Table of Contents
In open pit quarry operations the loading of the blasted rock for transportation to the primary crusher house involves either power-shovels. Any size of primary crusher may be used for hand-loaded rock; it all depends upon how much secondary shooting, and hand sledging, the operator feels he can afford. So called “one-man” stone or stone of a size that can be lifted into small cars or carts by the average laborer can be handled through a 10 or 13″ gyratory crusher, or a jaw crusher of equivalent receiving opening. Usually, for hand-loading operations, capacity and product size govern the choice of the primary crusher. The unit labor cost of feeding hand-loaded stone is higher for small crushers than it is for larger machines but, if the labor market is such as to permit hand-loading in the quarry, a little additional labor at the crusher will not add materially to the cost of production.
In the American quarry, gravel pit, and open-cut mine, the power shovel, supplemented to a lesser extent by other types of excavating equipment, has, within the last forty years, practically eliminated hand loading. Today, in these operations the power shovel is just as necessary as the crushing plant. In any quarrying or open-pit mining operation the primary crusher, shovel, and transportation equipment should function as a team; therefore these three items of equipment, when possible, should be considered as complements of each other when making selections. This is especially important with respect to the crusher and the shovel.
Shovel and Crusher Sizes
It has been customary for writers on this subject to tabulate a list of shovel dipper sizes and opposite these to list sizes of gyratory and jaw crushers that are considered to be suitable for operating in conjunction with power shovels equipped with such sizes of dippers. This is a little like putting the cart before the horse. The procedure omits one very essential factor: the character of the material that is to be crushed. For example, most limestone deposits are stratified, the cleavage planes usually being roughly parallel, and ranging anywhere from horizontal to almost vertical.
Regardless of how these strata lie, their thickness not only has an important bearing upon the type and size of primary crusher that can be expected to handle the rock with a minimum amount of secondary shooting, or bridging and blocking, but it also has a bearing upon the maximum size of shovel dipper that is suited for use in conjunction with a certain size of primary crusher. This statement is particularly applicable to the gyratory crusher because of the shape of its receiving openings. Two or three different maximum dipper sizes may be indicated for any one size of gyratory, depending upon the maximum strata thickness. In the case of the jaw crusher, with its rectangular opening, maximum dipper width and maximum strata thickness are established simply by the opening dimensions, and one maximum size dipper applies for each machine.
Suggested maximum sizes of shovel dippers (in cu. yd.) far use in various sizes of primary crushers, and for different thicknesses of rock conjunction with strata
[table “” not found /]
This table takes both dipper width and strata thickness into consideration. Opposite each listed size of gyratory crusher is tabulated the maximum advisable size of dipper, in cubic yards, for the different strata thicknesses up to the thickest ledge for which each crusher is suitable; that is, which it can be expected to handle with a minimum amount of secondary blasting. Crushers up to and including the 42″ machine are listed with both straight and non-choking concaves. Six sizes of jaw crushers are listed, the dipper sizes for each having been chosen as outlined in the preceding paragraph.
These dipper selections are of course predicated upon the assumption that the dipper is expected to act as a a measuring stick for the crusher, which necessarily presupposes that all rock will be passed through the dipper; a procedure that is rarely followed completely in any quarry operation. The experienced shovel runner soon learns how to judge the rock he is loading, with respect to the size and shape of the receiving opening it must enter, and a certain amount of “shuffling off of the dipper teeth” goes on in most quarries.
Admittedly no tabulation of this sort can substitute for actual experience with any particular rock or ore deposit. Some deposits which are of monolithic structure, and hence might be expected to shoot out in massive form, are readily shattered into workable sizes in the primary blasting operation; on the other hand, some stratified rocks shoot out in large slabs, which require either a large primary receiving opening, or a considerable amount of secondary shooting, or both. For those cases where no operational data are available to point the way, the table will serve as a guide that is believed to be on the safe side.
No particular problem exists in the matching of primary crusher and dipper size in the average gravel pit operation. The primary crusher is chosen on the basis of capacity (usually arrived at by estimating as closely as possible the percentage of boulders in the deposit), and receiving opening (as large as is consistent with the size of the operation), which may or may not involve crushing all of the boulders encountered in the bed of material. Quite frequently, in small or medium gravel operations, the larger boulders are cast aside and left in the pit.
The question of first cost of the crusher versus continued cost of disposing of oversize boulders is one that each gravel pit operator must settle to his own satisfaction. Most gravel pit operations involving the handling of large boulders incorporate some form of grizzly ahead of the primary crusher to “stop out” any boulders that are too large to enter the receiving opening. Therefore, the shovel dipper can generally be selected on the basis of required capacity. If the boulders are extremely large, and the plant capacity is high enough to justify the installation of a large primary crusher, the grizzly may be dispensed with, and the shovel dipper matched to the crusher receiving opening in the same manner as for the quarry.
Ore Transportation and Crusher Feeding
The size and type of transportation equipment in the quarry, pit, or mine should be coordinated with the primary crusher and with the proposed method of feeding this machine. It is not our purpose to discuss the selection of quarry equipment, other than to point out the ways in which different types and sizes of transportation equipment may affect the operation at the primary crusher house. It is difficult to deal with this subject in precise terms, because the factors involved are so variable, but a few general statements about what is, and what is not, considered to be sound practice may serve to point in the right direction, even if they do not give the exact distance.
Except for those rare cases where the size of the primary crusher receiving opening is greatly in excess of the size of the largest pieces of rock to be fed to it, the amount of material dumped into it at one time should not be much more than to fill the crushing chamber; otherwise, if blocking or hridging occurs, the time consumed in clearing the receiving opening is bound to be excessive. Therefore, if quarry cars of the quick-dumping type are to be used, their size should be selected with a . view to preventing such a condition. For the average quarry operation the following table will serve as an approximate guide in establishing the maximum size of quick-dumping car that should be used to feed different sizes of gyratory crushers:
Crusher Size | Car Capacity |
---|---|
20 in. | 4-5 tons |
30 in. | 6-8 tons |
36 in. | 8-10 tons |
42 in. | 8-10 tons |
50 in. | 10-12 tons |
54 in. | 12-15 tons |
60 in. | 15-20 tons |
If there are only occasional pieces in the feed that exceed about one- half the smallest dimension of the crusher receiving opening, these car sizes may be increased as much as 25 percent. They may of course be exceeded considerably in mining operations where there is a high percentage of undersize which is grizzlied out ahead of the crusher.
Generally speaking, jaw crushers should not be fed from quick-dumping cars unless the receiving opening is large enough to virtually eliminate any danger of bridging. Because the receiving opening of this type of crusher is relatively narrow, it is almost always necessary to use a flared hopper above it to receive the feed from the car or truck, the hopper may be two or three times as long as the receiving opening is wide. This means that the material must converge as it flows or falls toward the receiving opening, and this confluence is a natural invitation to bridging if a large amount of rock is dumped quickly into the hopper.
Controlled-dumping, used in conjunction with side-hinged cars and incorporated in all modern quarry trucks, permits the use of larger equipment. While it does not entirely eliminate bridging, it materially lessens the likelihood of its occurrence by the simple method of holding back part of the load until the crusher has a chance to clear itself of the other part.
Controlled-dumping works out well with any type of primary crusher. While it does not provide absolute control of- feed regulation, it is, next to the mechanical feeder, the best means of regulation for coarse material such as quarry-run or mine-run rock, certainly far superior to the quick-dumping car in this respect. It has one disadvantage: the time required to dump a load in two or more portions ties up the transportation equipment while the crusher is disposing of a considerable part of the original load. This tie-up is of no particular moment if the equipment consists of cars that are handled in trains of several units; for such operations the time-difference between quick- and controlled-dumping is negligible. On the other hand, if trucks are used, the aggregate idle time over an entire shift may add up to as much in the crusher house as it does at the shovel. Gyratory crushers, because of the greater volumes of their crushing chambers and their higher capacities, will usually function with less time-loss on this score than will comparable sizes of jaw crushers.
Car, skip, or truck bodies used for dumping directly into crushers of the jaw or single sledging roll types should be as short as is consistent with required capacity because of the relatively narrow receiving openings of these types. This will help to cut down congestion of material in the hopper above the crushing chamber, a tendency which we have mentioned in a preceding paragraph. Another point in favor of the short body is the saving in headroom between receiving opening and dump level. Somewhat longer bodies are permissible for gyratory crushers of comparable sizes because of the greater area and length of the receiving openings.
Feeders for Crushers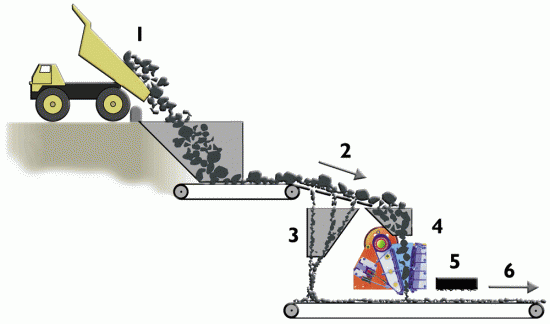
The ideal feeding arrangement for jaw crushers of any size is the mechanical feeder. This device, which has been developed in several forms, provides regulation as smooth as is possible to achieve in the handling of coarse materials; it permits instant shut-off of the flow of feed when blockades occur; it allows quick dumping of cars or trucks; and it delivers the feed to the crusher in a ribbon, the width of which can be adapted to the width of the receiving opening. For those installations employing grizzlies ahead of the crusher the advantage of the uniform flow is obvious; very short grizzlies will handle the coarse separation ordinarily required at this point, whereas grizzlies three or four times as long will generally be required if large amounts of material are dumped over them in a “one-shot” dose.
The mechanical feeder is of course an excellent device for feeding any type of primary crusher. Some type of feeder is used for such service in almost every gravel plant, at some point in the system at the shovel, under the surge pile, or immediately ahead of the crusher* depending upon the methods utilized ‘in excavating and transporting the; pit-run gravel to the crushing plant. Feeders of the reciprocating plate type, steel apron type, and electromagnetic type are all popular for this duty. These types are also extensively used in conjunction with underground mining operations.
For heavy-duty quarry or open-pit mining operations the heavy-duty steel apron feeder is the most practical type. It can be made in any length to fit in with any type and size of transportation equipment and crusher house arrangement. It has
been developed in sizes to suit any size of primary crusher, and of proportions suitable for handling any rock that the largest sizes of crushers will take.
Because of their heavy construction these heavy-duty apron feeders add materially to the initial cost of the primary crusher installation; naturally they add something to the overall cost of maintenance and power. The question of whether or not this added expense is justified will depend upon conditions surrounding each particular installation. If the crusher has an ample margin of capacity over and above the plant requirements, as is often the case when it has been chosen from the standpoint of an amply large receiving opening, occasional delays due to bridging are not apt to be serious; and the shovel and transportation equipment, chosen to work with such a crusher, are usually capable of making up for any time-losses thus incurred.
For such operations it is questionable if the cost of the heavy feeder is justified. On the other hand, if the operation demands full-time, or nearly full-time, crushing to meet the plant requirements, the case for the feeder is clear cut from every standpoint, at least so far as the jaw crusher is concerned. For reasons which have been discussed, their use with gyratory crushers, especially the larger sizes, is debatable, unless, as is done in some large mining operations, the designer wishes to establish a surge or stockpile ahead of the primary crusher.
To revert to the gravel and underground mining operations, now that vibrating screens of extra-heavy construction have been developed to handle large pieces of rock over their top deck, it is very probable that such screens will come to be used more and more as combination scalpers and feeders; a service for which they are admirably adapted. The advantage of being able to make a clean cut and definitely sized separation at this point will be of great value in many cases; and the high efficiency of the vibrating screen, as compared to the stationary bar grizzly, will appeal to those operators who want no undersize material in the feed to the primary crusher. The same idea in modified form, using smaller and lighter screens, can be applied to operations involving small rock and small crushers.
Rock Drilling and Blasting
It is not within the province of this work to discuss methods of drilling and blasting of rock or ore other than to point out that the system employed at any particular operation may have some influence upon the choice of the primary crusher, specifically, upon the size of the receiving opening. The foregoing discussion of primary crusher selection, for open-pit workings, has been predicated upon normal present-day practice in primary drilling and blasting, which in most cases involves either the familiar well drill or some system of tunnel shooting.
Admittedly, any kind of rock, regardless of physical structure or geological formation, can be blasted to suit any size of crusher receiving opening. During the early years of the application of power shovels to quarry operations in this country it was not uncommon to see crushers as small as the No. 6 (12″ receiving opening) operating in conjunction with shovels of 1.5 or 2 cubic yard dipper capacity; crushers such as the No. 8 (18″) and No. 9 (21″) were considered adequate for practically any primary crushing application within the ranges of their capacities.
Such operations almost invariably called for extensive secondary shooting in the quarry, even where the old tripod drills were employed for the primary drilling operation. They also necessitated the employment of from two to four men at the crusher to hand-feed the rock to the machine. Thus the labor and explosives costs were, in the light of present day practice, quite high, and with present day labor costs the expense of such a system of quarrying and crushing would be prohibitive.
Practically any open-pit operation will, over a period of years, justify the installation of a primary crusher of large enough proportions to permit carrying on the quarry operation with no more than a reasonable amount of secondary shooting. Quarrymen know that much can be done to minimize secondary shooting by adjusting primary drilling and blasting methods to suit the nature of the rock, but such expedients always involve an addition to the unit cost of operation; an expense that goes on and on through the life of the operation. The cost of providing an adequate receiving opening is a one-time expenditure, one that pays dividends over and over through the years.
The same argument may be carried on into the crusher house. If it costs $40,000 per year to maintain a man on the feed platform, simple arithmetic indicates that the maintenance of this man for a period of twenty years (a reasonable expectation for a crusher) will cost the operator some $800,000. Usually it will be found that the difference in first cost, between an inadequate and an adequate crusher, will be considerably less than this figure. The well designed modern primary crusher house should run with one man on the feed platform, with possibly a second man available on call to assist in emergencies.