Table of Contents
The third type of mill that I mentioned was an AUTOGENOUS MILL, this type of mill uses a completely different type of grinding media; the rock itself
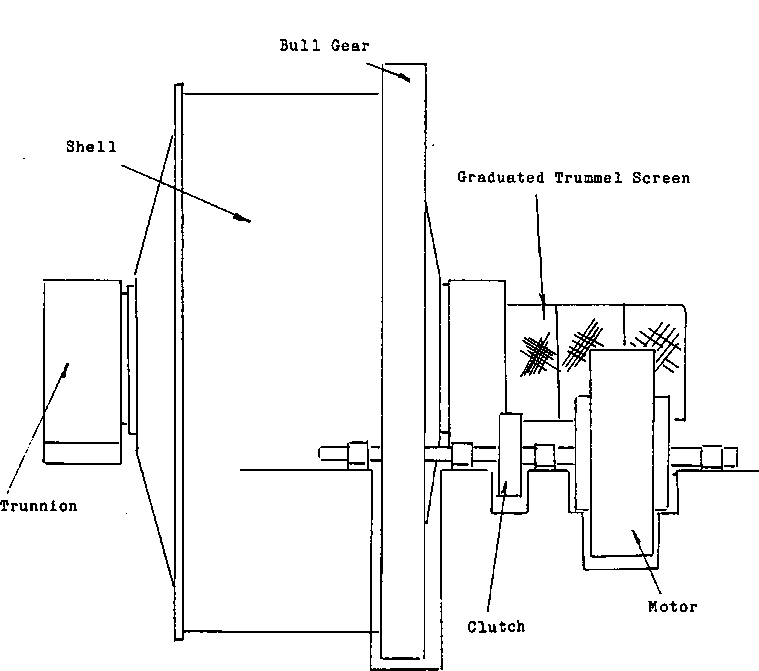
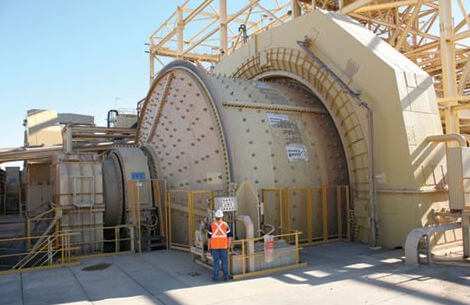
In conventional milling, the ore is crushed to, plus or minus, 3/8 of an inch, before it is put into a mill for grinding. In a autogenous mill the ore is fed directly into the mill from either the primary crusher or the mine itself. The size of the rock will be between four and eight inches. It will be this type of mill that will use a stock pile instead of a bin as fine ore storage. The feed is large enough that moisture and freezing won’t bother it. The mill design itself is a little different. In conventional mills the diameter of the mill is smaller than its length. In autogenous mills the diameter is greater than the length. They can be as much as 40+ feet in diameter.
Patented in 1959, AG Mills are not so popular any more.
This large diameter of mill is required to achieve the impact necessary to grind the ore. The main source of reduction comes from the impact of the rock falling on rock. The mill has only twenty five to thirty percent of its volume taken up with ore. With that diameter of mill the cascade point is very high from the toe of the load. Which is the impact zone for the media. This means that the ore is being broken up by falling against the liners and being hit by the larger rock. Some of the rock will only be broken in this manner just so far. The rock that reaches this critical size will build up in the mill until it either has to be taken out or large steel balls will have to be introduced to the mill to continue crushing it.
Intermediate Autogenous Grinding
Autogenous grinding tests were run in a 10-ft x 4-ft Rockcyl mill. The principle of prepared feed and media was utilized to determine how coarse a feed could be commercially fed to a rock mill. Secondary rock milling was expanded toward the particle sizes of primary milling while still utilizing the practices of secondary milling.
The closed circuit test mill was installed in an operating plant in parallel with existing conventional rod mill-ball mill circuits. Three stages of open circuit crushing were used to prepare rod mill feed. Grinding media was selected from various areas of the mine and tested separately. Impact tests on the three basic types of ore give Work Indices varying from 14.8 to 9.1 with two types appearing to be suitable as media and the third type questionable. The test mill was fed plant run ore with an average Work Index of 16.
Critical size buildup occurred in the first series of tests run, with a feed 80% passing 1¼ in. The size of media required for this size feed could not be obtained from the discharge of a primary crusher in commercial practice.
Using mill feed averaging 80% passing 5/8 in. critical size buildup occurred only when there was an excess of tramp oversize due to bin segregation and when using soft ore for grinding media. Screening mill feed at 1 in. square mesh solved the problem. It was established that rock milling could be applied to the product of a closed circuit tertiary crusher.
Media all plus 5 in. square and averaging 6½ in., weighing 10—15 lb. was found to be ample to perform the desired grind. Depending upon the type of ore used as media the average rate of media addition was 8 to 12% of the total feed rate, (new feed plus media). Mill power was used as a guide for media additions.
The test mill drew maximum power with about a 40% load and was run with from a 35 to 40% load. With no critical size buildup and with controlled rate of media addition there w:as no need for crushing in the mill so the load could be carried at near maximum power level. The media wore through the critical size range at least as fast as critical size material was generated. Critical size material not being in the feed must be generated in the mill and is probably only a small percentage of the total mill charge.
The Bond Work Index Formula was used to determine the operating Work Indices for the test rock mill and the parallel rod mill—ball mill circuits. This formula, taking into account feed size, product size and power, proved an accurate tool for comparison. The operating Work Indices compared favorably and checked laboratory Work Index data.
The conclusions reached from these tests run:
- Intermediate autogenous grinding can efficiently replace the rod mill and ball mill stage of a conventional grinding circuit.
- The need was shown for closed circuit operation of the last stage of crushing to control the top size of the mill feed.
- A reasonable rate ratio between media and total mill feed was established. This ratio is dependent upon the quality of the media and the grindability of the mill feed.
- With a proper size ratio of media to feed, critical size buildup did not occur.
- With proper rate ratio and size ratio of media to feed, the intermediate rock mill was as efficient as the rod mill—ball mill circuit.
- Liner wear in the test mill was higher than in the rod mill—ball mill circuit but total steel consumed was considerably less. Estimated saving for inter-mediate autogenous grinding is 65 to 70% of the cost of rod and ball consumption.
- The test mill required the constant attention of an operator. For a commercial plant with several mills, automation is necessary, using circulating load to control mill feed rate, and mill power to adjust and control media addition.
- Intermediate rock milling is a practical phase of autogenous grinding, with the advantages of secondary grinding and without the problems of primary grinding.
- Any ore or rock containing a suitable quantity and quality of media size material can be ground by intermediate rock milling.
- Wet grinding intermediate autogenous mills can have mill lengths from 0.5 to 1.0 times the diameter.
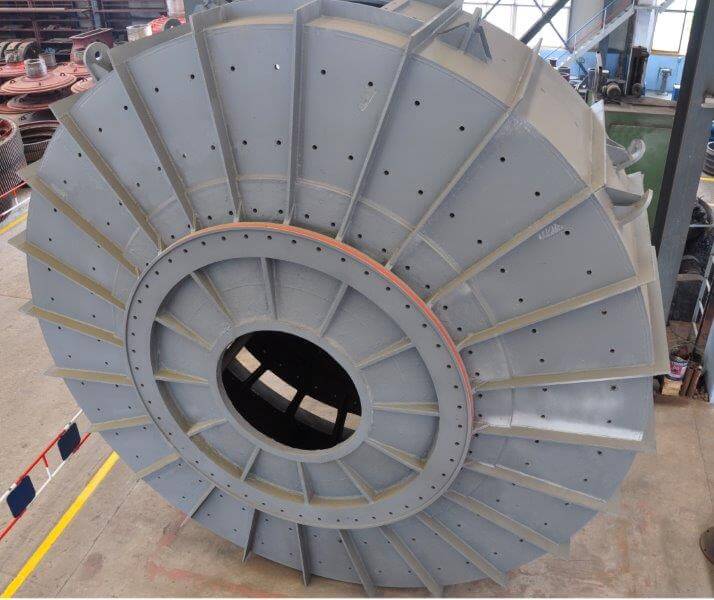
Autogenous Grinding Explained
Mill length was the primary variable investigated in an autogenous pilot mill circuit. The 5-½’ diameter mill had both pebble ports and ½” wide slotted grates. The plus ½” mill product was crushed in a cone crusher and returned to the mill feed along with the minus ½” plus 4 or 6 mesh fraction. Tests were run with a short mill, inside length of 26-3/8″, or diameter-to-length ratio of 2.50 to 1. The same mill was then lengthened to 48-3/8″, diameter-to-length ratio of 1.36 to 1.
Test Conditions
Autogenous Pilot Mill
Drive – 30 HP, 440 V motor, speed reducer and chain drive
Inside diameter – 66 inches measured inside of shell liners
Short = 26-3/8 inches; long = 48-3/8 inches measured inside end liners.
Diameter to length ratio: short = 2.50 to 1; long = 1.36 to 1
Speed = 25-¼ RPM, 77.3% of critical speed; lifters, 12 x 4″ high evenly spaced.
Discharge – low-grate trunnion
Grate – ½ inch wide slotted
Crusher, 3 foot Short Head Cone Crusher
Grinding Characteristics of Short Mill Versus Long Mill
In spite of small variations in mill charge level, and, in one case, an apparent variation of feed size structure, in all three series the same general relationships were found between short and long mill grinding characteristics. Those trends are:
- Circuit grinding rate per foot of mill length is higher with the shorter mill configuration.
- Power per ton of minus 200 mesh (or minus 400 mesh) produced is essentially the same in the short mill and long mill.
- Circuit product size distribution is finer In the longer mill circuit.
- Mill circulating load is lower in the long mill circuit than in the short mill circuit.
- The mill charge size distribution at the end of each eight or nine hour test run is finer in the long mill than the short mill.
The fall-off in circuit capacity or feed rate per unit of length with the longer mill is clearly shown. The long mill is 1.83 times the length (or volume) of the short mill, but the increase in capacity of the long mill is only 1.34 or 1.56, depending upon whether the grate open area is increased in the same proportion as the length. The circuit capacities per foot of mill length also show that the mill capacity favors the shorter mill configuration.
Power per ton of circuit product favors the shorter mill by a substantial margin in Series 1 and 2, and by a small margin in Series 3. The average of all three tests gives a short mill power of 9.5 KWH per ton compared with 11.35 KWH per ton for the longer mill circuit. Again, however, the effects of the finer grind become apparent when power per ton of minus 200 mesh produced is compared for the short and long mill runs.
The size structures of the circuit products at 35, 200 and 400 mesh show the trend of increased fineness in the longer mill product.
Observations and Recommendations
Based on these tests in a 5-½ foot diameter pilot autogenous mill, the effect of increasing the length is:
- The longer mill capacity does not increase in direct proportion to the increase in length.
- The size structure from the longer mill, compared with the shorter mill, is finer.
- The horsepower per ton of product is higher in the long mill (to be expected since product is finer),
- The horsepower per ton of -200 mesh (or say -400 mesh) produced is essentially the same in the long as the short mill.
It is not known whether the relationships found in these tests on the 5-½-foot diameter mill are valid for commercial size mills. However, if it is assumed that they are, the relative grinding characteristics of a 20-foot diameter mill of different lengths would be as follows: