Table of Contents
Let’s follow a rock through a crushing cycle to see what variables will have to be controlled. First the rock will enter the crushing chamber and drop as far as the angle of the crushing surface will allow it to. The crusher “breaks it and the fine material produced will drop through the gap between the mantle and the liner as it opens. The coarse material that can’t fall through will remain to be crushed with the next gyration. The speed of the crushing cycle depends upon how large the initial rock was, the revolutions per minute that the crusher is traveling at, and of course gravity. The speed in which the rock falls to the next nip- point.
By this description it is understandable that one of the main variables in tonnage throughput is the size of the discharge opening of the crusher. To control this variable, the opening is adjusted by a device called a hydro-set. It lifts or lowers the mantle to adjust the opening and to compensate for wear on the mantle and liners.
The gap opening of the primary’s mantle is very important not only to the production of the primary but also to the next stage of size reduction. As the ore becomes smaller it becomes harder to crush. This is because there aren’t the same amount of fracture lines in small rock as there are in large rock. This makes the size of crush, that the primary is set at, critical. Maximum throughput for the primary is required but at the same time the crush size must be small enough to allow the next stage of crushing to run at its most economical rate.
Rock Crushers fill the duty of rock size reduction and can be classified in various stages of duties:
- Primary crushing is the first crushing stage,
- secondary crushing is the second,
- Tertiary crushing is the third,
- Quaternary crushing is a rare forth stage of rock crushing,
Coarse crushing includes crushing operations discharging at sizes 4- to 6-in. or coarser; intermediate crushing comprises operations taking feeds 6- or 8-in. maximum and making products down to -1/2″ or 3/8″. Fine crushing is reduction by crushing to 1/4″ or finer; the distinctions are not sharp.
Rock Crushing is a mechanical operation in which a sufficient force is applied to relatively brittle solid particles in such directions that failure of the bonding forces in the particles is brought about. When the problem of crushing is thus approached, it becomes clear that crushing machines must be designed to exert either pushes or pulls on individual particles, since there are no other kinds of mechanical forces, and that the solid particles must be so introduced into and maintained in the force zone that the forces available can be applied to them. The study of the mechanics of materials has resulted in a classification of mechanical forces and of the structural elements for resisting them which, applied in reverse, supplies a terminology and basis for classification of crushing machines along mechanical lines. Thus the common load-bearing members are beams, columns, and ties; stresses induced in these by loading are tensile, compressive, and shearing; and the applied loads are stationary, slow-moving, or impact. Most crushers load the solid particles they crush as beams or short columns, but explosive shattering, whether by dynamite or by steam, loads them largely as ties. The induced stresses are mostly those of compression and shear, but tensile stresses arise in beam loading as well as in explosive shattering. The rate of loading in the majority of crushing machines is gradual; impact crushers form an important class, however; stationary loading is unknown.
With one or two relatively unimportant exceptions, all rock crushers taking coarse feeds apply pressure gradually to particles which take the load as simple beams or short columns. Two general types of mechanism are employed:
- reciprocating rock crushers in which the crushing surfaces alternately approach and withdraw from each other, and
- continuous rock crushers in which, in the crushing zone, there is continuous approach of the crushing surfaces to a substantially fixed predetermined minimum spacing.
Reciprocating-pressure rock crushers include jaw, gyratory, cone, and gyrasphere crushers; continuous-pres-sure rock crushers are typified by rolls, single-roll crushers, and the so-called roller mills. Impact crushers form a group comprising mechanisms some of which, e.g., stamps, load the particles primarily as short columns, whereas others load by striking particles in sue pension or by hurling them at high speed against stationary surfaces; hammer mills are typical of this latter class.
Tumbling mills (ball mills, rod mills, etc.) utilize both continuous-pressure and impact mechanisms. Blasting, explosive shattering, and decrepitation (fire-setting) are tension-type crushing operations; all three are relatively unimportant as crushing operations, although blasting is, of course, pre-eminently useful in rock excavation.
A crushing machine must not only crushes the rock but must provide means for continuous presentation of uncrushed material to the crushing zone and continuous discharge of crushed material therefrom. Gravity is the force employed for presentation in the great majority of machines; gravity, gravity aided by the carrying force of a fluid (air or water), and gravity aided by the mechanical impulse of the crushing surfaces are the usual means of discharge. In some cases, however, gravity is used as a retarding force against the discharge impulsion of a stream of fluid by putting a weir-type baffle in the path of the discharge stream; in other cases discharge is regulated—and retarded—by a screen or similar perforate septum.
The size characteristics of a crushed product are determined, all other things being equal, by the mechanical principles employed in the crushing machine. Gradual application of load, loading particles as beams and short columns, and rapid and unhindered discharge from the crushing zone make for a granular product with a minimum of very fine material; impact, shear, and slow restricted discharge all tend to produce fines. Cumulative weight-per cent, size curves for the product of crushers employing the first group of principles exclusively approach nearest to straight lines; the product of the grinding pan, which employs shear (abrasion) for crushing and interposes a high weir in the path of the water-borne discharge, plots as a highly concave curve. With doubtful exceptions the sizing curves of the products of all other comminuters fall between these limits.
Rock Crusher Types
Coarse crushers or breakers for rock are the jaw crusher, gyratory crusher, single-roll crusher, sledging or slugging roll, HPGR, and occasionally, the impact crusher. Intermediate crushers are the reduction gyratory, cone crusher, hammer mill, rolls. Fine crushers are rolls, hammer mills, short-head cones, fine-reduction gyratories, and stamps; certain grinding machines, e.g., the rod mill, may be used for fine crushing.
In general, jaw and gyratory crushers are pre-eminently adapted to crushing hard, tough, abrasive rocks. They are, therefore, used for the majority of metalliferous ores, which, it so happens, occur mostly with gangues of this description. The primary roll crushers and the hammer mill cannot crush such rocks economically but are particularly useful with the relatively soft, friable and sticky rocks that are characteristic of many nonmetallic mineral deposits.
Crushing is an integral portion of the comminution flowsheet for mineral processing operations and is critical for the preparation of ore for downstream processing. The selection of the right crushing equipment for a specific application is influenced by many factors some of which are upstream of the crushing plant (blasting pattern and mining method) and others which are downstream of the crushing plant (heap leach or mill, grinding circuit selection). For most applications there is a flowsheet previously designed that will match the requirements.
The cost to recover metal from ores continues to increase and at the same time fewer high grade deposits are being discovered. Designers and manufacturers, plant operations and maintenance personnel and plant designers continue to look for opportunities to enhance the plant operation with better equipment designs and/or unique applications that improve the economics of the operation. With the improvement in materials of construction larger crushers with more horsepower, higher speed and higher throughput have been designed. The equipment designers have attempted to make the new designs compatible with the smaller, older models to make it possible to upgrade existing facilities and minimize capital cost.
Jaw Crusher
The jaw crusher shown has a stationary jaw plate and a moveable jaw plate. The opening at the top of the jaws will be the limiting factor with respect to the maximum size of the rock that can be delivered to the crusher and on the capacity of the crusher. Jaw crushers can be found in a large range of sizes as the smaller models are frequently found in laboratories. For industrial applications the crusher sizes range from 450 mm to 1600 mm with capacities from 50tph to 1000 tph. The jaw plates and liners for the crushers provide a progressive crushing cavity, with the rock dropping through the crusher each time the moveable jaw swings open.
Jaw crushers have been the primary crushing equipment of choice offering simplicity of operation and maintenance and low head clearance to minimize the underground excavation requirements.
Gyratory Crushers
The gyratory crusher. provides a crushing chamber similar to the jaw crusher providing a progressive crushing cavity. The crushing action is provided through an eccentric that swings the bottom of the crusher mantle with respect to the bowl and concaves.
Gyratory crushers have the largest unrestricted opening when compared to other crushers. Standard crusher feed sizes range from 1067 mm (42”) to 1829 mm (72”). The 1067 mm gyratory crusher has essentially the same capacity as the 1600 mm (1600 x 2000) jaw crusher.
Gyratory crushers tend to offer more flexibility than most other crushers with respect to moderating feed rates. Gyratory’s arc generally fed end dump from haul trucks into the crushing chamber.
Impact Crushers
Horizontal Impact crushers, accomplish material breaking and size reduction through impact of the material with fixed or free swinging hammers that revolve about a central rotor. The product gradation will be a function of rotor speed and ore friability. In the impact crusher particles of an ore with a common impact value will break according to initial mass, larger pieces will be subjected to more severe impact and will break more readily than finer particles.
Impact crushers when compared to conventional compression crushers; jaw, gyratory, cone, will have a lower installed capital cost per ton of capacity. Because of the rotating speed of the crusher the operating and maintenance costs and equipment downtime will be higher for the impact crusher.
Vertical impact crushers are similar to the horizontal impact crushers in that they are high speed units that rely on kinetic energy to develop the crushing force. Ore is fed through the top center of the crusher into the rotor. The high speed rotor throws the ore to the outside of the crusher. Crushing results from interparlicle collisions and from ore striking the hammer or material bed that forms at the periphery of the crushing chamber. These crushers can be supplied with mechanical wear components and liners or for autogenous operations.
Roll Crushers
The high pressure grinding rolls (HPGR) have been used very successfully in diamond processing because of the ability to crush the host rock while minimizing diamond breakage. Crushing in the high pressure grinding rolls takes place between two counter-rotating rolls, one of which is Fixed and the other moveable. The ore is choke fed into the crushing chamber between the rolls which promotes crushing in the bed of particles. Compared to conventional roll crushers where crushing occurs between and in contact with the two rolls, contact between the rock and the surface of the roll is limited reducing abrasion of the rolls.
HPGR technology has also been used successfully in the iron ore industry and is undergoing further development for application in the gold and copper industry. Preliminary development work for the gold industry has indicated that the micro-fracturing that occurs in the HPGR may promote heap leaching kinetics and/or recoveries.
Cone Crushers
Cone crushers are typically installed for secondary and tertiary crushing applications. The operation of a cone crusher is similar to that of a gyratory crusher in that the cone or mantle travels eccentrically with respect to the bowl. The significant differences are that the cone operates with a higher speed and that the cone travels through a much larger distance. The configuration of (he cone and bowl provide a much flatter crushing angle than the gyratory.
The two main crusher configurations for cone crushers provide for standard and short-head configurations. For each of these there are different liner configurations; coarse, medium and fine, for both the cone and the bowl. Initial configurations will be determined based on pi ini throughput and top size of feed. Operations and maintenance personnel then have the ability to assess equipment wear, maintenance and operating characteristics to determine whether belter performances can be achieved by changing the shape of the liners.
The “Water Flush” crusher technology previously discussed is a cone crusher application with modifications to the crusher required to allow the addition of water with the ore feed.
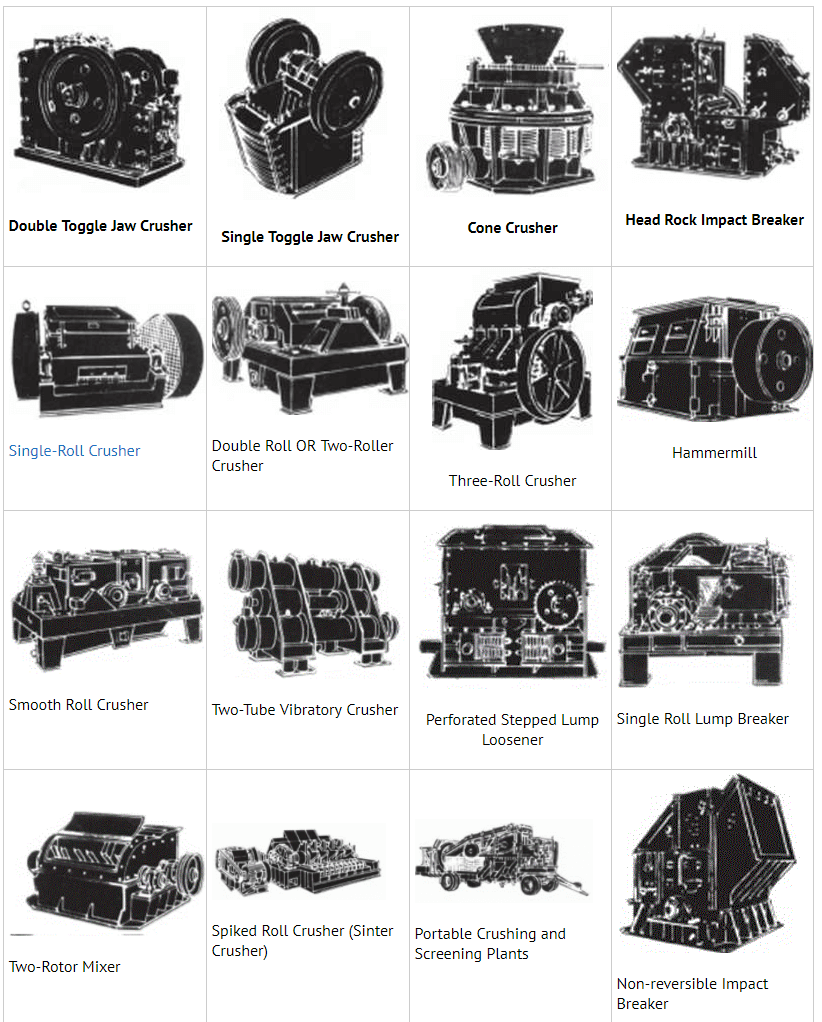