Table of Contents
The ways to obtain successful Separation of Copper and Lead into individual Concentrates, several process approaches can be examined; bulk copper-lead flotation with a reverse flotation stage depressing copper, the same bulk flotation with a reverse flotation to depress lead and a sequential copper-lead-zinc flotation circuit as well as a simple cleaning of the bulk Cu/Pb concentrate by Pb depression.
Here is a case study, depicting the various Cu-Pb Separation methods used in Laboratory tests which, for this sample, indicated that separate copper and lead concentrates could be produced. The ore tested in a Copper/Lead/Zinc ores hosted in acid generating pyrite.
At the end, the use of a sequential copper-lead-zinc flotation circuit produced the most efficient copper and lead separation. A bulk flotation process followed by a reverse flotation where copper was depressed and lead was floated from the bulk concentrate also produced separate concentrates, but at lower efficiency than the sequential circuit.
Both processes require the use of cyanide, but the bulk flotation process with copper reverse required very high doses of cyanide.
Successful treatment of poly metallic deposits using flotation requires a thorough understanding of the sulphide mineral suite present and how these minerals fragment from each other during the grinding process.
Master Composite sample contained nearly 40 percent by weight sulphides. Iron sulphides** were the most abundant category of sulphide mineral, accounting for nearly one quarter of the sample mass. The remaining sulphides, in order of relative abundance, were sphalerite, chalcopyrite and galena. The mineralization of the Master Composite are low in iron sulphide content. The ratio of galena to chalcopyrite will make it difficult to efficiently recovery high grade lead concentrates.
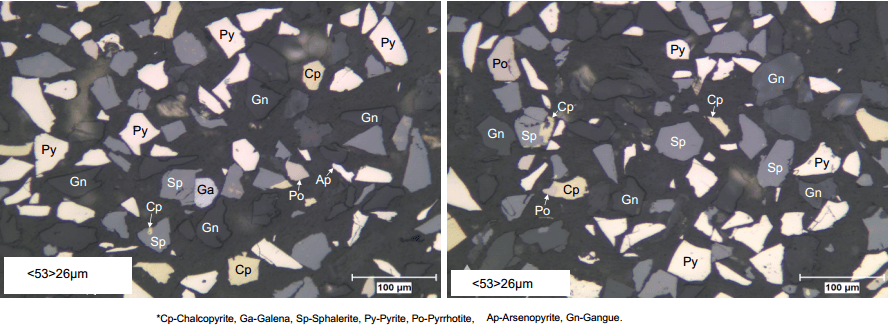
Chalcopyrite and galena had two dimensional liberation levels of 58 and 50 percent, respectively. Interlocking between these two minerals was relatively rare; however, both chalcopyrite and galena had significant interlocking with sphalerite and pyrite. Due to the nature of this interlocking, separation of chalcopyrite and galena is viable at this grind size, but additional regrind power would be required to liberate pyrite and sphalerite from chalcopyrite and galena.
The limiting grade recovery curves for chalcopyrite and galena are displayed below at the nominal grind sizing of P80 of 48 microns. To achieve grade and recovery points above the curve require regrinding, only points directly under the curve can be theoretically achieved.
This Copper Lead Concentrate Separation study includes the performing of 3 rougher tests and 18 batch cleaner tests. These tests were used to assess the metallurgical performance of several copper and lead separation processes. The initial rougher tests were used to determine general response of the sample and batch cleaner tests were used to examine the various reagent schemes and flowsheet configurations. Only the batch cleaner tests are discussed in the following subsections.
Four basic approaches (Flowsheet and Reagent Variants) were investigated to separate lead for copper by flotation to produce Separate Concentrate products:
![]() |
![]() |
Copper Lead Separation Flowsheet A: A bulk copper and lead flotation, followed by a copper depression reverse. This scheme uses cyanide to depress the copper in the reverse process. With the use of cyanide in the reverse, cyanide was also used in the bulk flotation process to depress sphalerite and pyrite. | Copper Lead Separation Flowsheet B: A bulk copper and lead flotation followed by a lead depression reverse. This process uses Sodium Metabisulphite (MBS) for depression in the bulk circuit and in the reverse circuit. |
![]() |
![]() |
Copper Lead Separation Flowsheet C: Sequential copper, lead and zinc flotation. This circuit would use MBS as the primary depressant. This option could require significantly more equipment installed at site to implement. | Copper Lead Separation Flowsheet D: Copper only flotation with lead depression to tailings. This approach is essential to the current practice at the plant. A few tests were performed to measure the effectiveness of this approach and examine some reagent dosages to enhance lead depression. |
This sample provided for this study contained 2.1 percent chalcopyrite, 0.5 percent galena, 14.3 percent sphalerite and 23 percent iron sulphides, present as mostly pyrite. The measured mineral content low in iron sulphide content. The fragmentation characteristics of the sample were measured at a nominal grind size of P80 = 50um. At this grind, chalcopyrite and galena were sufficiently liberated for recovery into a bulk rougher concentrate. More importantly, there was very little interlocking between copper and lead sulphide, indicating a separation of these minerals is possible at this grind size.
Chalcopyrite and galena were interlocked with mainly sphalerite and pyrite. Therefore, these minerals would require significant regrinding in advance of dilution cleaning to achieve efficient concentration and recovery to final concentrates.
There were four basic approaches to separate copper and lead studied in this program.
- A bulk rougher flotation of copper and lead followed by a reverse separation to recover lead and depress copper.
- A bulk rougher flotation of copper and lead followed by a reverse separation to float copper and depress lead.
- A sequential copper-lead-zinc flotation process.
- A process to produce higher grade copper concentrates by depression of lead.
The sequential flotation process produced the best batch test results: The test had the highest selectivity between copper and lead. Copper in the feed was, on average, 63 percent recovered into a copper concentrate grading 24 percent copper and 1.6 percent lead. On average, lead in the feed was 36 percent recovered into a concentrate grading 55 percent lead. Only 0.3 percent of the copper in the feed was recovered to the lead concentrate. This process used MBS in the copper circuit and relatively low doses of cyanide in the lead circuit.
A close second was the bulk flotation process with lead flotation reverse and copper depression. For the best three tests, copper in the feed was 57 percent recovered to a concentrate grading 27 percent copper and 5 percent lead. For the same three tests, lead in the feed was 39 percent recovered into a concentrate grading 52 percent lead and 7.8 percent copper. This process requires very high doses of cyanide, which would increase the operating cost and impose a potential environmental cost to the operation.
The other flowsheet variants and reagent schemes produced much poorer results. The tests for these flowsheets had high lead recovery to the copper concentrate. The batch cleaner test data demonstrated that separate copper and lead concentrates could be produced from this composite sample. It was also demonstrated that the production of separate copper and lead concentrates would result in reduced copper metal recovery to the copper concentrate when compared to the bulk flotation process.
In this case, locked cycle tests would be required to determine the final metallurgical estimates for both copper and lead.
Flotation of Copper-Lead Ore
The separation by flotation of copper from lead or zinc minerals can hardly be said to be standardized at present, and no more than a brief account of the usual procedure will therefore be given. The methods in general use have a more or less similar basis in that they are variations of the standard process for the treatment of lead-zinc ores described in the previous paragraph.
When copper-bearing minerals are to be separated from galena, the first step generally consists of the “bulk flotation” of both classes of mineral in one copper-lead concentrate by the use of reagents very similar to those employed in the lead flotation section of a lead-zinc plant. Any zinc and iron sulphides are depressed with sodium cyanide and/or zinc sulphate and floated in subsequent zinc and iron sections in the ordinary way. The addition of cyanide for this purpose must be kept to a minimum, since not only does it depress copper-bearing sulphides if present in sufficient strength, but an excess may also result in the formation of copper cyanide in solution with consequent activation of the zinc sulphides. The depressing effect, however, is so much more pronounced on the zinc and iron than on the copper minerals that a reasonable recovery of the latter is usually possible.
The lead-copper concentrate is cleaned if necessary, diluted to a suitable pulp density, and treated in a conditioner with sodium cyanide in sufficient strength to depress the copper minerals, the galena remaining unaffected, and with enough soda ash to make the pulp distinctly alkaline; a pH value of 9.0-10.0 is usual. The pulp then passes to a flotation machine where a lead concentrate more or less free from copper is taken off after the addition of the minimum amount of frothing reagent and little or no promoter. The tailing of this operation, substantially free from galena, constitutes the copper concentrate. It is often possible by the above method to make a lead concentrate containing 50% of lead and 5% or less of copper, and a copper concentrate containing 20% or more of copper and 5% or less of lead. Higher grade concentrates than this are not common as the ores usually carry pyrite, from which it is difficult to keep the products entirely free.
Another method, which is often more effective than the preceding one, consists of the oxidation and depression of the galena by means of sodium dichromate with subsequent flotation of the copper minerals. A bulk lead-copper concentrate is made as before and run without dilution into a conditioning tank where it is treated with sodium dichromate for the requisite period. The amount of reagent necessary varies with the percentage of lead in the concentrate. One rich in lead often requires as much as 4 lb. of dichromate per ton of original ore with a 20-minute period of contact, while a concentrate consisting mainly of copper mineral may only need 0.25 lb. per ton with a 5-minute contact. The pH value of the pulp must not fall below 7.5; it normally ranges from 7.5-8.5. After being conditioned, the pulp is diluted and pumped to a flotation machine with the addition of a small quantity of pine oil or cresylic acid. The copper sulphides can then be floated off, the galena passing out in the tailing which thus comprises the lead concentrate. The copper and lead concentrates obtained by dichromate treatment are generally of rather better grade than those made by the cyanide method.
Flotation Copper-Zinc Ores
The separation of copper-bearing from zinc sulphides is effected by two-stage selective flotation, the zinc minerals being depressed and the copper minerals brought up in the first stage with reagents similar to those required in the lead flotation section of a lead-zinc plant; the zinc sulphides are floated in the second stage in the ordinary way. The ores treated by this process are mainly those containing chalcopyrite, sphalerite, and marmatite in a very pyritic gangue. On account of the presence of pyrite, the cyanide addition must be kept to a minimum for the same reasons that make it necessary for copper-lead ores. Lime is generally employed to regulate the alkalinity on account of its action in preventing the pyrite from floating. Aerofloat and dithiophosphates are useful as promoters, since xanthates often have too great a tendency to bring up zinc and iron sulphides. One or two stages of cleaning are usually needed for the copper concentrate on account of the presence of pyrite.
When the copper mineral is chalcopyrite, it should be possible to make a copper concentrate running 20% of copper or slightly more with less than 5% of zinc, and a zinc concentrate running 40 to 50% of zinc, depending on whether the mineral is mainly marmatite or sphalerite, with less than 5% of copper.