developing tensile strains in the pulp which are relieved by cracks and channels (the clear liquid reaching surface through these avenues). During the final stages of thickening, especially in the presence of high lime, cohesion no longer causes closer union between slime particles, or between flocs; but it still strongly resists any force tending to change the shape of the flocs. This resistance reduces settling rate by opposing the compression, due to pulp depth, which would otherwise force the flocs to displace the liquid in the interfloccular spaces. The greater density attained by the deeper pulp columns in Table 3 can best be explained on this basis.
It has been noted by Coe and Clevenger that after settling has ceased in the shorter columns, it may be caused to continue by decanting the clear liquid and agitating the thick pulp. This behavior is quite as apparent in the absence of classified sand as when classified sand occurs in the pulp. The cause of the action appears to be the rearrangement of the slime particles. Before agitation, a slightly flocculated structure is noted, a close inspection disclosing clear liquid between the flocs. After agitation, no flocculation is apparent. Evidently the pulp flocculates “en masse” after agitation, and settling is resumed because cohesion aids instead of resists compression.
The rate at which flocs form in the free-settling zone is an item of importance in the operation of continuous-settling tanks. When pulp first leaves the feed column of a tank, flocs are entirely unformed and the settling rates are low or nil. The dilute pulp spreads out laterally—over the top of the denser pulp in the bottom of the tank. As the lateral movement lessens, flocs begin to form and the settling rate increases correspondingly. The rate at which flocs develop depends upon temperature, dilution, and strength of electrolytes. During warm weather, and in the presence of high lime, the slime becomes fully flocculated almost immediately after leaving the feed column. Under such conditions the average settling rate, over the entire area of the tank, is high. During cold weather, and in the presence of low lime, partially flocculated pulp may spread practically to the tank periphery; forming a blanket over the pulp surface, which retards egress of liquid from the more completely flocculated pulp in the lower horizons of the tank.
The various stages in the development of flocs are well represented in laboratory tests at free-settling dilutions. When tests are first started, flocculation is imperfect and settling rates are low, this stage representing conditions near the feed column in continuous-settling tanks. As the tests continue, flocs become more perfectly developed and settling rates increase. When lime, dilution, and temperature are high, flocculation is completed and maximum settling rates are attained before the pulp surface has settled 1/8 in. When lime, dilution and temperature are low, complete flocculation and maximum settling rate are attained only after the pulp surface has settled ¼ or 1/2 in. The complete flocculation and consequent maximum settling rates, finally attained in the tests, correspond to the conditions existing near the tank periphery and also in the lower free-settling horizons of the tank.
Laboratory tests, for determining the settling rates corresponding to the various horizons in a continuous-settling tank, should be so performed that the degree of flocculation in the tests is approximately the same as occurs at the various depths in the settling tanks. Tests at the dilution of feed should aim to represent the imperfectly flocculated condition occurring near the feed column as well as the more complete flocculation at the tank periphery, the average settling rate over the entire pulp surface being the result desired. Experience at Tigre, under varying conditions of dilution, lime and temperature, indicates that this result can best be accomplished when the first 0.05 ft. settled in-the tests furnishes the basis for the calculation of the settling rates corresponding to feed dilutions.
In case doubt exists that area might be governed by the permeability of some horizon below that of the feed, a series of settling tests at lower free-settling dilutions are run. In this series, observations are not started until after flocs are fully developed and maximum settling rates are attained. This condition is usually fulfilled when the second 0.05 ft. settled in the tests furnishes the basis for calculating the settling rates corresponding to the lower dilutions in the depths of the settling tank.
At Tigre, area is invariably governed by the settling rate of the feed horizon. Hence, the tests at lower dilutions are usually omitted. In Table 2, a series of settling rates, experimentally determined at feed dilutions, are compared with actual settling rates in a 32-ft. continuous-settling tank, a considerable range in lime, dilution and temperature being obtained in the comparison. The experimentally determined settling rates will be observed to check closely with those occurring in actual practice. Minor differences are probably due to changes in the character of ore from day to day, and to the difficulty of properly correlating dilutions of feed and discharge. The tank was operated at maximum capacity throughout the tests, so errors introduced by changes in pulp level were slight.
Table 3 also illustrates the effect of deficient area on thickening operations below critical dilution. In all cases recorded in the table, the thickness of discharge was limited by settling rates in the free-settling zone, the area being inadequate to secure any benefit from the depth of tank. Even when the feed entered the tank below critical dilution, it was diluted to critical dilution by the excess of liquid rising from the lower depths, the bulk of pulp in the tank being practically at critical dilution. Final thickness in such cases was limited by the settling rate at critical dilution.
Practical Principles:
The foregoing discussion of settling phenomena differs somewhat from that of Coe and Clevenger. The differences are mostly theoretical in character and are not insurmountable in a practical consideration of the subject. For the application of experimental data to the solution of practical problems, fundamental principles are all-important. In the conception of fundamental principles, Coe, Clevenger and myself are fully agreed.
The principles underlying settling operations may be briefly stated as follows:
- Settling rates in the free-settling zone are independent of pulp depth. Stated in other words: At dilutions above critical dilution, elimination of water is a function of settling area, and is independent of pulp depth.
- Settling rates in the thickening zone vary directly with pulp depth. Stated in other words: At dilutions below critical dilution, elimination of liquid is a function of pulp volume, being dependent on both area and depth. Or, in the words of Coe and Clevenger, “elimination of water in the zone of compression is a function of time.”
- Settling rates vary with the dilution of the natural slime in the pulp, being usually greatest for high dilutions and smallest for low dilutions.
- Settling rates are practically independent of the amount of sand occurring in the pulp (regardless of the fineness of the sand).
- Settling rates increase as the temperature increases.
- Settling rates vary with the degree of flocculation of the slime particles.
- Degree of flocculation depends upon:
(a) The nature and preceding treatment of the ore.
(b) The character and concentration of electrolyte.
(c) The dilution and temperature of the pulp.
(d) The time elapsed after inception of flocculation. - Critical dilution depends primarily upon the character and proportion of natural slime in the ore; secondarily upon the strength of flocculating agents in solution; and thirdly (only slightly) upon temperature.
The above principles furnish the basis for the solution of settling problems. The first two principles are of direct importance in the determinations, by laboratory tests, of the settling equipment required in metallurgical plants. The remaining principles enumerate the effects of other influences upon settling operations and illustrate the importance of maintaining these influences the same in the tests as in actual practice.
Tests For Determining Settling Equipment:
In designing or remodeling hydro-metallurgical plants, questions frequently arise regarding the number and size of settling tanks to be installed. Occasionally the tanks are required for some definite service in a predetermined flow sheet of the plant. In such cases, the conditions of temperature, electrolyte, tonnage, dilution of feed, and desired thickness of discharge, are known beforehand, the problem being to provide sufficient settling equipment to fulfill these conditions. Usually, the flow sheet depends to some extent upon settling operations, rendering it necessary to determine approximately the settling equipment required under varying conditions, in order to decide intelligently upon the conditions best suited for a well balanced plant.
The first step, in the solution of such problems, is to secure a representative sample of the pulp to be settled. The sample should contain the maximum proportion of natural slime that would occur in the mill pulp during any single day of operation. It should secure as nearly as possible the same preliminary treatment as would occur in mill practice. Above all, the sample should not be dried at a high heat, since heat changes the character of the slime, greatly increasing subsequent settling rates. The importance has been pointed out, by Coe and Clevenger, of not allowing the sample to remain a greater time in contact with water than would occur in plant operations; the degree of flocculation, and consequently the settling rate, being changed by this treatment. The electrolytes present in the water should be the same as would occur in plant practice. Often, electrolytes are derived partly from the ore and can be introduced in proper proportions only by bringing the water into repeated contact with fresh samples of ore, the procedure being the same as in the return of water to the head of the mill. The entire object of these precautions is to secure a sample that will represent the pulp to be fed to the tanks.
This sample is settled, preferably over night. The clear water is decanted and set aside for diluting the pulp in the various tests. The thickened pulp is mixed, and tested for liquid to solid ratio. The following procedure in testing has given most uniformly reliable results:
For determining critical dilution, glass graduates are filled to a depth of 1 ft. with varying consistencies of the pulp to be tested. After 10 or 15 min. of undisturbed settling, channels develop in the columns of thicker pulp, clear liquid rising through the channels. If no channels are observed, or if they develop first in the bottom of the vessel, the critical dilution is lower than that of the test. If channels develop first near the pulp surface, or if transverse cracks form in the pulp, the critical dilution is higher than that of the test. The exact critical dilution is indicated by the simultaneous formation of channels in all parts of the settling column, the channels in the upper part of the column being usually replaced later by the extensions of the channels from the bottom of the vessel.
For determining settling rates in the free-settling zone, cylinders are filled to a depth of 1 ft, with various dilutions of pulp, one sample being at exactly critical dilution, the remaining samples representing an ascending scale of dilutions above the critical point. The L:S ratio of each sample is determined by test or by calculation. Each sample is violently agitated and the settling tests started. From the first 0.05 ft. settled in the tests, are calculated the settling rates corresponding to the feed horizons of continuous-settling tanks. These may be termed “the settling rates of feed.” From the second 0.05 ft. settled in the tests (of lower dilutions) are calculated the settling rates corresponding to the various free-settling dilutions in the depths of continuous-settling tanks. These may be termed the “free-settling-rates.”
Settling rates in the thickening zone are determined in a single test. For this purpose a cylindrical graduate, of 1 liter, or greater, capacity, is marked at the following depths:
Marks on Testing Cylinder | |
Depths in feet | Depths in feet |
1.160 | 0.636 |
1.050 | 0.576 |
0.950 | 0.521 |
0.860 | 0.471 |
0.778 | 0.427 |
0.704 | 0.386 |
Each depth is 95/105 of the previous one. The distance between any two consecutive depths is one-tenth the average of the two depths. Hence the distance settled between any two consecutive marks represents 1/10 ft., per foot depth of pulp. This principle is of great assistance in calculating settling rates in the thickening zone.
The specially marked cylinder is filled to the 1.05-ft. mark with pulp at exactly critical dilution. Solution is added until the combined pulp and solution reaches the 1.16-ft. mark. The mixture is then agitated and the test started. Due to the addition of solution, the test begins in the free-settling zone, and flocs are at least partially formed before the critical dilution is reached. This somewhat parallels usual plant practice and gives more representative results than are obtained when the test is started at exactly critical dilution. The time is first noted as the pulp surface passes the 1.05-ft. mark, and is thereafter noted for each subsequent mark until settling ceases. This test indicates the lowest dilution that can be obtained in the tank discharge, and furnishes the basis for calculating the depth of tank required to produce that dilution, or any other dilution in the thickening zone. The settling rates in the thickening zone must represent the average rate of subsidence of pulp surface, per foot depth of pulp, in settling from the critical dilution to the various possible dilutions of discharge.
The average settling rate, corresponding to any dilution of discharge, may be quickly calculated by considering each space as 1/10 ft., and by dividing the aggregate space settled (so considered) by the time required for the pulp surface to settle from critical dilution to the dilution considered. The method for tabulating observations and calculating settling rates is illustrated in Table 1.
The dilutions of pulp, corresponding to the various marks on the thickening cylinder, may be successively calculated from the critical dilution by the following formula:
D = 0.905 C – 0.095/G
D and C are the L :S ratios corresponding to any two consecutive depths.
G is the specific gravity of dry pulp.
This method for calculating dilutions may be extended to the free- settling tests by similarly marking all cylinders, the range of free-settling dilutions being secured by filling the various vessels to the different depths with pulp at critical dilution and adding solution to each vessel until the 1.05-ft. mark is reached.
Determination of Area and Depth of Continuous-Settling Tanks:
The determination of the settling area, required for any definite settling operation, is based on the principle that the elimination of water in the free-settling zone is a function of settling area and is independent of pulp depth. Expressed as a formula, this law is :
A=1.34 (F-D)/S
Where
A = Area in square feet per ton of dry pulp settled daily.
F = L : S ratio of the governing dilution.
D = L : S ratio of the dilution of discharge.
S = Settling rate of governing dilution (as determined by laboratory test at free-settling dilutions).
The numerical constant (1.34) is the factor introduced by reducing the quantity of water eliminated, from cubic feet per hour to tons per day.
The derivation of this formula is explained more fully by Coe and Clevenger, and also in a former article on the settling of Tigre slime. The idea of a governing dilution (introduced by Coe and Clevenger) generalizes the formula, rendering it applicable, should area be governed by some free-settling rate in the depths of a settling tank.
As an example of the application of the above formula, the area of tank required to settle Tigre pulp from a dilution of 14 :1 to a dilution of 2.3:1, may be calculated from the data presented in Table 1. The settling rate of the feed, determined by interpolation in the table, is 0.78 ft. per hour. Substituting in Formula 3:
A = 1.34 (14-2.3)/0.78 = 20 sq. ft. per dry ton Settled daily (based on the settling rate of the feed).
When the same formula is applied to the various free-settling dilutions between 14:1 and 5.1:1 (critical dilution), the largest area required is 16 sq. ft.—corresponding to the dilution of 13.1:1. This is considerably less than the area determined by the feed dilution. Hence in this case, the settling rate of the feed is the governing factor, the required area being 20 sq. ft. per ton of dry pulp settled daily.
The determination of the depth required in continuous-settling tanks depends on the law that the elimination of water in the thickening zone is a function of both area and depth. This law is expressed in the following formula:
Depth = 1.34 (C – D)/A x T
Where:
C and D are respectively the L : S ratios of critical dilution and of discharge.
A is the settling area (as previously determined by Formula 3).
T is the average settling rate, per foot depth of pulp, in settling from dilution C to dilution D (determined in laboratory tests, previously described).
In the problem to be solved:
C = 5.1; D = 2.3; A = 2.0; and T = 0.03 (from Table 1).
Substituting in Formula 4:
Depth = 1.34 (5.1 – 2.3) / 20 x 0.03 = 6.3ft.
From the above calculations, it appears that in order to settle Tigre pulp from a feed dilution of 14:1 to a dilution of discharge of 2.3:1 (the lime being 0.3 lb. per ton and the temperature 75° F.) it is necessary to provide a minimum area of 20 sq. ft. per ton of dry pulp settled daily, and a minimum effective depth of 6.3 ft. This checks closely with actual requirements in the plant.
The method outlined above is applicable for any other dilutions of feed and discharge within the limits of the tests.
Problems, involving the determination of dilutions of feed or discharge when area and depth are known, may be solved by transposing or combining Formulas 3 and 4.
Graphical Method for Solving Settling Problems:
In designing settling equipment it is often necessary to consider numerous combinations of interdependent settling operations. The algebraic solution of such problems is cumbersome, involving a great bulk of calculations for each combination considered. A graphical method, designed to meet the needs at Tigre, might be suggested for use in such cases.
Fig-1. Ratio: Liquid to solids by weight
For the graphical method, settling tests are performed as previously described, the specially marked cylinders being used in all tests. The settling rates, corresponding to the various dilutions, are plotted on a printed chart (see Fig. 1). The vertical axis of the chart represents settling rates. The horizontal axis is calibrated for both L: S ratios and divisions marked on the cylinders (the short marks above the axis representing the marks on the cylinders). With the L:S ratio of the critical dilution known, lower or higher dilutions may be determined by counting divisions to left or right, thus obviating the necessity for calculating the ratios of liquid to solids, corresponding to the various dilutions. The radial calibrations at the upper and right-hand margins of the chart are for the purpose of graphically solving problems of area. The problem solved algebraically above is solved graphically in Fig. 1.
Following is the standard procedure for determining area and depth, when dilutions of feed and discharge are known:
- From the point on the horizontal axis representing dilution of discharge, draw an inclined line to the point on the curve representing settling rate of feed. In case the inclined line intersects the free-settling curve, it is rotated downward until tangent to the lowest depression on the curve. In this case, the point of tangency represents the dilution which governs area If the inclined line does not intersect the free-settling curve, area is governed by the settling rate of feed.
- Parallel to the inclined line, draw a line from the zero point of the axis to the margin of the chart and read the area required for each ton of dry pub, settled daily.
- Observe the settling rate indicated by the intersection of the inclined line with the ordinate through the critical dilution. Divide this settling rate by the settling rate shown on the curve, corresponding to the dilution of discharge. The quotient is depth required.
Problems involving the dilution of feed or discharge, when depth and area of tank are known, may be solved by reversing this procedure.
The fundamental principles underlying the graphical calculations are identical with those upon which the algebraic determinations are based. Results are the same when calculated by either method. The advantages of the graphical method are greater simplicity, greater rapidity, and the possibility of solving a larger number of problems from a single set of observations. The graphical method is of most service in solving complex problems, in which various settling operations are interdependent.
Scope of Laboratory Tests:
The laboratory methods for ascertaining the required dimensions of continuous-settling tanks are by no means perfect. Small errors are undoubtedly introduced by the empirical manner of experimentally determining the effects of the rate of flocculation on settling. Other errors possibly enter on account of the failure to determine the extent to which the pulp in the upper part of the tank is diluted by water rising from below. These errors are not serious. Quite possibly they may be altogether eliminated by future investigations. In the meantime, the methods already developed may be employed with the assurance of obtaining reasonably accurate results.
The particular advantage of laboratory determinations lies in the rapidity with which they may be performed. A complete series of tests, covering all necessary dilutions of feed and discharge, usually requires 3 hr. of constant attention, followed by 6 hr. of intermittent attention, and perhaps a couple of observations the next day. In 3 or 4 days it is often possible to cover, in a general way, all conditions of dilution, electrolyte, and temperature, that might occur in the plant.
Fig.2- Ratio: Liquid to Solids by Weight
Laboratory tests are most useful for preliminary investigations prior to mill construction. They furnish means for roughly estimating the settling equipment necessary for various requirements and under varied conditions in plant practice. These data, combined with similar information regarding dependent operations, enable the mill designer to decide intelligently upon the conditions to be maintained in the plant, and the duty to be performed by the settling equipment. It is as an aid in deciding upon the flow sheet of a contemplated plant, that laboratory settling tests are particularly useful. The approximate determination of the settling equipment necessary to fulfil the requirements imposed by the flow sheet, is a secondary advantage.
Unit Tests:
Before proceeding with extensive installations, it is usually advisable to check, by unit tests, the laboratory determinations of the required settling equipment. Unit tests should preferably be performed in tanks of full height, though the area may be considerably less than that of the
Fig.3- Ratio: Liquid to solids by Weight
tanks to be installed. Test tanks, for determining the size of small installations, may be constructed of 12- or 16-in. pipe, suitable overflow, feed column, cone bottom, and continuous discharge being provided. For determining extensive installations, the tests should preferably be conducted in standard settling tanks. Observations in unit tests may be started as soon as the required dilution is secured in the discharge, and may be continued over periods ranging from a day to 6 month, the duration of the tests depending upon the accuracy desired and the importance of the equipment to be installed. It is important that the required conditions of dilution, electrolyte, temperature, and pulp depth, be maintained throughout the tests; and that the capacity, under these conditions, be accurately ascertained. In determining settling equipment from unit tests, capacity is regarded as proportional to settling area.
Fig.4- Ratio: Liquid to solids by Weight
Repeated mention is made in the foregoing discussion of the importance, in settling operations, of dilution and temperature. The effects of variations in these conditions, upon sundry phases of settling at Tigre, are ‘graphically illustrated in Fig. 2, 3 and 4. The data, presented in these figures, may be briefly summarized as follows:
Effects of Dilution:
In the free-settling zone, settling rates are greatest at high dilutions and lowest at low dilutions.
In the thickening zone, settling rates are greatly increased at dilutions just below critical dilution, reaching a maximum when the dilution is four-fifths that of critical dilution. Below this dilution, settling rates rapidly decrease as the dilution is reduced.
Effects of Lime:
In the free-settling zone, settling rates of feed are trebled by increasing lime from 0 to 0.2 lb. per ton of solution, and are quadrupled by increasing lime from 0 to 0.7 lb. Further addition of lime above 0.7 lb. produces little advantage.
The critical dilution is doubled by increasing lime from 0 to 0.4 lb. Further addition of lime produces little effect on critical dilution.
At the higher dilutions in the thickening zone, lime up to 0.4 lb. greatly increases settling rate.
At the lower dilutions in the thickening zone, variations in lime have little effect on settling rate, except in very shallow columns, or in the absence of classified sand.
Effects of Temperature:
In the free-settling zone, an increase in temperature from 40° to 80° F. trebles settling rates.
Critical dilution increases slightly as the temperature is raised.
At the higher dilutions in the thickening zone, increase in temperature from 40° to 100° doubles settling rates.
At the lower dilutions in the thickening zone, changes in temperature have little effect on settling rates.
General Conclusions:
High dilution, low lime and low temperatures predicate extensive settling area and tanks of shallow depth.
Low dilutions, high lime, and high temperatures predicate less area and comparatively deep tanks.
Adequate area is the first consideration in settling. Any advantage from increased depth can also be obtained from increased area. On the other hand, when area is inadequate, tank depth has no effect on results of settling.
Settling Problems at El Tigre:
Recent changes in treatment at El Tigre necessitated the reduction of lime in the mill water, from 1.5 lb. per ton to 0.02 lb. Before the changes were made, it was realized that this reduction in electrolyte would greatly decrease the already low settling rate of Tigre pulp. Hence all conditions affecting settling were carefully re-examined.
The ore at Tigre is crushed in stamp batteries to pass a 2-mesh screen. It is then ground to 20-mesh in a Hardinge mill. After concentration, it is further reduced, in tube mills, until 85 per cent, will pass a 200-mesh screen. The all-slime product is then settled to the L:S ratio of 5 :1.
Tigre ore contains 25 per cent, natural slime. In the presence of this proportion of slime, classification of fine sand in the tube-mill circuit can be accomplished only at dilutions above 15:1.
To settle Tigre pulp, in the absence of strong electrolytes, requires extremely large settling area. This is especially true during the cold winter months. Preliminary laboratory tests-indicated that in order to settle average Tigre ore from a dilution of 15 :1 to a dilution of 5 : 1, the lime being 0.02 lb. and the temperature 45° F., it would be necessary to provide 110 sq. ft. of settling area per ton of ore settled daily. On this basis, 61 settling tanks, each 24 ft. in diameter, would be required to handle the Tigre tonnage of 250 tons per day.
The problem was solved, not by supplying this excessive equipment, but by modifying conditions elsewhere in the plant.
The dilution at which classification of sand can be accomplished in mechanical classifiers depends upon the coarseness of the sand to be separated and the proportion of natural slime in the pulp.20 To separate 20-mesh sand, dilutions between 4 :1 and 1:1 are usually required. The classification of finer sand necessitates higher dilutions. With 25 per cent, natural slime in the pulp, 200-mesh sand can be separated only at dilutions above 15:1. When the pulp contains 8 per cent, natural slime, satisfactory classification of 200-mesh sand can be effected at the dilution of 6 :1. In the presence of 1 per cent, natural slime, classification is satisfactory at the dilution of 1:1. It thus appears that classification is a function of the dilution of the natural slime and is practically independent of the proportion of sand occurring in the pulp.
Settling rates, also, vary inversely with the percentage of natural slime in the pulp. It follows, therefore, that in order to obtain a thick, “all-slime” product from an ore containing an excessive amount of natural slime, it is important to separate the natural slime and sand, while the slime is undiluted and the sand is still coarse. The coarse sand can then be diluted sufficiently to insure good classification in the fine- grinding department of the plant, without necessitating extensive equipment for dewatering the product.
These objects are accomplished at El Tigre by modifications in the stamp mill. The batteries are divided into two units, a mechanically operated classifier receiving the discharge from each unit. The sand from both classifiers is sluiced to the Hardinge mill with fresh water. Attrition in the Hardinge mill produces a certain amount of natural slime—from the disintegration of clay balls, etc. This is washed from the sand in hydraulic classifiers. The sand from the hydraulic classifiers is concentrated, and flows by gravity to the tube-mill room.
The slime overflow from the hydraulic classifiers is elevated and used as feed water in the first unit of batteries. The slime overflow from the classifier below the first unit of batteries is elevated and employed as feed water in the second unit. Thus the battery feed water is used in three operations, acquiring a load of slime in each operation. The final slime product, overflowing from the classifier below the second unit of batteries, has a dilution of 6 :1 and requires .no further thickening.
On account of the low dilution of the final slime product, much fine sand is carried over with the slime overflow of the second classifier. This is separated on Deister slime tables, which are equipped with deep riffles for the purpose. The shallow flow of slime across these tables and the sharp movements imparted by the mechanism prevent flocculation and effect a good separation of sand from the thick pulp. The slime tailing from the Deister tables tests 87 per cent, through 200-mesh, which is satisfactory. The sand product is concentrated on a recleaning table, equipped with standard riffles. Improved concentration is secured on the Deister tables by this roughing and recleaning process. The final sand tailing from the recleaning table joins the sand from the upper part of the mill and flows by gravity to the tube mills.
The low dilution in the battery discharge necessarily reduces tonnage through the batteries. This effect is counteracted by employing coarser screens and by using the same feed water successively in the two sets of batteries. An average daily tonnage of 12 tons per 1,200-lb. stamp is maintained.
Low efficiency in the batteries is offset by improved efficiency in the Hardinge and tube mills.
The cost of the successive elevations of slime in the stamp mill is offset by reduced cost of pumping from the bottom of the mill.
The sand entering the tube-mill room still contains some natural slime. More slime is liberated in the tube mills by the disintegration of partially kaolinized feldspar. The final overflow from the tube-mill classifiers contains 7 per cent, natural slime, and 93 per cent, fine sand. This product tests 85 per cent, through 200-mesh. The dilution is 7:1. It is settled to a dilution of 4 :1 in 12 shallow settling tanks, each 24 ft. in diameter.
The combined dilution of final sand and slime products is 5:1, which is the dilution required.
Thus the problem was solved by the installation of one-fifth the settling equipment estimated as necessary, and without sacrificing any . element of efficiency in mill operations.
In the above discussion, an effort has been made to submit, as briefly as possible, any results of investigation at El Tigre which might have application elsewhere. Since tests have been limited to one class of ore, many of the observations can have only local importance, or at the most,
serve to indicate what may be expected under like conditions elsewhere. In other instances, the investigations at El Tigre and the more comprehensive investigations of Coe and Clevenger, are mutually confirmatory,
No classification of sand observed.
No channels in 3-in. column.
Short channels in upper part of 6-in.
Strong channels in 12-in., 24-in. and 48-in. columns, but these closed during last part of test.
Only short channels (less than 2 in. long) occurred near the surface in the observations below the heavy line.
Settling rates below heavy line are independent of pulp depth.
No arching of the slime occurred and no cracks or pockets of clear liquid could be detected at the end of the tests.
making it possible to formulate, and employ with confidence, many general principles of settling. Although all phases of settling have by no means been investigated, sufficient work has been done to render possible the formulation of certain standard methods for the solution of settling problems. Undoubtedly these methods will be simplified and rendered more accurate by future investigations.
Discussion:
H. S. COE, St. Louis, Mo. (written discussion*).-I feel much gratified that Mr. Mishler has confirmed those principles of slime settlement expressed by Mr. Clevenger and myself. I wish to state that when we wrote the article referred to by Mr. Mishler we had not seen his earlier article in which he gave a formula to be applied to the settling rate of feed pulp for determining thickener area required at El Tigre. It has been my experience that in cyanide work the settling area required is determined by the settling rate of the feed pulp for perhaps 20 per cent, of all of the ores to be encountered. For the other ores, the area required is greater than that indicated by the settling rate of the feed and corresponds to the settlement of a somewhat thicker free-settling pulp. Mr. Mishler, in his paper, has thoroughly outlined a set of tests for determining thickener capacity, which, if carefully carried out, should be entirely reliable, provided allowance is made for changes in the mill feed from time to time.
Two features of his paper, I believe, need comment. In speaking of the time required for slime to flocculate after being fed, Mr. Mishler quite properly states that the actual settling rate for the feed pulp cannot be that of completely flocculated pulp because of this time lost in flocculation. It seems to me, however, that this feature cannot be of very great importance, for the following reason: The upper zones of pulp in a thickener may be, and often are, as thin as the feed pulp. If, therefore, the feed be introduced at sufficient depth below the pulp surface to prevent agitation at the surface, there will be ample time for it to become flocculated before it becomes the surface layer, and it will therefore cause no appreciable retardation in the settlement of the surface of the pulp.
Mr. Mishler speaks of the stage of settlement in which, after the pores and water channels collapse, further settlement depends again directly on the area of the container and not on the volume. I have often observed this to be true, and where settlement is required to a density of discharge thicker than that at which the channels close, increased depth is not advantageous for a tank, but rather increased area, as has been demonstrated in settling Anaconda flotation concentrates. It seems highly probable that in the final stage a stirring of the pulp, such as is accomplished by the thickener mechanism, will increase the rate of settlement; and since this final settlement is extremely slow, sometimes amounting to almost nothing when not stirred, the average settling rate in the final thickening stage may be so increased, by stirring, as both to diminish the depth of tank required and to increase the thickness of the final discharge.
Mr. Bloomfield, in his work with shallow Dorr trays at the Golden Cycle mill, reports results which strongly indicate this to be the fact for Golden Cycle ore. Stirring would not increase the capacity of the thickener beyond the natural capacity for discharging pulp of the consistency at which the channels have just closed; on the contrary, the capacity should be slightly lower, due to the fact that the D in Mr. Mishler’s formula No. 3 becomes less and A, or required area, consequently becomes greater.
Another phase of slime settlement which has not been discussed should be spoken of. I refer to the clarification of water or the settling of very thin pulps too dilute to flocculate in the ordinary way. I have found that a 10-ft. depth of turbid water will become clear in approximately the same time as a 1-ft. depth.
In the cases observed, the minute particles in suspension are drawn together in an accidental manner to form floccules which fall to the bottom. The water thus clears by degrees and all of the particles will have flocculated and settled from a large volume in about the same time as would be required for a small volume. In clarifying water for domestic use, the basins are designed to contain water for what is designated as “the detention period,” or time required to clear the water.
Whenever very clear overflows are required from thickeners, the tank should be constructed to retain the solution above the pulp level for the required detention period. That is, the tanks should be sufficiently deep to allow the requisite zone of clarifying liquid above the pulp.
Methods for Determining the Capacities of Slime-thickening Tanks by R. T. MISHLER,” ESQDEDA, SONORA, MEX.